Abstract
Objectives
The most important drawback of dental implant/abutment assemblies is the need for a fixing screw. This study aimed to develop an esthetic one-piece Y-TZP abutment to suppress the use of the screw.
Methods
Material characterization was performed using a bar-shaped specimen obtained by slip-casting to validate the method prior to prototype abutment fabrication by the same process. The mechanical behavior of the prototype abutment was verified and compared with a conventional abutment by finite element analysis (FEA). The abutment was evaluated by micro-CT analysis and its density was measured.
Results
FEA showed stress concentration at the first thread pitch during installation and in the cervical region during oblique loading for both abutments. However, stress concentration was observed at the base of the screw head and stem in the conventional abutment. The relative density for the fabricated abutment was 95.68%. Micro-CT analysis revealed the presence of elongated cracks with sharp edges over the surface and porosity in the central region.
Significance
In the light of these findings, the behavior of a one-piece abutment is expected to be better than that of the conventional model. New studies should be conducted to clarify the performance and longevity of this one-piece Y-TZP abutment.
1
Introduction
Clinical trials have demonstrated that the most significant drawback of metallic implant/abutment assemblies is the presence of a titanium fixing screw, which may fracture or become loosen with time due to localized plastic deformations . These problems related to the fixing screw have also been observed in laboratory studies that evaluated the fracture load of implant abutments. The presence of an internal gap around the screw has been claimed to be the reason for the observed failures . Fracture and loosening of titanium screws have also been reported for ceramic abutments and seem to be related to stress concentrations at the base of the screw head . One way to overcome the aforementioned failures in metallic implants is to use internal tapered connections. Besides the fact that this type of connection is more stable than other connection types, tapered abutments do not need to be fixed with a screw when they are designed as a single piece made of solid titanium with an apical threaded portion .
Currently, yttria-stabilized tetragonal zirconia polycrystal (Y-TZP) abutments with tapered connections are only available with titanium fixing screws (two-piece abutment). The inherent brittleness of ceramic materials makes them very hard to be machined, and therefore it is not possible to produce the apical threaded portion for one-piece solid Y-TZP abutments. A previous work evaluated the fracture load of two-piece Y-TZP abutments attached to implants with internal tapered connections and showed that fractures occurred at the cervical portion of the abutment after screw loosening . Therefore, the development of one-piece Y-TZP abutments could represent a good prosthetic solution as they are expected to be more reliable for all-ceramic implant-based rehabilitations.
One-piece Y-TZP abutments cannot be produced by machining due to the low milling precision of currently available equipments. Alternatively, these structures may be fabricated by the slip-cast technique, which uses a gypsum mold to produce pieces with complex shapes, like the apical threaded portion of ceramic abutments. It has been demonstrated that the slip-casting process leads to Y-TZP pieces with high density and nanometric grain size .
The aim of this study was to develop a one-piece solid Y-TZP abutment with tapered connection and apical threaded portion using the slip-casting technique. Initially, finite element analysis (FEA) was used to predict the stress distribution throughout the abutment during simulation of its installation and application of an oblique incisal load. A conventional two-piece abutment was also modeled for comparison purposes. In addition to the FEA, one bar-shaped specimen obtained by slip-casting was produced for microstructural characterization and determination of physical properties. The actual one-piece solid Y-TZP prototype was also produced and structural quality assessed by means of 3D micro-computed tomography (micro-CT) and density determination. The main hypothesis of the study was that FEA would show more homogenous stress distribution for the one-piece Y-TZP abutment compared to the conventional two-piece abutment during installation and loading.
2
Materials and methods
2.1
Finite element analysis
The software Rhinoceros 4.0 (McNeel North America, Seattle, WA, USA) was used to model the one-piece Y-TZP abutment proposed in this study and also a conventional Y-TZP abutment fixed by a metallic screw. The prototype model had a 6 mm-high coronal portion and a base with a width of 4.5 mm in diameter converging at a 5° angle to a 3 mm diameter to the occlusal surface, where it had a hexagonal niche to attach the fastening tool. The conventional abutment model had the same dimensions of the prototype except for the niche, which was replaced by an access hole that allowed the screw to pass through the abutment body. The tapered connection dimensions of both models were 6 mm in total height, 1.5 mm of transmucosal height, converging to the apical threaded portion at an angle of 11.5°.
The 3D models were transferred to the FEA software Ansys Workbench v13 (ANSYS Inc., Canonsburg, PA, USA) that was fed with Young’s modulus, Poisson’s ratio for the titanium (implant and screw) and Y-TZP (abutment). The Y-TZP elastic constants were measured using the bar-shaped specimen later described. The Ansys software generated the meshes for the models, using predominantly tetrahedral quadratic elements. After the mesh convergence test, the prototype with its corresponding titanium implant model had 381.436 nodes for 252.788 elements and the conventional abutment with its titanium screw and implant model had 339.692 nodes for 215.342 elements. The connection type between the implant and abutment models was selected as frictionless, except for the titanium screw and the conventional zirconia abutment connection for which a frictional ratio of 0.275 was used .
In the first simulation, the abutments were fixed to their corresponding implant with a 15 N cm torque. In the second simulation, the fixed abutments were obliquely loaded at the coronal portion with a 60° angulation. The load magnitude was based on the mean bite force determined for the central incisors region (210.5 N) .
2.2
Y-TZP bar-shaped specimen
A commercially 3 mol% Y-TZP slip (Jahr Bioceramicas, Porto Alegre, RS, Brazil) was slip-cast to form a bar-shaped specimen in a type II dental stone mold. After 24 h at room temperature, the slip-cast Y-TZP green bar was carefully removed from the mold and finished manually with 600-grit sandpaper to remove edges and irregularities. To calculate the Y-TZP shrinking rate, the dimensions and volume of the Y-TZP green bar were measured with a digital caliper before and after sintering.
The Young’s modulus ( E ), shear modulus ( G ), and Poisson’s ratio ( ν ) were obtained in a Sonelastic ® Equipment (ATCP Engenharia Fisica, Sao Carlos, SP, Brazil) using the dynamic method described in the ASTM E-1876 . The mean grain size of the slip-cast Y-TZP was measured according to the ASTM E-1382 following heat treatment to reveal grain boundaries . SEM micrographs were digitally analyzed to determine the Feret diameter (μm).
2.3
One-piece Y-TZP abutment
To produce the mold that allowed slip-casting of the one-piece Y-TZP prototype abutment with an apical threaded portion, first an enlarged metallic master model was machined to compensate for the zirconia sintering. The total expansion of the gypsum used to make the final slip-cast mold (0.35%) was subtracted from the dimensions of the enlarged metallic model. This enlarged metallic model was duplicated with wax using a silicon mold fixed in a cast ring and embedded in dental stone. Following wax removal with hot water, the Y-TZP slip (Jahr Bioceramicas) was slip-cast in the mold and left to dry for 24 h. The gypsum was calcinated simultaneously with the pre-sintering cycle for the prototype zirconia abutment. After removal from the mold, the abutment was finished and fully sintered with subsequent density measurement (theoretical density assumed 6.12 g cm −3 ) .
The zirconia prototype abutment was scanned in a Skyscan 1172 micro-CT (Skyscan, Kontich, Belgium) equipped with an X-ray source configured to detect pores and flaws smaller than 8 μm in diameter. Software CT Analyser (Skyscan) was used to measure the three largest flaws detected in the abutment. A 3D qualitative analysis (Software 3D-Tool, Alps Electric Co. Ltd., Japan) was also used to measure porosity and to identify the crack shape, depth and plane.
3
Results
3.1
Finite element analysis
The FEA showed high stress concentrations at the beginning of the thread portion for both abutments during installation. In the first thread pitch of the prototype abutment, maximum tensile stresses of around 97.6 MPa were observed, with most stress values varying from 40.4 to 76.4 MPa ( Fig. 1 A). The titanium screw of the conventional abutment showed von Mises stress concentration values varying from 25.0 to 44.5 MPa in the first thread pitch ( Fig. 1 B). In this abutment, tensile stress concentrations were also observed in the apical margin of the tapered connection.
After simulation of one incisal bite, both abutments showed maximum principal stress concentration in the cervical region, where their tapered connections start. Of these stresses, the tensile ones were located on the side where the load was applied, while the compression stresses were located on the opposite side ( Figs. 2A and 3A ). For the prototype abutment, bite simulation resulted in tensile stress values of approximately 109 MPa ( Fig. 2 B) and compression stresses of approximately 114 MPa ( Fig. 2 C). As observed for the conventional abutment, this analysis showed tensile stresses of approximately 200 MPa ( Fig. 3 B) and compression stresses of 190 MPa ( Fig. 3 C). Relatively high tensile stresses (∼200 MPa) were observed in the coronal region of the loaded side, and von Mises stress concentration was noted at the bottom of the fixing screw head (70–90 MPa) and stem (20–40 MPa) ( Fig. 3 D).
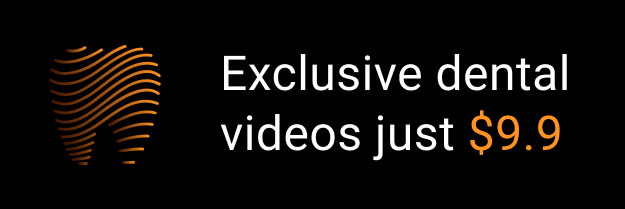