Abstract
The objective was to investigate the influence of maxillary alveolar bone on the stress distribution of zygomatic implants in an extra-sinus position. A three-dimensional finite element model was created based on a computed tomography scan of an edentulous female patient. Two zygomatic implants were modelled and placed in the skull in an extra-sinus position. These were supported by the zygomatic bone and the maxillary alveolar bone and were connected by a fixed bridge. This model was duplicated, and the area of the maxillary alveolar bone supporting the implants was removed. Occlusal and lateral forces were applied to both models and the maximum von Mises stresses were recorded. Higher maximum stresses were noted in the model with no alveolar support. Occlusal stresses were higher than lateral stresses in the model with no alveolar support, while occlusal stresses were lower than lateral stresses in the model with alveolar support. Low stresses were noted in the zygomatic bone in both models. Maxillary alveolar bone support is beneficial in the distribution of forces for zygomatic implants placed in an extra-sinus position.
Zygomatic implants may be used in the severely atrophic maxilla to support fixed or removable prosthodontics. Intra- and extra-sinus positions for zygomatic implants have been described, both with high success rates. They provide an alternative for patients who do not have sufficient maxillary bone to retain conventional dental implants and for whom grafting procedures are unsuitable.
Brånemark originally proposed that zygomatic implants should be placed, via the sinus, into the zygomatic bone with support from the maxillary alveolar or palatal bone at the coronal end of the implant. The sinus slot technique was described by Stella and Warner in 2000. It places the implant along the lateral wall of the maxillary sinus and provides some significant advantages over the original technique. Direct visualization of the implant is facilitated during the surgery when an extra-sinus position is used. Placing the implant outside of the maxillary sinus may also achieve a more favourable restorative position. It is often possible to place the head of the implant in the line of the maxillary dental arch. An extra-sinus position is not always possible due to regional anatomical variation. Chow et al. in 2010 reported that no patients in their series of 37 extra-sinus zygomatic implants developed sinus problems when a modified surgical technique was used to protect the sinus membrane and prevent perforations occurring.
Our group previously investigated the effect of alveolar bone on the stress distribution of zygomatic implants in an intra-sinus position. It was demonstrated that alveolar bone was beneficial for the support of zygomatic implants in a finite element analysis (FEA) model. Low stresses were shown to be transmitted to the zygomatic bone due to occlusal and lateral forces applied to a bridge supported by zygomatic implants. This study investigated the importance of the alveolar bone in supporting zygomatic implants placed in an extra-sinus position using a modified finite element model.
Materials and methods
Model construction
A three-dimensional computer model of half of a skull was used for this study. The model was based on a computed tomography (CT) scan of a consenting edentulous adult female undergoing zygomatic implant placement, which was converted into a virtual solid model. The details of the construction of this model are described in a previous study. Briefly, this involved converting the CT scan into a stereolithography (STL) file using Mimics software (version 12, Materialise NV, Leuven, Belgium). This file was repaired using netfabb software (version 4, netfabb GmbH, Parsberg, Germany) and converted to a surface composed of non-uniform rational B splines using Rhinoceros 3D (version 4, McNeel North America, Seattle, WA, USA). This surface model was converted into a virtual solid model using SolidWorks (version 2011, Dassault Systèmes SolidWorks Corporation, Waltham, MA, USA).
Virtual solid models of two zygomatic implants were created based on the manufacturer’s information. These incorporated a bend at the coronal ends of the implants to correspond to the angled head of zygomatic implants. The threads of the implants were omitted as all elements would be considered to be continuous in our FEA. The implants were positioned so that their apices were embedded in the zygomatic bone. The coronal ends of the implants were positioned along the line of the residual maxillary arch in the canine and premolar areas. The implants passed along the lateral wall of the maxillary sinus as described in the sinus slot technique. A virtual bar of 6 mm by 10 mm in cross-section was formed along the line of the maxillary arch to simulate a rudimentary bridge. The heads of the implants were extended to meet the bar in order to simulate abutments. All components were assembled, creating a model of a fixed bridge supported by zygomatic implants ( Fig. 1 ). This model was duplicated and holes of diameter 5.5 mm were made around both implants as they passed through the maxillary bone. This left a gap of 0.5 mm around the implants in the maxillary alveolar bone, preventing the implants being supported in this area ( Fig. 2 ).


Material properties
All components of the model were considered to be homogeneous and linearly elastic. The properties of the bony components were based on averaged values described in cadaver studies of the human skull. The properties of the bridge and implant were based on known properties for commercially pure titanium. The values used are shown in Table 1 .
Property | Bridge and zygomatic implant | Skull |
---|---|---|
Elastic modulus | 1.05 × 10 11 N/m 2 | 1.5 × 10 10 N/m 2 |
Poisson’s ratio | 0.37 | 0.34 |
Mass density | 4510 kg/m 3 | 1678 kg/m 3 |
Mesh creation and analysis
A mesh was generated from the solid models and consisted of 33,151 elements and 8541 nodes for the model with alveolar support and 32,631 elements and 8531 nodes for the model without alveolar support. The superior elements of the model were fully restrained, while the medial elements of the model were restrained using a slider–roller restraint. This allowed no movement at the superior aspect of the skull but permitted movement in the vertical plane at the midline of the skull. This set-up was designed to best simulate the mirrored other half of the skull.
Forces were applied to each model individually in the molar area of the bridge at varying angles to the occlusal plane in order to assess the effect of changes in force direction. The magnitudes of the forces directed normal to the occlusal plane and at 30° in a buccal and palatal direction were varied to assess the effect of changes in force magnitude. Magnitudes of 50–600 N were analysed, which were designed to exceed known masticatory forces. A three-dimensional FEA was run and maximum von Mises stresses were recorded for each model under the different loads. Graphical representations of the von Mises stresses were produced to demonstrate the location of the stresses in the implants, bridge, and skull.
Material properties
All components of the model were considered to be homogeneous and linearly elastic. The properties of the bony components were based on averaged values described in cadaver studies of the human skull. The properties of the bridge and implant were based on known properties for commercially pure titanium. The values used are shown in Table 1 .
Property | Bridge and zygomatic implant | Skull |
---|---|---|
Elastic modulus | 1.05 × 10 11 N/m 2 | 1.5 × 10 10 N/m 2 |
Poisson’s ratio | 0.37 | 0.34 |
Mass density | 4510 kg/m 3 | 1678 kg/m 3 |
Mesh creation and analysis
A mesh was generated from the solid models and consisted of 33,151 elements and 8541 nodes for the model with alveolar support and 32,631 elements and 8531 nodes for the model without alveolar support. The superior elements of the model were fully restrained, while the medial elements of the model were restrained using a slider–roller restraint. This allowed no movement at the superior aspect of the skull but permitted movement in the vertical plane at the midline of the skull. This set-up was designed to best simulate the mirrored other half of the skull.
Forces were applied to each model individually in the molar area of the bridge at varying angles to the occlusal plane in order to assess the effect of changes in force direction. The magnitudes of the forces directed normal to the occlusal plane and at 30° in a buccal and palatal direction were varied to assess the effect of changes in force magnitude. Magnitudes of 50–600 N were analysed, which were designed to exceed known masticatory forces. A three-dimensional FEA was run and maximum von Mises stresses were recorded for each model under the different loads. Graphical representations of the von Mises stresses were produced to demonstrate the location of the stresses in the implants, bridge, and skull.
Results
The maximum von Mises stresses recorded for each of the models is shown in Table 2 . The distributions of these stresses in the models and the implants are shown in Figs. 3–8 . In both models, the maximum stresses increased linearly as the applied force was increased, regardless of force direction ( Fig. 9 ). The maximum stresses were located within the bridge or at the coronal end of the implants in both models. The stresses observed within the zygomatic bone were low in both models when compared to the stresses observed in the implants.
Model | Force | 50 N | 150 N | 300 N | 600 N |
---|---|---|---|---|---|
With alveolar support | Occlusal | 5.046 | 15.139 | 30.277 | 60.554 |
30° Buccal | 7.152 | 21.455 | 42.91 | 85.82 | |
30° Palatal | 6.477 | 19.432 | 38.864 | 77.727 | |
Without alveolar support | Occlusal | 11.545 | 34.635 | 69.269 | 138.54 |
30° Buccal | 8.151 | 24.435 | 48.907 | 97.813 | |
30° Palatal | 8.895 | 26.686 | 53.372 | 106.75 |
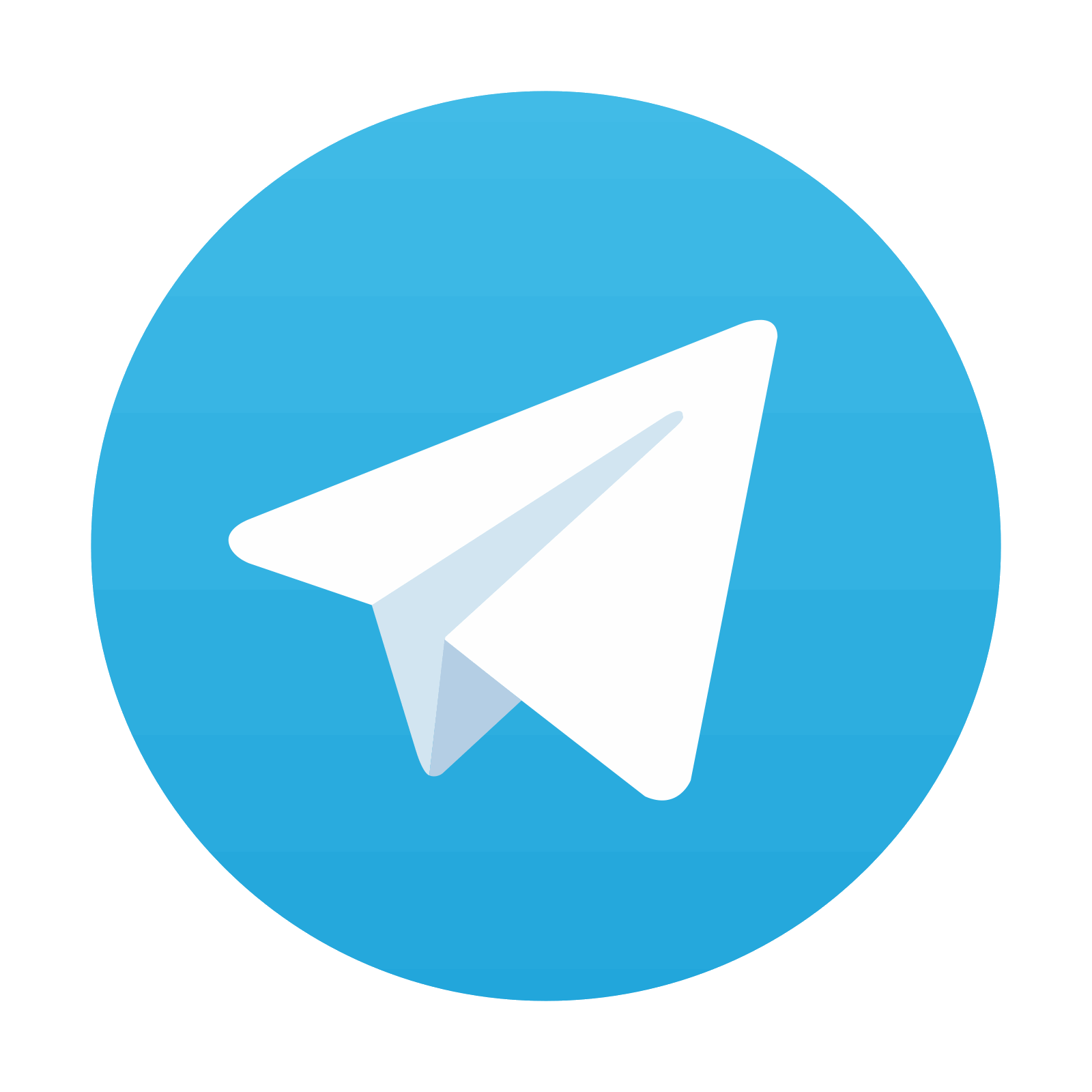
Stay updated, free dental videos. Join our Telegram channel

VIDEdental - Online dental courses
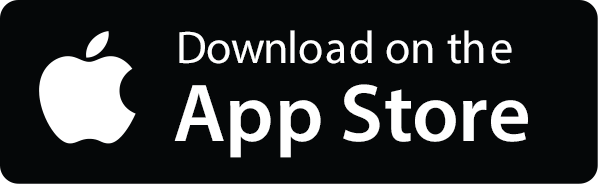

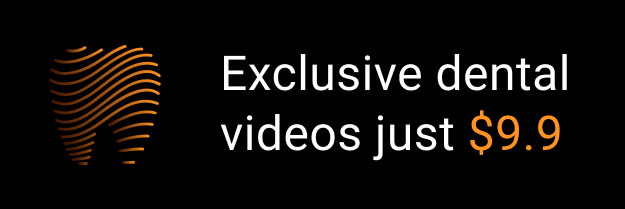