Abstract
Objective
The applicability of the edge chipping method to denture tooth materials was assessed. These are softer materials than those usually tested by edge chipping. The edge chipping fracture resistances of polymethylmethacrylate (PMMA) based and two filled resin composite denture tooth materials were compared.
Methods
An edge chipping machine was used to chip rectangular blocks and flattened anterior denture teeth. Force versus edge distance data were collected over a broad range of forces and distances. Between 20 and 65 chips were made per condition depending upon the material, the scatter, and the indenter type. Different indenter types were used including Rockwell C, sharp conical 120 o , Knoop, and Vickers. The edge toughness, Te, was evaluated for different indenter types.
Results
The edge chipping data collected on the blocks matched the data collected from flattened teeth. High scatter, particularly at large distances and loads, meant that many tests (up to 64) were necessary to compare the denture tooth materials and to ascertain the appropriate data trends. A linear force–distance trend analysis was adequate for comparing these materials. A power law trend might be more appropriate, but the large scatter obscured the definitive determination of the precise trend. Different indenters produce different linear trends, with the ranking of: sharp conical 120 o , Rockwell C, and Knoop, from lowest to highest edge toughness. Vickers indenter data were extremely scattered and a sensible trend could not be obtained. Edge toughness was inversely correlated to hardness.
Significance
Edge chipping data collected either from simple laboratory scale test blocks or from actual denture teeth may be used to evaluate denture materials. The edge chipping method’s applicability has been extended to another class of restorative materials.
1
Introduction
The edge chipping test is used to evaluate the resistance of brittle materials to flaking near an edge as shown in Fig. 1 . This method, originally developed in the late 1980s to study hard metal cutting tools at the National Physical Laboratory in London , has been applied to dental restoration materials human dentin and enamel . A short review paper on edge chipping as applied to dental materials was recently prepared . A detailed evaluation of six computer aided design and machining) CAD/CAM restorative materials including porcelains glass ceramics, filled resin composites, and zirconia was recently reported .

Chips are formed by advancing an indenter or stylus into a material near an edge. The force required for chip formation is recorded as a function of the distance from the edge. The greater the load application point distance is from the edge, the greater is the force that is needed to create the chip. The shape of the chip is usually independent of the material tested.
In this work, the edge chipping test was applied to denture tooth materials. They are not as hard and are more compliant (lower elastic modulus) than some of the materials cited above and exhibit some ductility. Nevertheless, clinical chipping of denture teeth had been observed, and a simple quick test to evaluate candidate materials for dentures would be helpful. The goal of this work was to: ascertain whether the laboratory chipping tests could compare the edge chipping resistance of candidate denture materials and expand the applicability of the test method to softer materials.
Three hypotheses are set forth in this paper: edge chip indenter type does not affect test results, force versus distance data follow a linear trend; and the edge chip resistance of several denture tooth materials can be differentiated.
2
Materials and methods
Three resin based denture tooth materials were evaluated as shown in Table 1 . 1
1 Commercial products and equipment are identified only to specify adequately experimental procedures and does not imply endorsement by the authors, institutions or organizations supporting this work, nor does it imply that they are necessarily the best for the purpose.
The first is a highly cross-linked polymethylmethacrylate (PMMA) with organic filler . It was available in the form of monolithic wear test type rectangular blocks and also anterior teeth that were made of three layers. The upper two layers were incisal and dentin designated versions of the highly cross-linked PMMA, which had the similar composition and properties, but different pigmentation. A supporting cervical (neck) region was a less highly cross-linked PMMA.
Material | Primary constituents a | Elastic Modulus (GPa) * | HV0.5/30 (MPa) ** | Fracture toughness, K Ic (MN/m 1.5 ) *** |
---|---|---|---|---|
PMMA Blueline SR Vivodent Plus DCL |
Dimethacrylate 8% PMMA 71–73% cross-linked prepolymer 20% |
3.4 | 200 | 1.2 (0.02) |
Composite I SR Phonares NHC |
Aliphatic-aromatic UDMA 17–25% PMMA 19–24% inorganic filler 18–25%, silanized silica inorganic filled prepolymer (PMMA/UDMA) 35–40% |
4.5 | >260 | – |
Composite II SR Phonares II Incisal and Dentin |
MMA 17–20% Dimethacrlyates (UDMA) 17.5–22% PMMA 6–9% inorganic filler 9–12%, silanized silica inorganic filled prepolymer (PMMA/UDMA) 39–45% |
3.9 incisal 4.4 |
235 Incisal 258 |
1.40 (0.15) incisal 1.55 (0.10) |
** Vickers hardness, 0.5 kgf (4.9 N) force, 30 s dwell.
*** Single edge V-notched beam, 3 point bending. Computed from maximum force.
a PMMA, polymethylmethacrylate; UDMA, urethandimethacrylate; NHC, nanohybrid composite.
The other two materials are hybrid silica-filled urethandimethacrylate (UDMA) composites . They have small differences in composition and filler content. Composite I (SR Phonares NHC) was available in the form of wear blocks and four-layered anterior denture teeth. It is described by the manufacturer as a “nano hybrid composite” (NHC) . The two uppermost (incisal and dentin) layers, into which the chips were made, were supported by cervical (neck) material that was a low cross-linked PMMA. Composite I had been developed to offer reduced shrinkage and improved wear resistance and durability in comparison to acrylic teeth , but there were some reports of in vivo chipping fractures. Composite II (SR Phonares II) was a newer refined composite, with slight changes in the composition as compared to Composite I, and was designed to mitigate or eliminate the reported in vivo chipping fractures. The dentin and incisal versions of Composites I and II differ only in the amount of pigments added.
Test pieces for all three materials were available in the form of six wear test type rectangular blocks, nominally 10 mm × 15 mm × 4.5 mm thick. The six surfaces were polished to make well-defined, reproducible edges. They were progressively hand ground wet with a rotary polishing wheel using 1200, 2400, and 4000 grit wet SiC papers.
Incisal denture teeth of all three materials were also prepared by polishing as shown in Fig. 2 a . The gingival side was ground flat to support the tooth evenly on the edge chipping machine base as shown in Fig. 2 b. The incisal surface was ground parallel to the base. Finally the palatal surface was ground flat to eliminate a small amount of material and to make the 90° edge. The incisal and palatal surfaces were polished to provide a single well defined 90° edge.

A commercial edge chipping machine (Engineering Systems Model CK 10, Nottingham, UK) was used to make the chips. All test pieces were waxed to a mounting plate. At the beginning of a test sequence, the indenter was positioned over a flat portion of the specimen well away from the edge, and a small indentation was made. The instrument crosshair was then precisely lined up with the center of the indentation. The X–Y stage then was moved to make indentations and chips at prescribed distances from the edge, ranging from 0.05 mm to 0.60 mm. Force was gradually applied in displacement control until the chip fractured off the specimen. The forces increased linearly during the loading sequence with the exception that a slight hesitation of a few seconds occurred at about 35–45 N as the mass of the machine head (about 3 kg) shifted on the drive screws. It was thought that the loading rate may be important, so the maximum machine speed of 3 mm/min was used for most experiments although some were done at 1 mm/min. The chipping sequence took 5–30 s depending upon the material and edge distance. Temperatures were 20 °C to 25 °C. The peak load was recorded. Twenty to thirty-five chips were typically made per material. A sharp conical 120° single crystal diamond indenter was used as described previously . For comparison, some experiments were also done with Rockwell C, and Knoop indenters. Only a few experiments were done with a Vickers indenter, since results were highly variable and chips often did not form. The long axis of the Knoop indenter, or one edge axis of the Vickers indenter, was aligned parallel to the test piece edge.
One problem detected in this work was “overchipping”. Ideally, once a chip pops off, the indenter should instantly extract. In practice, the indenter continued to contact the intact side of the test piece for a split second prior to indenter extraction and made additional damage and a larger indentation. We verified this by interrupting some chips just prior to their popping off and comparing the indentation size and chip sizes to those where the chip did pop off. This overchipping behavior severely affected measurements of the edge distances by post-test examination. The distances sometimes were overestimated. Even the commercial edge chipping machine that we used was susceptible to this problem. It had a sensitive break detection circuitry that automatically extracted the indenter once a sudden load drop off was detected. The sensitivity could be adjusted, but in many cases some overchipping still occurred. The matter was worse in compliant materials. When a full chip formed, it might not pop completely off and would only partially detach. 2
2 The problem was particularly difficult with some softer resin materials (not included in the present work). In such cases, we resorted to visual monitoring of the chip formation on the side of the specimen with the aid of a hand magnifier. The crosshead return button was manually activated as quickly as possible.
In this study, edge distances were precisely set prior to each test in order to avoid interpretation problems of the contact site for measurement of the edge distance.
A further problem with the softer, more compliant materials was that sometimes the chips did not actually detach from the test piece side. In such cases, the side of the test piece was visually observed with a hand magnifier during the test, and once the customary large chip popped in suddenly, the test was stopped manually and the peak force recorded. In a number of instances, depending upon the material and the type of indenter and the loading rate, a chip did not form and the indenter started pushing into the material creating substantial plastic deformation. These tests were stopped and the trial deemed invalid.
Edge chipping force versus distance data trends are either linear or fit a power law as discussed in detail in Ref. . If the data fit a linear trend,
F = T e d
where F is the chipping force and d is the distance from the edge. The usual convention is to report the slope of the fitted line as the edge toughness, T e , (N/mm). 3
3 Edge toughness is sometimes denoted as M.
Edge chip resistance may be correlated to fracture toughness for many materials as discussed elsewhere. Although there are cases (e.g., Refs. ) where a power law might fit the data better, nearly all the data in this study were well fit by the linear trend.
Watts et al. defined an edge strength, S E (0.5) with units of N, which denotes the force necessary to create a chip at the distance of 0.5 mm. This is felt to be a clinically relevant distance. 4
4 Watts et al. did not use this specific symbol S E (0.5) in their publications, but it was agreed upon in private communication in April 2012.
If the data follow a linear trend, Eq. (1) , it is readily apparent that the numerical value of the edge strength, S E (0.5) is exactly one half the value of the edge toughness, T e. They have different units, however: N for the former and N/mm for the latter.
Edge chips were photographed with a stereoptical microscope 5
5 Model M10, Leica/Wild Heerbrug, Switzerland.
at magnifications up to 63 power to the eyes. Chips sometimes were stained with a green felt tip marker pen in order to cut down internal reflections and to highlight topographical and fractographic features.
Hardness tests were conducted with the sharp conical 120°, Rockwell C, and Knoop indenters mounted on the edge chipping machine, which is designed to do hardness tests as well as the edge chipping. For the sharp conical and Rockwell C indenters, the peak load was set to 100 N with a 15 s dwell time. A peak load of 19.6 N and dwell time of 15 s was used for the Knoop indentations. It was easy to measure the diameter of the large round indentations using a stereoptical microscope with a X–Y traversing stage with a 1 μm resolution, provided that care was taken to illuminate the indentations the same way each time. For all three indenters, hardness was computed as the load divided by the projected surface area. This is the conventional procedure for Knoop indentations, but is new for the cases of the Rockwell C and sharp conical indenters. Five to fifteen indentations were made in each case.
2
Materials and methods
Three resin based denture tooth materials were evaluated as shown in Table 1 . 1
1 Commercial products and equipment are identified only to specify adequately experimental procedures and does not imply endorsement by the authors, institutions or organizations supporting this work, nor does it imply that they are necessarily the best for the purpose.
The first is a highly cross-linked polymethylmethacrylate (PMMA) with organic filler . It was available in the form of monolithic wear test type rectangular blocks and also anterior teeth that were made of three layers. The upper two layers were incisal and dentin designated versions of the highly cross-linked PMMA, which had the similar composition and properties, but different pigmentation. A supporting cervical (neck) region was a less highly cross-linked PMMA.
Material | Primary constituents a | Elastic Modulus (GPa) * | HV0.5/30 (MPa) ** | Fracture toughness, K Ic (MN/m 1.5 ) *** |
---|---|---|---|---|
PMMA Blueline SR Vivodent Plus DCL |
Dimethacrylate 8% PMMA 71–73% cross-linked prepolymer 20% |
3.4 | 200 | 1.2 (0.02) |
Composite I SR Phonares NHC |
Aliphatic-aromatic UDMA 17–25% PMMA 19–24% inorganic filler 18–25%, silanized silica inorganic filled prepolymer (PMMA/UDMA) 35–40% |
4.5 | >260 | – |
Composite II SR Phonares II Incisal and Dentin |
MMA 17–20% Dimethacrlyates (UDMA) 17.5–22% PMMA 6–9% inorganic filler 9–12%, silanized silica inorganic filled prepolymer (PMMA/UDMA) 39–45% |
3.9 incisal 4.4 |
235 Incisal 258 |
1.40 (0.15) incisal 1.55 (0.10) |
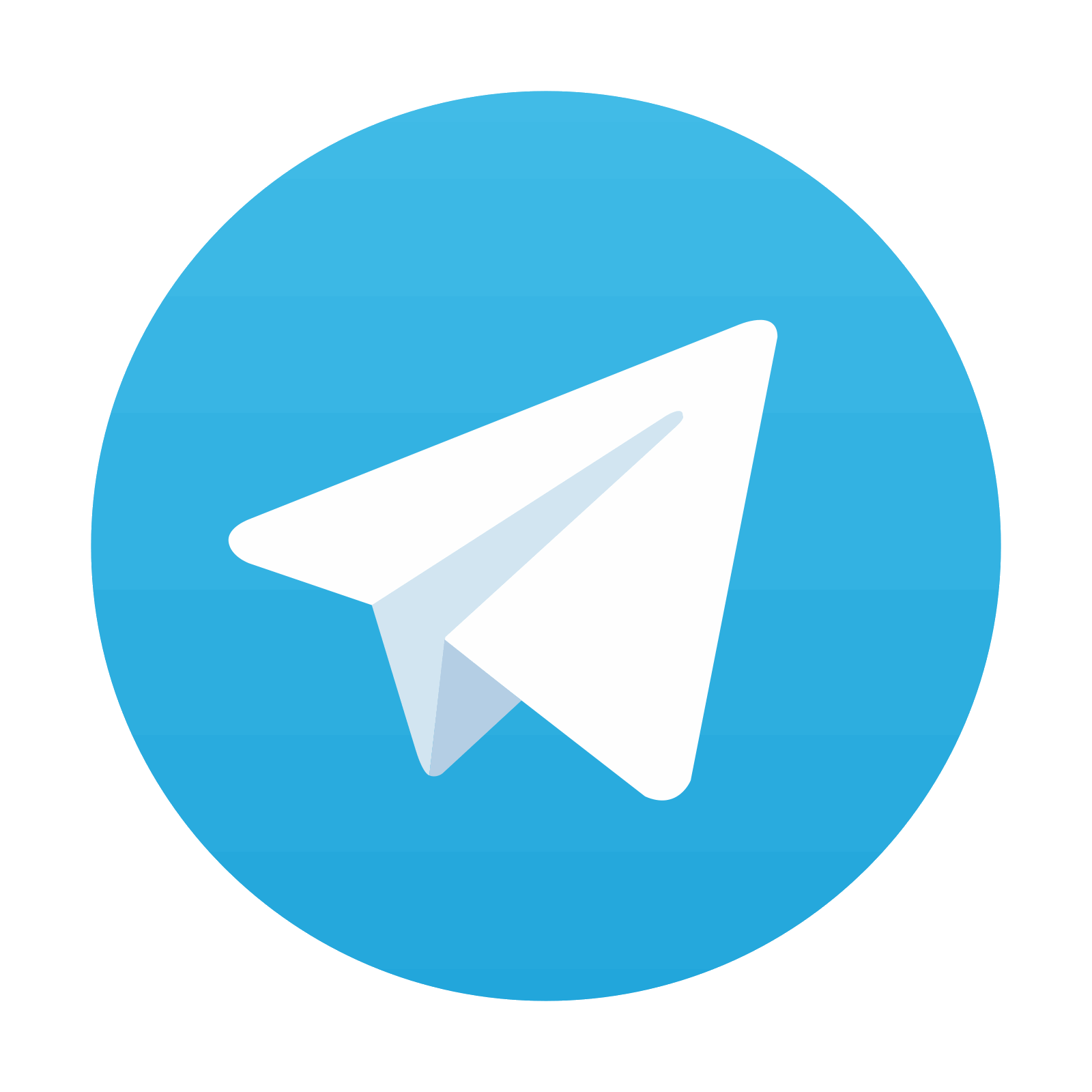
Stay updated, free dental videos. Join our Telegram channel

VIDEdental - Online dental courses
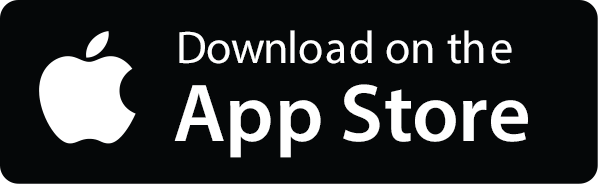

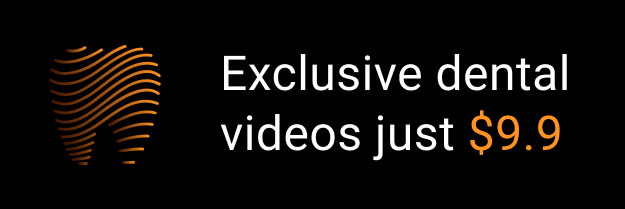