Introduction
Recently, manufacturers have marketed alginate impression materials, claiming dimensional stability for up to 100 hours to allow shipping to a dental laboratory for digital model fabrication. The purpose of this study was to evaluate the dimensional changes of these newer materials after storage at different temperatures and times.
Methods
Two extended-pour alginates (claiming 100 hours of accuracy) (Kromopan; Lascod, Florence, Italy; and Triphasix; Parkell, Edgewood, NY), 2 traditional alginates (Jeltrate; Dentsply-Caulk, York, Pa; and Kromatica; Matech, Sylmar, Calif), and 1 vinyl polysiloxane (VP Mix; Henry Schein, Melville, NY) were used to impress a scored aluminum die. The distance between the score lines was measured on the impressions at 10 minutes, 24 hours, and 100 hours after mix, and the percentages of dimensional change were calculated. Temperature effects were studied by storage at cold (–9°C), room (22°C), or hot (46°C) temperatures for 8 hours.
Results
All alginates had statistically significant dimensional changes at 24 and 100 hours (0.69%-6.13%). VP Mix exhibited no statistically significant changes for any storage condition. The Kromopan (100 hour) and Kromatica (traditional) alginates were the most stable (0.85%-2.22% at 100 hours). Triphasix (100 hour) and Jeltrate (traditional) were the least stable (1.53%-4.73% at 100 hours). Cold-temperature storage resulted in the most dimensional changes (1.96%-4.73% at 100 hours). Room-temperature storage resulted in the least dimensional changes (0.97%-1.53% at 100 hours).
Conclusions
All alginate impression materials in the study had significant changes at 24 and 100 hours in all storage conditions tested.
Digital models to augment and, in many instances, replace gypsum dental casts are being used in orthodontic offices because of their unique advantages. One digital model company claims to have processed more than 1,000,000 patients. Proponents of digital models suggest that the advantages of digital models include (1) reduced need for storage, (2) easy retrievability at chairside, (3) ease of transfer to colleagues, and (4) accurate measurements of tooth and arch dimensions.
This ability of the commercial software to provide accurate measurements electronically might be undermined by how digital models are produced by commercial companies. The process used to produce the digital model is different for different companies, varying from laser scanning poured plaster models to cone-beam computed tomography scans of the impression and digital scans of the patient’s dental arches. A common technique is making alginate impressions of a patient’s dentition by the orthodontic staff and sending the impressions to the digital model company via a commercial courier service. After the impression is processed by any of the above methods, a 3-dimensional digital image is available to the orthodontist via electronic download from the company’s Web site in 4 or 5 business days. The accuracy of this process is predicated on the assumption that the alginate impression is dimensionally stable and the process is accurate. This assumption might not be correct.
Traditional alginate materials produce impressions that are dimensionally unstable, and an accurate representation of the impressed structures is only achievable if the gypsum model is poured immediately. Dimensional stability is defined as the ability of a material to maintain its dimensional accuracy over a period of time. Recently, manufacturers have brought new products to the marketplace, with the claim that these new alginates are stable for up to 120 hours; these are called “extended-pour” or “100-hour alginates.”
Despite the manufacturers’ claims of dimensional stability, the studies of the extended-pour alginates provide mixed results on the accuracy of the manufacturers’ claims. In addition, questions arise regarding the dimensional changes that occur in the stored impressions of these alginates when they are subjected to extremely hot or cold temperatures during transit from the orthodontic office to the digital model laboratory. Studies that included shipping as part of their protocol did not control the environmental variables associated with shipping and did not include temperature extremes.
The purpose of this study was to evaluate the dimensional changes of 2 traditional irreversible hydrocolloids, 2 newer extended-pour irreversible hydrocolloids, and a vinyl polysiloxane impression material at 10 minutes and 24 and 100 hours after mixing, and the effect of extreme temperatures that might be experienced during shipping with commercial courier services.
Material and methods
To evaluate the dimensional changes of the extended-pour (claiming 100 hours of accuracy) alginates, a stainless steel die similar to the American Dental Association’s specification number 19 was fabricated, but with sharp and deeply scored lines that allowed easy visualization and accurate measurement directly on the impression materials ( Fig 1 ). This registration avoided pouring a gypsum cast and the variability of gypsum’s inherent dimensional change; hence, the change in the impression material alone was evaluated. The distance between score marks was measured on the die and the impression surface by using a measuring microscope (Gaertner Scientific, Chicago, Ill) accurate to ±2 μm. The measured distance on the impression was then directly compared with the true distance on the standardized die (20.192 mm) to determine the amount of linear change.
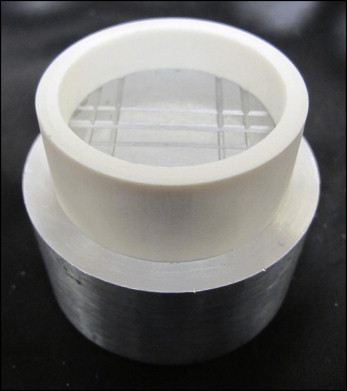
The sample groups consisted of 2 brands of extended-pour, 100-hour alginate, impression materials, Kromopan (Lascod, Florence, Italy) and Triphasix (Parkell, Edgewood, NY); 2 brands of traditional alginate impression materials, Jeltrate (Dentsply-Caulk, York, Pa) and Kromatica (Matech, Sylmar, Calif), and 1 brand of vinyl polysiloxane impression material as a control, VP Mix Monophase (Henry Schein, Melville, NY). A total of 75 specimens were divided into 5 groups of 15 specimens for each impression material and further subdivided into 3 temperature subgroups of 5 specimens each, all of which were measured at 10 minutes, 24 hours, and 100 hours after the start of the mix. One subgroup for each impression material was stored at room temperature (23°C), and the other 2 subgroups were stored at either a high (46°C) or a low (–9°C) temperature for the first 8 hours to examine the effect of temperature extremes that might occur during commercial shipping in hot or cold climates. All specimens were made at room temperature (23°C) and were removed from the die at 7 to 8 minutes from the start of the mix to ensure full set and measured immediately, at 10 minutes after the start of mix. After the first measurement, the specimens were stored according to the digital model companies’ recommendations for shipping: ie, each specimen was wrapped in a wet paper towel and sealed in a plastic bag with 1 tablespoon of distilled water. The specimens were then stored at either room (23°C) or hot (46°C) or cold (–9°C) temperature for 8 hours. At the end of 8 hours, all specimens were brought to room temperature (if required) and stored at room temperature for the remaining time before the measurements at 24 and 100 hours.
The impression material for each specimen was carefully measured and mixed by hand by the principal investigator (J.A.T.) according to the manufacturer’s directions. Although Frey et al found that the mechanical properties of alginates are improved using a mechanical mixer, the volumes of alginate needed for our study were too small to allow the proper use of a mechanical mixer. The technique is consistent with the method of hand mixing used in a dental office. The “impression trays” were constructed from 1.5-in diameter polyvinyl chloride pipe, which fit closely around the scored die and allowed a consistent thickness of impression material and consistent tray placement ( Fig 1 ). The alginate was retained in the “impression tray” by using tray adhesive (Henry Schein). A light layer of separating medium (Vaseline; Unilever, London, United Kingdom) was applied to the die to allow separation of the impression without sticking and consequent distortion of the impression material.
Statistical analysis
Means and standard deviations were calculated for each experimental group. A 3-way analysis of variance (ANOVA) was used to assess the effects of material brand, storage temperature, and storage time and their interactions, followed by a Student-Newman-Kuels post-hoc test as needed. Alpha was predetermined at P ≤0.05.
Results
The results are presented in Tables I and II and Figures 2 through 4 and explained below.
Brand (material type) | Storage temperature | n | Time after start of mix | Statistical difference between brands P ≤0.05 | Statistical difference of temperature within brand P ≤0.05 | |||||
---|---|---|---|---|---|---|---|---|---|---|
10 min | 24 h | 100 h | ||||||||
Specimen size (mm) mean ± SD | Dimensional change (%) | Specimen size (mm) mean ± SD | Dimensional change (%) | Specimen size (mm) mean ± SD | Dimensional change (%) | |||||
Jeltrate (traditional) | Cold (–9°C) | 5 | 20.07 ± 0.11 | −0.59 ± 0.53 | 19.30 ± 0.52 | −4.44 ± 2.60 | 19.39 ± 0.23 | −3.96 ± 1.15 | a | A |
Room (22°C) | 5 | 20.16 ± 0.11 | −0.17 ± 0.56 | 20.05 ± 0.12 | −0.69 ± 0.61 | 19.85 ± 0.17 | −1.72 ± 0.82 | B | ||
Hot (46°C) | 5 | 20.07 ± 0.11 | −0.60 ± 0.57 | 19.61 ± 0.34 | −2.90 ± 1.69 | 19.88 ± 0.12 | −1.53 ± 0.61 | A, B | ||
Kromatica (traditional) | Cold (–9°C) | 5 | 20.13 ± 0.13 | −0.29 ± 0.63 | 19.74 ± 0.58 | −2.24 ± 2.86 | 19.74 ± 0.36 | −2.22 ± 1.77 | b | i |
Room (22°C) | 5 | 20.11 ± 0.07 | −0.38 ± 0.37 | 20.02 ± 0.08 | −0.85 ± 0.38 | 19.94 ± 0.06 | −1.25 ± 0.28 | i | ||
Hot (46°C) | 5 | 20.20 ± 0.65 | 0.03 ± 3.20 | 19.89 ± 0.18 | −1.49 ± 0.88 | 19.98 ± 0.33 | −1.05 ± 1.66 | ii | ||
Kromopan (extended pour) | Cold (–9°C) | 5 | 19.92 ± 0.37 | −1.34 ± 1.85 | 19.57 ± 0.12 | −3.10 ± 0.58 | 19.80 ± 0.17 | −1.96 ± 0.86 | b | α |
Room (22°C) | 5 | 20.21 ± 0.07 | 0.07 ± 0.34 | 20.42 ± 0.09 | 1.14 ± 0.44 | 20.36 ± 0.11 | 0.85 ± 0.55 | ηα | ||
Hot (46°C) | 5 | 20.06 ± 0.09 | −0.67 ± 0.43 | 19.98 ± 0.11 | −1.07 ± 0.56 | 20.00 ± 0.12 | −0.97 ± 0.60 | ηα | ||
Triphasix (extended pour) | Cold (–9°C) | 5 | 20.06 ± 0.06 | −0.67 ± 0.31 | 18.95 ± 0.37 | −6.13 ± 1.81 | 19.24 ± 0.28 | −4.73 ± 1.40 | a | L |
Room (22°C) | 5 | 20.18 ± 0.10 | −0.08 ± 0.51 | 19.94 ± 0.12 | −1.23 ± 0.61 | 19.75 ± 0.19 | −2.17 ± 0.96 | M | ||
Hot (46°C) | 5 | 20.12 ± 0.03 | −0.36 ± 0.15 | 19.86 ± 0.12 | −1.67 ± 0.61 | 19.88 ± 0.13 | −1.60 ± 0.66 | L, M | ||
VP Mix | Cold (–9°C) | 5 | 20.20 ± 0.02 | 0.05 ± 0.08 | 20.15 ± 0.04 | −0.21 ± 0.20 | 20.14 ± 0.04 | −0.24 ± 0.21 | c | 1 |
Room (22°C) | 5 | 20.17 ± 0.06 | −0.11 ± 0.30 | 20.15 ± 0.04 | −0.20 ± 0.17 | 20.15 ± 0.06 | −0.20 ± 0.27 | 1 | ||
Hot (46°C) | 5 | 20.14 ± 0.03 | −0.26 ± 0.17 | 20.14 ± 0.02 | −0.28 ± 0.09 | 20.14 ± 0.06 | −0.25 ± 0.30 | 1 |
Storage temperature | Brand (material type) | Statistical difference between temperatures P ≤0.05 | Statistical difference of brand within temperature P ≤0.05 |
---|---|---|---|
Cold (–9°C) | Jeltrate (traditional) | a | a |
Kromatica (traditional) | b, c | ||
Kromopan (100 hour) | a, c | ||
Triphasix (100 hour) | a | ||
VP Mix | d | ||
Room (22°C) | Jeltrate (traditional) | b | α |
Kromatica (traditional) | β | ||
Kromopan (100 hour) | β | ||
Triphasix (100 hour) | γ | ||
VP Mix | δ | ||
Hot (46°C) | Jeltrate (traditional) | c | 1 |
Kromatica (traditional) | 2 | ||
Kromopan (100 hour) | 2 | ||
Triphasix (100 hour) | 2 | ||
VP Mix | 3 |
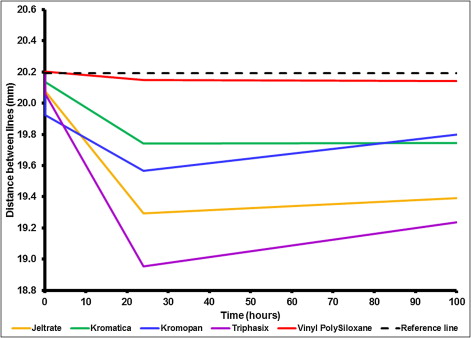
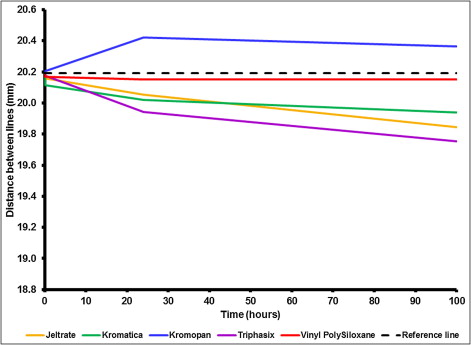
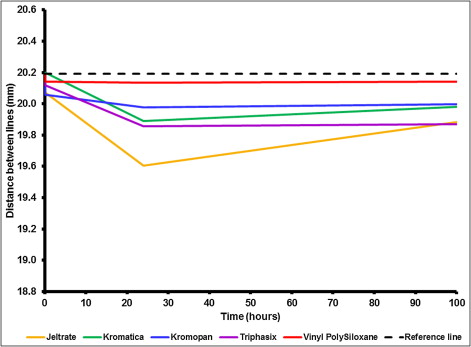
Statistical analysis of the vinyl polysiloxane samples showed no statistically significant differences between the mean measurements regardless of storage temperature or duration. All vinyl polysiloxane samples showed dimensional changes less than 0.30%.
When measured at 24 and 100 hours, all alginate samples had significant dimensional changes from the original die and the vinyl polysiloxane specimens. No significant differences were found between any alginates when measured at 10 minutes after the start of impression mix. From 10 minutes to 24 hours, there were statistically significant dimensional changes in all alginates. However, from 24 to 100 hours, there was no significant dimensional change, regardless of storage condition.
When all storage conditions were grouped together, Kromopan (extended pour) and Kromatica (traditional) exhibited significantly less dimensional changes than did Triphasix (extended pour) and Jeltrate (traditional).
There were temperature effects on the impression materials. Storage at below freezing temperatures for 8 hours affected the dimensional changes of alginates differently ( Fig 3 ). However, all alginate samples stored at freezing temperatures showed double the percentages of dimensional changes at 24 and 100 hours than did those stored at either hot or room temperature. The dimensional changes of Triphasix (extended pour) and Jeltrate (traditional) were not significantly different from each other. Kromopan (extended pour) and Kromatica (traditional) were also not significantly different from each other. These 2 subgroups, however, were statistically different from each other. At room temperature, the dimensional changes of all alginate samples were significantly different from each other, with the exception of Krompan (100 hour) and Kromatica (traditional), which were not significantly different ( Fig 3 ). Storage at a hot temperature for 8 hours also affected the impression materials ( Fig 4 ). Jeltrate (traditional) at high temperatures responded significantly differently from all other impression materials. Kromopan (extended pour), Kromatica (traditional), and Triphasix (extended pour) were not statistically different from each other. Room-temperature samples showed the least dimensional changes, with hot storage resulting in more changes and cold storage the highest percentages of dimensional changes.
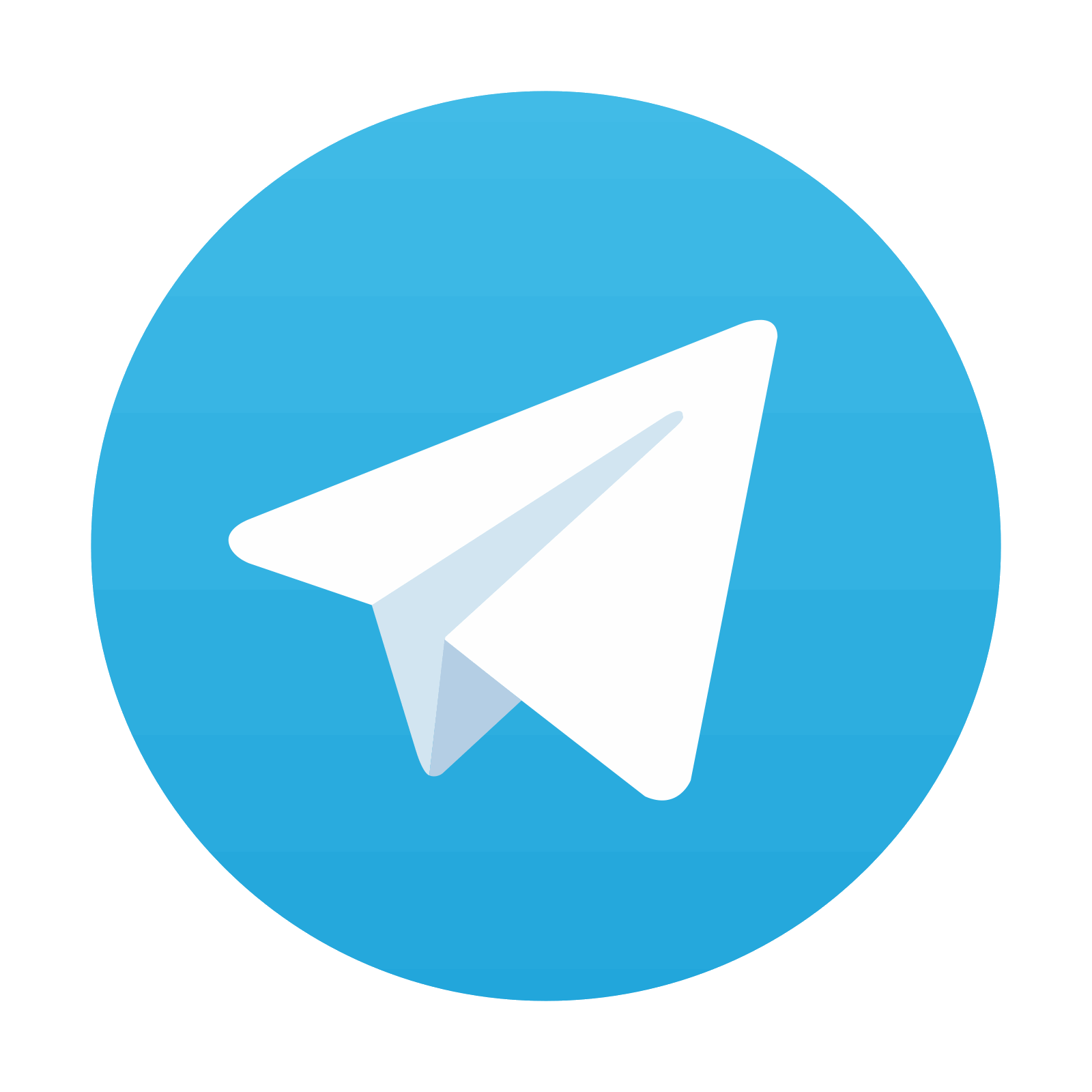
Stay updated, free dental videos. Join our Telegram channel

VIDEdental - Online dental courses
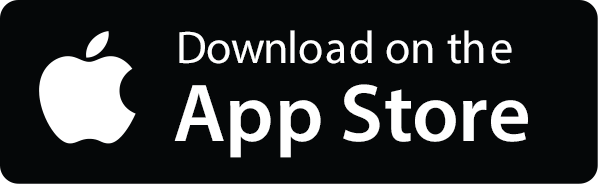
