Introduction
The objective of this research was to evaluate and compare linear and surface accuracy of dental models fabricated using 3 different vat photopolymerization printing units: digital light synthesis (M2 Printer; Carbon, Redwood City, Calif), digital light processing (Juell 3D Flash OC; Park Dental Research, New York, NY), and stereolithography apparatus (Form 2; Formlabs Inc, Somerville, Mass), and a material jetting printing unit: PolyJet (Objet Eden 260VS; Stratasys, Eden Prairie, Minn).
Methods
Maxillary and mandibular dental arches of 20 patients with the American Board of Orthodontics Discrepancy Index scores ranging between 10 and 30 were scanned using an intraoral scanner. Stereolithographic files of each patient were printed via the 3-dimensional (3D) printers and were digitized again using a 3D desktop scanner to enable comparisons with the original scan data. One-sample t test and linear regression analyses were performed. To further graphically examine the accuracy between the different methods, Bland-Altman plots were computed. The level of significance was set at P <0.05.
Results
Bland-Altman analysis showed no fixed bias of one approach vs the other, and random errors were detected in all linear accuracy comparisons. When a 0.25 mm tolerance level was deemed acceptable for any positive or negative surface changes, only the models manufactured from digital light processing and PolyJet units showed more than 97% match with the original scans.
Conclusion
The surface area of 3D printed models did not yield an utterly identical match to the original scan data and was affected by the type of printer. The clinical relevance of the differences observed on the 3D printed dental model surfaces requires application-specific judgments.
Highlights
- •
3D printed models from 3 units were printed using commercial software.
- •
Statistical evaluations showed no fixed bias of one approach vs the other.
- •
Random errors were detected in all comparisons.
- •
Surface deviations—showed significant differences.
- •
Always consider the degree of surface mismatch in 3D printing of orthodontic models.
Additive manufacturing technologies such as 3-dimensional (3D) printing have become a popular venue for orthodontists recently. By using various techniques and printing devices, it is possible to build 3D dental models and appliances via the sequential addition of multiple thin layers. Therefore, the International Organization for Standardization defines the term additive manufacturing as the general term for those technologies that, on the basis of a geometric representation, create physical objects by successive addition of material.
A variety of additive manufacturing processes enable the production of 3D objects and include vat photopolymerization, material extrusion, binder jetting process, material jetting, powder bed fusion, and sheet lamination. Additive manufacturing systems using vat photopolymerization, material extrusion, , binder jetting process, , and material jetting , , , , have broadly been used in orthodontic practice and evaluated for accuracy. Although some authors , , suggest the clinical acceptability of dental models produced by certain additive manufacturing systems, some reported that printed models were not comparable to stone models because of their contraction in the transverse dimension and limitation to accurately replicate the degree of crowding.
The findings from research studies should be interpreted carefully as all new developments require time and training for acquiring full competency with their use and materials involved in the application. In addition, some inconsistencies may exist between the additive manufacturing systems because of differences in their respective design and technology, , , layer thickness, , , and model-based design. Although the disagreements between different manufacturing systems may not be clinically relevant, it is important to understand the nature of their occurrence and take necessary measures in clinical applications accordingly.
Although complex 3D objects could be printed with intricate details with reduced material waste compared with machining, the slow and costly nature of additive manufacturing, together with the need for postprocessing, makes the process arduous and labor-intensive. Recently, an industrial type of vat polymerization unit that uses proprietary digital light synthesis (DLS) technology was introduced. According to the manufacturer (Carbon, Redwood City, Calif), the advantage of this system is the ability to produce parts with improved mechanical properties, resolution, surface finish, and streamlined postprocessing procedures. In this study, we aimed to evaluate and compare the linear and surface accuracy of dental models fabricated using the DLS technology with models from 2 other vat photopolymerization units (stereolithography apparatus [SLA] and digital light processing [DLP]) and a material jetting unit (PolyJet).
Material and methods
The study cohort was selected from a group of patients who presented for an initial records appointment. Maxillary and mandibular dental arches of 20 patients with the American Board of Orthodontics Discrepancy Index scores ranging between 10 and 30 were scanned using the iTero Element intraoral scanner (Align Technology, Santa Clara, Calif). All patients were in permanent dentition (aged 12-20 years) with no missing teeth or tooth anomalies. Once the scans were completed, the raw images were converted to stereolithographic (STL) file format using 3D imaging software (Dolphin Imaging and Management Solutions, Chatsworth, Calif) to arrange the models on the build platform. All models were oriented with the occlusal plane parallel to the platform and the occlusal surfaces facing away from it.
The prepared STL file for each patient was printed using 3 vat photopolymerization printing units: DLS (M2 Printer; Carbon), digital light processing (Juell 3D Flash OC; Park Dental Research, New York, NY), and SLA (Form 2, Formlabs Inc, Somerville, Mass) and a material jetting unit: PolyJet (Objet Eden 260VS; Stratasys, Eden Prairie, Minn). The characteristics of the printing units used in the study are shown in Table I . All printing units were calibrated at the beginning of the study in accordance with the manufacturer’s instructions, when applicable, and printer settings optimized by the manufacturer for each respective material were used. All dental models were manufactured with a horseshoe-shaped base but without the addition of supporting structures. Models were postprocessed in accordance with the manufacturer’s instructions for the respective systems and materials. After the manufacturing process, the models were digitized using a 3D desktop scanner (Ortho Insight 3D laser scanner; Motionview Software, Hixson, Tenn) and saved as STL files ( Fig 1 ). The digitization of the 3D-manufactured models enabled the comparison of linear and surface accuracy of the additive-manufactured models with respect to the original STL files.
Characteristics | Carbon M2 | Juell 3D | Form 2 | Objet Eden 260VS |
---|---|---|---|---|
Technology | DLS | DLP | SLA | PolyJet |
Layer thickness (μm) | 75 | 100 | 100 | 16 |
Average print time per model (min) | 28.5 | 11.6 | 42.4 | 30.8 |
Build size (inch) | 7.4 × 4.6 × 12.8 | 7.6 × 4.25 × 9.0 | 5.7 × 5.7 × 6.9 | 10.0 × 9.9 × 7.9 |

Linear measurements were carried out using the Netfabb additive manufacturing and design software (Autodesk, San Rafael, Calif). For the purposes of testing the linear accuracy based on hypothetical transverse contraction, the width measurements between the first premolars and molars from both the maxillary and mandibular arches were recorded. Measurements were made on unsectioned, shaded digital models of the STL files with the software’s built-in ruler tool to the nearest 0.01 mm. Surface accuracy measurements ( Fig 2 ) were performed with the original STL files serving as the comparative surface anatomy using the best-fit alignment feature of the Geomagic Control software (version 2015.3.1; 3D Systems, Inc, Rock Hill, SC). Surface registration was achieved using an automated best-fit alignment algorithm within the metrology software, which used 300 points for course alignment followed by refinement alignments using 1500 and 10,000 points. The best-fit alignment algorithm was applied for all samples in the study. After the registration protocol, the root mean square error of all points in the comparison and standard deviation of the differences between the reference digital model and manufactured model scan were recorded using the 3D comparison tool of the same software. A tolerance level of ±0.25 mm between the two-shell comparisons was deemed as clinically acceptable. Accordingly, the percentage of surface area match within the tolerance limits was computed. Finally, average positive and negative deviations (mm) were calculated for the reference and manufactured model pairs.

SPSS (version 25; IBM, Armonk, NY) was used for statistical analysis. Interpremolar and intermolar measurements performed on the digital scans of models from each additive manufacturing unit were paired with corresponding measurements of the original scan file. A 1-sample t test was used to test the hypothesis that there would be no difference between the paired sets of measurements. The test value was set at 0. No significant differences were found for any of these comparisons. Therefore, the 4 measurements obtained from the same model were combined to represent the DLS, DLP, SLA, and PolyJet units for further analysis. The Bland-Altman plots were computed for the paired comparisons of the 4 units. The analysis was used to visually demonstrate the agreement for measurement values between the measurements from the original scan file and the digital scans of models produced by the additive manufacturing units. The within-observer repeatability was evaluated using intraclass correlation analysis by repeating all of the measurements from 10 randomly selected models at a 1-month interval. Error study was performed using Dahlberg’s formula.
Furthermore, linear regression analyses were used to investigate whether there was a proportional bias in the data. In the comparison of average positive and negative deviations between the 2 shell pairs, no significant differences were found between the maxillary and mandibular models in each additive manufacturing group. Therefore, the data was combined. The differences between the additive manufacturing units were compared with a 1-way analysis of variance analysis. Multiple comparisons were made with the Bonferroni post-hoc test. The level of significance was set at P <0.05 for all tests.
Results
Repeatability for each paired measurement set was excellent, with the intraclass correlation coefficients ranging between 0.97 and 0.99. Operator error measurements varied between 0.06 mm to 0.32 mm. Table II represents the descriptive statistics for the linear arch width measurements. According to the 1-sample t test, there were no significant differences between any of the paired methods, which indicated a certain level of agreement between the additive manufacturing units tested. The Bland-Altman plots of the method comparisons are shown in Figures 3-6 . The Bland-Altman plots were used to visually demonstrate the agreement of measurements between the original digital models and scans of the additive-manufactured models. The difference and the mean between the 2 measurements were represented in the y- and x-axis of the plots, respectively. For each comparison, the bias is represented in red , whereas the positive and negative limits of agreement are represented in green lines. After the visual inspection of Figures 3-6 , it was evident that all comparisons were free of systematic disagreement. The mean difference values were scattered in a random manner; as such, none are higher (or lower) than those from the other by a constant amount. In short, the Bland-Altman analysis showed no fixed bias of one approach vs the other, and random errors were detected in all comparisons. The results of the linear regression analyses were shown in Table III . None of the comparisons displayed statistical significance for the t scores. This indicated that there was no proportional bias in any of these comparisons, and no method gave values that are higher (or lower) than those from the other by an amount that is proportional to the level of the measured variable. This meant that there was no trend for any of the mean difference values being above or below the mean bias level demonstrated in Bland-Altman scattergram plots.
Groups | Measurements | Minimum | Maximum | Mean | Standard deviation |
---|---|---|---|---|---|
Original 3D Scan | Max4 width | 6.25 | 8.62 | 7.46 | 0.61 |
Max6 width | 9.85 | 11.75 | 10.84 | 0.59 | |
Mand4 width | 6.06 | 8.14 | 7.27 | 0.55 | |
Mand6 width | 10.24 | 12.71 | 11.33 | 0.66 | |
DLS | Max4 width | 6.46 | 8.57 | 7.41 | 0.57 |
Max6 width | 9.63 | 11.99 | 10.8 | 0.6 | |
Mand4 width | 5.92 | 8.06 | 7.27 | 0.52 | |
Mand6 width | 10.19 | 12.67 | 11.22 | 0.67 | |
DLP | Max4 width | 6.57 | 8.54 | 7.47 | 0.56 |
Max6 width | 9.77 | 12 | 10.93 | 0.63 | |
Mand4 width | 6.15 | 8.11 | 7.43 | 0.52 | |
Mand6 width | 10.65 | 13.06 | 11.46 | 0.64 | |
SLA | Max4 width | 6.53 | 8.51 | 7.42 | 0.6 |
Max6 width | 9.56 | 11.87 | 10.78 | 0.6 | |
Mand4 width | 6.06 | 8 | 7.33 | 0.48 | |
Mand6 width | 10.19 | 12.74 | 11.23 | 0.69 | |
PolyJet | Max4 width | 6.2 | 8.38 | 7.42 | 0.62 |
Max6 width | 9.68 | 11.68 | 10.83 | 0.55 | |
Mand4 width | 6.22 | 7.99 | 7.3 | 0.48 | |
Mand6 width | 10.45 | 12.91 | 11.42 | 0.74 |
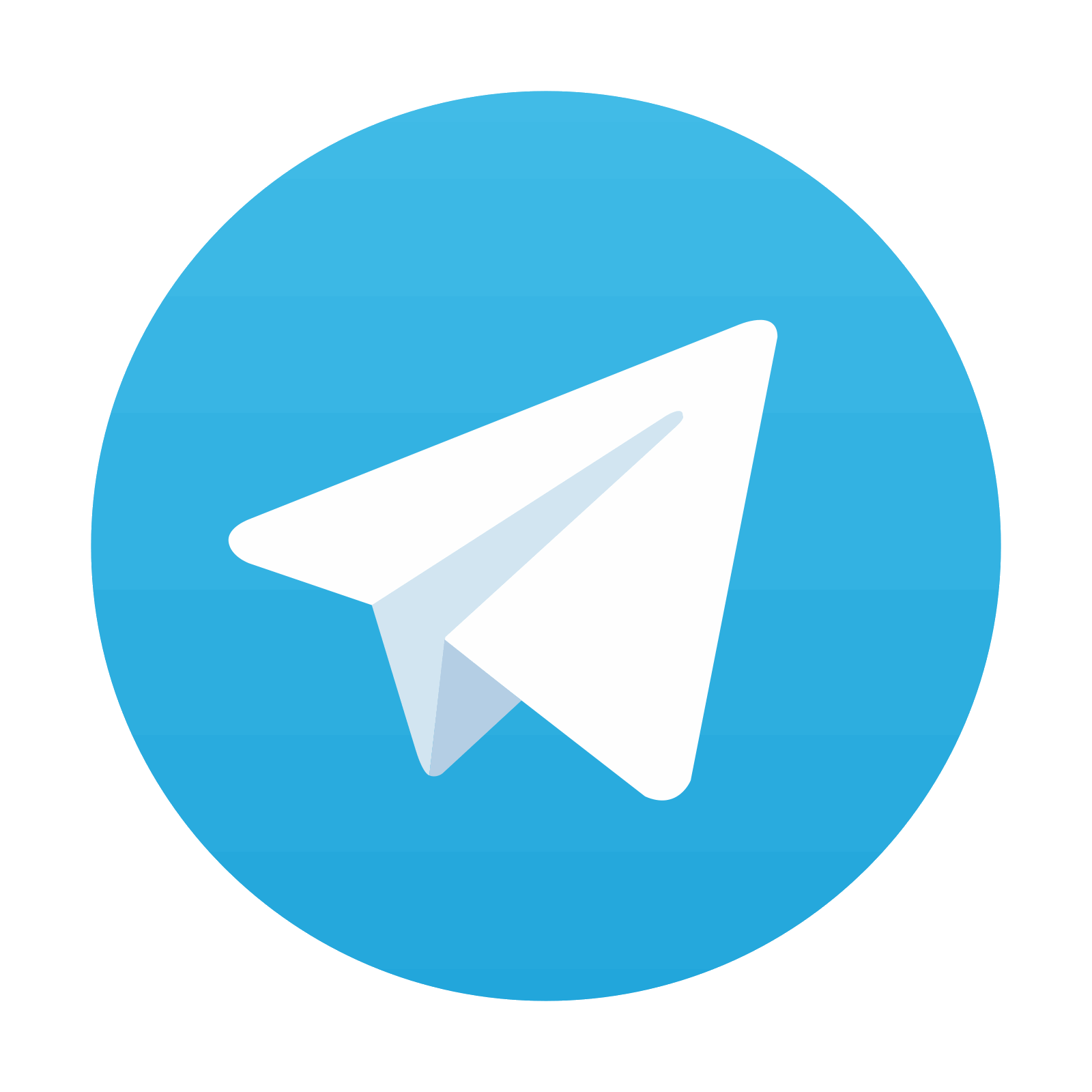
Stay updated, free dental videos. Join our Telegram channel

VIDEdental - Online dental courses
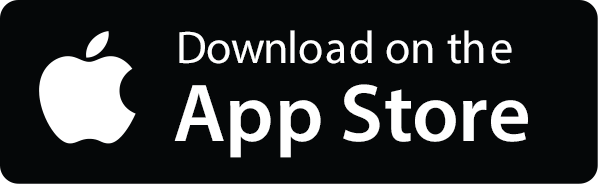

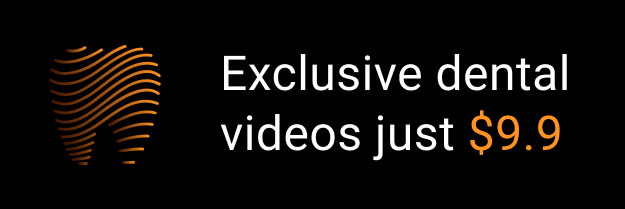