Abstract
Objective
This study evaluated the effect of different chemical surface treatments on the surface characteristics of commercially pure titanium (cp Ti) and the adhesion of the porcelain–titanium system by means of strain energy release rate ( G -value, J/m 2 ). Surface roughness and morphology of treated cp Ti were additionally evaluated.
Methods
Two hundred and thirty specimens of machined cp Ti plates grade II were prepared. The specimens were divided into ten groups in each test according to the surface treatment used; Gr 1 (control; machined), Gr 2 (sandblasted), Gr 3 (CH 2 Cl 2 for 5 min), Gr 4 (CH 2 Cl 2 for 10 min), Gr 5 (10% H 2 O 2 for 5 min), Gr 6 (10% H 2 O 2 for 10 min), Gr 7 (30% H 2 O 2 for 5 min), Gr 8 (30% H 2 O 2 for 10 min), Gr 9 (9% HF for 5 min) and Gr 10 (9% HF for 10 min). Titanium–porcelain (Vita Titankeramik) was applied to each group for testing the adhesion. The G -value (J/m 2 ) was measured with a four-point bending configuration. Following fracture testing specimens were examined with a scanning electron microscope (SEM). Surface roughness and SEM analysis were carried out. Data were analyzed using ANOVA and Tukey’s test.
Results
Groups treated with 9% HF or CH 2 Cl 2 baths for 10 or 5 min showed the highest adhesion values (J/m 2 ) (34.23 ± 4.31, 30.75 ± 4.91, 28.92 ± 4.33 and 22.54 ± 3.58) respectively among the groups. The machined groups demonstrated the lowest value (8.18 ± 1.95) (J/m 2 ). SEM analysis indicated a combination of cohesive and adhesive fractures for 9% HF, CH 2 Cl 2 , sandblasted and 30% H 2 O 2 (10 min) groups, while mainly adhesive fractures were found with the other groups. There was no direct correlation between surface roughness and adhesion.
Significance
Adhesion between porcelain and cp Ti can be improved by the use of certain chemical surface treatments prior to porcelain firing as alternative techniques to sandblasting treatment.
1
Introduction
Titanium (Ti) and its alloys are commonly used as biomaterials in the medical and dental fields due to their proven biocompatibility, excellent corrosion resistance, appropriate mechanical properties and lower cost . One of the dental applications of Ti is the metallic substrate for porcelain-fused-to-metal (PFM) restorations. However, practical problems with Ti for titanium porcelain bonding remain to be solved .
One property that contributes to the excellent biocompatibility of Ti but also causes problems when bonding to porcelain is the presence of surface oxides. When dental porcelain is applied and during the sintering cycle, Ti has great affinity to oxygen, and its oxidation rate increases exponentially at elevated temperatures . The oxide layer formed on Ti surfaces at porcelain sintering temperatures is porous, nonadherent and unsuitable for porcelain bonding. It easily spalls off and cracks because of its porosity and internal stresses .
A number of surface modification methods have been proposed to improve oxidation properties of Ti in an effort of enhancing bonding between Ti and porcelain. They included sandblasting, gold coating, acid treatment, chromium plating, silicon nitride and ceramic coating . Although airborne-particle abrasion of the Ti surface prior to ceramic application improves the adhesion of the ceramic to the Ti substrate, this procedure remains technique sensitive . Derand and Hero observed that the use of larger alumina particles with a diameter of 250 μm, compared with 50 μm particles, significantly improved the bond between Ti and porcelain . It is possible that the small particles may imbed in the Ti surface . In fact, Gilbert et al. found that airborne-particle abrasion could contaminate the surface of Ti with alumina particles, which could weaken the mechanical interlocking of the porcelain and Ti . Contamination of the Ti surface might also decrease its corrosion resistance and biocompatibility .
Donachie reported that caustic and acid baths have been successfully used in the industry for cleaning contaminated Ti surface after heat treatments. From an industrial viewpoint, a variety of reactive solutions can be used, such as nitric and hydrochloric acids or sodium hydroxide aqueous solutions . Hydrofluoric acid (HF) solution is also mentioned as an etching agent and surface modifier for Ti, where the modification promotes a better quality of the surface with the removal of contaminant elements that originate from the industrial manufacturing process .
In spite of the variety of solutions available for industrial surface modifications of commercially pure titanium (cp Ti), the literature lacks reports about the use of these solutions to promote better bond strength values between porcelain and the metal substrate . The organic solvent, methylene chloride solution, has also not been evaluated for its effect on the adhesion of porcelain to cp Ti. An assumption is raised as to how the cp Ti surface treatment using certain chemical baths (such as methylene chloride, hydrogen peroxide, and hydrofluoric) could lead to better bond strength or adhesion results. Thus, the purpose of this study was to investigate the effect of different chemical surface treatments on the bond strength of a specific low-fusing titanium porcelain bonded to cp Ti. The research hypothesis was that the proposed chemical surface treatments of cp Ti would enhance the titanium-porcelain bond strength when compared with machining and sandblasting methods.
2
Materials and methods
Two hundred and thirty specimens of cp Ti plates (ASTM, Grade II, Modern Techniques and Materials Engineering Center, Egypt) were machined, ground on a 600-grit silicon carbide paper (Leco Co., St. Joseph, MI, USA) under running water and then cleaned in an ultrasonic (Bandelin, Sonorex, Germany) bath filled with distilled water for 5 min. Titanium–porcelain used was Vita Titankeramik (Vita Zahnfabrick, Bad Säckingen, Germany).
2.1
Specimen preparation
The specimens in each test were divided into ten groups according to the method of surface treatment applied, as follows:
Group 1: Machined (control) group; the specimens were exposed only to grinding and ultrasonic cleaning as mentioned above.
Group 2: Sandblasted group; the specimens were abraded with alumina particles (110 μm) with a dental airborne-particle abrasion unit (Micro-Blaster; Daedong Industrial Co, Ltd., Daegu, Korea). The air pressure was set at 2 bar, and the distance between the nozzle tip and the specimen surface was maintained at 15 mm, during the airborne-particle abrasion, for 20 s, and then cleaned in an ultrasonic bath filled with distilled water for 5 min.
Group 3: The specimens were immersed in methylene chloride (CH 2 Cl 2 , formula weight: 84.13 g/mol, El Nasr Pharmaceutical Chemicals Co., Egypt) for 5 min and then cleaned in an ultrasonic bath filled with distilled water for 5 min.
Group 4: The specimens were immersed in methylene chloride for 10 min and then cleaned in an ultrasonic bath filled with distilled water for 5 min.
Group 5: The specimens were immersed in 10% H 2 O 2 (Liza, Mash Co., Egypt) for 5 min and then cleaned in an ultrasonic bath filled with distilled water for 5 min.
Group 6: The specimens were immersed in 10% H 2 O 2 for 10 min and then cleaned in an ultrasonic bath filled with distilled water for 5 min.
Group 7: The specimens were immersed in 30% H 2 O 2 (Liza, Mash Co., Egypt) for 5 min and then cleaned in an ultrasonic bath filled with distilled water for 5 min.
Group 8: The specimens were immersed in 30% H 2 O 2 for 10 min and then cleaned in an ultrasonic bath filled with distilled water for 5 min.
Group 9 : The specimens were immersed in 9% HF (El Nasr Pharmaceutical Chemicals Co., Egypt) aqueous solution for 5 min and then cleaned in an ultrasonic bath filled with distilled water for 5 min.
Group 10: The specimens were immersed in 9% HF aqueous solution for 10 min and then cleaned in an ultrasonic bath filled with distilled water for 5 min.
2.2
Strain energy release rate test
2.2.1
Porcelain application
One hundred rectangular specimens of cp Ti plates (30 mm × 8 mm × 1.5 mm) were divided into ten groups according to surface modification procedures as mentioned before ( n = 10). A specially designed split Teflon mold (30 mm × 8 mm × 1.5 mm) was used to apply porcelain (Vita Titankeramik) onto the titanium plate. A thin layer of bonder porcelain was applied, followed by a second opaque layer and two dentin body layers, each of them fired separately according to the manufacturer’s instructions in a dental vacuum porcelain furnace (Programat P500, Ivoclar Vivadent, Germany). The specimens were submitted to final glaze firing. Both surfaces (30 mm × 8 mm) of the specimens were ground to achieve flat and smooth surfaces using 240-grit and 320-grit silicon carbide paper, respectively. The porcelain surface that would be in contact with the rollers of the four-point bending jig was ground and then polished with 45 μm diamond abrasive, to ensure a flat loading surface, using the rotary polishing machine (Cooke Throughton, Simms Ltd., York, UK).
2.2.2
Notching the specimen
Notching across the width and entirely through the depth of the porcelain layer at the middle of the specimen was made using a water cooled low-speed diamond saw (Isomet, Buehler GmbH, Düsseldorf, Germany) which gave an accurate notch of width 0.4 mm and a depth of 1.5 mm (the thickness of porcelain). A pre-crack was created in a three-point bending jig, for which the applied load is controlled by a screw-knob and the specimen is supported completely on rubber. The pre-crack started from the base of the notch and extended along the interface with a total length of 2 mm approximately.
2.2.3
Testing procedures
The pre-cracked specimens were then placed in a four-point-bending jig mounted in a universal testing machine (Model TT-B, Instron Corp., Canton, MA, USA) with the inner rollers 14 mm and the outer rollers 26 mm. They were subjected to load at a crosshead speed of 0.05 mm/min until the crack reached the inner rollers. The load and crosshead displacement data were collected for calculation of the strain energy release rate, G. The testing configuration shown in Fig. 1 illustrates the relationship between the specimen and the rollers of the four-point bending jig.
2.2.4
Adhesion determination
The strain energy release rate, G , is given by
G = η [ P 2 l 2 ( 1 − ν m 2 ) ] E m b 2 h 3
where P is the load to stably propagate the crack, l the moment arm or distance between inner and outer load line (rollers) on the same side, ν m and E m are Poisson’s ratio and elastic modulus of metal substructure, and b and h are the specimen width and total thickness, respectively. The non-dimensional parameter η is calculated as follows:
η = 3 2 1 ( h m / h ) 3 − λ { ( h p / h ) 3 + λ ( h m / h ) 3 + 3 λ ( h p h m / h 2 ) [ ( h p / h ) + ( λ h m / h ) ] − 1 }
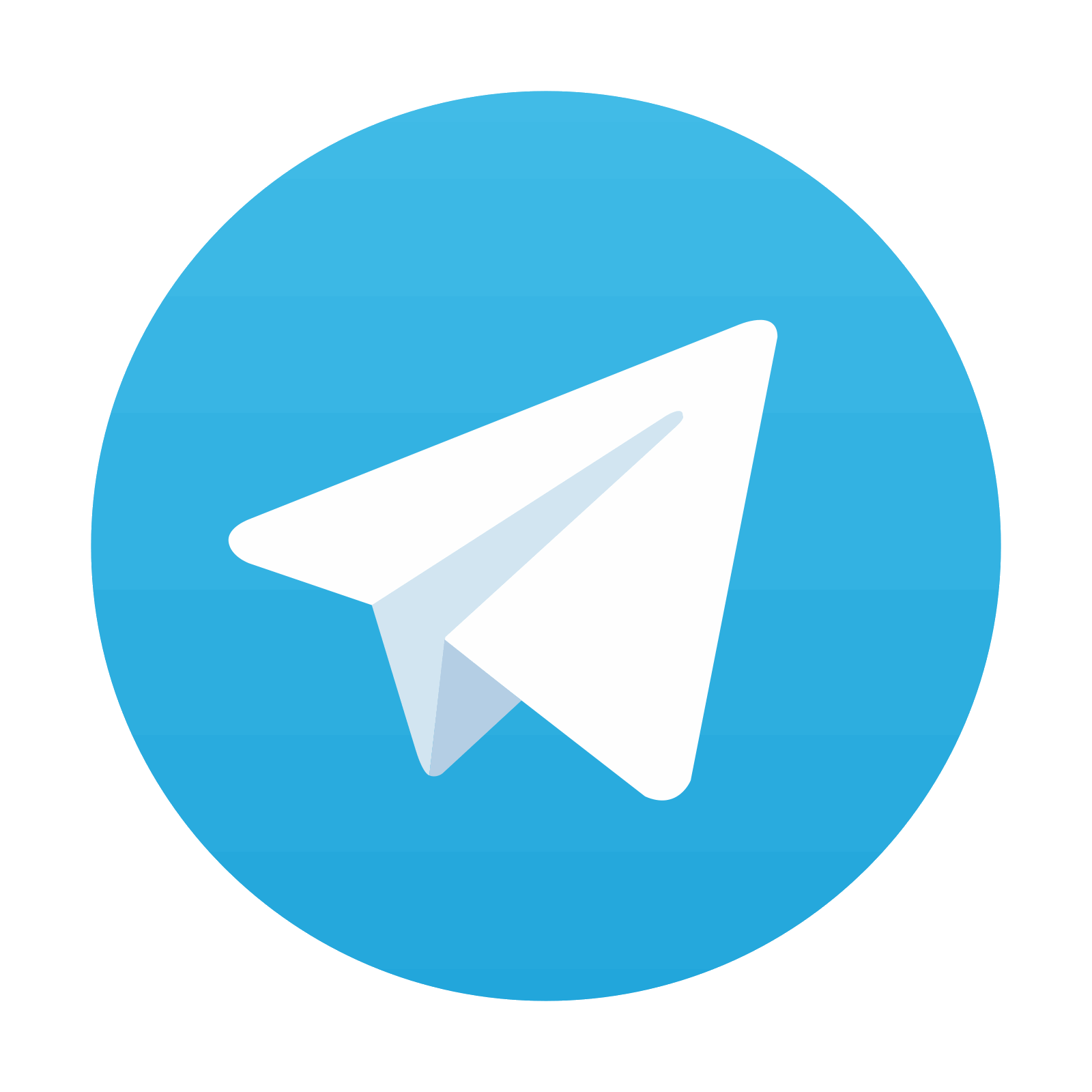
Stay updated, free dental videos. Join our Telegram channel

VIDEdental - Online dental courses
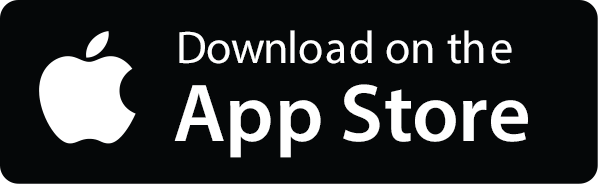
