Abstract
Objectives
To test the hypotheses that shear bond strength ( σ s ) and contact angle ( ) are influenced by the thermal expansion/contraction behavior of bilayered all-ceramic systems.
Methods
Glass-infiltrated ceramics (A – In-Ceram ALUMINA) and zirconia-reinforced alumina (Z – In- Ceram ZIRCONIA) were veneered with feldspathic ceramics (7 – VM7; 9 – VM9; 13 – VM13), yielding 6 experimental groups. Surface roughness (Ra) of A and Z core ceramic disks (12 mm diameter × 1.2 mm high) was measured to assure that values were similar. A cylinder of veneer (2 mm diameter × 2 mm high) was fired onto the center of all core disks, cooled under identical conditions and tested for σ s to failure ( n = 20). For the evaluation ( n = 10) similar specimens (veneer 1 mm high) were overfired to develop an equilibrium that was then measured from digital images (AutoCAD 2006). Published thermal expansion data were used.
Results
The mean values of σ s (MPa) and (°) for the core-veneer ceramic groups were, respectively: A7 (19.4 ± 4.7; 49 ± 4.7); Z7 (23.4 ± 6.2; 56 ± 4.9); A9 (0.9 ± 1.6; 55 ± 5.8); Z9 (9.8 ± 5.7; 59.8 ± 2.9); A13 (0; 70 ± 6.0); Z13 (0; 67.2 ± 6.3). As the difference in coefficient of thermal expansion (coreveneer) increases, the value increases ( r = 0.95) and the σ s value decreases ( r = −0.92), p ≤ 0.01.
Conclusion
The contact angle measurement and the shear bond strength test of core-veneer ceramics are influenced by the thermal expansion behavior of these all-ceramic systems.
1
Introduction
Increases in the crystalline content (to 100% polycrystalline) and advancements in dental ceramics processing have made possible the replacement of metal alloys by ceramics in the frameworks of many fixed partial dentures . While all of these materials are more translucent than metal alloys, these high crystalline content ceramics (more than 40% of volume) are often not translucent enough to achieve tooth-like optical properties . Thus, many all-ceramic restorations are covered by a veneering ceramic (more translucent) to promote high aesthetics quality. However, these two ceramics often have significant differences in their chemistry and microstructure and, consequently, in certain mechanical properties especially the elastic modulus ( E ) and the coefficient of thermal expansion (CTE) .
The cooling rate (slow or rapid cooling), the viscosity, and the differences in CTE between core and veneer ceramics ( Δ α ) determine independent and distinct thermal behaviors such as the development of interfacial tensile and compressive stresses during cooling. It has been shown that fast cooling generates compressive residual stresses, while slow cooling tends to generate tensile residual stresses in the veneer layer . In general, global residual compressive stresses significantly increase the flexural strength of bilayer materials. However, this accumulated energy can be released when the system is submitted to the oral environment, propagating the pre-existent flaws at the margins, in the bulk or at the core/veneer interface that can result in delamination (chipping) of the veneering material .
Delamination of veneer ceramics is a mode of failure frequently observed in the clinical situation . Its occurrence is more prevalent when the ceramics have high E and large core/veneer CTE differences . Compatibility in ceramics is promoted by the ability of the veneer to both wet and flow into irregularities of the core ceramic surface increasing the bond strength between the materials . This wetting behavior (wettability) can be characterized using the measurement of the angle formed by the substrate surface (solid) and the tangent of interface that intercepts the 3 phases (liquid/solid//air) . The contact angle is a consequence of surface energy and molecular interactions across the core/veneer interface . Therefore contact angle values can be used as an indicator of total surface energy and wettability.
Ceramic manufactures use dilatometry to assess thermal compatibility, usually defined as core–veneer differences in CTE ≤ 1 × 10 −6 °C. However, as veneer delamination is still a common mode of failure of all-ceramics restorations, the core–veneer compatibility could be influenced not only by the thermal mismatch, but also by other physico-chemical interactions that occur at core/veneer interface.
To better understand these interactions, the purpose of this study was to test the hypotheses that the shear bond strength test ( σ s ) and the contact angle measurement ( ) are influenced by core–veneer thermal expansion behavior for bilayer all-ceramic systems.
2
Materials and methods
Feldspathic ceramics Vita VM7 (7) and Vita VM9 (9), which are indicated for veneering high crystalline content ceramic structures, a leucite-based ceramic Vita VM13 (13), used for metal–ceramic restorations, an alumina-based glass-infiltrated ceramic (Vita In-Ceram ALUMINA – A) and an alumina-based zirconia-reinforced glass-infiltrated ceramic (Vita In-Ceram ZIRCONIA – Z) were used in this study. Average chemical compositions of the core and veneering materials are presented in Table 1 .
Material | Average composition (in wt%) |
---|---|
In-Ceram Alumina a Batch: 1532 | Alumina powder: Al 2 O 3 (100) Alumina glass powder: Al 2 O 3 (14–17), SiO 2 (14-17) B 2 O 3 (12–15), TiO 2 (3–5), La 2 O 3 (39–48), CeO 2 (2–5), CaO (2–4) |
In-Ceram Zircônia a Batch: 0124 | Zirconia powder: Al 2 O 3 (67) ZrO 2 (33) Ce-stabilized Zirconia Glass powder: Al 2 O 3 (14–18), SiO 2 (14–18), B 2 O 3 (11–15), TiO 2 (2–7), La 2 O 3 (25–30), CeO 2 (6.10), CaO (4–8), ZrO 2 (1–4), Y 2 O 3 (2–6) |
Vita VM7 b Batch: 22970 | SiO 2 (66–70); Al 2 O 3 (15–16); K 2 O (10–11); Na 2 O (3–4); CaO (2–3), ZrO 2 (<1) |
Vita VM9 c Batch: 24690 | SiO 2 (60–64); Al 2 O 3 (13–15); K 2 O (7–11); Na 2 O (4–6); B 2 O 3 (3–5) |
Vita VM13 c Batch: 22970 | SiO 2 (59–63), Al 2 O 3 (13–16), K 2 O (9–11), Na 2 O (4–6) |
2.1
Specimen fabrication
Ninety ceramic discs (12 mm diameter × 1.2 mm thickness) were fabricated from each core ceramic, A and Z, in accordance to manufacturer’s instructions (Vita Zahnfabrik, Bad Sackingen, Germany).
To control the topography, 10 discs from each core ceramic were randomly selected and tested for mean surface roughness (Ra, in μm) using a surface profilometer (Surfcorder SE 1200, Kosaka-Lab). The profilometer was calibrated with cut-off ( λ c ) of 0.8 mm and tracing speed of 0.5 mm/s. A mean of three readings was calculated for each specimen.
The core discs were randomly divided into six groups according to the veneer ceramics of different degrees of thermal compatibility ( Table 2 ). The lower value of CTE, calculated from 500 °C to 25 °C by the manufacture, was used in this study. The differences in CTE ( Δ α ) of core-veneer ceramic combinations were calculated by subtracting the CTE values of core ( α c ) and veneer ( α v ) ( Δ α = α c − α v ). The CTE values considered for this study are presented in Table 2 and the Δ α values are shown in Table 3 .
Group | Core ceramic and CET value range a | Veneer ceramic and CET value range a | Compatibility |
---|---|---|---|
A7 | A—(7.2–7.6) × 10 −6 K −1 | VM7—(6.9–7.3) × 10 −6 K −1 | Strong |
A9 | A—(7.2–7.6) × 10 −6 K −1 | VM9—(8.8–9.2) × 10 −6 K −1 | Poor |
A13 | A—(7.2–7.6) × 10 −6 K −1 | VM13—(13.1–13.6) × 10 −6 K −1 | Incompatible |
Z7 | Z—(7.6–7.8) × 10 −6 K −1 | VM7—(6.9–7.3) × 10 −6 K −1 | Strong |
Z9 | Z—(7.6–7.8) × 10 −6 K −1 | VM9—(8.8–9.2) × 10 −6 K −1 | Poor |
Z13 | Z—(7.6–7.8) × 10 −6 K −1 | VM13—(13.1–13.6) × 10 −6 K −1 | Incompatible |
a The lower CET value of each ceramic was used to calculate the Δ α shown in Table 3 .
Groups | Δ α (×10 −6 K −1 ) | σ s (MPa) | Θ (°) | Mode of failure (no) | ||||
---|---|---|---|---|---|---|---|---|
Mean | SD | Mean | SD | C/V | V | C | ||
A7 | 0.3 | 19.4 A | 4.7 | 49.0 c | 4.7 | 1 | 19 | 0 |
A9 | 1.6 | 0.9 C | 1.6 | 55.0 bc | 5.8 | 14 | 6 | 0 |
A13 | 5.9 | 0 D | 0 | 70.1 a | 6.0 | 20 | 0 | 0 |
Z7 | 0.7 | 23.4 A | 6.2 | 56.0 b | 4.9 | 1 | 19 | 0 |
Z9 | 1.2 | 9.8 B | 5.7 | 59.8 b | 2.9 | 2 | 18 | 0 |
Z13 | 5.5 | 0 D | 0 | 67.2 a | 6.3 | 20 | 0 | 0 |
a Values followed by similar letters in the same column did not present statistical difference ( p ≥ 0.05).
2.2
Shear bond strength test
The veneer ceramic powder was mixed with modeling liquid (Vita Modeling Liquid, Vita-Zahnfabrik) and applied in cylinder shape (2 mm high × 2 mm diameter) onto the core ceramic disc using a specially designed split mold. The excess of liquid was removed with absorbent paper and the dimensions were checked ( Fig. 1 ). The veneer ceramics were sintered in a calibrated furnace (Vita Vacumat 40, Vita-Zahnfabrik) in accordance to the manufacturer’s instructions.
The specimens ( n = 20) were mounted using the Bencor Multi-T device (Danville Engineering Inc., San Ramon, CA, USA) in a universal testing machine (EMIC DL2000, São José dos Pinhais, PR, Brazil) and loaded to failure in shear ( σ s ). The load was applied as close to the veneer–core interface as possible at a crosshead speed of 0.5 mm/min. The load at fracture ( F , in N) was recorded and the adhesion area ( A , in mm 2 ) was measured. The σ s results (in MPa) were calculated using σ s = F/A.
Fracture surfaces were analyzed by light microscopy (Olympus CBB, Tokyo, Japan), with 40× magnification. The mode of failure was classified as follows: adhesive failure (C/V—delamination of the veneer ceramic from the core ceramic), cohesive failure of veneer ceramic (V—veneer ceramic remains on the core surface) and cohesive failure of core ceramic (C—fracture of core ceramic).
2.3
Contact angle measurement
The same split mould was used to prepare ten specimens of each experimental group. The dimensions of the veneer ceramic cylinder before sintering were 1 mm diameter and 2 mm high.
Two distinct modified firing procedures for the veneer ceramics were necessary to promote equilibrium contact angle evaluation. For the first firing, the time of final temperature was calibrated as 30 min. At the second firing, the final firing temperatures of 7, 9 and 13 veneer ceramics were raise to 1070 °C, 1070 °C and 1040 °C, respectively, which are 160 °C above the final temperature recommended by the manufacturer for sintering of the ceramics. Other sintering stages were maintained according to the manufacturer’s instructions. Photographs of representative specimens before and after the veneer firing procedure are shown in Fig. 2 .
Photographs were taken after sintering, first at a right angle with the long axis of the veneer ceramic cylinder and then parallel to the cylinder axis. The camera (Nikon ® Coolpix 5700, Nikon Inc, Japan) was fixed in a special device to standardize the distance between the objective lens and the specimen (30 mm). The optic zoom tool was used to obtain a specimen image with 8× magnification and high quality. The photographs were recorded in JPEG (Joint Photographic Experts Group) format with no alterations.
Specimens images were analyzed using a computer program (AutoCAD 2006, Z54.10 version, Autodesk Inc, EUA) using an angular dimension tool to measure the contact angle ( ) as described above. Right and left angles were measured and registered in order to obtain a mean value of each specimen.
2.4
Statistical analysis
The results were analyzed using Sigmastat 3.01 (Systat INC) software with a significance level of 95% ( p ≤ 0.05). Student’s t -test was performed for comparison between the mean Ra values of A and Z ceramics. Non-parametric test of Kruskal–Wallis was performed to compare the mean σ s values. The data were analyzed by one-way analysis of variance (ANOVA) and Tukey multiple comparisons test (95%) in order to determine the differences among groups. Correlation coefficient ( r ) was used to evaluate the association between the mean values of σ s , and Δ α .
2
Materials and methods
Feldspathic ceramics Vita VM7 (7) and Vita VM9 (9), which are indicated for veneering high crystalline content ceramic structures, a leucite-based ceramic Vita VM13 (13), used for metal–ceramic restorations, an alumina-based glass-infiltrated ceramic (Vita In-Ceram ALUMINA – A) and an alumina-based zirconia-reinforced glass-infiltrated ceramic (Vita In-Ceram ZIRCONIA – Z) were used in this study. Average chemical compositions of the core and veneering materials are presented in Table 1 .
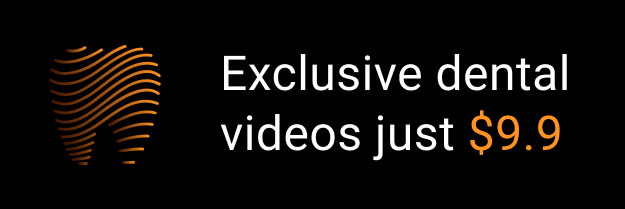