23
Designing and Manufacturing Customized Orthodontic Appliances
Nearchos C. Panayi1,2
1 School of Dentistry, European University Cyprus, Nicosia, Cyprus
2 Clinic of Orthodontics & Pediatric Dentistry, Center of Dental Medicine, University of Zurich, Zurich, Switzerland
Orthodontics is a specialty that combines the biology of tooth movement with the science of engineering. Orthodontic therapy is based on the interaction between mechanics and biology (Davidovitch and Krishnan, 2009). Thus, the term biomechanics entails aspects of orthodontic treatment, biology, and mechanics.
In recent years digital technology has caused a tremendous evolution of engineering, which has changed many aspects of our daily life. Orthodontics was no exception and we are witnessing transformation of the profession from an analog to an almost completely digital one. Surface scanning (intraoral), volume scanning (cone beam computerized tomography, CBCT), computer‐aided design (CAD) software for three‐dimensional (3D) design of appliances, artificial intelligence (AI) machines, additive manufacturing (3D printing), resins for 3D printing, archwire bending robots, and lately zirconia printers are already in the armamentarium of the orthodontist to perform treatment using customized orthodontic appliances. Moreover, as digital technology progresses, it allows inclusion of such technological advances within the space of the orthodontic office where 3D design and printing can be performed. In that sense, an orthodontic office can incorporate within its space a small laboratory without the need for traditional machines and materials, but instead with the presence of computers, software, 3D printers, and other post‐printing units. Nevertheless, including all units and materials in the orthodontic office entails health hazards that cannot be overlooked (Panayi and Eliades, 2022).
A fully digital orthodontic office instead of an analog one essentially includes software that manages all the digital input taken by CBCT (or a digital cephalometric and panoramic x‐ray machine), an intraoral scan, and a face scan. Intraoral and face examinations are also recorded in the software to create the so‐called virtual patient (Panayi, 2021; Retrouvey and Abdallah, 2021). This software is the core of a digital office that helps the clinician make the diagnosis, set the treatment goals and treatment options, and finally create the treatment plan. The software can be useful for presenting the treatment options and the treatment plan to the patient. Another essential digital tool in a digital orthodontic office is CAD software, which enables the orthodontist to design and print orthodontic appliances. During the last few years new CAD software has appeared on the market that helps to design clear thermoformed or printed aligners, metallic appliances like rapid palate expanders (RPEs), lingual arches, molar distalizers combined with temporary anchorage devices, surgical splints, and so on. Very recently new CAD software has been released for the in‐house design and printing of customized orthodontic brackets (Panayi and Tsolakis, 2021). In the armamentarium of a digital office are 3D printers, while lately retainer wire bending machines and archwire bending robots have started to show up. At this point, metal printing using bed powder fusion printers can only be performed in laboratories due to the machines’ size and the workflow that demands special post‐printing units.
Orthodontic imaging and analysis software
As already mentioned, the core of a digital office is the software that gathers all the digital and nondigital data from surface and volume scanners and intraoral–extraoral examinations. An example of such software is that from Dolphin Imaging (Chatsworth, CA, USA). As the company states, this imaging and management software enables the orthodontist to superimpose a CBCT scan with a face and intraoral scan, perform digital measurements, analyze a cephalogram, and helps to diagnose the patient’s orthodontic problem, set the treatment goals, make treatment simulations, and finally define a treatment plan. In addition, the orthodontist can present to the patient the treatment plan and the possible outcome at the end of treatment. In orthognathic surgery cases, the patient can visualize the predicted bony and soft tissue changes to their face after treatment. At the same time, surgical splints can be designed and sent for 3D printing. During the course of and at the end of treatment, digital records can be imported into the software to evaluate the treatment process.
Recently, new software has appeared on the market that allows for online evaluation and analysis of cephalometric, panoramic x‐rays, and CBCTs. Most of these services use AI software to automatically trace cephalograms, segment CBCTs, and up to a point diagnose dental or orthodontic problems. CephX (Orca, Las Vegas, NV, USA; Borohovitz et al., 2021) is an example of an online service offering cephalogram analysis and CBCT segmentation, while Diagnocat (Tel‐Aviv, Israel) is another company that offers panoramic analysis and diagnosis using AI.
Surface and volume scanning
Surface scanning is a general term for intraoral, desktop, or face scanning. A surface scanner can scan the outer surface of an object in 3D. A volume scanner (CBCT) scans the whole volume of an object and not only its surface, using x‐rays. A CBCT is not always essential in a digital orthodontic office, although its presence helps a lot in diagnosis, treatment planning, and designing certain orthodontic appliances. Due to the high radiation emitted, a tomograph should be taken with caution and only when it is justified by the ALARA (as low as reasonably achievable) rule (Yeung, 2019).
On the other hand, surface scanning is harmless and can be used as many times as desired. Intraoral scanners are extensively used in orthodontics, giving an accurate digital impression of the oral cavity. Intraoral scanners can be also used to evaluate the progress of orthodontic treatment by superimposing dental scans of the patient. Desktop scanners, although more accurate compared to intraoral ones (Su and Sun, 2015), are mainly installed in laboratories for dental model or impression scanning. A 3D scanner projects light onto the scanning object, which then is reflected and recorded as separate images or videos (Kravitz et al., 2014; Martin et al., 2015). The most common file format for a 3D object acquired by a scanner is the STL (Standard Tessellation Language) format.
A surface scanner can also be used to acquire a 3D image of a patient’s face. Some CBCT machines include a face scanner that acquires 3D face images together with or without volume scanning. Stand‐alone facial scanners can also be found in the market and are used mostly for nonorthodontic purposes. Companies that manufacture CBCT, intraoral, and face scanners use a common software interface, enabling superimposition of all the images in a single 3D file allowing a global visualization of the bony, soft tissue, and intraoral structures, thus helping to create a virtual patient. The whole process of transforming a real object into a 3D digital one is called digitization, while the process of transforming a 3D digital object into a real object is called undigitization (Panayi, 2021).
Orthodontic computer‐aided design software
CAD software has been on the market for over 50 years, mainly for aerospace and engineering. The purpose of CAD software is to create, modify, analyze, and optimize a design. At the same time, it helps the designer improve the design quality and create a database for manufacturing. The first CAD software in dentistry appeared on the market in 1985 when Mőrmann and Brandestini introduced the Chairside Economical Restoration of Esthetic Ceramics (CEREC®) system, which uses software (CAD and computer‐aided manufacturing, CAM) and computer‐controlled machinery to automate a manufacturing process (Mörmann et al., 1985). Manufacturing is performed using subtractive technology (milling) or additive technology (3D printing). During the last few years, orthodontic CAD software like Maestro (Age Solutions, Pisa, Italy), Onyxceph (Image Instruments, Chemnitz, Germany), Ortho System (3Shape, Copenhagen, Denmark), and Deltaface (Coruo, Limoges, France) has been introduced mainly for the design of clear aligners (thermoformed or printed), orthodontic appliances like RPEs, lingual arches, bands, and so on. The first CAD software for 3D design and printing of customized brackets, called Deltaface Ubrackets (Panayi and Tsolakis, 2021).
Three‐dimensional manufacturing
The general term 3D manufacturing includes subtractive and additive manufacturing. Subtractive manufacturing (milling) is removing material from an object to create a 3D model according to a 3D object that was designed in CAD software. Additive manufacturing (3D printing) is creating 3D objects by laying down successive layers of material until the object is created (Shahrubudin et al., 2019). Subtractive manufacturing is mainly used in dentistry for creating crowns, bridges, and so on. Due to the excessive loss of material and the geometrical complexity of orthodontic appliances, subtractive manufacturing is not used in orthodontics. Another important reason why milling is not used in orthodontics is that the 20 mm thick discs used are not enough to manufacture orthodontic appliances.
On the other hand, 3D printing is a process that is used exclusively in orthodontic appliance manufacturing. It was invented in 1980 by Hideo Kodama of Nagoya Municipal Industrial Research Institute, Japan, who first presented the process for creating 3D plastic parts by photo‐hardening polymers with ultraviolet (UV) light exposure (Kodama, 1981a, 1981b). In 1983, Charles (Chuck) Hull developed a system referred to as stereolithography (SLA), in which layers were added by curing photopolymers with UV lasers (Hull, 2012). In 1986, Hull co‐founded 3D Systems (Rock Hill, SC, USA) to introduce the technology to the market, while the first ever 3D printer, the SLA‐1®, was introduced in 1987.
In 2009, the American Society for Testing and Materials (ASTM) created the F42 Technical Committee to develop the first additive manufacturing standards. Those standards established 3D printing as an industrial manufacturing technology (Lee et al, 2019). According to the ISO/ASTM 52900 standard, seven general types of 3D printing were defined:
- Vat polymerization, which uses UV light to cure liquid photopolymer in a vat.
- Powder bed fusion, which uses a high‐energy source to fuse material powder particles.
- Material extrusion, which selectively dispenses material through a nozzle to create the 3D object.
- Binder jetting, which selectively binds powder using a liquid bonding agent.
- Material jetting, which deposits and cures droplets of material.
- Direct energy deposition, which uses a high‐energy source to fuse material as it is deposited.
- Sheet lamination, which bonds and forms sheets of material layer by layer.
The types that are mainly used in orthodontics are vat polymerization, powder bed fusion, and material extrusion. Vat polymerization, also known as stereolithography, utilizes photopolymer resins to create dental models, splints, indirect bonding trays, surgical splints, directly printed aligners, and lately customized orthodontic brackets. The 3D printers that belong to the vat polymerization category are SLA printers that use a laser beam to polymerize the resin, DLP (direct light processing) that uses a UV light projector to cure the resin, and more recently MSLA (masked stereolithography) that uses a liquid crystal display (LCD) panel to cure the resin (Gibson et al., 2010; Gupta et al., 2019).
Many resins can be found on the market for all printing purposes: model, splint, indirect bonding trays and casting resins, permanent and temporary crown resins, denture resins, and lately a directly printed aligner resin called TC‐85DAC (Graphy, Seoul, Korea; Can et al., 2021). A forthcoming new material currently under study and construction is bracket resin.
Customized orthodontic appliances
Many of the traditionally made orthodontic appliances could be called customized. For instance, a lingual arch or an RPE is an appliance manufactured for a specific patient and cannot be used for another one. Nevertheless, a few parts of those appliances, like bands or wires, are universal, and they are chosen and bent to fit each different patient. Aligners or positioners are also tailor‐made the traditional way using plaster set‐ups. In contrast to the conventional customization method, digitally designed customized orthodontic appliances are designed and manufactured differently. The most important difference between traditional appliances and digitally designed appliances is the design and manufacturing environment. Traditional appliance manufacturing is performed in an orthodontic laboratory using plaster, bands, wires, soldering material, and so on. In contrast, the modern 3D digital design process is mostly performed on a computer, using CAD software, and a 3D printer is used to manufacture the orthodontic appliances (Figure 23.1). In fact, the ability to design all appliances on a computer together with the ease of appliance manufacturing using 3D printers has moved part of the laboratory work into the space of the orthodontic office, although it is important to be aware that not all appliances can be 3D printed in an orthodontic office.

Figure 23.1 Virtual appliance design using 3 Shape appliance design software.
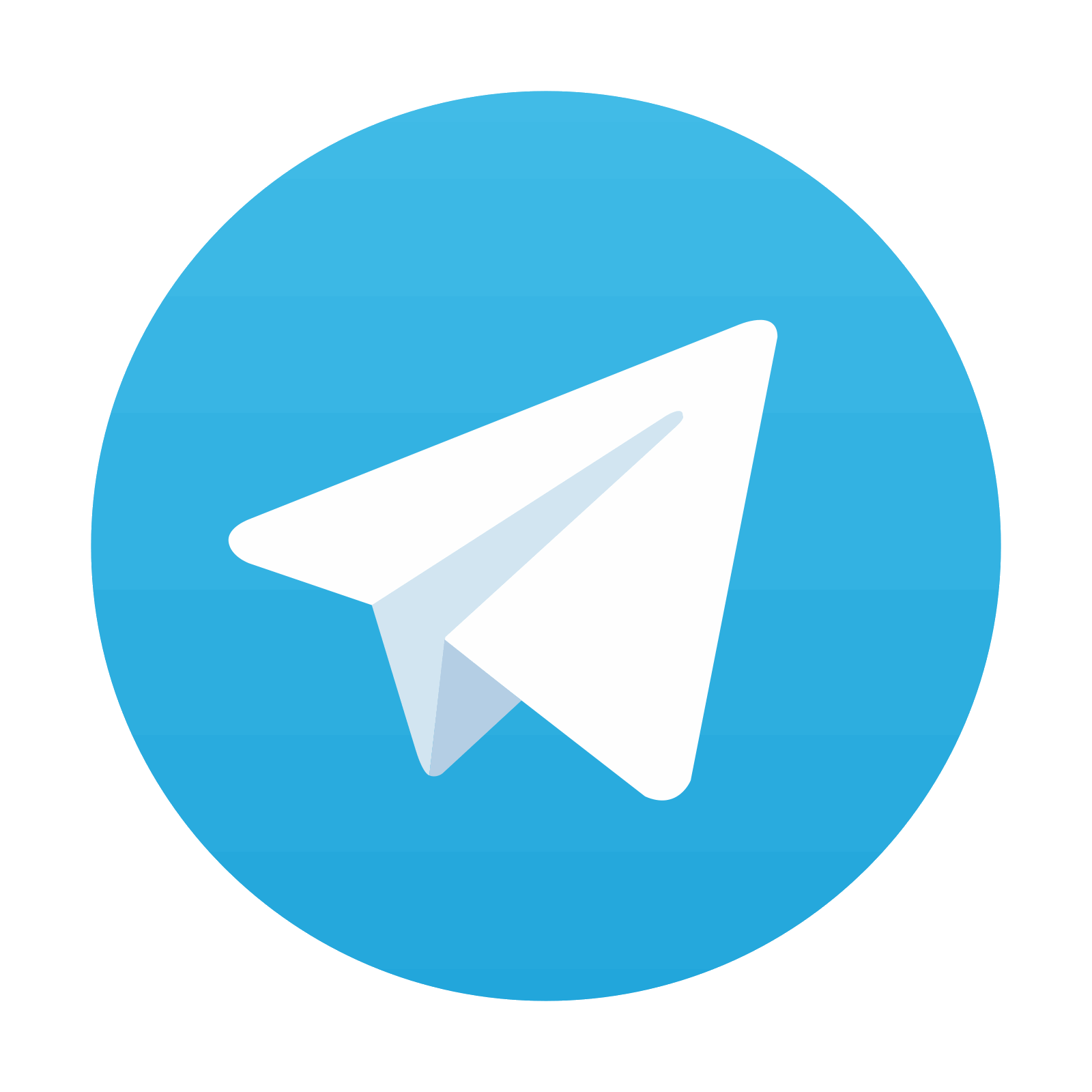
Stay updated, free dental videos. Join our Telegram channel

VIDEdental - Online dental courses
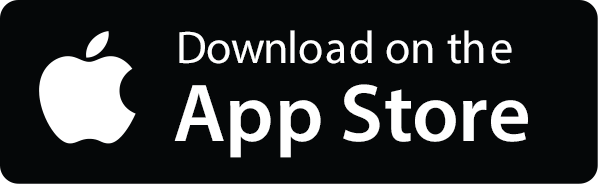
