Abstract
Objectives
To evaluate the effect of the microstructure on the Weibull and slow crack growth (SCG) parameters and on the lifetime of three ceramics used as framework materials for fixed partial dentures (FPDs) (YZ – Vita In-Ceram YZ; IZ – Vita In-Ceram Zirconia; AL – Vita In-Ceram AL) and of two veneering porcelains (VM7 and VM9).
Methods
Bar-shaped specimens were fabricated according to the manufacturer’s instructions. Specimens were tested in three-point flexure in 37 °C artificial saliva. Weibull analysis ( n = 30) and a constant stress-rate test ( n = 10) were used to determine the Weibull modulus ( m ) and SCG coefficient ( n ), respectively. Microstructural and fractographic analyzes were performed using SEM. ANOVA and Tukey’s test ( α = 0.05) were used to statistically analyze data obtained with both microstructural and fractographic analyzes.
Results
YZ and AL presented high crystalline content and low porosity (0.1–0.2%). YZ had the highest characteristic strength ( σ 0 ) value (911 MPa) followed by AL (488 MPa) and IZ (423 MPa). Lower σ 0 values were observed for the porcelains (68–75 MPa). Except for IZ and VM7, m values were similar among the ceramic materials. Higher n values were found for YZ (76) and AL (72), followed by IZ (54) and the veneering materials (36–44). Lifetime predictions showed that YZ was the material with the best mechanical performance. The size of the critical flaw was similar among the framework materials (34–48 μm) and among the porcelains (75–86 μm).
Significance
The microstructure influenced the mechanical and SCG behavior of the studied materials and, consequently, the lifetime predictions.
1
Introduction
The use of ceramic materials with high crystalline content for dental restorations was improved by the development of CAD/CAM (computer-aided design/computer-aided manufacturing) technology. Alumina and zirconia-based systems were introduced as framework materials to produce restorations subjected to high stress concentration, such as posterior crowns and fixed partial dentures (FPDs). These materials are available as pre-fabricated blocks for CAD/CAM. All-ceramic restorations are produced in two layers: a high strength ceramic framework is veneered with porcelain to provide a more natural-looking restoration . Although clinical evaluation of zirconia-based all-ceramic FPDs showed high success rate there is still some concern about the reliability of these systems, since the follow up period reported in these studies is relatively short, around 3–5 years .
The limitations of all-ceramic restorations are related to the brittle behavior of ceramic materials. Ceramics are sensitive to stress concentrations around pre-existing cracks. The stress field at the tip of a crack can be described by the stress intensity factor ( K I ) that is controlled by the loading in Mode I (opening mode). The flaw will propagate when the stress intensity factor reaches a critical condition, K Ic , which is also called the critical stress intensity factor or fracture toughness and characterizes the resistance to unstable propagation of pre-existing cracks . These flaws form during processing ( i.e. pores, inclusions) or subsequent handling, finishing, or service damage . Thus, the strength of ceramic materials is limited by the presence of these pre-existing cracks associated with the relatively low fracture toughness. Large variability in strength is a consequence of the distribution in crack sizes, and the time-dependency of strength results from the material susceptibility to a phenomenon called “subcritical crack growth” .
Strength variability is usually characterized using the Weibull distribution, which is based on the premise that the weakest link in a body controls strength. The distribution function relates the cumulative probability of failure of a volume or area under tensile stress to two parameters, the Weibull modulus and the Weibull characteristic strength, m and σ 0 , respectively. The characteristic strength or scale parameter represents the value at which 63.21% of the test specimens have fractured. The Weibull modulus or shape parameter ( m ) describes the relative spread of strength values in the asymmetrical distribution, with high m corresponding to less spread. A large value of Weibull modulus ensures a smaller variability in strength estimation, and greater precision .
The literature reports a large range of flexural strength and Weibull modulus values for ceramics used as FPDs framework materials. For yttria partially stabilized tetragonal zirconia ceramic (Y-TZP), the flexural strength varies from 700 to 1200 MPa and the Weibull modulus from 10 to 18 . Studies showed, for an alumina-based zirconia-reinforced glass infiltrated ceramic (In-Ceram Zirconia), lower flexural strength values (440–620 MPa) than the ones found for Y-TZP . However, the Weibull modulus values obtained were in the same range as YZ, from 9 to 14 . A polycrystalline alumina ceramic (Vita In-Ceram AL) can also be used as framework material for FPDs. Although the manufacturer reported a mean flexural strength of 500 MPa, there is a lack of studies that characterize the mechanical performance of this ceramic material.
“Subcritical crack growth” (SCG) is a process that involves the stable growth of pre-existing flaws at stress intensity factor ( K I ) levels lower than that necessary for the flaw to become unstable ( K Ic ) . In the case of stress-corrosion, this phenomenon can result from a water-assisted breakage of silicate or oxide bonds at the crack tip under applied stress. Catastrophic failure will occur once the crack has grown to a critical size, at a given stress . SCG can be determined by direct measurement of the crack velocity as a function of stress intensity factor. Otherwise, inferences about crack propagation can be made using indirect methods such as dynamic, cyclic and static fatigue tests . The coefficient of subcritical crack growth, n , represents the inverse of degree of susceptibility of a material to SCG in a particular environment. Therefore, high n values correspond to lower susceptibility to the subcritical growth . Studies showed for alumina polycrystalline ceramic n value of 44, and values varying from 29 to 57 for Y-TZP . For In-Ceram Zirconia, the literature reported n values around 20 .
A strength test produces two important information: the strength data and the fracture origin or flaw. Quantitative fracture surface analysis can be used to identify the size and location of the fracture initiating crack, the stress at failure, the nature of the stress state, the existence of residual stress or SCG, and knowledge of local processing anomalies that affect the fracture process .
A combination of high fracture toughness, high resistance to stress corrosion, and lack of severe flaws is required for structural reliability . However, few studies systematically evaluated all the factors necessary to predict the behavior of framework and veneer materials. Therefore, the first objective of this study was to analyze the microstructure of three ceramics used as framework material for FPDs and of two veneering porcelains in order to establish a relationship with the results obtained in the fracture strength test and Weibull analysis. The tested hypothesis was that the materials’ microstructures affect their mechanical behavior. The second objective was to determine the SCG parameters of these materials, testing the hypothesis that the materials’ microstructures influence the slow crack growth behavior. The third objective was to perform lifetime predictions for the studied materials combining both the SCG and Weibull parameters. The hypothesis was that the microstructure of the material significantly affects the lifetime of specimens predicted in vitro.
2
Materials and methods
Three ceramics used as framework materials for FPDs and two veneering porcelains were studied. The materials and the experimental groups are described in Table 1 .
Group | Material a | Composition | Indication |
---|---|---|---|
YZ | Vita In-Ceram YZ | Yttria partially stabilized tetragonal zirconia polycrystal | Framework |
IZ | Vita In-Ceram Zirconia | Alumina-based zirconia-reinforced glass infiltrated ceramic | Framework |
AL | Vita In-Ceram AL | Alumina polycrystal | Framework |
VM7 | Vita VM7 | Feldsphatic porcelain | Veneer |
VM9 | Vita VM9 | Feldsphatic porcelain | Veneer |
YZ, IZ and AL bar-shaped specimens were obtained by cutting pre-sintered blocks using a diamond disc in a precision cutting machine (Isomet 1000, Buehler, Lake Bluff, USA) at 275 rpm. YZ and AL specimens were sintered in the Zyrcomat furnace (Vita Zahnfabrik, Germany) at 1520 °C for 2 h. IZ material was infiltrated with glass (Zirconia Glass Powder, Vita Zahnfabrik, Germany). The infiltration cycle was performed in the Inceramat 3 furnace (Vita Zahnfabrik, Germany), and the excess glass was removed with burs. The glass infiltration cycle was performed at 1110 °C for 6 h, according to the manufacturer’s instruction. VM7 and VM9 specimens were fabricated by mixing ceramic powder with distilled water. The mixture was poured into a metallic mold and condensed with manual vibration. The excess water was blotted out with absorbent paper. Keramat I furnace (Knebel, Porto Alegre, Brazil) was used for the porcelain sintering as follows: pre-drying at 500 °C for 6 min, heating to 910 °C at a rate of 55 °C/min under vacuum, heating at 960 °C for 1 min and slow cooling (∼6 min).
After YZ, AL, VM7 and VM9 sintering and IZ glass infiltration, all specimens were ground to their final dimensions (2 mm × 4 mm × 16 mm). The 4-mm wide face was polished to 1 μm finish using a polishing machine (Ecomet 2, Buehler, Lake Bluff, USA). All edges were chamfered at a 0.1 mm wide chamfer, following the ISO 6872:2008 standard.
The SCG parameters were evaluated by the constant stress-rate test using five different rates: 10 −2 , 10 −1 , 10 0 , 10 1 and 10 2 MPa/s. For all groups, ten specimens were tested at each stress rate. Except for 1 MPa/s stress rate, in which thirty specimens were tested to perform Weibull analysis . The mechanical testing was performed according to the ISO 6872:2008 standard. The flexural strength ( σ f ) was determined using a three-point flexure fixture in a universal testing machine (Sintech 5G, MTS, São Paulo, Brazil) at constant stress rates, in 37 °C artificial saliva with the following composition : 100 mL of KH 2 PO 4 (2.5 mM); 100 mL of Na 2 HPO 4 (2.4 mM); 100 mL of KHCO 3 (1.50 mM); 100 mL of NaCl (1.0 mM); 100 mL of MgCl 2 (0.15 mM); 100 mL of CaCl 2 (1.5 mM); and 6 mL of citric acid (0.002 mM). The three-point flexural strength ( σ f , MPa) was calculated using the following equation:
σ f = 3 P l 2 w b 2
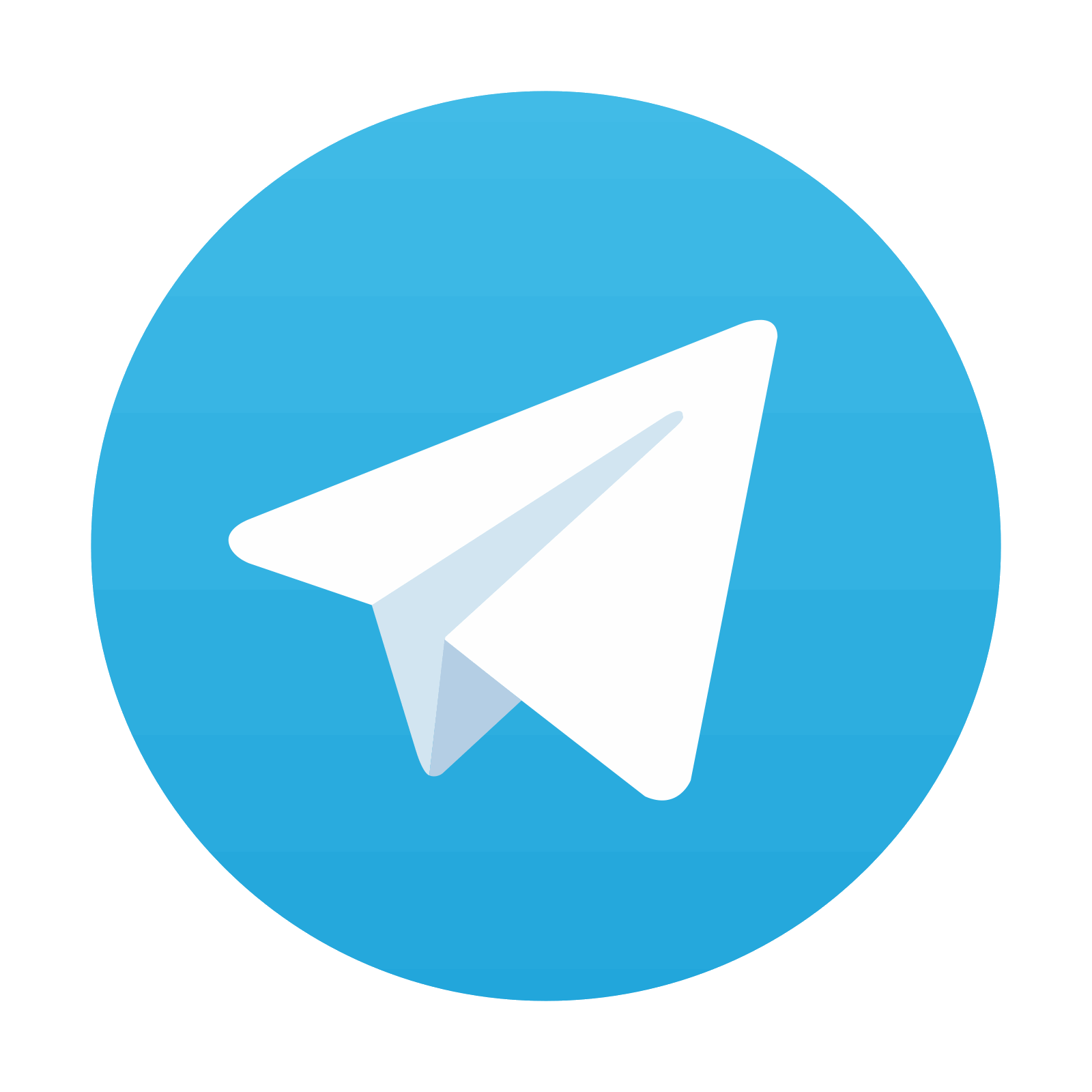
Stay updated, free dental videos. Join our Telegram channel

VIDEdental - Online dental courses
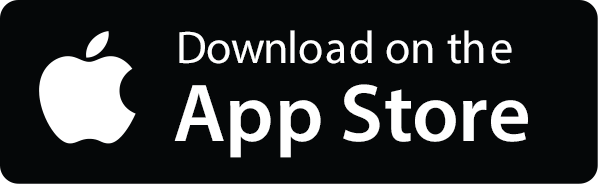
