Introduction
Three-dimensional (3D) printing technologies are profoundly changing the landscape of orthodontics. To optimize treatment-oriented applications, dimensional fidelity is required for 3D-printed orthodontic models. This study aimed to evaluate the effect of build angle and layer height on the accuracy of 3D-printed dental models and if each of their influences on print accuracy was conditional on the other.
Methods
A maxillary cast was scanned using an intraoral scanner. One hundred thirty-two study models were printed at various combinations of build angle (0°, 30°, 60°, 90°) and layer height (20 μm, 50 μm, 100 μm) with a digital light processing printer (n = 11 per group). The models were digitally scanned, and deviation analyzed using a 3D best-fit algorithm in metrology software.
Results
A statistically significant interaction was consistently found between build angle and layer height for each positive deviation, negative deviation, and proportion out of bounds. Average deviations of all study models were within clinically acceptable ranges, but the least accurate models were printed at 0°/20 μm. Although there was a tendency for an oblique build angle of 30° or 60° with a smaller layer height of 20 μm or 50 μm to print the most accurate models, 95 % confidence intervals overlapped with all other angles and heights except for 0°/20 μm.
Conclusions
Build angle and layer height have statistically significant interactive effects on the accuracy of 3D-printed dental models. Overall, digital light processing printers produced models within clinically acceptable bounds, but the choice of build angle and layer height should be considered in conjunction with the clinical application, desired print time, and preferred efficiency of each print job.
Highlights
- •
Build angle and layer height interacted to affect the accuracy of 3-dimensional-printed models.
- •
Average deviations of all study models were within clinically acceptable ranges.
- •
A combination of 0° build angle and 20 μm layer height produced the least accurate models.
- •
Clinical and workflow requirements should inform selection of build angle and layer height.
Three-dimensional (3D) printing technologies are a major force driving the rapid digital transformation in modern orthodontics. From new treatment modalities such as aligner therapy to customized choices of 3D-printed brackets, 3D imaging and printing have made the delivery of orthodontic treatment possible through an almost entirely digital workflow.
Three-dimensional printers build an object layer by layer with a printable material such as resin. A critical factor in the success of orthodontic 3D printers is their dimensional accuracy, particularly when applications involve precise tooth movement or precise tooth fit and retention. Among various printing technologies, stereolithography (SLA) and digital light processing (DLP) are the major printer types currently used by orthodontists. Many factors throughout the digital workflow can affect the fidelity of printed models, including the accuracy of the digital model created by an intraoral scanner. However, the layer-by-layer additive nature of 3D printers makes build angle and layer height particularly important print settings for the accuracy of a 3D print.
Build angle is the orientation of the printed model with respect to the printer build platform. As the build angle changes, the geometry of printed layers changes. This, in turn, changes the supporting relationship of a given print layer to its successively printed layers, which can ultimately affect the print accuracy in that region. , Studies by Alharbi et al have shown that out of 9 different build angles from 90° to 270°, a 3D-printed full-coverage crown was most accurate at 120° and 135° when produced by an SLA and DLP printer, respectively. Short et al reported that orthodontic models printed with an SLA printer were the least accurate at the build angle of 90° (base perpendicular to the platform) compared with 0° and 20°.
Layer height is the height of each layer of a print material extruded, cured, or sintered by a 3D printer. Notably, a smaller layer height, synonymous with a higher z-axis resolution, does not necessarily correspond to a more accurate 3D print. The effect of layer height on print accuracy can be further complicated by the printing technologies and the geometric complexity of dental models. , Favero et al have reported that larger layer heights printed more accurate dental models by the Form 2 SLA printer, with 100 μm models more accurate than 50 μm models and 50 μm more accurate than 25 μm. Yet, Zhang et al observed the opposite relationship using the same Form 2 SLA printer and found that the 100 μm layer height had the lowest print accuracy for dental models compared with 50 μm and 25 μm. They also reported that 50 μm was the most accurate layer height by DLP printers compared with 25 μm and 100 μm.
Despite growing research interests, the effects of build angle and layer height on the accuracy of 3D-printed dental models have only been investigated independently so far with a single predetermined layer height and a single predetermined build angle, respectively. , It is unclear whether there is any crucial interplay between build angle and layer height in shaping the accuracy of printed dental models. The influence of one factor on accuracy could well depend on or be conditional on the other. In application, both factors need to be determined by clinicians or technicians before any orthodontic 3D printing processes. Therefore, this study aimed to evaluate the independent and interactive effects of build angle and layer height on the accuracy of 3D-printed orthodontic models using a DLP printer.
Material and methods
The maxillary arch of a posttreatment, American Board of Orthodontics quality plaster cast (reference model) was scanned with the intraoral iTero Element 2 scanner (Align Technology, Santa Clara, Calif) and converted into a standard tessellation language (STL) file. Using Netfabb software (Autodesk, San Rafael, Calif), a reference plane was set up for the digital model using 3 points: the apices of the buccal gingival margin of the first molars and the midpoint of the line connecting the apices of the facial gingival margin of the central incisors. The digital model was cut with a plane parallel to and 6 mm above the reference plane, generating the master STL file.
Study models from the master STL file were printed on a MoonRay S printer (SprintRay, Model Gray resin, Los Angeles, Calif) with varying build angles (0°, 30°, 60°, 90°) and layer heights (20 μm, 50 μm, 100 μm) ( Fig 1 , A ). Power analysis with an intermediate effect size showed that a sample size of 11 for each of the 12 build angle and layer height groups would yield a power of 0.8, with α = 0.05.

The MoonRay S printer allows for simultaneous printing of maximally 2 models with the same layer height for each print job at a 0° build angle. Therefore, stratified randomization with Excel (Microsoft Office; Microsoft, Redmond, Wash) list randomizer was used first to randomize the front and back print position within each layer height group, and then the print job order for all groups. The printer was calibrated according to the manufacturer’s instructions. Two images of the master STL file were opened in Legacy RayWare (version 1.4.6; SprintRay) and oriented with the base flat and incisors centered on the platform and the posterior base parallel to the front end of the platform. The 2 images were each further oriented in their desired build angles between the base and the platform ( Fig 1 , B ). The 30° and 60° models had print supports generated automatically by the software between the base and the platform, whereas the 0° and 90° orientations were printed directly on the platform. The oriented images were then printed with a predetermined layer height of 20 μm, 50 μm, or 100 μm according to our randomization design.
Postprinting, models were left on the platform for 5-10 minutes to allow the extra resin to drip off into the resin tank. The excess resin was removed with a rubber spatula. The entire build platform, including the models, was removed from the printer, washed in a 90 % isopropyl alcohol bath with agitation for 5-10 minutes, and gently cleaned with a soft toothbrush to remove the remaining excess uncured resin. Models were then removed from the platform with a metal scraper and supports cut with a flush cutter per the manufacturer’s recommendation. Models were further air-dried, cured in a SprintRay ultraviolet unit for 15 minutes, and scanned to produce study STL files using the same iTero Element 2 scanner.
The master and study STL images were further trimmed digitally to remove nonanatomic structures with approximately 4 mm of remaining soft tissue. Each study STL file was then superimposed with the master STL file using the best-fit algorithm of the metrology software (Geomagic Control, version 2015.1.1; 3D Systems, Rock Hill, SC), and surface deviations were quantified using the 3D Compare tool in the software. On the basis of previous studies, the bounds for acceptability were set at ± 0.25 mm. Points from the study STL file deviating from the master STL file more than 0.25 mm were considered out of bounds, either positively or negatively.
Statistical analysis
Generalized linear models (GLM) were used to analyze the independent and combined effects of build angle and layer height on each of 4 response variables, namely standard deviation (SD), positive deviation (PD), negative deviation (ND), and proportion out of bounds (POB). SD was the extent of total deviation of the study model from the reference model. PD was the extent of all deviation of the study model in the positive direction. ND was the extent of all deviation in absolute value in the negative direction. Finally, POB was the proportion of points deviating beyond the bound of 0.25 mm in both positive and negative directions. The GLM error distributions were gamma (SD, PD, ND) or quasibinomial (POB), as the response variables were not normally distributed. Confidence intervals (95 % confidence interval [CI]) were reported for each combination group of build angle and layer height. Statistical analyses were performed using R statistical software (R Foundation for Statistical Computing, Vienna, Austria).
Results
GLM models showed a statistically significant interaction between build angle and layer height for PD, ND, and POB ( Table ). The interaction was marginally significant for SD ( Table ) ( P = 0.065). These data indicate that build angle and layer height have a complex and interactive effect on the accuracy of 3D-printed models, whereby the effects of build angle and layer height depend on one another in shaping accuracy.
Variables | LR χ 2 | Df | P (>χ 2 ) |
---|---|---|---|
SD | |||
Angle | 53.635 | 3 | <0.001 ‡ |
Layer height | 16.377 | 2 | <0.001 ‡ |
Angle to layer height | 11.888 | 6 | 0.065 |
PD | |||
Angle | 45.124 | 3 | <0.001 ‡ |
Layer height | 10.796 | 2 | 0.005 † |
Angle to layer height | 14.984 | 6 | 0.020 ∗ |
ND | |||
Angle | 10.964 | 3 | 0.012 ∗ |
Layer height | 16.418 | 2 | <0.001 ‡ |
Angle to layer height | 20.471 | 6 | 0.002 † |
POB | |||
Angle | 19.2059 | 3 | <0.001 ‡ |
Layer height | 6.7938 | 2 | 0.034 ∗ |
Angle to layer height | 14.8371 | 6 | 0.022 ∗ |
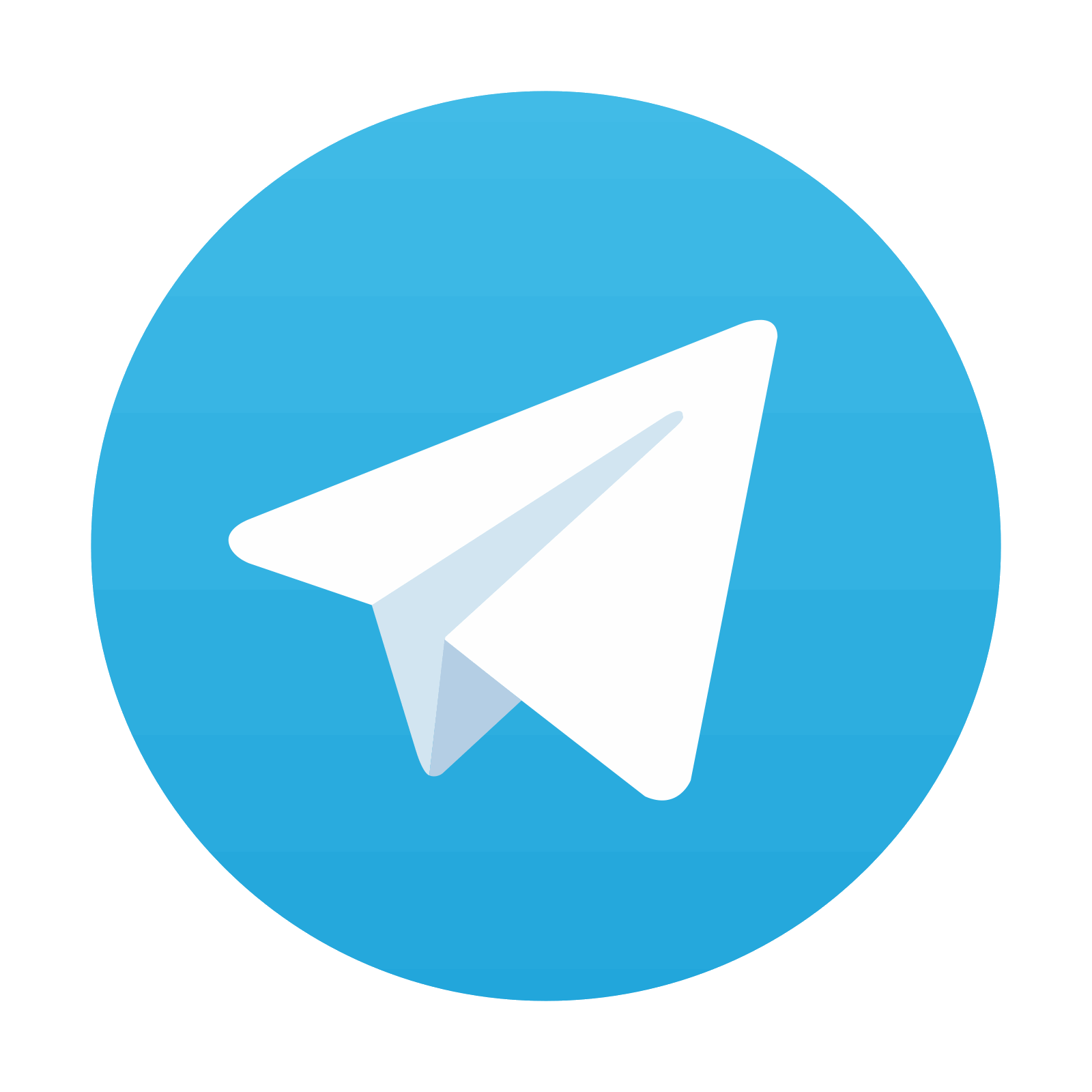
Stay updated, free dental videos. Join our Telegram channel

VIDEdental - Online dental courses
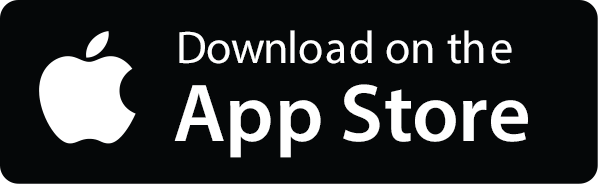

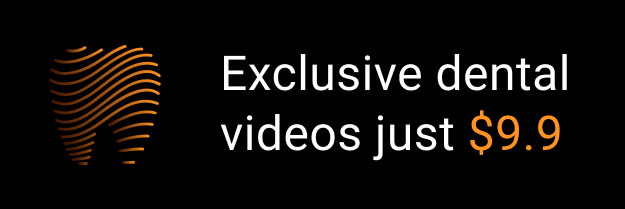