Abstract
Objective
The purpose of this study was to investigate a range of variables affecting the synthesis of a miserite glass-ceramic (GC).
Methods
Miserite glass was synthesized by the melt quench technique. The crystallization kinetics of the glass were determined using Differential Thermal Analysis (DTA). The glasses were ground with dry ball-milling and then sieved to different particle sizes prior to sintering. These particle sizes were submitted to heat treatment regimes in a high temperature furnace to form the GC. The crystal phases of the GC were analyzed by X-ray diffraction (XRD). Scanning electron microscopy (SEM) was used to examine the microstructure of the cerammed glass.
Results
XRD analysis confirmed that the predominant crystalline phase of the GC was miserite along with a minor crystalline phase of cristobalite only when the particle size is <20 μm and the heat treatment at 1000 °C was carried out for 4 h and slowly cooled at the furnace rate. For larger particle sizes and faster cooling rates, a pseudowollastonite crystalline phase was produced. Short sintering times produced either a pseudowollastonite or xonotolite crystalline phase.
Significance
The current study has shown that particle size and heat treatment schedules are major factors in controlling the synthesis of miserite GC.
1
Introduction
Glass-ceramics are polycrystalline materials containing a residual glass phase formed by the controlled devitrification of a glass. They have the potential to possess a fine grained and randomly oriented crystal structure, associated with little or no porosity and good mechanical properties . The crystal numbers, sizes and growth rates are controlled by the time and temperature used in the ceramming heat treatment . Some GCs, as described by Beall , are based on chain silicates such as jade minerals nephrite and jadeite that are well known for their excellent strength and resistance to crack propagation. These GCs have similar microstructures of randomly oriented interlocked rod or blade-shaped crystals, which provide the basis for several families of GCs with high fracture toughness. Miserite is a member of this family of chain silicates . It is regarded as a complex chain silicate. It has been previously described as triclinic structure with the P 1 space group, a = 10.1 Å, b = 16.014 Å, c = 7.377 Å, Z = 2, α = 96.42°, β = 111.15°, γ = 76.57°. Its appearance varies from red to brown, pink with a slight violet and transparent to translucent. The ideal mineral formula for miserite is (KCa 5 □ M(Si 2 O 7 )(Si 6 O 15 )F), where □ denotes a vacancy within the structure .
Pinckney et al. have fabricated a miserite GC with promising properties. They pointed out that the microstructure of the highly crystalline miserite GC was typically comprised of interlocked, lath or long shaped miserite crystals with evidence of cleavage, resulting in an abraded flexural strength as high as 235 MPa and fracture toughness value of ≥ 3.0 MPa m 1/2 . It has been shown that miserite can be crystallized via both volume/bulk and surface crystallization depending on the chemical compositions . The percentages of the constituents and the thermal history of the glass controls the crystallization behavior when the glass contains K 2 O–CaO(CeO 2 )–SiO 2 –F system . It has been reported that particle size and the composition of the parent glass have a major effect in the crystallization process . For surface nucleation, the glass can potentially benefit the surface glass grain and the interior surface remains glassy . Miserite can be used as a potential biomaterial, since miserite has good mechanical properties and can be used for applications where mechanical strength and stability are required . However, to date there has been no detailed scientific studies available to show factors controlling miserite formation. The objective of the present study was to determine the effect of particle sizes and heat treatment schedules, on the formation of miserite GC.
2
Materials and methods
2.1
Glass formulation and manufacture
The miserite forming glass for this study was derived from the stoichiometric formulation given by Pinckney et al. . A batch of glass was synthesized using the reagent grade raw materials listed in Table 1 . A batch to produce 300 g of glass was prepared, placed in a Zirconia Grain Stabilized (ZGS) platinum crucible and melted in an electric furnace (Vecstar VF2, UK) preheated to 1450 °C for 3 h. The glass melt was then quenched rapidly into water to obtain a frit. The resulting glass frit was dried for 4 h in an electric furnace at 150 °C prior to use. The frit was placed in 12 ml zirconium oxide grinding jar and dry ground in a planetary ball-milling machine (Retsch PM100, Germany) for 2 h at 450 rpm and sieved to produce a range of particle sizes. Sieving was performed by placing two different sieving sizes (>20 on bottom <45 μm on top) of each other and covered. It was placed on the sieve shaker (Minor, Endecotts, UK) for 15 min, sample in between was then collected.
Glass components | Moles | Weight % | Source ofchemicals (batch) | Amount (g) |
---|---|---|---|---|
SiO 2 | 63 | 59.4 | SiO 2 | 178.20 |
CaF 2 | 11 | 13.0 | CaF 2 | 39.00 |
K 2 O | 5 | 7.6 | K 2 CO 3 | 33.45 |
CaO | 20 | 18 | CaCO 3 | 96.37 |
Y 2 O 3 | 0.5 | 1.4 | Y 2 O 3 | 4.20 |
Al 2 O 3 | 1 | 0.6 | Al 2 O 3 | 1.80 |
100.5 | 100.0 | 353.02 |
2.2
DTA analysis
A glass that had been ground down to <20 μm was used to determine the glass transition (Tg) and crystallization temperature (Tc) using differential thermal analysis (DTA) (Perkin Elmer Diamond DT/TGA, USA). A 10 mg sample of the ground glass (<20 μm and >100 μm) was heated in a platinum crucible at a 10 °C min −1 heating rate to 1100 °C and held for 2 h before furnace cooling. The same weight of calcined Al 2 O 3 was used as a reference.
2.3
Heat treatment schedules and phase analysis
Samples having particle sizes <20 μm, >20 < 45 μm, >45 < 100 μm, and >100 μm were prepared using planetary ball-milling and sieved as described previously. Surface nucleation procedure was employed in this study. The glass particle sizes were converted to GCs by heat treatment in an electric furnace (UF2, Lenton Thermal Design, UK). All heat treatments were carried out at a heating rate of 10 °C/min at 1000 °C but two cooling rates with various durations were used as described in Table 2 . A silica pestle and mortar was utilized to break sample only for 4 h sintered GC having the smallest particle size then sieved as described previously. Sieved samples were placed on aluminum specimen holder for X-ray powder diffraction (XRD) analysis.
Particle sizes (μm) | Holding time (h) | Cooling rate (°C/min) | |
---|---|---|---|
<20 | 4 | Furnace rate | 10 |
<20 | 2 | Furnace rate | 10 |
<20 | 1 | – | 10 |
<20 > 45 | 4 | Furnace rate | 10 |
<45 > 100 | 4 | Furnace rate | 10 |
>100 | 4 | Furnace rate | 10 |
Crystalline phase analysis was undertaken after heat treatment by using XRD (Philip PW 1830) with Cu Kα radiation λ = 0.15406 nm) and accelerating voltage of 50 kV between 2 θ values of 10–70°, using a step scanning technique with a fixed step of 0.05° and a scan rate of 1°/min. Data was analyzed using STOE WinXPOW search and match software (STOE & Cie GmbH, Darmstadt, Germany) in conjunction with Joint Committee in Powder Diffraction Standards (JCPDS) for miserite [JCPDS-23-125], cristobalite [JCPDS-27-605], pseudowollastonite [JCPDS-74-874] and xonotolite (calcium silicate hydrate) [JCPDS-23-125]. All the tests carried out in the current work were from the same batch of material.
Scanning electron microscopy (SEM) (Philips XL-20, Eindhoven, Netherland) was carried out to examine the fractured surface of the GCs to analyze the microstructure. The SEM samples were prepared by mixing glass powder with VITA-modeling fluid to produce a slurry and packed into 12 mm diameter, 2 mm thick silicone molds and dried using a tissue. Discs were placed on an alumina boat for heat treatment in an electric furnace (UF2, Lenton Thermal Design, UK). For SEM, discs were broken by hammer and attached to aluminum stub (12.5 mm diameter) by double-sided carbon adhesive and coated with gold.
2
Materials and methods
2.1
Glass formulation and manufacture
The miserite forming glass for this study was derived from the stoichiometric formulation given by Pinckney et al. . A batch of glass was synthesized using the reagent grade raw materials listed in Table 1 . A batch to produce 300 g of glass was prepared, placed in a Zirconia Grain Stabilized (ZGS) platinum crucible and melted in an electric furnace (Vecstar VF2, UK) preheated to 1450 °C for 3 h. The glass melt was then quenched rapidly into water to obtain a frit. The resulting glass frit was dried for 4 h in an electric furnace at 150 °C prior to use. The frit was placed in 12 ml zirconium oxide grinding jar and dry ground in a planetary ball-milling machine (Retsch PM100, Germany) for 2 h at 450 rpm and sieved to produce a range of particle sizes. Sieving was performed by placing two different sieving sizes (>20 on bottom <45 μm on top) of each other and covered. It was placed on the sieve shaker (Minor, Endecotts, UK) for 15 min, sample in between was then collected.
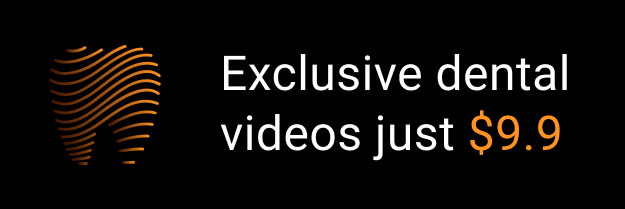