Graphical abstract
Highlights
- •
GeO 2 increased the degradability of 0.48- xSiO 2 , xGeO 2 , 0.36ZnO, 0.16CaO glasses.
- •
Increased GeO 2 reduced initial GIC viscosity and slowed cement setting.
- •
Increased GeO 2 delayed initial crosslinking of GIC matrix by divalent cations.
- •
GeO 2 had little impact on 24h biaxial flexural strength.
- •
Complex species proposed as mechanism to delay but not impair GIC matrix formation.
Abstract
Objective
To elucidate the mechanism(s) responsible for the profound impact germanium has on the setting reaction of zinc silicate glass ionomer cements (GICs).
Methods
Five <45 μm glass powder compositions (0.48- x SiO 2 , x GeO 2 , 0.36 ZnO, 0.16 CaO; where x = 0.12, 0.24, 0.36, 0.48 mol. fraction) were synthesized. Glass degradation was assessed under simulated setting conditions using acetic acid from 0.5 to 60 min, monitoring the concentrations of ions released using ICP-OES. Subsequently, GICs were prepared by mixing fresh glass powders with polyacrylic acid (PAA, Mw = 12,500 g/mol, 50 wt% aq. solution) at a 1:0.75 ratio. Cement structure and properties were evaluated using ATR-FTIR and rheology (for 60 min), as well as 24 h biaxial flexural strength.
Results
Reduced Si:Ge ratios yielded faster degrading glasses, yet contrary to expectation, the corresponding ATR-FTIR spectra indicated slower crosslinking within the GIC matrix. Rheology testing found the initial viscosity cement pastes reduced with decreased Si:Ge, and Ge containing cements all set significantly slower than the Si based GIC. Interestingly, biaxial flexural strength remained consistent regardless of setting behavior.
Significance
This counter-intuitive combination of behaviors is attributed to the presence of a chemical complex species specific to Ge-containing glasses that delays, but does not hinder, the formation of the GIC matrix. These findings embody chemical complex species as a mechanism to decouple glass reactivity from cement setting rate, a mechanism with the potential to enhance the utility of GICs in both dental and orthopaedic applications.
1
Introduction
Glass ionomer cements (GICs) demonstrate an innate relationship between handling characteristics and mechanical behavior. Both of these properties are highly dependent on the reactivity of the glass, and altering one often has a reciprocal effect on the other . GICs are the product of mixing a basic glass powder with an aqueous solution of polyalkenoic acid. Initial setting of the cement results from the formation of a polysalt matrix produced as multivalent cations (e.g. Al 3+ , Ca 2+ , Zn 2+ leached from the acid degradable glass) crosslink the polyanion chains of the deprotonated acid . After the initial set (i.e. gelation), GICs continue to harden over time due to continued crosslinking and as hydrated silicate or phosphate networks are formed . This setting reaction serves as the origin for the innate relationship between the handling and mechanical properties of GICs. Setting times can be adjusted by controlling the rate and the extent to which the glass degrades, but mechanical integrity is dependent on the number and strength of the metal-carboxylate crosslinks within the matrix . This imbalance is present in both conventional GICs (i.e. those comprising aluminosilicate glasses) used in dentistry , and aluminum-free GICs (e.g. zinc silicates) proposed for various orthopaedic applications . For conventional cements, this issue has been practically circumvented through the application of fluoride-containing glasses and or the use of (+)-tartaric acid as an additive in GIC systems . However for the aluminum-free compositions, this correlation has yet to be adequately addressed and represents a fundamental obstacle towards their clinical applicability.
The authors have previously reported on the unexpected findings that a full replacement of SiO 2 with GeO 2 in zinc silicate glasses significantly extends the setting time of GICs while maintaining their strength . These slow setting and high strength characteristics have potential implications to the use of GICs in both dental and orthopaedic applications, but are completely counterintuitive given the innate relationship between handling and mechanical performance described above. Current knowledge regarding the impact of germanium (Ge) on the GIC setting reaction is limited, as only discrete data derived from the assessment of handling characteristics (i.e. working and setting times), of cement systems comprising overly complex glasses have been obtained . The present study addresses this knowledge gap by examining various stages of the cement setting reaction over time in simplified Ge-modified zinc silicate GIC systems. Specifically, (i) the assessment of glass reactivity by profiling glass degradation rates under simulated setting conditions; (ii) profiling in situ structural changes as the GIC matrix is formed using attenuated total reflectance Fourier transform infrared spectroscopy; (iii) directly measuring the progression of GIC setting using rheology to obtain viscosity profiles; and (iv) monitoring the post-gelation hardening of the GIC matrix by measuring the biaxial flexural strength. The objective of this work is to elucidate the mechanism(s) associated with the delayed setting of GICs containing Ge.
2
Experimental
2.1
Glass synthesis
Five experimental glasses (BD1-5) were synthesized with molar compositions of: (0.48- x ) SiO 2 , x GeO 2 , 0.36 ZnO, 0.16 CaO; where x = 0.12, 0.24, 0.36, 0.48. Analytical grade reagents silica, germanium dioxide, zinc oxide and calcium carbonate (Sigma–Aldrich, Canada) were weighed out and blended together for 1 h in a mechanical mixer. Post-mixing, powder compositions were packed into platinum crucibles (Alfa-Aesar, USA) and fired (1500 °C, 1 h) in a high temperature furnace (Carbolite RHF 1600, UK) then subsequently quenched in water at room temperature. The resultant glass frit was dried overnight (120 °C) then ground in a planetary ball mill (Fritsch Pulverisette 7, Germany) and sieved to retrieve a particle size less than 45 μm. All glass powders were subsequently annealed in platinum crucibles in a high temperature furnace at T g – 30 °C for 3 h and left to furnace cool ( T g provided in Table 1 ). All prepared glass powders were stored in a desiccator for subsequent analysis.
Si: Ge Ratio | SiO 2 | GeO 2 | ZnO | CaO | T g [°C] | |
---|---|---|---|---|---|---|
BD1 | 1:0 | 0.48 | 0 | 0.36 | 0.16 | 673 |
BD2 | 3:1 | 0.36 | 0.12 | 0.36 | 0.16 | 653 |
BD3 | 1:1 | 0.24 | 0.24 | 0.36 | 0.16 | 631 |
BD4 | 1:3 | 0.12 | 0.36 | 0.36 | 0.16 | 620 |
BD5 | 0:1 | 0 | 0.48 | 0.36 | 0.16 | 597 |
2.2
Differential scanning calorimetry
The glass transition temperature ( T g ) for each glass composition was determined using a differential scanning calorimeter (Netzsch STA 409PC, USA). Approximately 30 mg of glass powder was placed into a platinum closed pan with the reference pan left empty. Samples were heated at 10 °C min −1 to 1000 °C. Proteus Thermal Analysis software (Netzsch Instruments, USA) was used for data analysis with T g taken as the point of inflection.
2.3
X-ray diffraction
Prior to heat treatment, glass powders were analyzed with an x-ray diffractometer (Bruker, D8 Advanced, Canada) equipped with a LynxEye silicon strip detector and Cu Kα radiation generated at 40 kV and 40 mA. Specimens were pressed in round polymethyl methacrylate holder and exposed to x-ray beam incident at 5° with the detector collecting scatters between 5° < 2θ < 100° over 950 s.
2.4
Glass ion release profiles under simulated setting conditions
To simulate the setting process of a GIC, each experimental glass was mixed with acetic acid for 0.5, 1, 2, 5, 10, 15, 30, and 60 minutes and concentration of released ions were subsequently measured, similar to the method described by Wasson . Extracts ( n = 3 per glass per time point) were prepared by mixing 0.15 g of annealed glass powder with 10 mL of 2.8 M aqueous acetic acid (Sigma-Aldrich, Canada), with a starting pH of 2.2 (i.e. typical pH level at the start of GIC mixing ) in 15 mL polystyrene tubes. Samples were mixed using a rotational mixer (Rotamix, ATR Inc., USA) at 1 Hz for the time periods of 0.5, 1, 2, 5, 10, 15, 30, and 60 min at 22 °C, then immediately centrifuged for 1 min after which 5 mL of extract was drawn off the top of each sample for ICP-OES analysis.
2.5
ICP-OES
Ion release extracts were analyzed using inductively coupled plasma optical emission spectroscopy (ICP-OES). Extracts were diluted at a 1:100 ratio in 2% aqueous nitric acid (Sigma–Aldrich, Canada) for ICP-OES analysis. An Optima DV8000 ICP-OES system (Perkin–Elmer, Canada) was calibrated with certified solutions (Perkin–Elmer, Canada) and used to measure the concentration of Si, Ge, Zn 2+ , and Ca 2+ ions released into the acetic acid solution. From the measured concentrations of each ion, the percentage release of each component was calculated according to equation 1, where numerator is the concentration of Y as measured in the extract solution and denominator is the theoretical mole fraction of Y ( Table 1 ), where Y represent either Ge, Si, Zn 2+ , or Ca 2+ . The release profiles of each ion were modeled as one-phase associations with the y-intercept set to zero using statistical software (Prism 6, Graph Pad, USA).
2.6
Cement preparation
Cements derived from BD glasses were prepared by mixing annealed glass powders with 50 wt% aqueous solution of polyacrylic acid (PAA) with a molecular weight of 12,500 g mol −1 (Advanced Healthcare, UK) and deionized water at a ratio of 1:0.75. Mixing was complete within 30 s. The naming convention for these cements was cBDZ, where Z identifies the parent glass (e.g. cBD1 is the cement derived from BD1 glass).
2.7
ATR-FTIR of Setting GIC
Attenuated total reflectance Fourier transform infrared spectroscopy (ATR-FTIR) was used to examine the structure of cements as they set. Ninety seconds from the commencement of mixing cement components, their contiguous pastes were placed directly on a temperature controlled diamond ATR element (Golden Gate, Specac, USA) maintained at 22 °C. Cement structures were probed using an infrared spectrometer (Tensor 27, Bruker, USA); the final spectra at each time point were recorded as the average of 17 runs collected over one minute. Each run consisted of 32 scans in the mid-IR region (400–4000 cm −1 ) at resolution of 4 cm −1 . Spectra were collected at 2, 5, 10, 15, 30, and 60 minutes after the commencement of cement mixing. The resulting spectra ( Fig. 3 ) represent the average of n = 3 replicates for each cement composition. To identify and isolate potential interactions between Ge and PAA, both aqueous PAA alone and aqueous PAA mixed with crystalline powder GeO 2 (Sigma Aldrich, Canada) in accordance with the methodology of Section 2.4 , were examined with ATR-FTIR under the conditions described above.
To assess the progress of GIC setting, the ratio between c. 1700 cm −1 and c. 1550 cm −1 band heights were calculated from each spectrum identified in Fig. 3 , where the band heights were taken as the absorbance magnitudes of the spectra with a horizontal baseline. For clarity, each spectrum is averaged from three replicates, where each replicate comprises 17 runs , and each run consists of 32 scans. The 1700 cm −1 band corresponds to C O in the un-reacted carboxyl (COOH). The bands in the range of 1537–1562 cm −1 correspond to metal-carboxylate structures (COO − M z+ ) identified in Table 3 . The difference in the COO − M z+ /COOH band height ratio, as a function setting time (at 2, 5, 10, 15, 30, and 60 min), was defined as per equation 2 (graphically represented in Fig. 1 ).
R a t e o f C O O − M z + f o r m a t i o n = C O O − M z + C O O H f i n a l − C O O − M z + C O O H i n i t i a l 1 minute
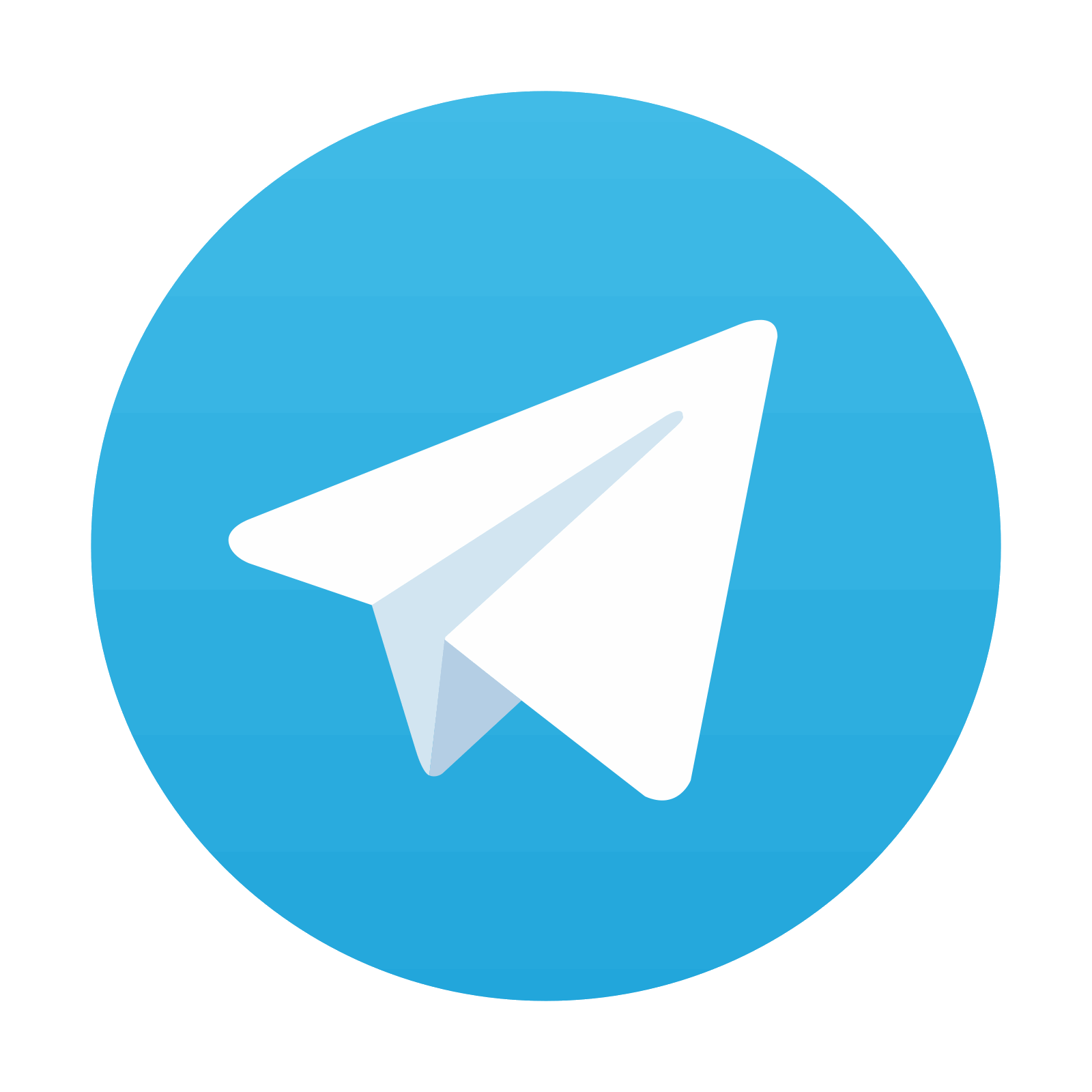
Stay updated, free dental videos. Join our Telegram channel

VIDEdental - Online dental courses
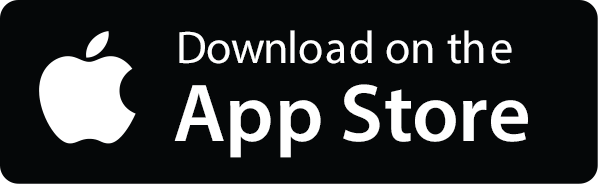
