Abstract
Objectives
It is proposed that a non-uniform rational B-spline (NURBS) based solid geometric model of a ceramic crown would be a flexible and quick approach to virtually simulate root canal access cavities. The computation of strain components orthogonal to surface flaws generated during the drilling would be an appropriate way of comparing different access cavity configurations.
Methods
A μCT scan is used to develop a full 3D NURBS geometric solid model of a ceramic crown. Three different access cavity configurations are created virtually in the geometric model and there are then imported into proprietary finite element software. A linear analysis of the each crown is carried out under appropriate in vivo loading and the results are post-processed to carry out a quantitative comparison of the three configurations
Results
The geometric model is shown to be a flexible and quick way of simulation access cavities. Preliminary indications are that post processed strain results from the finite element analysis are good comparators of competing access cavity configurations.
Significance
The generation of geometric solid models of dental crowns from μCT scans is a flexible and efficient methodology to simulate a number of access cavity configurations. Furthermore, advanced post-processing of the primary finite element analysis results is worthwhile as preliminary results indicate that improved quantitative comparisons between different access cavity configurations are possible.
1
Introduction
Classical structural mechanics fails to produce an adequate elucidation of the stresses and strains developed in a system as geometrically complex as a grinding tooth. Naturally, the boundary of such a surface cannot be described by a singular component such as a beam or a plate, and therefore a computer simulation must be carried out. All physical phenomena are modeled mathematically as partial differential equations. It is rare that the solutions for these partial differential equations are trivial , but since the development of the computer, numerical solutions are now mainstream. For boundary value field problems, including structural mechanics, the finite element method (FEM) is the standard numerical approach. The ability of the FEM to accurately compute stress and strain fields has particular advantages in the field of restorative dentistry where an understanding of the deformation responses due to in vivo loading is of critical importance.
A very common procedure performed by dentists is root canal treatment (RCT). RCT is performed when the pulp becomes infected or damaged, causing pain to proliferate through the tooth. Indeed, this is such a common complaint that ‘root canal’ is a something of a vernacular synonym for serious discomfort and distress. Clinically, root canal pain is tackled by endodontic therapy, which involves any number of procedures that take place inside the tooth, the general principles of which have been traced as far back as 1826 . Studies have shown that the side-effects of crown fabrication and installation can cause irreversible pulp necrosis (tissue death), which may consequently necessitate RCT. In fact, a 3–25% pulpal necrosis rate has been recorded in teeth with full coverage fixed restorations over an 18–25 month period . It is further estimated that between 20% and 50% of all RCT is performed through complete coverage crowns .
1.1
Motivation
It has been known for quite some time that endodontic access itself can cause varying levels of distress to the crown due to subsequent in vivo loading. Flaws generated by the action of the drilling burs are hypothesized to ultimately develop into cracks and propagate causing failure in crowns. Recent studies have shown that the failure load of restorations post-access is independent of drilling implement or technique . Therefore, whether or not one selects a high efficiency diamond rotary cutting instrument or a tungsten carbide fissure burr has no appreciable effect, as some micro cracks will form, regardless of the instrument. The clinician has control over the following: geometry, location, number of access cavities and the filling material. Research into these parameters has not been very active and provides the motivation for this work. If recommendations of optimal access cavity configurations, alongside a choice of filling material, could be formulated, they would be clinically useful. Currently there is no conclusive body of research that has determined the correct restoration method and material; judgments based on 3D modeling could effect change as it offers a wide scope relative to biomedical research, a field in which it may be either prohibitively expensive to or ethically questionable to test on in vivo or even in vitro samples .
1.2
Purpose
This paper aims to demonstrate that a non-uniform rational B-spline (NURBS) based solid geometric model of ceramic crowns is a flexible and quick approach to virtually simulate root canal access cavities. Furthermore, it is proposed that tensor strain components orthogonal to surface flaws, rather that scalar strain quantities, are an appropriate way of comparing different access cavity configurations.
1.3
Paper summary
Section 2 will describe the development of the geometric model from a μCT scan of a representative dental ceramic crown and the virtual modeling of three different access cavity configurations. The geometric model is then imported into proprietary FE software and an in vivo loading scenario is applied and the results of the FE analyses are presented in Section 3 . Section 4 discusses the effectiveness of the geometric modeling approach presented and presents some preliminary results of a strain based post-processing methodology that better predicts the long term effect of low intensity cyclic loading on the crown. The conclusions are detailed in Section 5 .
2
Materials and methods
In any finite element analysis (FEA), there are four key factors that the analyst must consider in order to develop a sound model; geometry, material properties, loading and boundary conditions. To that end the modeling methodology used in this work will be illustrated under those headings.
2.1
Geometry
2.1.1
Acquisition
For the purposes of this work, a representative sample ceramic crown was created using the lost-wax technique in a dental laboratory in Cork University Dental School & Hospital. This crown is approximately 9.35 mm at its widest and 8.16 mm at its highest, and depicts the crown of a mandibular first molar, purposively selected as it is the most common tooth to undergo endodontic treatment . This tooth was scanned by a Scanco ® CT40 μCT device and the outputted data was saved in the scanner’s native format.
2.1.2
Data processing
A simple MATLAB ® procedure converted the original data to the more commonly used DICOM format. Each μCT slice is a greyscale image, 1024 × 1024 pixels in size, and has a 16-bit color depth. In total, 450 slices at a thickness of 0.02 mm were recorded amounting to approximately 950 MB of data. Therefore to facilitate visualization, a workstation with 16 GB of RAM operating on 64-bit Windows was used. It may be noticed that the data recovered from a μCT scan is raw and requires some basic image processing before 3D reconstruction is possible. In this work, all image processing and reconstruction work is undertaken in 3D Slicer , an open source medical visualization software package .
The main point of a 3D reconstruction from μCT imaging is to identify the structures of interest from each slice and assemble these into a 3D model. This process is commonly referred to as segmentation and it refers to the conglomeration of all points on the μCT slice that are of interest into one cogent structure known as a label map, which is simply a binary image superimposed over the original slice. In essence, one is designating particular areas of the μCT image that they want to include in the resulting model as the label map(s) that are used to create the 3D visualization. Note that there is the possibility of isolating several structures: one could simply create several label maps, based on areas of the slice of different radiodensity (the quality, which is analogous to corporeal, physical density). Commonly, dentists use μCT imagery to segment and create models encompassing all major structures in the tooth – enamel, dentin etc. This would be achieved by the use of several label maps. As this analysis is concerned with visualizing a ceramic crown, only a single label map is required.
Like much image processing, segmentation is an iterative process, the results of the initial segmentation effort may be seen in Fig. 1 . Further refining is necessary, as it is quite clear that the result of this operation leaves a rather noisy image. It can be seen that the edge of the label map is quite rough and there are many isolated pockets of noise (known as ‘islands’).
It is possible to edit the label map; using a combination of a Gaussian smoothing algorithm and island removal procedures, the image in Fig. 2 may be achieved. Once a succinct and accurately smoothed label map is created, the model making process can be started.
2.1.3
3D reconstruction
3D Slicer builds the model by collating all the refined label maps and, running the Marching Cubes algorithm it extracts a polygonal mesh from the isosurface created by the perimeter of the label map. Fig. 3 shows a screenshot of the finished model in the 3D Slicer software environment.
Following model generation, some simple post processing options are available at this stage, including decimation and smoothing. Decimation reduces the number of triangles by averaging the shapes of several small triangles into one larger triangle, which is of importance in reducing the mesh density and, hence, file size. The finalized model is outputted as a stereolithography (STL) file.
2.1.4
Parametric geometric model
The innovative step in this methodology was to move aside from the polygonal mesh to facilitate the creation of a realistic endodontic access cavity. By converting the polygonal mesh to a parametric geometric model, it is possible to adapt the geometry in a convenient work environment such as Autodesk Inventor . There are many options of parametric model, but by far the most flexible and mainstream are non-uniform rational B-spline (NURBS) models . Most computer aided design (CAD) and finite element analysis (FEA) software can manipulate and import them. In order to do this, the surfacing feature of Leios ® (a reverse engineering meshing software) was used to ‘wrap’ an air-tight surface of stitched together NURBS patches over the original 3D polygonal mesh ( Fig. 4 ).
This has a twofold benefit. Firstly, the geometry could be imported directly as into the FEA software Strand7 ® , which takes advantage of the advanced automesher and can create a congruent surface mesh of quadratic, or 6 node triangles, followed by a solid mesh of 10 node tetrahedra which accurately reflect the surface geometry. Polygonal meshes from reconstructions are for visualization purposes only, therefore 3 node linear elements (facets) suffice, however in an advanced FEA higher order elements are to be preferred . The second benefit is that, once in this CAD format, a whole host of possibilities are opened up editing the geometry of the model while using a software system such as Inventor ® .
Simple shapes; a rounded rectangle, an ellipse and two small loops were sketched in 2D and copied with each copy placed on either end of the tooth model (top and bottom). Using a loft method, a smooth continuous object was created, which formed the geometry of the access cavity and filling. A combination of the Boolean operations (subtract and add) was applied, which first cut the access cavity and subsequently re-filled the model with a separate solid object. This is demonstrated in Fig. 5 .
2.1.5
FE mesh
The final geometry, including the endodontic access, was saved and exported as a step (STP) file, a CAD file format which is suited to this form of solid modeling as it stores differing materials in a way that Strand7 can easily separate. Upon importing the geometry, a default clean was performed: this is worthwhile, as any small disconnections, imperceptible in the CAD environment, need to be seamed together and overall connectivity will be checked, a point emphasized by Magne . The same FE meshing process is applied as described previously in that a surface mesh is developed, followed by a solid element mesh.
At this juncture, it is important to interrogate the model to assess its quality, as visual inspection alone may not be enough to verify the competence. Of critical importance to solid meshes are the aspect ratio, which may be assessed by computing the determinant of the Jacobian matrix and the dihedral angle ratio of each solid element. Decisions to manually adapt the mesh or entirely re-mesh, refining problematic areas, can be better informed by using the checks mentioned. That being said, in meshes of this size (circa 60,000) and complexity, it is unlikely that every element will be perfect: in the present case, it may be attributed to the curved nature of the crown, where high aspect ratios and large curvatures are unavoidable. However, the global performance of the mesh will not be hampered by a sporadic spurious element.
It must be noted that meshing geometric solid models is still a laborious and iterative process, but is potentially more accurate and useful than the current methods of FE mesh generation of CT generated models, as described in the literature. As demonstrated here the generation of a number of significantly different access cavity geometries is easily achieved with the solid model using standard Boolean operations.
2.2
Material properties
The analyses in this study simulates the dental ceramic, IPS e.max Press ® and filling composite Tetric EvoCeram ® , both manufactured by Ivoclar Vivadent. This material has been examined previously by Oeblawi et al. ( Table 1 ).
Material properties | IPS e.max | Tetric EvoCeram ® |
---|---|---|
Young’s modulus (GPa) | 95 | 10 |
Poisson’s ratio | 0.234 | 0.25 |
Density (g/cm 3 ) | 2.1 | 1.7 |
2.3
Loading
The models in this paper were assessed in a manner reflective of in vivo loading conditions. The manner in which FE models of teeth are loaded is a question of some debate, but there are two main approaches: some researchers tend to simulate laboratory experiments and others aim to mimic the in vivo environment (i.e. the general loading applied by the dental forces) .
In a recently published work , Qeblawi et al. studied the effect of endodontic access on, all-ceramic restorations (a lithium disilicate glass ceramic, similar to the dental ceramic in this study). Several crowns of different ceramics were manufactured and subsequently endodontically accessed. Loaded with a hemispherical indenter, driven by a piston, they found that the crowns can withstand direct loads of up to 2354 ± 476 N.
Conventional and clinical knowledge immediately refutes this as occlusal forces never reach such a figure. Maximum forces approach 800 N with the average bite force lying somewhere around 200 ± 50 N . Ausiello et al. follow this protocol and apply a loading condition based on a similar experiment, i.e. two 300 N point loads at 35° to the vertical at pre-specified locations.
However, the use of point loads is disputed by Benazzi et al. , who suggest that such an approach constitutes an over-simplification. The point load creates a singularity in the stress tensor at the location of the load application, which will manifest itself in a linear FEA as an artificially high stress concentration, which will tend to drive the analyst to refine the mesh, increasing mesh density in the vicinity of the applied point load. Indeed the process of refining throws up several further unnecessary complications which are to be avoided. It is felt therefore that this type of loading does not seem to be an appropriate reflection of actual behavior; a point that is underscored by Kelly , who insists that for laboratory tests, and FEA by extension, to be relevant, they need to replicate the damage caused in clinical failure. Crucially, tests which create damage uncharacteristic of clinical situations can be a misleading guide to clinicians.
Therefore this analysis does not mimic the setup of a laboratory experiment but rather follows the more realistic approach set out by Dejak et al. and Rodrigues et al. who apply a general pressure over the occlusal surface simulating a masticatory or chewing action (the hypothesis is that food being grinded by teeth would cover the occlusal surface, hence creating a uniformly distributed load). By applying such a load, i.e. a pressure which results in a normal reaction force of 200 N, an accurate simulation of in vivo loading conditions is achieved.
2.4
Boundary conditions
Boundary conditions for this analysis are simple – fixity or zero displacement for all nodes on the bottom surface and bottom edge of the crown, simulating the behavior of the crown at the cementoenamel junction. This is standard practice in current simulations and is not disputed: see .
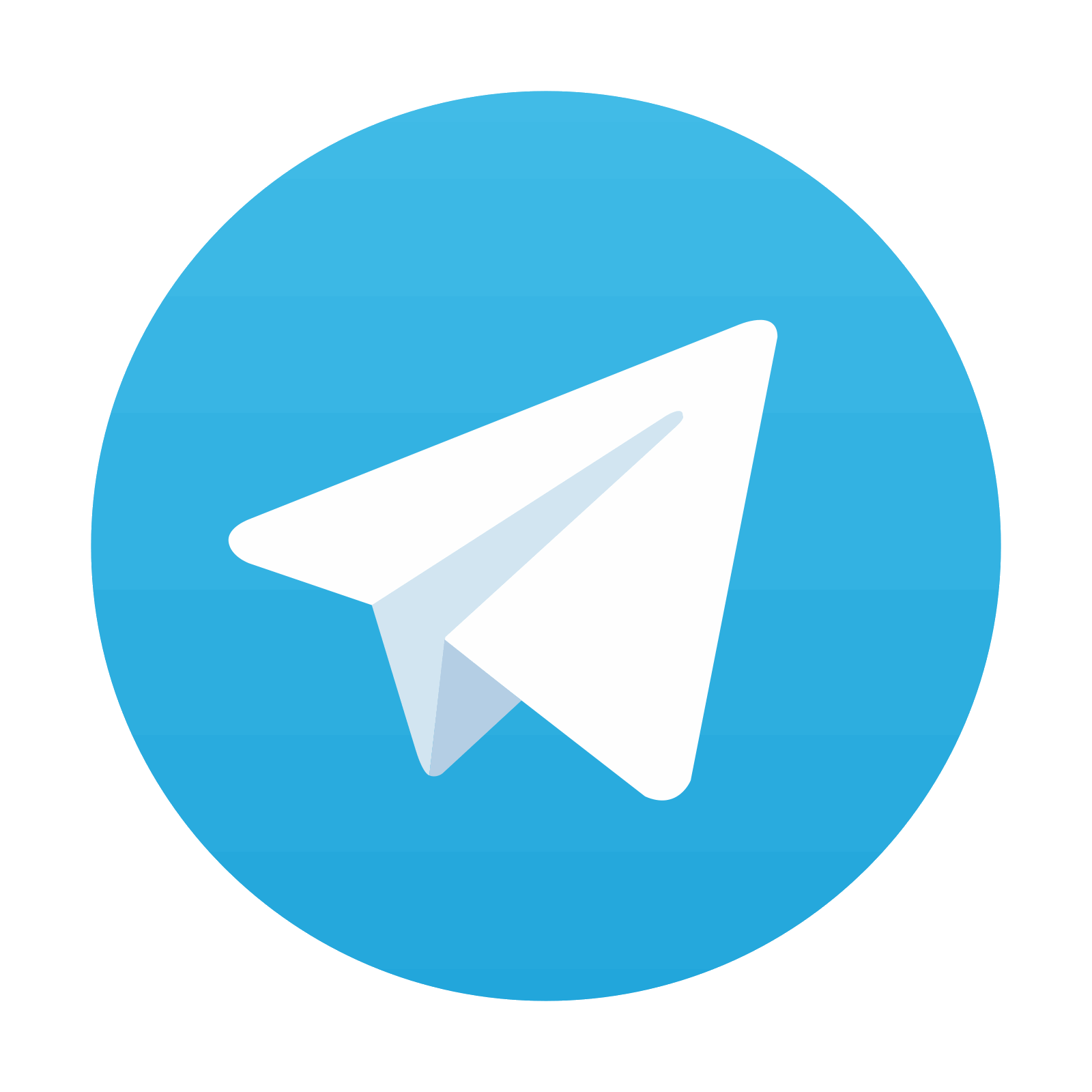
Stay updated, free dental videos. Join our Telegram channel

VIDEdental - Online dental courses
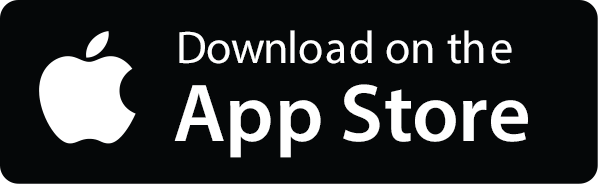
