Abstract
Objectives
The aim of the present study was to investigate the effect of thermal oxidation on the corrosion behavior of Ti–5Ag alloy.
Methods
The microstructure of Ti–5Ag alloy without and with thermal oxidization treatment were characterized, with commercial pure (CP) Ti as control, by means of X-ray diffraction (XRD), X-ray photoelectron spectroscopy (XPS) and scanning electron microscopy (SEM). The electrochemical behavior in artificial saliva solution was compared for CP Ti, Ti–5Ag alloy with and without thermal oxidation.
Results
Compared to CP Ti, Ti–5Ag alloy without thermal oxidization treatment possessed much lower current density, higher open circuit potential, larger impedance value, and its corrosion resistance could be further improved with thermal oxidation.
Significance
The corrosion resistance was enhanced by Ag addition for titanium and could be further improved by thermal oxidation.
1
Introduction
Ti and Ti-based alloys have been widely used in dental devices, such as CP Ti dental implants and TiMo alloy arc wires . Their wide applications are mainly due to their good mechanical properties, outstanding corrosion resistance and excellent biocompatibility. Ti–Ag binary alloys are recently developed as dental materials with several advantages: (1) The yield strength of as-cast Ti–5Ag alloy is about 280 MPa , which is higher than that of CP Ti. (2) It was reported that Ti–Ag alloys possess better grindablity than that of CP Ti. (3) Ti–5Ag alloy fabricated by three-dimensional printing (3DP™) and sintering at 1300 °C shows good passivation behavior in a simulated body fluid . Additionally, the corrosion studies carried out by Shim et al. revealed that, among Ti-Ag alloys, Ti3.0Ag (at.%) alloy had a higher resistance against the attack of fluoride ions in fluoride-containing solution.
The human mouth presents a very aggressive environment for metals used for therapy. For dental alloys, systemic and local toxicity allergy, and carcinogenicity all result from elements in the alloys being released into the mouth . Although titanium alloys exhibit superior corrosion resistance due to the presence of stable and dense titanium oxide film, released alloying element ions into the surrounding tissues and into the serum had been reported . To minimize biologic risks, dental titanium alloys should have the best corrosion resistance and the lowest release of elements. Therefore, it is necessary to improve the corrosion resistance of titanium alloys for dental usage.
The corrosion resistance of Ti and Ti-based alloys in biological environments are ascribed to the rapid formation of passive titanium-dioxide film at the surface. The thicknesses of the passive film formed on titanium alloys in aqueous solutions are usually about several tens of nanometers . Since the corrosion resistance is known to increase with the thickness of the oxide layer , several attempts have been made to form thicker TiO 2 layer on the Ti alloy substrate by different methods, such as anodization , thermal oxidation , and the sol–gel process . Among these methods, the simple and effective method is developing oxide films by thermal oxidation. Velten et al. found that thermally oxidized Ti and Ti–6Al–4 V alloys exhibited much lower passive current densities compared with non-treated Ti alloys. López et al. reported that thermally oxidized Ti–6Al–7Nb alloy exhibited excellent corrosion behavior in Hank’s solution. Moreover, it has been reported that the TiO 2 layer formed by thermal oxidation provided good wear resistance and excellent osseintegration .
The purpose of this study was to further investigate the effect of thermal oxidation on the corrosion behavior of Ti–5Ag alloy. Scanning electron microscopy (SEM), X-ray diffraction (XRD), and X-ray photoelectron spectroscopy (XPS) tests were carried out to analyze the surface characteristics of Ti–5Ag alloy without and with thermal oxidation, with CP Ti as control. Electrochemical measurements were used to evaluate their corrosion resistance.
2
Materials and methods
2.1
Sample preparation
CP Ti and Ti–5Ag (wt.%) alloy was prepared by arc-melting method with titanium wire (99.9%) and silver wire (99.9%) as raw materials. They were melted four times to ensure the homogeneity. The plate samples with the size of 10 mm × 10 mm × 1 mm were cut from the buttons by wire-cut electric discharge machine, mechanically polished step by step, with 400#, 1000# and 2000# silicon carbide papers, and then ultrasonically cleaned in acetone and alcohol for about 10 min. For thermal oxidation, samples were heat treated at 700 °C in air for 2 h, and then quenched into water. Fifteen specimens for each group were prepared for the following tests.
2.2
Surface analyses
Phase identification was carried out by XRD using X’pro from Philips Panalytical. The surface morphology and the chemical composition were analyzed using SEM (Phillips, Quenta 200) and energy dispersive spectroscopy (EDS), respectively. The XPS data were taken on an AXIS-Ultra instrument from Kratos Analytical using monochromatic Al Kα radiation (225 W, 15 mA, 15 kV) and low-energy electron flooding for charge compensation. To compensate for surface charges effects, binding energies were calibrated using C 1s hydrocarbon peak at 284.80 eV.
2.3
Electrochemical behavior tests
For electrochemical impedance spectrum (EIS) measurements, a potentiostat (Solartron 1287A) combined with a frequency response analyzer (Solartron 1260) was used. The potentiostat (Solartron 1287A) was used alone in open circuit potential tests, cyclic voltammetric tests and potentiostatic tests. The cell used was conventional three-electrode configuration with a Pt electrode and a saturated calomel electrode (SCE) as the counter electrode and reference electrode, respectively. The test solution was Fuayama Mayer artificial saliva (NaCl 0.4 g/L; KCl 0.4 g/L; CaCl 2 0.6004 g/L; NaH 2 PO 4 ·2H 2 O 0.78 g/L; KSCN 0.300 g/L; Na 2 S·9H 2 O 0.005 g/L; urea 1.000 g/L). The pH value of the test solutions was adjusted to 4.0 by adding lactic acid, the concentration of lactic acid used was no more than 0.02 wt.%.
In the corrosion potential tests, the specimens were submerged into the electrolyte without any imposed potential for 3 h. Cyclic voltammetric tests were started at a potential in the hydrogen evolution region (−1.0 V vs. SCE) by scanning at 50 mV/s towards more positive potentials up to 8.0 V (vs. SCE), then the scanning was reversed towards the initial potential. Different potentials (0 V and 2 V) were added on CP Ti and Ti–5Ag alloy with and without thermal oxidation treatment in the potentiostatic tests, the samples were aged for 15 min in the test.
Before the electrochemical impedance spectrum measurements (EIS), the specimens were immersed in artificial saliva solution for 3 h. Electrochemical impedance spectrum (EIS) measurements were performed by applying a sinusoidal potential perturbation of 10 mV at the open circuit potentials. The impedance spectra were measured with frequency sweep from 10 kHz to 10 mHz in logarithmic increment.
2
Materials and methods
2.1
Sample preparation
CP Ti and Ti–5Ag (wt.%) alloy was prepared by arc-melting method with titanium wire (99.9%) and silver wire (99.9%) as raw materials. They were melted four times to ensure the homogeneity. The plate samples with the size of 10 mm × 10 mm × 1 mm were cut from the buttons by wire-cut electric discharge machine, mechanically polished step by step, with 400#, 1000# and 2000# silicon carbide papers, and then ultrasonically cleaned in acetone and alcohol for about 10 min. For thermal oxidation, samples were heat treated at 700 °C in air for 2 h, and then quenched into water. Fifteen specimens for each group were prepared for the following tests.
2.2
Surface analyses
Phase identification was carried out by XRD using X’pro from Philips Panalytical. The surface morphology and the chemical composition were analyzed using SEM (Phillips, Quenta 200) and energy dispersive spectroscopy (EDS), respectively. The XPS data were taken on an AXIS-Ultra instrument from Kratos Analytical using monochromatic Al Kα radiation (225 W, 15 mA, 15 kV) and low-energy electron flooding for charge compensation. To compensate for surface charges effects, binding energies were calibrated using C 1s hydrocarbon peak at 284.80 eV.
2.3
Electrochemical behavior tests
For electrochemical impedance spectrum (EIS) measurements, a potentiostat (Solartron 1287A) combined with a frequency response analyzer (Solartron 1260) was used. The potentiostat (Solartron 1287A) was used alone in open circuit potential tests, cyclic voltammetric tests and potentiostatic tests. The cell used was conventional three-electrode configuration with a Pt electrode and a saturated calomel electrode (SCE) as the counter electrode and reference electrode, respectively. The test solution was Fuayama Mayer artificial saliva (NaCl 0.4 g/L; KCl 0.4 g/L; CaCl 2 0.6004 g/L; NaH 2 PO 4 ·2H 2 O 0.78 g/L; KSCN 0.300 g/L; Na 2 S·9H 2 O 0.005 g/L; urea 1.000 g/L). The pH value of the test solutions was adjusted to 4.0 by adding lactic acid, the concentration of lactic acid used was no more than 0.02 wt.%.
In the corrosion potential tests, the specimens were submerged into the electrolyte without any imposed potential for 3 h. Cyclic voltammetric tests were started at a potential in the hydrogen evolution region (−1.0 V vs. SCE) by scanning at 50 mV/s towards more positive potentials up to 8.0 V (vs. SCE), then the scanning was reversed towards the initial potential. Different potentials (0 V and 2 V) were added on CP Ti and Ti–5Ag alloy with and without thermal oxidation treatment in the potentiostatic tests, the samples were aged for 15 min in the test.
Before the electrochemical impedance spectrum measurements (EIS), the specimens were immersed in artificial saliva solution for 3 h. Electrochemical impedance spectrum (EIS) measurements were performed by applying a sinusoidal potential perturbation of 10 mV at the open circuit potentials. The impedance spectra were measured with frequency sweep from 10 kHz to 10 mHz in logarithmic increment.
3
Results
3.1
Surface analyses
The X-ray diffraction patterns of CP Ti, Ti–5Ag alloy with and without thermal oxidation were shown in Fig. 1 (a) . Only α-Ti phase can be identified in CP Ti and Ti–5Ag alloy without thermal oxidation. Corresponding EDS results revealed that the concentration of Ag was about 4.67% in the α-Ti matrix, and the amount of Ag was not enough to form intermetallic compound, according to the Ti–Ag phase diagram. For Ti–5Ag alloy with thermal oxidation, two phases, α-Ti and TiO 2 with rutile structure, were identified from the XRD pattern.
The XPS survey spectrum for Ti–5Ag alloy with thermal oxidation was shown in Fig. 1 (b), with the inset showing enlarged view at about 460 eV. Apart from carbon, elements titanium and oxygen were detected and no peak from element silver was found. It was evident that the surface of thermal oxidized Ti–5Ag alloy mainly consisted of TiO 2 .
The surface and the cross-sectional morphologies of Ti–5Ag alloy with thermal oxidation were further observed using SEM, as shown in Fig. 2 , with the surface morphology of Ti–5Ag alloy without thermal oxidation also be shown as reference. The surface morphology of CP Ti was similar to that of Ti–5Ag alloy so the picture was not shown here. Fig. 2 (a) shows the typical mechanically polished surface morphology with tiny grooves of Ti–5Ag alloy without thermal oxidation. After thermal oxidation, the surface became flat, as shown in Fig. 2 (b). The thickness of the thermal oxidation layer was evaluated to be about 5 μm, as indicated by Fig. 2 (c). EDS results revealed that the Ag concentration of the Ti–5Ag alloy substrate beneath the oxide layer was 5.02 wt.%.
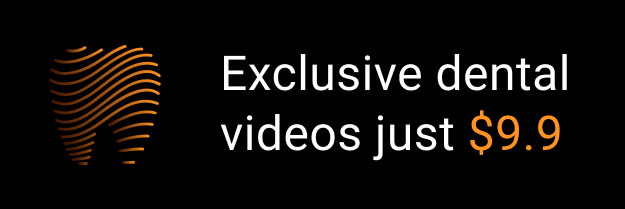