Abstract
Objectives
This in vitro study should assess the fracture resistance of veneered zirconia-based crowns with either luted or fused veneer.
Methods
Thirty-two identical zirconia frameworks (IPS e.max ZirCAD; Ivoclar/Vivadent), were constructed (inLab 3.80; Sirona Dental Systems). All frameworks were veneered with CAD/CAM-fabricated lithium disilicate ceramic (IPS e.max CAD; Ivoclar/Vivadent). For half the crowns ( n = 16) the veneer was luted to the framework (Multilink Implant; Ivoclar/Vivadent); for the other it was fused (IPS e.max Crystall./Connect; Ivoclar/Vivadent). Half of the specimens were then loaded until failure without artificial aging; the other half underwent artificial aging before assessment of the ultimate load. To compare the two techniques further, finite element analysis (FEA) and fractographic assessment using SEM and EDX analysis were conducted. Statistical assessment was performed by use of non-parametric tests.
Results
Initial fracture forces were higher in the fusion group (mean: 1388 ± 190 N versus 1211 ± 158 N). All specimens were insensitive to artificial aging. FEA showed that tensile stresses in the veneer at the frame–veneer interface were much higher for crowns with luted veneer; this may be the reason for their lower fracture resistance. Fractographic analysis revealed that both fused and luted specimens had cohesive and adhesive fracture patterns which resulted in partial delamination of the veneer.
Significance
Fused crowns are superior to luted crowns. Comparison of fracture resistance with the maximum loads which may occur clinically ( F max = 600 N on one tooth) suggests both techniques might be used clinically, however.
1
Introduction
Because chipping has been identified as a major technical complication for veneered zirconia restorations , several means of improving the performance of these restorations have been reported in recent years. In addition to optimization of firing procedure and framework design , etc., it has been suggested that CAD/CAM production improves the mechanical properties of the veneer . CAD/CAM-produced veneers have many fewer flaws than hand-layered veneers. There are two main reasons for this: first, the blanks themselves are industrially produced and contain fewer material defects; second, during manual production of the veneer, imperfections will inevitably be created, even when production is performed accurately.
To improve the fracture resistance of all-ceramic crowns further, changeover from feldspathic ceramic to lithium disilicate ceramic for production of the veneer has been suggested, because of the superior mechanical properties of lithium disilicate ceramic . Furthermore, frame and veneer were milled from ceramic blanks by use of the so-called “CAD-on” technique. After sintering of the zirconia framework, the lithium disilicate veneer can be attached to the framework by use of resin cement or by fusion of the ceramic. Although fusion is recommended by the manufacturer, it might be relevant to determine the effect of attachment technique on fracture resistance, because, e.g., in the dental laboratory or even chair-side luting is often preferred because of rapid and easy handling. However, the effect of these two approaches on the fracture resistance of the crowns is unknown.
As recommended by Anusavice et al. , several approaches were included in this study to enable comprehensive analysis of the failures. FE computations enabled assessment of the effect of interface layer stiffness on stresses occurring within the specimens during simulated loading . Fractographic analysis enabled identification of the site of initiation of the fracture and EDX enabled adhesive and cohesive failure to be distinguished and aided identification of the location (on core or veneer) of attachment material after failure. The results of all these methods were combined to enable better understanding of the effect of the material used to attach the veneer to the core.
The hypothesis of this study was that, with regard to load to failure, crowns with fused veneer would outperform crowns with luted veneer.
2
Material and methods
2.1
Test series
With regard to chipping and/or delamination of the veneer, the performance of all-ceramic molar crowns fabricated with the new CAD/CAM technique was of interest. The particular focus of the study, on the effect of attachment technique on fracture load, resulted in two test series:
- 1)
CAD-on with luted veneer (Multilink Implant)
- 2)
CAD-on with fused veneer (IPS e.max Crystall./Connect)
2.2
Manufacture of the crowns
One trained dental technician (D.M.) produced all the specimens to avoid any operator effect.
2.2.1
Manufacture of the zirconia framework
An artificial molar was prepared and an impression was taken which was poured using gypsum in order to produce a die. This die was duplicated 32 times in CoCrMo alloy.
On these dies, 32 identical zirconia frameworks (IPS e.max ZirCAD), 0.6 mm thick with an anatomically shaped occlusal area, were constructed (Sirona inLab 3.80). The frames were then milled (Sirona inLab MC XL) and sintered (Vita ZYrcomat). After sintering, all frameworks were checked for flaws, etc., by light microscopy (Stemi SR; Carl Zeiss, Oberkochen). Also, for each frame, the thickness at five previously defined points was measured by use of calipers.
2.2.2
Construction of the veneer
After construction of the veneer by use of inLab 3.80 (Sirona), the mesio-lingual cusp was modified by use of Rapidform Dental software (INUS Technology, Seoul, Korea) as follows:
- 1)
constant 30° angle between the occlusal surface of the cusp and the tooth axis, and
- 2)
construction of a mold (radius: 3.0 mm, depth: 0.1 mm) defining the loading site for mechanical testing. The thickness of the veneer at the mesio-lingual cusp was approximately 2.0 mm.
2.2.3
Milling of the veneer
The modified veneer was milled (inLab MC XL; Sirona) from a lithium disilicate ceramic blank (IPS e.max CAD). After this process, wall thickness readings were checked and recorded to ensure correct geometric fabrication.
2.2.4
Attachment of the veneer to the framework
In one group (luting group; n = 16) the veneer was attached to the framework by use of Multilink Implant after separate crystallization and glaze firing of the veneer shell.
Multilink Implant was used in accordance with the manufacturer’s guidelines: etching of the veneer for 20 s with 5% hydrofluoric acid (IPS Ceramic Etching Gel; Ivoclar Vivadent) and application of Monobond Plus (Ivoclar Vivadent). The zirconia frameworks were sandblasted (P-G400; Harnisch & Rieth, Winterbach, Germany, aluminum oxide, 50 μm, 2.0 bar) and cleaned for 2 min with 95% isopropyl alcohol in an ultrasonic bath (Sonorex super RK 102H; Bandelin, Berlin, Germany). After cementation, the specimens were stored at 37 ± 1 °C for 24 h.
In the second group (fusion group; n = 16) the veneer was attached to the framework in a furnace (Programat 700; Ivoclar Vivadent) by use of IPS e.max Crystall./Connect. The fusion ceramic was used in accordance with the manufacturer’s guidelines; details of the firing procedure are given in Table 1 . This method was no more time-consuming than the first, because crystallization of the lithium disilicate veneer and fusion to the zirconia framework were performed in one firing.
Working temp. [°C] | Closing time [min] | Increase of temp. t 1 [°/min] | Increase of temp. t 2 [°/min] | Temp. T 1 [°C] | Temp. T 2 [°C] | Exposure time H 1 [min:s] | Exposure time H 2 [min:s] | Vacuum V1 1 /V1 2 [°C] | Vacuum V2 1 /V2 2 [°C] | Cooling [°C] |
---|---|---|---|---|---|---|---|---|---|---|
403 | 2 | 30 | 30 | 820 | 840 | 2:00 | 7:00 | 550/820 | 820/840 | 600 |
2.3
In vitro tests
The purpose of this study was to assess the effect of different attachment techniques on forces leading to delamination (adhesive failure at the frame–veneer interface) and/or chipping (cohesive failure within the veneer ceramic) of CAD-on molar crowns.
Mechanical tests were performed by applying a load to the mesio-lingual cusp at an angle of 30° to the direction of insertion ( Fig. 1 a). For chewing simulation and fracture testing the metal dies were embedded in steel molds at an angle of 30° to the direction of insertion with cold-curing resin (Technovit 4071; Heraeus Kulzer GmbH, Hanau, Germany). The placement of the metal dies could be reproduced exactly by use of a special metal key, i.e. a CAM-manufactured metal block containing the negative form of the prepared tooth surface with 30° inclination, orienting the metal dies in the desired direction during use of a parallelometer table. Consequently, the loaded cusp was oriented horizontally ( Fig. 1 a) after the crowns were luted to the metal dies with Panavia F 2.0 (Kuraray Medical Inc. Japan). Before in vitro testing the specimens were stored for 24 h at 37 ± 1 °C.
For each of the two attachment techniques, two series of tests were conducted ( n = 8 for each series).
In the first series, the initial fracture resistance (Zwick/Roell Z005, Ulm, Germany; crosshead speed of 0.5 mm/min., force shutdown threshold of 100 N) was determined directly after manufacture of the crowns whereas the second series underwent artificial aging (10,000 thermal cycles between 6.5 and 60 °C, dwell time 45 s; Willytec THE-1100; SD Mechatronik, Feldkirchen, Germany) and 1.2 million chewing cycles with a force magnitude of F max = 108 N, water storage (Willytec CS3) before the final fracture tests were performed. Steel spheres 6 mm in diameter were used as antagonists for both chewing simulation and fracture tests. The test setup is illustrated in Fig. 1 b.
The crowns were inspected after each step (manufacture, thermal cycling, and chewing simulation) under a microscope (Stemi SR; Carl Zeiss, Oberkochen) to detect formation of potential flaws or cracks.
2.4
Statistics
Means, standard deviations, and medians were analyzed by use of descriptive statistics.
Non-parametric tests (Kruskal–Wallis test and Mann–Whitney U -test with α < 0.05 as significance level) were used to assess the effect of the different attachment techniques on fracture load. The results were depicted by use of whisker and box plots. A post hoc power analysis was performed using the program “PS power and sample size calculation V 2.1.30” .
2.5
Finite element computations
Because the stiffness of the interfacial layer between frame and veneer will affect stress distribution, finite element computations (ANSYS 13.0) were performed with different interface materials on the basis of the original geometry ( Fig. 1 c). The Young’s modulus of the interface layer was varied, i.e., E = 3.5 GPa for Multilink Implant, and E = 70 GPa for IPS e.max Crystall./Connect (material properties in accordance with manufacturers’ data). The properties of all the linear–elastic materials are listed in Table 2 . The FE model consisted of approximately 65,000 20-node hexahedral elements and 240,000 nodes. The CoCrMo stump was assumed to be rigid, i.e., all displacements of nodes located on the inner surface (stump–cement interface) were restricted. As a consequence, the stump was not included in the computations. Loading was performed by contact (area-to-area contact formulation) with a steel sphere (6 mm diameter), by analogy with loading in the in vitro tests ( Fig. 1 b). For computations for each interface material, the corresponding mean ultimate loads F u,m from the in vitro tests were chosen as final loads, i.e. at this load critical stresses should be seen within the restoration. Thermal residual stress which might occur to some extent within the fused crowns were not included in the FE analysis.
2.6
Fractographic analysis and EDX
Fractographic analysis was performed by use of an FE SEM (Field Emission Scanning Electron Microscope; Supra 40 VP; Zeiss, Germany) equipped with an EDX detector (Energy Dispersive X-ray Spectroscopy). Before analysis the fracture surfaces were cleaned with ethanol in an ultrasonic bath.
2
Material and methods
2.1
Test series
With regard to chipping and/or delamination of the veneer, the performance of all-ceramic molar crowns fabricated with the new CAD/CAM technique was of interest. The particular focus of the study, on the effect of attachment technique on fracture load, resulted in two test series:
- 1)
CAD-on with luted veneer (Multilink Implant)
- 2)
CAD-on with fused veneer (IPS e.max Crystall./Connect)
2.2
Manufacture of the crowns
One trained dental technician (D.M.) produced all the specimens to avoid any operator effect.
2.2.1
Manufacture of the zirconia framework
An artificial molar was prepared and an impression was taken which was poured using gypsum in order to produce a die. This die was duplicated 32 times in CoCrMo alloy.
On these dies, 32 identical zirconia frameworks (IPS e.max ZirCAD), 0.6 mm thick with an anatomically shaped occlusal area, were constructed (Sirona inLab 3.80). The frames were then milled (Sirona inLab MC XL) and sintered (Vita ZYrcomat). After sintering, all frameworks were checked for flaws, etc., by light microscopy (Stemi SR; Carl Zeiss, Oberkochen). Also, for each frame, the thickness at five previously defined points was measured by use of calipers.
2.2.2
Construction of the veneer
After construction of the veneer by use of inLab 3.80 (Sirona), the mesio-lingual cusp was modified by use of Rapidform Dental software (INUS Technology, Seoul, Korea) as follows:
- 1)
constant 30° angle between the occlusal surface of the cusp and the tooth axis, and
- 2)
construction of a mold (radius: 3.0 mm, depth: 0.1 mm) defining the loading site for mechanical testing. The thickness of the veneer at the mesio-lingual cusp was approximately 2.0 mm.
2.2.3
Milling of the veneer
The modified veneer was milled (inLab MC XL; Sirona) from a lithium disilicate ceramic blank (IPS e.max CAD). After this process, wall thickness readings were checked and recorded to ensure correct geometric fabrication.
2.2.4
Attachment of the veneer to the framework
In one group (luting group; n = 16) the veneer was attached to the framework by use of Multilink Implant after separate crystallization and glaze firing of the veneer shell.
Multilink Implant was used in accordance with the manufacturer’s guidelines: etching of the veneer for 20 s with 5% hydrofluoric acid (IPS Ceramic Etching Gel; Ivoclar Vivadent) and application of Monobond Plus (Ivoclar Vivadent). The zirconia frameworks were sandblasted (P-G400; Harnisch & Rieth, Winterbach, Germany, aluminum oxide, 50 μm, 2.0 bar) and cleaned for 2 min with 95% isopropyl alcohol in an ultrasonic bath (Sonorex super RK 102H; Bandelin, Berlin, Germany). After cementation, the specimens were stored at 37 ± 1 °C for 24 h.
In the second group (fusion group; n = 16) the veneer was attached to the framework in a furnace (Programat 700; Ivoclar Vivadent) by use of IPS e.max Crystall./Connect. The fusion ceramic was used in accordance with the manufacturer’s guidelines; details of the firing procedure are given in Table 1 . This method was no more time-consuming than the first, because crystallization of the lithium disilicate veneer and fusion to the zirconia framework were performed in one firing.
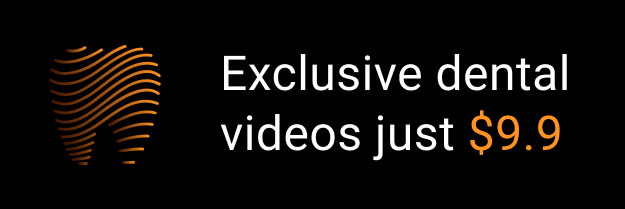