Abstract
Objectives
To investigate the chipping resistance of veneered zirconia specimens and compare it to the chipping resistance of porcelain fused to metal (PFM) specimens.
Methods
Veneered zirconia and PFM bar specimens were prepared in clinically relevant thicknesses. The specimen edges were chipped with different magnitude forces, producing chips of various sizes. The range of sizes included small chips that did not penetrate all the way through the veneers to the substrates, and also chips that were very large and reached the zirconia or metal substrates. The relationship between force magnitude and chip size (edge distance) was graphed. The resulting curves were compared for the veneered zirconia and PFM specimens. Knoop hardness vs. force graphs for the veneers and substrates were also obtained.
Results
The zirconia and PFM veneer chipping data followed a power law (coefficient of determination, R 2 > 0.93) as expected from the literature. The curves overlapped within the combined data scatter, indicating similar resistance to chipping. The chips made in both types of specimens detached and did not penetrate into the substrate when they reached the veneer/substrate intersections. The hardness–load curves for the veneers and substrates all exhibited an indentation size effect (ISE) at low loads. The Knoop hardness values with uncertainties of ±one standard deviation at 4 N loads for the metal, zirconia, and the metal and zirconia veneers are: (2.02 ± 0.08, 12.01 ± 0.39, 4.24 ± 0.16 and 4.36 ± 0.02 GPa), respectively, with no statistically significant difference between the veneers (Tukey pairwise comparison at 0.95 family confidence).
Significance
This work indicates that a similar resistance to chipping might be expected for veneered zirconia and PFM restorations, in spite of the large difference in substrate hardness. Differences in susceptibility to chip spalling were not detected, but the chips in both specimen types detached off the sides in a similar manner instead of extending into the substrates.
1
Introduction
Explorations into the use of yttria-stabilized zirconium oxide (zirconia, YSZ) as a biomaterial began in the 1960s . Soon thereafter, the promising in vitro properties, as well as the history of orthopedic use, attracted the attention of dental materials researchers. Over the last decade, zirconia has been used as a substructure material for the fabrication of fixed prosthodontic restorations. Marketed in the dental arena under numerous brand names, zirconia is regarded as offering superior strength, toughness and reliability over other ceramic materials due to the transformation toughening mechanisms of its microstructure .
Clinical studies are now available that support zirconia’s performance potential, with indications of expanded functionality compared with other ceramics, such as use in long span bridges . The primary issues noted in such studies were not related to framework integrity, but rather chipping, wear, and fracture of the veneering ceramics . A recent study suggests that such chipping could also be an issue around endodontic access openings for all-ceramic crowns .
These observations prompted thinking about differences between porcelain fused to metal (PFM) veneering ceramics, which have been used for over 40 years , and the more recently developed veneering ceramics intended for zirconia. The veneering ceramics exhibit some compositional and microstructural differences, but are manufactured to identical international standards in terms of mechanical properties . Based on clinical observations, as well as the in vitro materials data, the question arises whether zirconia veneers are more susceptible to chipping than PFM veneers.
One way to investigate this question is to utilize an edge chipping test. This test involves the purposeful formation of chips in a material utilizing an indenter or stylus, with an attached load cell to measure the chip-forming forces ( Fig. 1 ). The edge chip test is being utilized in diverse applications such as evaluation of cutting tool materials , ceramics , ceramic valves , machinability of brittle materials , heat treatment effects in archeological flint-knapping , and dental materials . Although many groups have adapted conventional hardness machines or universal strength testing machines for edge chipping experiments, at least one commercial edge testing machine has been developed. 1
1 Engineering Systems Model CK 10 edge chipping machine (Nottingham, UK).
, 2
2 Commercial products and equipment are identified only to specify adequately experimental procedures and does not imply endorsement by the authors, institutions or organizations supporting this work, nor does it imply that they are necessarily the best for the purpose.
A conference on fractography of glasses and ceramics featured a technical session on edge chipping fractography . Gogotsi and Mudrik recently commented on the diversity of indenter shapes and analyses that have been used for edge chipping experiments. “Edge chipping” resistance, which is alternatively referred to as “edge strength,” “edge fracture,” or “edge flaking resistance,” has been strongly correlated with fracture toughness, K Ic or the critical strain energy release rate, G Ic .

In this study, the edge chipping test is used to compare the resistance of PFM and zirconia veneered specimens to chipping. The null hypothesis is that the edge chip resistances of the two material systems are different. Hardness measurements at different loads were also obtained for the veneers and substrates, given the dependence of measured hardness on load for ceramics (indentation size effect or ISE) which has been related to brittleness and susceptibility to cracking .
2
Materials and methods
2.1
Materials
Layered specimens for the edge chipping tests were constructed by laminating metal and zirconia substrates with appropriate veneers. The materials were all donated by Dentsply Ceramco (York, PA), with the following product trade names material descriptions, and compositions from the company literature. The PFM substrates were cast using Ultracrown SF alloy of 0.65 mass fraction Au and 0.26 mass fraction Pd, with small amounts of In, Ga, Ru and Sn. This alloy is listed as being compatible with most conventional and low fusing porcelains. In the current study, it was veneered with Ceramco 3, a feldspathic veneering porcelain containing about 0.30 volume fraction leucite. The zirconia substrates were milled out of Cercon, composed of zirconia stabilized with 3 mole% yttria, with small amounts of hafnia, alumina and silica present. They were veneered with Ceramco PFZ, a feldspathic veneering porcelain with no leucite, engineered to be compatible with zirconia frameworks.
2.2
Methods: specimen preparation
A bar shape specimen was selected for ease of testing in the edge chipping machine, but the specimen preparation and layering thicknesses were chosen with regard to clinical relevancy. Ten substrates for each material system were provided in thin (≈0.5 mm) 4 mm × 40 mm rectangular slabs and coated with a thin liner and then veneered in two layers following procedures recommended in the manufacturer’s literature. A vacuum dental furnace (model: Centurion VPC, Ney Dental, Inc., Burlington, NJ) was used to fire the veneers. The Ceramco 3 veneer for the alloy had a heat up rate of 55 °C/min to a peak firing temperature of 960 °C and 0 min hold. The Ceramco PFZ veneer for the zirconia had a heat up rate of 60 °C/min to a peak temperature of 900 °C and a short 15 s hold on the first firing and 890 °C and 0 min hold on the second firing. After veneering, the specimens were rough-polished on the bottom substrate surface (350 grit) to eliminate any bowing or small surface lumps so that the specimens lay flat in the edge chipping machine. The top veneered surfaces were more carefully polished with successively smaller grits down to 1200 grit, in order to provide a smooth, consistent surface for applying the edge chipping force and measuring the chip size. Three specimens of veneered zirconia and three PFM bar specimens were prepared in this manner to obtain edges suitable for chipping. These were sufficient to provide enough total edge length for the edge chipping experiments described below.
The layered specimens were then placed in a holder ( Fig. 2 ) that enabled the side edges to be polished to 1200 grit at right angles to the specimen’s top and bottom surfaces. This step was not essential since small differences in specimen side surface preparation and substrate thicknesses are not expected to affect the amount of force needed to cause chipping in these experiments, as the chip cracks initiate at the specimen top surface veneer beneath the indenter and emerge at the specimen sides without penetrating the substrate. However, the extra side surface polishing step was done to make the chips are easier to see and measure.
2.3
Methods: dimension measurement
The final specimen and specimen veneer thicknesses after polishing were measured in a stereoptical microscope (model MZ-16, Leica, Heerbrugge, Switzerland) with a traveling stage capable of providing measurements to the nearest μm. Eight thickness measurements of the veneering ceramic and eight total thickness measurements were made for each of the six specimens, for a total of 96 measurements. The thickness (with uncertainties of ±one standard deviation) of the specimen veneers on the metal and zirconia substrates were measured to be 0.777 ± 0.060 and 0.769 ± 0.052 mm, respectively, with no significant difference for Tukey pairwise comparison at 0.90 family confidence. The total specimen thickness uncertainties of ±one standard deviation for the PFM and veneered zirconia specimens were measured to be 1.216 ± 0.041 and 1.278 ± 0.040 mm, respectively. This difference is small, but statistically significant for Tukey pairwise comparison at 0.90 family confidence. The reason the zirconia specimens were slightly thicker was that they were slightly less bowed after removal from the furnace and were not polished as much on the bottom substrate surface. The final veneer and total specimen thicknesses are within the range used for restoration crown preparation in normal clinical practice.
2.4
Methods: edge chipping measurements
The prepared specimens were placed in an Engineering Systems Model CK 10 edge chipping machine (Nottingham, UK), with a 1000 N load cell and a conical 120° diamond scribe indenter with a very sharp tip (with a radius less than 10 μm). This indenter is very inexpensive (less than $15 US) and easy to replace as opposed to the Rockwell, Vickers, or Knoop indenters used by other investigators. The load readout resolution was 0.1 N and the load cell was certified to be accurate to better than 0.1 N. Load was gradually applied until the chip fractured off the specimen and the peak load was recorded. The contact locations were spaced well apart from each other, typically two or more times the chip widths as shown in Fig. 2 , to avoid any interference between chips. Forces up to 120 N were used to create 56 chips of various sizes in the veneered specimens. The indenter was frequently viewed under an optical microscope to confirm the integrity of the diamond tip between test series. Ten to fifteen chips were made in each specimen. The edge distance as shown in Fig. 1 was measured in mm from the center of the indentation location to the edge using the previously described stereoscopic microscope system.
2.5
Methods: hardness (ISE) measurements
Two additional specimens, one of veneered zirconia and one PFM, were polished along one side using the holder in Fig. 2 and tested for Knoop hardness with a Wilson Tukon hardness machine (Binghamton, NY) according to ASTM C1326 . In order to determine the hardness dependence on load (indentation size effect, ISE), loads ranging from 0.098 to 3.92 N were used, with 10 indentations at each load. The ISE graphs for both the PFM and zirconia veneers and the metal and zirconia substrates were obtained. Indentations were made both near and remote from the interface to get a sense of whether residual stresses may have been present at the interface, but no difference in hardness with location was detected. The indenter was in contact with the test piece at peak load for 15 s in accordance with ASTM C 1326.
2
Materials and methods
2.1
Materials
Layered specimens for the edge chipping tests were constructed by laminating metal and zirconia substrates with appropriate veneers. The materials were all donated by Dentsply Ceramco (York, PA), with the following product trade names material descriptions, and compositions from the company literature. The PFM substrates were cast using Ultracrown SF alloy of 0.65 mass fraction Au and 0.26 mass fraction Pd, with small amounts of In, Ga, Ru and Sn. This alloy is listed as being compatible with most conventional and low fusing porcelains. In the current study, it was veneered with Ceramco 3, a feldspathic veneering porcelain containing about 0.30 volume fraction leucite. The zirconia substrates were milled out of Cercon, composed of zirconia stabilized with 3 mole% yttria, with small amounts of hafnia, alumina and silica present. They were veneered with Ceramco PFZ, a feldspathic veneering porcelain with no leucite, engineered to be compatible with zirconia frameworks.
2.2
Methods: specimen preparation
A bar shape specimen was selected for ease of testing in the edge chipping machine, but the specimen preparation and layering thicknesses were chosen with regard to clinical relevancy. Ten substrates for each material system were provided in thin (≈0.5 mm) 4 mm × 40 mm rectangular slabs and coated with a thin liner and then veneered in two layers following procedures recommended in the manufacturer’s literature. A vacuum dental furnace (model: Centurion VPC, Ney Dental, Inc., Burlington, NJ) was used to fire the veneers. The Ceramco 3 veneer for the alloy had a heat up rate of 55 °C/min to a peak firing temperature of 960 °C and 0 min hold. The Ceramco PFZ veneer for the zirconia had a heat up rate of 60 °C/min to a peak temperature of 900 °C and a short 15 s hold on the first firing and 890 °C and 0 min hold on the second firing. After veneering, the specimens were rough-polished on the bottom substrate surface (350 grit) to eliminate any bowing or small surface lumps so that the specimens lay flat in the edge chipping machine. The top veneered surfaces were more carefully polished with successively smaller grits down to 1200 grit, in order to provide a smooth, consistent surface for applying the edge chipping force and measuring the chip size. Three specimens of veneered zirconia and three PFM bar specimens were prepared in this manner to obtain edges suitable for chipping. These were sufficient to provide enough total edge length for the edge chipping experiments described below.
The layered specimens were then placed in a holder ( Fig. 2 ) that enabled the side edges to be polished to 1200 grit at right angles to the specimen’s top and bottom surfaces. This step was not essential since small differences in specimen side surface preparation and substrate thicknesses are not expected to affect the amount of force needed to cause chipping in these experiments, as the chip cracks initiate at the specimen top surface veneer beneath the indenter and emerge at the specimen sides without penetrating the substrate. However, the extra side surface polishing step was done to make the chips are easier to see and measure.
2.3
Methods: dimension measurement
The final specimen and specimen veneer thicknesses after polishing were measured in a stereoptical microscope (model MZ-16, Leica, Heerbrugge, Switzerland) with a traveling stage capable of providing measurements to the nearest μm. Eight thickness measurements of the veneering ceramic and eight total thickness measurements were made for each of the six specimens, for a total of 96 measurements. The thickness (with uncertainties of ±one standard deviation) of the specimen veneers on the metal and zirconia substrates were measured to be 0.777 ± 0.060 and 0.769 ± 0.052 mm, respectively, with no significant difference for Tukey pairwise comparison at 0.90 family confidence. The total specimen thickness uncertainties of ±one standard deviation for the PFM and veneered zirconia specimens were measured to be 1.216 ± 0.041 and 1.278 ± 0.040 mm, respectively. This difference is small, but statistically significant for Tukey pairwise comparison at 0.90 family confidence. The reason the zirconia specimens were slightly thicker was that they were slightly less bowed after removal from the furnace and were not polished as much on the bottom substrate surface. The final veneer and total specimen thicknesses are within the range used for restoration crown preparation in normal clinical practice.
2.4
Methods: edge chipping measurements
The prepared specimens were placed in an Engineering Systems Model CK 10 edge chipping machine (Nottingham, UK), with a 1000 N load cell and a conical 120° diamond scribe indenter with a very sharp tip (with a radius less than 10 μm). This indenter is very inexpensive (less than $15 US) and easy to replace as opposed to the Rockwell, Vickers, or Knoop indenters used by other investigators. The load readout resolution was 0.1 N and the load cell was certified to be accurate to better than 0.1 N. Load was gradually applied until the chip fractured off the specimen and the peak load was recorded. The contact locations were spaced well apart from each other, typically two or more times the chip widths as shown in Fig. 2 , to avoid any interference between chips. Forces up to 120 N were used to create 56 chips of various sizes in the veneered specimens. The indenter was frequently viewed under an optical microscope to confirm the integrity of the diamond tip between test series. Ten to fifteen chips were made in each specimen. The edge distance as shown in Fig. 1 was measured in mm from the center of the indentation location to the edge using the previously described stereoscopic microscope system.
2.5
Methods: hardness (ISE) measurements
Two additional specimens, one of veneered zirconia and one PFM, were polished along one side using the holder in Fig. 2 and tested for Knoop hardness with a Wilson Tukon hardness machine (Binghamton, NY) according to ASTM C1326 . In order to determine the hardness dependence on load (indentation size effect, ISE), loads ranging from 0.098 to 3.92 N were used, with 10 indentations at each load. The ISE graphs for both the PFM and zirconia veneers and the metal and zirconia substrates were obtained. Indentations were made both near and remote from the interface to get a sense of whether residual stresses may have been present at the interface, but no difference in hardness with location was detected. The indenter was in contact with the test piece at peak load for 15 s in accordance with ASTM C 1326.
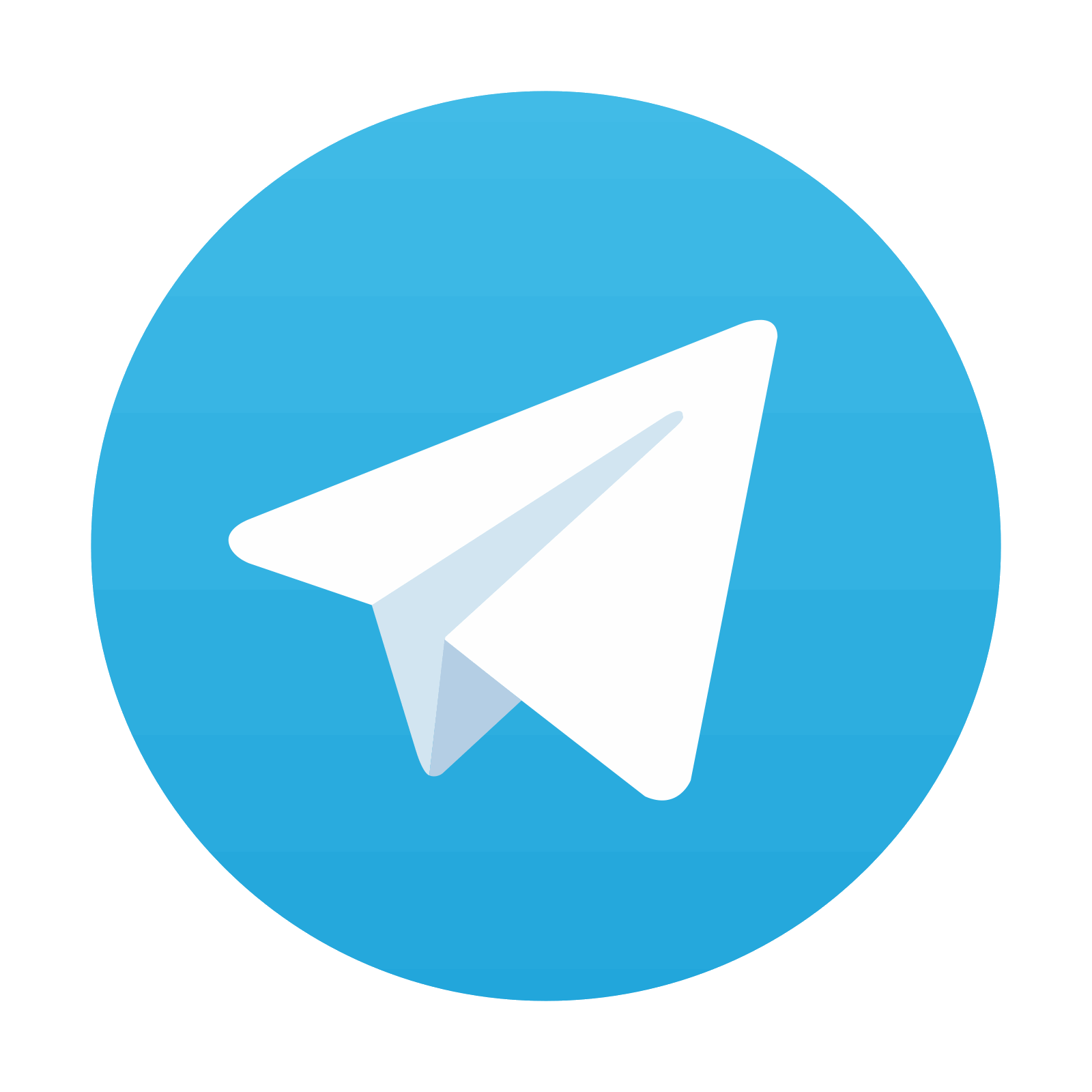
Stay updated, free dental videos. Join our Telegram channel

VIDEdental - Online dental courses
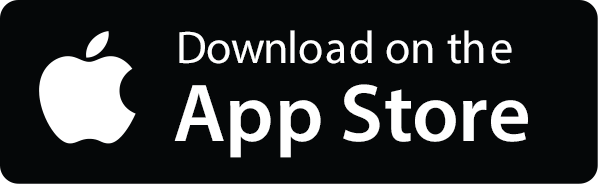
