Abstract
Objective
To investigate the potential application of bilateral treatment of glazing plus staining in machinable veneer mechanical strength improvement.
Methods
Standard laminate specimens ( n = 105) were sliced from machinable ceramic blocks and divided into seven batches for further treatments: (1) batch C, standard specimens; (2) batch P, one specimen surface polished; (3) batch F, fired in glaze-firing-program without glaze; (4) batch G, fired with glaze on one surface; (5) batch S, fired with stain on one surface; (6) batch GA, fired with glaze on one surface, then re-fired in stain-firing-program without stain, and (7) batch GS, fired with glaze on one surface then fired with stain on the other side. The flexural strength of all specimens was tested with a three-point-bending test and the results statistically evaluated. Scanning electron microscopy (SEM) was used to analyze fractographs of bilateral treatment specimens. X-ray diffraction (XRD) analysis was performed to evaluate the influence of thermal annealing effect on strength improvement in bilateral treatment.
Results
The flexural strength of bilateral treated GS (143.23 ± 14.02 MPa) was significantly higher ( P < 0.05) than unilateral treated G (125.92 ± 14.01 MPa) and P (114.48 ± 8.45 MPa) and other batches, including C (100.11 ± 6.65 MPa), F (99.48 ± 8.61 MPa), S (119.28 ± 19.34 MPa) and AG (126.65 ± 9.83 MPa). SEM imaging showed that no underlying separation between the glaze–matrix or stain–matrix could be found in the fractured GS specimen. No evidence of Bragg diffraction peak broadening could be seen in XRD spectra compared with specimens from batches C and AG.
Significance
To improve machinable laminate strength, a bilateral treatment comprising staining and glazing gave higher strength than unilateral glazing or polishing alone. It was the surface layer effect achieved by glazing and staining, not the thermal annealing effect achieved during glaze and stain sintering, which contributed to the laminate strength improvement.
1
Introduction
Feldspar machinable ceramics are used in chair-side CAD/CAM (computer aided design/computer aided manufacturing system). These prefabricated ceramic blocks can be directly sculpted by a digital milling machine into the shape of the final restorations during a one-visit treatment . The restorations can be stained or glazed before placement or polished after cementation .
The success rate of the CAD/CAM restorations depends not only on the precision of the machining system but also on the strength of the materials . The CAD/CAM prefabricated blocks initially present with good mechanical strength because they are manufactured under precise industrially controlled conditions, which result in fine crystals and no pores. However, the final restoration needs to be shaped into a desirable contour using CAM-controlled high-speed rotating bars. This milling process may result in a large number of microscopic cracks on the surface of the ceramics and decrease the mechanical strength of the restoration , as the strength of these brittle dental materials correlates with the surface flaws. If the applied stress is higher than the strength of the brittle material, mechanical failure occurs. This point depends on the size of the cracks formed during the process of the fabrication . On the other hand, when the stresses are sustained or intermittent over a long period, brittle materials will inherently show a tendency to fatigue. Additionally, small cracks may grow, in particular in the presence of water, self-propagate and result in catastrophic failure . These problems could be worse in laminate veneers due to their lack of thickness that might otherwise resist crack propagation. In addition, the bonding side is the initiation surface for cracks that progress into fractures because this side bears the tensile force when load is applied to the veneer.
For the aesthetic purposes and longevity requirements, re-strengthening of CAD/CAM veneers is required so glazing or polishing strategies have been practiced. Glaze is fired onto the surface of the ceramics to reduce the depth and width of the surface flaws and it also applies residual surface compression to improve the contact damage resistance of the ceramics . Polishing is another method widely used in the clinic to reduce the surface flaws of the ceramics .
Regardless of whether glazing or polishing is used, the conventional strategy to improve material strength is to use one of these methods on the labial surface of the veneers. However, the milling process also produces flaws on the surface of the veneer’s bonding side, which is not treated and protected. The hypothesis of this study was that bilateral treatment of the veneer’s two surfaces – labial side glazing plus bonding side staining – might attain an improved re-strengthening effect than unilateral treatments by glazing or polishing of the labial surface alone.
2
Materials and methods
2.1
Specimen preparation
Standard specimens (14.0 × 4.0 × 0.9 mm) were manufactured from machinable ceramic blocks (VITABLOCS, Mark-II for CEREC, I-12 A1C, Vita Zahafabric, Bad Säckingen, Germany), which were sliced by a water-cooled linear precision saw (ISOMET 4000, Buehler, USA) at low speed (0.5 mm/min). The specimens’ surface roughness ( R a ) ranged from 0.3 to 0.5 μm, measured by a Surface Roughness Tester (Starret 3800, L. S. Starrett Company, MA, USA). In addition, the four long borders (14.0 mm) of each specimen were finished with silicon rubber instrument to remove brim defects.
105 specimens were divided into seven batches, each consisting of n = 15 specimens, according to differing subsequent treatments:
-
Control batch (C): the specimens were left untreated to simulate crude restorations, directly sculpted by the CAD system.
-
Polishing batch (P): one surface of the specimens was polished with a rotating grinding rubber disc (Enamel Polishing Kit, Shofu Company, Japan) to attain R a < 0.2 μm to simulate the polishing effect in clinics.
-
Firing batch (F): specimens were fired in a furnace (Vita Vacumat 40T, Germany), following the glaze-firing-procedure (GFP) in accordance with the company’s recommendations (peak heating temperature was 980 °C).
-
Glazing batch (G): glazes (Vita Akzent glaze Akz25, Vita Akzent fluid , weight ratio of powder/liquid = 1:1) were fired on one surface of the specimens following the GFP. To control glaze thickness, a tape pool (0.2 mm in depth) was used to hold the glaze mud before firing.
-
Staining batch (S): stains (Vita Akzent Akz05 gold earth stain, Vita Akzent glaze Akz25, Vita Akzent fluid, weight ratio of powder/powder/liquid = 2:1:3) were fired on one surface of the specimens using the stain-firing-procedure (SFP). The thickness control was the same as that in the glazing batch but the peak heating temperature was 850 °C.
-
Annealed glazing batch (AG): specimens were first glazed by the method used for the G batch, then re-fired by the method used for the S batch but without applying stains.
-
Glazing plus staining batch (GS): one surface of the specimens was first fired with glazes and then the other surface was fired with stains. The firing programs were the same as those carried out for batches G and S, respectively.
Before testing, all specimens were ultrasonically cleaned and stored in tap water at 37 °C for 24 h.
2.2
Flexural strength testing
All specimens in the seven experimental groups were fractured at room temperature (23 °C) in a three-point bending test (span L = 10 mm) with a universal testing machine (Instron Model 1362, Instron Corp., Canton, MA, USA) at a crosshead speed of 0.5 mm/min. The load-deflection ( P , u ) curves were recorded. The thickness ( d ) and the width ( b ) were measured with a micrometer. A crosshead extension was used to align and center the flexure-testing jig. In each test, the treated surface of the specimen was positioned opposite the crosshead, as the testing surface assigned to the tension surface ( Fig. 1 ), Eq. (1) was used to calculate the flexural strength.
σ = 3 W L 2 b h 2
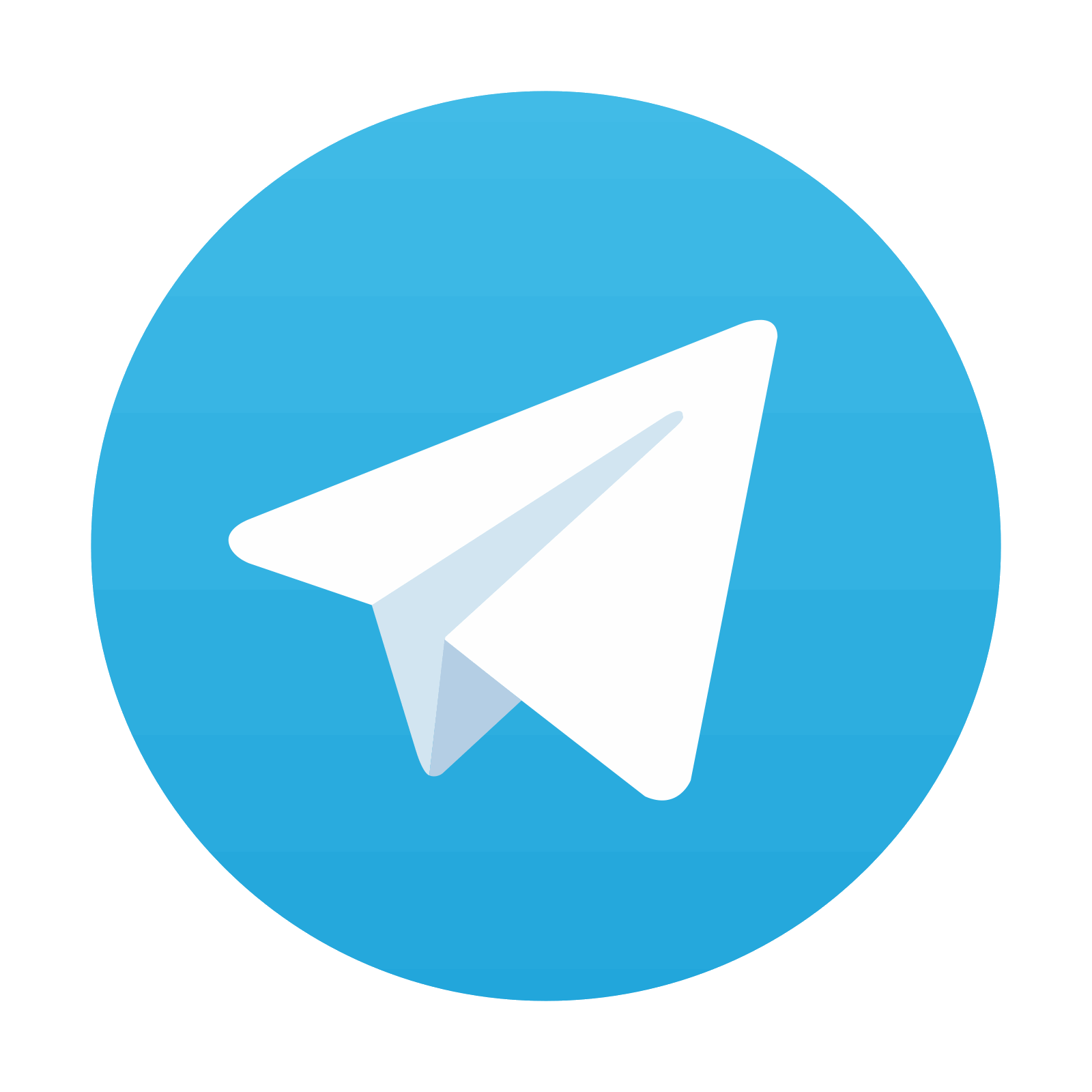
Stay updated, free dental videos. Join our Telegram channel

VIDEdental - Online dental courses
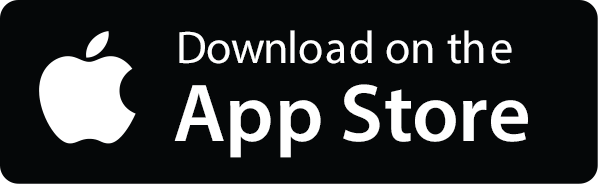
