The aim of this pilot study was to illustrate the feasibility of a new digital procedure to fabricate metallic orthodontic appliances. Hyrax appliances for rapid palatal expansion were produced for 3 patients using a CAD/CAM procedure without physical impressions or printed models. The work flow consisted of intraoral scanning, digital design with incorporation of a scanned prefabricated expansion screw, direct 3-dimensional metal printing via laser melting, welding of an expansion screw, insertion, and finally activation in the patients’ mouths. Finite element analyses of the actual hyrax appliances were performed to ensure that the printable material used in combination with the chosen design would withstand the stress generated during activation. The results of these analyses were positive. The clinical results showed that this procedure is an efficient and viable digital way for constructing metallic orthodontic appliances. The flexibility of the digital appliance design, together with the biocompatibility and strength of the chosen material, offers a huge potential for more advanced appliance design.
Highlights
- •
New possibilities of CAD/CAM technologies in orthodontics are illustrated.
- •
A hyrax appliance can be produced with a full digital work flow.
- •
Finite element analysis showed that the design and material delivered the needed strength.
Digital models were introduced commercially into the orthodontic market in 1999 by OrthoCad (Cadent, Carlstadt, NJ). They were initially produced by scanning plaster casts created by pouring the impressions and later by scanning the impressions directly. The advantages of digital casts are mainly the possibility of more precise cast analysis (especially space analysis and Bolton discrepancy), the reduced need for storage, and the ease of handling, sharing, and sending them.
One of the first intraoral scanners for orthodontic purposes was the iTero, introduced in 2007 (Align Technology, Santa Clara, Calif). In addition to their high precision, intraoral scanners provide increased comfort to the patient because of reduced risk of the gag reflex, despite the longer scanning time compared with the 20 to 30 seconds needed for a classic alginate impression. For clinicians, the advantages are mostly related to the practical aspects: less chair-side material (eg, different sizes and jaw specific impression trays), overall less chair-side time, and fewer issues with cross infection. The work flow after scanning is also much quicker, since the data (models) are immediately available for the orthodontist. Moreover, there is no need to physically pack and send the impressions trays to a dental laboratory.
CAD/CAM technology has been used in dentistry, more specifically in prosthodontics, since 1985, with the Cerec system from Sirona (Siemens, Bensheim, Germany), initially for manufacturing single crowns and later for complete bridges. In orthodontics, CAD/CAM technology was first used for individual bracket base manufacturing (eg, Incognito; 3M Unitek, Monrovia, Calif), robot wire bending (eg, SureSmile; OraMetrix, Richardson, Tex), and aligners (eg, Invisalign, Align Technology). Nowadays, digital setups can be produced in dental laboratories, and aligners can be manufactured from printed casts.
Yet, traditional orthodontic appliances such as hyrax, lingual and transpalatal arches, Herbst appliances, and so on are still routinely produced with analog impressions and conventional laboratory techniques. To explore the possibilities offered by CAD/CAM technology to achieve a complete digital work flow to produce such appliances, a simple device was needed: the hyrax appliance was thus chosen. The goal was to avoid not only the analog impression, but also the traditional, plaster model based production of a printed cast.
The aim of this clinical pilot study was to investigate the feasibility of a fully digital production of a hyrax appliance. See Supplemental Materials for a short video presentation about this study.
Material and methods
The first step consisted of taking digital impressions of both jaws and an occlusal bite, using an intraoral scanner (Trios Pod Version; 3Shape, Copenhagen, Denmark). After the scanning process, the digital model was checked with the colored output on the scanner’s screen. The digital impressions were then sent to the technician using the direct upload link.
After instructions of the orthodontist (S.G.), the hyrax was designed using the 3Shape Appliance Designer software by the laboratory technician. Conventional molar bands had to be replaced by printed clasps to obtain a fully digital procedure: the clasps were modeled surrounding the molars and extending on the palatal side to the deciduous canines, but not into the interdental spaces ( Fig 1 ). The surfaces covering the teeth were designed as large as possible to improve the retention of the appliance. On the other hand, to facilitate debonding of the appliance, small hooks were designed on the buccal sides of the molars and on the palatal sides of the deciduous first molars ( Fig 1 ). Some areas with a thinner section at the molar clasp level were designed to facilitate separation in case of difficulties in debonding. The bonding gap was designed to be 0.05 mm. Since an expansion screw cannot yet be produced by printing, a 12-mm self-locking screw (Forestadent, Pforzheim, Germany; 0.9 mm, complete turn) was digitally inserted. The appliance was designed with ideal welding area to accommodate the screw ( Fig 2 ). The design and extension of the appliance were then checked and finally accepted by the orthodontist.


The final digital design was then sent to the laser-melting (printing) machine. The material chosen for creating the appliance was Remanium Star (Dentaurum, Ispringen, Germany), a metal alloy that comes in a powder. This material is widely used by prosthodontic dental laboratories.
After laser melting, the appliance was electro polished, and the expansion screw was welded onto the prepared area. The bonding surfaces were then sandblasted.
Clinical cases
Three patients treated with hyrax appliances, all produced following the above-described method, are presented in this section.
Patient 1 was a girl (age, 8.3 years) in the mixed dentition, with a unilateral crossbite on the left side, a transversal discrepancy of 7 mm at the molar level, and a 2-mm lack of space in the maxillary arch. She had a convex profile and a mandibular shift to the left due to premature contact of the deciduous left canines. She was normodivergent with a skeletal Class I.
The hyrax surface was prepared with Scotchbond universal adhesive (3M Unitek) and subsequently bonded with Transbond XT (3M Unitek). The patient’s parents were instructed to activate the hyrax a quarter turn twice a day (morning and evening) for 20 days, producing 9 mm of expansion, corresponding to 2 mm of overcorrection of the crossbite, since a small relapse was expected.
At the end of the 20-day activation period, the hyrax was left in situ for 6 months for retention before debonding ( Fig 3 ).
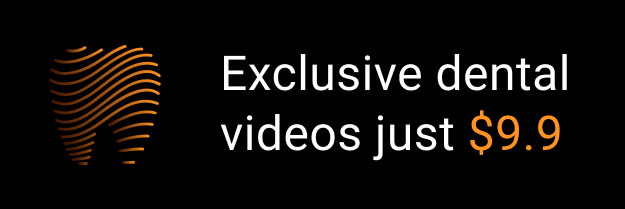