Abstract
Objectives
Machined restorations have been investigated for their preciseness before, while detailed information on the milling-step itself are lacking. Therefore, the aim of this laboratory study was to quantify the effect of a novel milling-procedure on the marginal and internal fit of ceramic restorations.
Methods
An acrylic model of a lower left first molar was prepared to receive a ceramic partial crown and was duplicated by one step dual viscosity impressions. Gypsum casts were formed and laser-scanned to realize virtual datasets, before restorations were designed, exported (PRE) and machined from lithium disilicate blanks. Crowns were digitized by a structure-light-scanner to obtain post-milling-data (POST). PRE and POST were virtually superimposed on the reference tooth and subjected to computer-aided-inspection. Visual fit-discrepancies were displayed with colors, while root mean square deviations (RMSD) and degrees of similarity (DS) were computed and analysed by t -tests for paired samples ( n = 5, α = 0.05).
Results
The milling procedure resulted in a small increase of the marginal and internal fit discrepancies (RMSD mean: 3 μm and 6 μm, respectively). RMSD differences were not statistically significant ( p = 0.495 and p = 0.160 for marginal and internal fit, respectively). These results were supported by the DS data.
Significance
The products of digital dental workflows are prone to imprecisions. However, the present findings suggest that differences between computer-aided designed and actually milled restorations are small, especially when compared to typical fit discrepancies observed clinically. Imprecisions introduced by digital design or production processes are small.
1
Introduction
Contemporary dental workflows combine computer-aided design (CAD) and manufacturing (CAM) steps in the fabrication of esthetical pleasing restorations. Open access systems allow data to be captured from a variety of sources (intraoral scanner, model scanner, computer tomography and magnet resonance imaging) , before being further processed and manufactured in the dental office, dental laboratory, or at dedicated production centers . Advantages of open systems may include increased precision and reproducibility of the final product, and access to advanced materials with refined composition and microstructure .
High strength ceramics are enjoying increased popularity among dentists, technicians, and patients. However, they cannot withstand elastic deformation to the same extent as tooth structures or resinous materials. Stress concentrations depend on the geometry of the specimen material, loading conditions, the presence of intrinsic or extrinsic flaws, and marginal and internal fit. Resin-based luting agents have been shown to reduce, yet not completely absorb, the resulting shear-forces . Succeeding leucite-reinforced ceramics, lithium disilicate materials offer improved physical characteristics, while also remaining suitable for computer-aided-machining in a pre-sintered state. Mechanical properties include a modulus of elasticity of 91.0 GPa, a hardness of 5.5 GPa, and a biaxial-flexure-strength of 375 MPa . Thus, contemporary lithium disilicate based ceramic cores may be used for replacing a missing second premolar as a pontic in posterior fixed dental prostheses .
Despite improvements in additive manufacturing, subtractive technologies remain the most common to process advanced dental ceramics. For example, computer numeric controlled (CNC) milling is a frequently used abrasive process. It shapes materials by the generation of small chip fragments. Computer assisted machining (CAM) tools with sharp cutting edges induce strain to the material surface, which is followed by the initiation and propagation of micro-cracks and subsequent chipping . It has been shown that cracks on and beneath the newly formed surface structure remain as a chipping residue. Classified as surface and subsurface damage, these intrinsic flaws can severely change the mechanical behavior of machined restorations under masticatory load. Furthermore, materials with a relatively low fracture-toughness such as feldspathic ceramics are susceptible to surface and subsurface damage accumulation. Since chip fragments are achieved by hard particles located on the grinding tool ( e.g. diamond burs), additional surface irregularities that match the particle pattern can occur.
Marginal and internal fit of ceramic restorations are important determinants of clinical longevity , as gap sizes larger than 150 μm were reported to promote marginal discoloration, exposure of luting resin, dissolution of cement, microleakage, plaque retention, secondary decay, and gingival inflammation . Criticized for misfit before, digital design and production cycles and especially the CNC-milling technique were improved to meet clinical fit-requirements . Recent investigations on titanium frameworks even found superior precision of CNC-milled products when compared to their traditionally fabricated analogs. However, no data have been published on the precision of the actual CNC-milling step, although it was suspected to be a significant source of dimensional variability .
The objective of this in vitro study was to estimate the marginal and internal fit variability of lithium disilicate partial crowns that can be attributed to the CNC-milling procedure. This was accomplished using a structured light scanner that allowed the non-destructive three-dimensional assessment of the intaglio surface of a prepared molar . The tested null hypothesis was that CNC-milling does not affect the marginal or internal fit of partial coverage crowns fabricated from lithium disilicate glass ceramic blocks.
2
Materials and methods
2.1
Tooth preparation
An acrylic model of a mandibular left first molar (AG-3 ZE 36, Frasaco GmbH, Tettnang, Germany) was prepared to receive a partial crown restoration using a standard set of diamond burs (Set 4562, Brasseler GmbH, Lemgo, Germany). The preparation featured a 1.5 mm occlusal height reduction, a 1 mm rounded shoulder finish line of the buccal wall, and a 1 mm deep occlusal box. The 3 mm deep proximal grooves were finished with oscillating diamond tips (SONICflex prep ceram, KaVo Dental GmbH, Biberach, Germany) to achieve 90° margins as well as rounded and soft internal line angles.
2.2
Impression taking and cast fabrication
The prepared tooth was mounted in a typodont (AG-3, Frasaco GmbH). Five one-step dual viscosity impressions were taken with a vinyl siloxanether material (Identium, Kettenbach GmbH, Eschenburg, Germany). Light-bodied impression materials (viscosities according to ISO 4823:2000 ) were auto-mixed with a manual dispenser system (Applyfix 4, Kettenbach GmbH). Heavy-bodied impression materials were mixed and dispensed using a dynamic mixer (Sympress 6000, Renfert GmbH, Hilzingen, Germany). All impressions were taken under standard laboratory conditions (22 °C) by the same investigator (O.S.).
Next, the typodont was mounted on a rectangular base that featured three conical guide pins allowing for reproducible tray positioning. Light-bodied impression material (Identium Light, Kettenbach GmbH) was injected on and around the prepared tooth and dispersed using a brief air blast. The customized impression trays were filled with heavy-bodied material (Identium Heavy, Kettenbach GmbH), then lowered gently until the final position was reached.
All impressions were allowed to set three times longer than recommended by the manufacturer to assure adequate polymerization at room temperature. Shape and size of the tray ensured a minimum impression material thickness of 3 mm at any aspect of the prepared tooth . The impressions were inspected for defects using a magnifying glass (2.7× magnification, starVision SV1, starMed GbR, Munich, Germany). Impressions that did not show defects were allowed to recover for 2 h than spray-treated with 0.5 mL of Debubblizer Surfactant solution (Almore International Inc., Portland, USA) to reduce surface tension and improve the quality of the resulting cast . The surfactant remained untouched for 30 s until air was used to remove excess liquid. Then, casts were poured using type IV dental stone (Tewerock, Kettenbach GmbH). Distilled water (20 mL) and gypsum powder (100 g) were vacuum mixed for 45 s (Wamix-Classic, Wassermann Dental-Maschinen GmbH, Hamburg, Germany), and carefully poured into the impressions under constant vibration (KV-16, Wassermann Dental-Maschinen GmbH). Casts were allowed to set for 45 min before separation from the impression and final inspection.
2.3
Partial crown fabrication
Next, the casts were laser scanned (7Series, Dental Wings Inc., Montreal, Canada) to generate digital datasets. A calibration procedure with a standard metal block was performed prior to the first measurement and repeated whenever requested by the scanner’s software. The scanner projected single light bands onto the cast’s surface and recorded the signal simultaneously with three high-resolution cameras installed at fixed, predefined angles. The instrument thereby achieves a measurement uncertainty of 15 μm (according to manufacturer). Dental design software (DWOS, Dental Wings Inc.) used the scanned information to define an ideal insertion direction for the restoration and also selected the preparation margins. Finally, computer-aided designed restorations were calculated from a database of anatomical crown shapes and with respect to the minimum material thicknesses required for veneer crowns and to the material parameters for lithium disilicate restorations as provided by the manufacturer (vertical and horizontal cement gap: 60 μm, cervical cement gap: 20 μm, distance to margin: 1.2 mm, margin thickness: 0.2 mm, offset angle: 65°, drill radius 0.605 mm). Datasets were generated in STL format and served to determine the status before CNC-machining (PRE). The same datasets were then used to operate the fabrication of ceramic partial crowns from lithium disilicate blanks (IPS e.max CAD, Ivoclar Vivadent AG, Schaan, Liechtenstein). A five axis CNC-milling unit (Ultrasonic 20 linear, Sauer GmbH, Stipshausen, Germany) was used for machining restorations. The conventional rotation of the employed grinding tools is superimposed by an additional oscillation movement with a predefined vibration amplitude (so called kinematic oscillation). Thereby, low process forces can be realized, that enable the fabrication of thin-walled structures and significantly reduce surface and subsurface damage accumulation. The milling unit featured a special mounting mechanism that was able to pick up and fix the metal mandrel bonded to the lithium disilicate blank before milling.
2.4
Digitization and evaluation
The prepared reference tooth and the fabricated ceramic crowns were digitized using a self-calibrating structured-light scanner (Flex 3A, Otto Vision Technology GmbH, Jena, Germany). The instrument featured a measurement-uncertainty of <5 μm and a homogenous measuring-point-distance of 5 μm (manufacturer data). STL datasets as the primary output format of the reference scanner were computed for each restoration (POST) and the reference tooth as well.
PRE and POST records were superimposed on the prepared tooth by computing all possible orientations (Qualify 12, Geomagic GmbH, Stuttgart, Germany) and selecting the one with the best object-to-object penetration . The root mean square deviation (RMSD) was used to estimate dimensional differences between the reference surface of the prepared molar and the intaglio surface of the restorations. The average deviation x (RMSD) is frequently used to compare predicted and observed data ( Fig. 1 ).
Measurements were performed with emphasis on the preparation finish line (marginal fit) and the entire prepared surface of the reference tooth (internal fit). Color-coded difference images were used to analyse PRE and POST data semi-quantitatively. Image recognition algorithms (implemented by Eclipse Indigo, Eclipse Foundation Inc., Ottawa, Canada) were applied to compare similarities between corresponding graphics. Images were processed within a common color space, allocating red, green, and blue levels from a 2 8 element interval (RGB). Two corresponding pixels were considered similar if their red, green, and blue distances were smaller than 2 5 elements of the RGB-color space ( Fig. 2 ). The number of similar pixels was also used to calculate the degree of similarity (DS):
where h is the image height and w is the image width.
2.5
Statistical analysis
Statistical computations were made using IBM SPSS Statistics 19 software package (IBM SPSS Inc., Chicago, USA). Means (RMSD, DS), standard deviations, and upper and lower 95% confidence intervals were calculated for marginal and internal surfaces. The t -test ( p < 0.05) for paired comparisons was conducted to assess the difference between PRE and POST.
2
Materials and methods
2.1
Tooth preparation
An acrylic model of a mandibular left first molar (AG-3 ZE 36, Frasaco GmbH, Tettnang, Germany) was prepared to receive a partial crown restoration using a standard set of diamond burs (Set 4562, Brasseler GmbH, Lemgo, Germany). The preparation featured a 1.5 mm occlusal height reduction, a 1 mm rounded shoulder finish line of the buccal wall, and a 1 mm deep occlusal box. The 3 mm deep proximal grooves were finished with oscillating diamond tips (SONICflex prep ceram, KaVo Dental GmbH, Biberach, Germany) to achieve 90° margins as well as rounded and soft internal line angles.
2.2
Impression taking and cast fabrication
The prepared tooth was mounted in a typodont (AG-3, Frasaco GmbH). Five one-step dual viscosity impressions were taken with a vinyl siloxanether material (Identium, Kettenbach GmbH, Eschenburg, Germany). Light-bodied impression materials (viscosities according to ISO 4823:2000 ) were auto-mixed with a manual dispenser system (Applyfix 4, Kettenbach GmbH). Heavy-bodied impression materials were mixed and dispensed using a dynamic mixer (Sympress 6000, Renfert GmbH, Hilzingen, Germany). All impressions were taken under standard laboratory conditions (22 °C) by the same investigator (O.S.).
Next, the typodont was mounted on a rectangular base that featured three conical guide pins allowing for reproducible tray positioning. Light-bodied impression material (Identium Light, Kettenbach GmbH) was injected on and around the prepared tooth and dispersed using a brief air blast. The customized impression trays were filled with heavy-bodied material (Identium Heavy, Kettenbach GmbH), then lowered gently until the final position was reached.
All impressions were allowed to set three times longer than recommended by the manufacturer to assure adequate polymerization at room temperature. Shape and size of the tray ensured a minimum impression material thickness of 3 mm at any aspect of the prepared tooth . The impressions were inspected for defects using a magnifying glass (2.7× magnification, starVision SV1, starMed GbR, Munich, Germany). Impressions that did not show defects were allowed to recover for 2 h than spray-treated with 0.5 mL of Debubblizer Surfactant solution (Almore International Inc., Portland, USA) to reduce surface tension and improve the quality of the resulting cast . The surfactant remained untouched for 30 s until air was used to remove excess liquid. Then, casts were poured using type IV dental stone (Tewerock, Kettenbach GmbH). Distilled water (20 mL) and gypsum powder (100 g) were vacuum mixed for 45 s (Wamix-Classic, Wassermann Dental-Maschinen GmbH, Hamburg, Germany), and carefully poured into the impressions under constant vibration (KV-16, Wassermann Dental-Maschinen GmbH). Casts were allowed to set for 45 min before separation from the impression and final inspection.
2.3
Partial crown fabrication
Next, the casts were laser scanned (7Series, Dental Wings Inc., Montreal, Canada) to generate digital datasets. A calibration procedure with a standard metal block was performed prior to the first measurement and repeated whenever requested by the scanner’s software. The scanner projected single light bands onto the cast’s surface and recorded the signal simultaneously with three high-resolution cameras installed at fixed, predefined angles. The instrument thereby achieves a measurement uncertainty of 15 μm (according to manufacturer). Dental design software (DWOS, Dental Wings Inc.) used the scanned information to define an ideal insertion direction for the restoration and also selected the preparation margins. Finally, computer-aided designed restorations were calculated from a database of anatomical crown shapes and with respect to the minimum material thicknesses required for veneer crowns and to the material parameters for lithium disilicate restorations as provided by the manufacturer (vertical and horizontal cement gap: 60 μm, cervical cement gap: 20 μm, distance to margin: 1.2 mm, margin thickness: 0.2 mm, offset angle: 65°, drill radius 0.605 mm). Datasets were generated in STL format and served to determine the status before CNC-machining (PRE). The same datasets were then used to operate the fabrication of ceramic partial crowns from lithium disilicate blanks (IPS e.max CAD, Ivoclar Vivadent AG, Schaan, Liechtenstein). A five axis CNC-milling unit (Ultrasonic 20 linear, Sauer GmbH, Stipshausen, Germany) was used for machining restorations. The conventional rotation of the employed grinding tools is superimposed by an additional oscillation movement with a predefined vibration amplitude (so called kinematic oscillation). Thereby, low process forces can be realized, that enable the fabrication of thin-walled structures and significantly reduce surface and subsurface damage accumulation. The milling unit featured a special mounting mechanism that was able to pick up and fix the metal mandrel bonded to the lithium disilicate blank before milling.
2.4
Digitization and evaluation
The prepared reference tooth and the fabricated ceramic crowns were digitized using a self-calibrating structured-light scanner (Flex 3A, Otto Vision Technology GmbH, Jena, Germany). The instrument featured a measurement-uncertainty of <5 μm and a homogenous measuring-point-distance of 5 μm (manufacturer data). STL datasets as the primary output format of the reference scanner were computed for each restoration (POST) and the reference tooth as well.
PRE and POST records were superimposed on the prepared tooth by computing all possible orientations (Qualify 12, Geomagic GmbH, Stuttgart, Germany) and selecting the one with the best object-to-object penetration . The root mean square deviation (RMSD) was used to estimate dimensional differences between the reference surface of the prepared molar and the intaglio surface of the restorations. The average deviation x (RMSD) is frequently used to compare predicted and observed data ( Fig. 1 ).
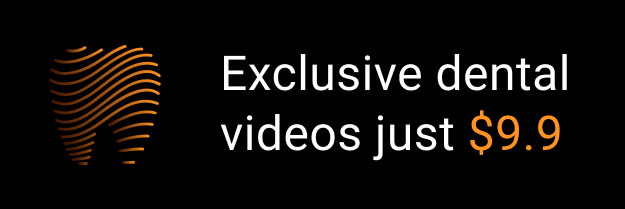