Abstract
The aim of this study was to compare the three-dimensional (3D) imaging accuracy between a digital stereophotogrammetry device and a projection moiré profilometry setup using anatomical models in conjunction with surface matching software. Twenty-two 3D surface models of the middle third of the face derived from computed tomography (CT) scans were used to fabricate photopolymer models by rapid prototyping. These were digitized using digital stereophotogrammetry and projection moiré profilometry. The 3D surface models acquired were compared for shape differences with the original CT models using surface matching software. Global registration between each pair of corresponding models was carried out using an iterative closest point algorithm. The mean surface deviations following registration were used to calculate Bland–Altman limits of agreement between the two methods. The distributions of measured surface differences were used to calculate L-moments. Paired t -tests were carried out for hypothesis testing. Correlation between difference and mean was −0.3, and 95% limits of agreement were −0.084 mm and 0.064 mm. No statistically significant differences in mean measurement error (L1 moments) were observed ( P = 0.1882). The experimental moiré profilometry setup employed produced 3D models of facial anatomy of comparable accuracy to a widely used commercialized digital stereophotogrammetry device.
Three-dimensional (3D) surface imaging of the face is of specific interest to maxillofacial surgery and prosthodontics. Computed tomography (CT), cone beam CT (CBCT), and magnetic resonance imaging (MRI) allow high-resolution 3D imaging of the hard and soft tissues, but are not indicated for repeated surface measurements due to ionizing radiation exposure (CT, CBCT), costs, and the need for a dedicated clinical unit (CT, MRI). Furthermore, CT and MRI require the patient to be placed in supine position, which may result in distortion of the facial tissues compared to the anatomic position. Optical scanning techniques such as laser scanning, digital stereophotogrammetry, and structured light pattern techniques are therefore more appropriate. These can achieve high levels of accuracy, are safe, fast and inexpensive, easy to install in small spaces, and can be used with the patient in the anatomic position. Various applications for 3D surface imaging in maxillofacial rehabilitation have been reported.
Digital stereophotogrammetry offers significant advantages over other 3D imaging techniques, such as a very short data acquisition time (<2 ms), which eliminates the risk of motion artefacts, and capturing of surface data and surface texture, which is useful for landmark identification, patient recognition, and consent procedures. Based on the above, it has been suggested that digital stereophotogrammetry is the technique of choice for routine imaging procedures of the face.
Moiré profilometry is one of many structured light pattern 3D surface imaging techniques, and is based on the generation of interferometric fringes on the object surface, which can be analyzed to acquire surface height information. Moiré profilometry has been applied to maxillofacial imaging since the late 1970s, but even though structured light (fringe projection) techniques have been used widely in industrial applications of freeform measurement due to the high speed of data acquisition and high accuracy of 3D surface imaging, there is lack of evidence in the current literature regarding the application of more recently developed projection moiré techniques for imaging the face.
The aim of this study was to compare the accuracy of surface reproduction of anatomical models of the middle third of the face between two 3D surface imaging techniques: (1) digital stereophotogrammetry, and (2) projection moiré profilometry. For this purpose it was appropriate to use anatomical models in order to relate the findings to a clinical scenario, in conjunction with latest generation surface matching software to carry out surface comparisons, a protocol already validated in previous studies.
Materials and methods
Ethical approval was obtained for use of anonymized CT data. Twenty-two CT datasets (Digital Imaging and Communications in Medicine, DICOM) were selected from an existing database. CT parameters were the same for all datasets; slice thickness was 0.5 mm, voxel size was 0.58 mm × 0.58 mm × 0.5 mm, and scanning resolution was 256 × 256 × 185. Power calculations were based on previous pilot experimentation data, and were carried out using G*Power 3 software. For an effect size of 0.4 and significance of 0.05, 22 specimens in each group would give a power of 0.81. Each dataset was used to reconstruct a 3D model, which was edited using voxel rendering software (Robin’s 3D Software, Robin Richards, UK) to select a volume of interest corresponding to the middle third of the face, based on anatomical features present on all datasets. The 3D volume models were transformed to 3D surface models by selecting soft tissue surface data and converted to 3D solid standard tessellation language (STL) models of 2-mm thickness.
The 22 STL models were used to fabricate photopolymer models by rapid prototyping technology. PolyJet printing technology was used (PolyJet Process; Objet Geometries Ltd, Rehovot, Israel) to construct the models with a liquid photopolymer (VeroWhite Plus; Objet Geometries Ltd), which was polymerized by ultraviolet light emission upon deposition of sequential 16-μm layers. The system-reported typical accuracy of printing was 20–85 μm for features below 50 mm and up to 200 μm for full model size.
Digitization by digital stereophotogrammetry
The 22 photopolymer models were digitized using a digital stereophotogrammetry system (Di3D FTP-001; Dimensional Imaging Ltd) controlled by a PC running specialized software (Di3Dcapture; Dimensional Imaging Ltd). The system comprised four linked digital cameras (EOS 400D; Canon UK Ltd, Surrey, UK) mounted in pairs on either side of a main unit, which was in turn mounted on a tripod. Each camera had a resolution of 10 megapixels and was equipped with a 50-mm lens (EF 50 mm f/1.8 II; Canon UK Ltd). The two superiorly positioned cameras were connected to white-light flash units (Speedlite 430 EX II; Canon UK Ltd). The cameras were set for ISO sensitivity 100, shutter speed 1/20 s, and focal ratio (aperture) 20. Calibration of the system was carried out using a calibration panel provided by the manufacturer. The average system error has been reported at 0.21 mm, and the calibration error was 0.476 pixels as reported by the system.
A wooden frame was used to position the models. Each model was suspended from the frame and tied to brass dowel pins attached on the non-tissue surface of each model. Black water-based face paint was dabbed on each model to provide surface texture, as recommended by the manufacturer for high-detail recordings. Positioning of each model was at an arbitrary angle simulating the natural head position. All recordings were carried out following the manufacturer’s recommended protocol. Twenty-two 3D surface STL models (specimens) were obtained and allocated to the first experimental group (Di3D group).
Digitization by projection moiré profilometry
The 22 photopolymer models were digitized using an experimental projection moiré profilometer controlled by a PC running purpose-written software in Matlab environment (Matlab; Mathworks Inc., Natick, MA, USA), as described by Dirckx et al. The system mainly comprised an LCD projector (VT595; NEC Display Solutions Europe GmbH), a CCD camera (Foculus FO442B; NET GmbH), and lenses (Schneider Kreuznach G-Claron f/9; Jos. Schneider Optische Werke GmbH) ( Figs. 1 and 2 ). The projector created both the projection and demodulation grids, which were controlled in RGB (red, green, blue) colour space by a computer driver using a graphics board (GeForce 8800GT; NVIDIA Corp., Santa Clara, CA, USA) and custom-written software. The projector incorporated three liquid crystal modulators (LCMs), for red, blue, and green colour, one of which (blue) was transferred externally (LCM2). A lens (L1) projected the light going through the first LCM (LCM1, green) onto the object surface (O). The projected grid pattern was modulated by the object geometry, and then projected through a second grid on the second LCM (LCM2) by an identical lens (L2), creating a moiré interferogram ( Fig. 3 ). A third lens (L3) was used to record the interference pattern using the CCD camera, which had a resolution of 1392 × 1040 pixels (SXGA) at 15 frames per second. Three phase-shifted interferograms were required for the software to reconstruct a 3D surface model. Calibration of this device was performed by imaging objects of known dimensions. For the photopolymer models used, measurement error was calculated at 0.3 mm during calibration.
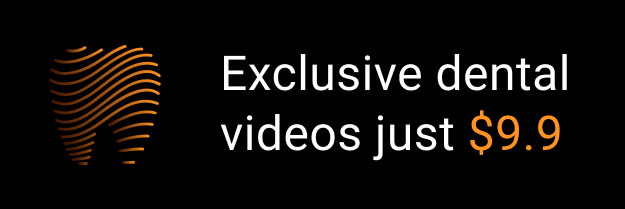