Abstract
Objective
The Shore hardness test is a quick and convenient way to measure hardness of elastomers. The test specifies that the specimen should be at least 6 mm thick; however, published work in the literature indicates that workers often use much thinner samples. The aim of this study was to investigate the effect of thickness on the measured hardness of a range of dental elastomers and develop a theoretical relationship to predict the effect.
Methods
7 dental silicone elastomers were selected to give a range of hardness values. Shore A scale hardness measurements were made on standard thickness samples, and those of lower thicknesses. A theoretical analysis was derived, whereby the effect of thickness of the sample on its measured hardness can be predicted and was tested using the results obtained.
Results
The results show reasonable agreement between theoretical and experimental values. The measured Shore hardness increased inversely with thickness, the effect being most pronounced with thin samples. Results ranged from 66.3 ± 1.6–80.9 ± 0.4 for 1 mm thick to 35.0 ± 1.7–69.1 ± 0.6 for the 6 mm thickness. Ratio of the measured hardness of 1 mm/6 mm ranged from 1.97 for the softest material to 1.17 for the hardest.
Significance
Measurements obtained with a Shore A hardness tester on samples of less than the specified 6 mm thickness will give erroneously high values, the error being greater as thickness decreases. The theoretical treatment proposed gives a basis on which data obtained from studies that used thinner specimens can be better analysed.
1
Introduction
The measurement of hardness can conveniently be divided into two main types:
- (a)
On metals and other rigid ductile materials. In this case the indenter is applied with sufficient force to produce plastic deformation. There are a number of such tests, e.g. Brinell, Rockwell, and Vickers . The theoretical basis of such testing was established by Tabor .
- (b)
On elastomers, where the deformation is elastic. There are basically two types of test, namely the International Standards Organisation (ISO) test, which employs a spherical indenter , and the Shore hardness test, which employs a truncated cylinder ; there are two Shore hardness tests, Shore A and Shore D, covering different hardness ranges.
The ASTM specification for Shore hardness specifies a test specimen “shall be at least 6 mm thick—the lateral dimensions of the specimen shall be sufficient to permit measurements at least 12 mm from any edge.” This is presumably to ensure that the stresses around the indenter are effectively zero both at the bottom and the edges of the specimen. In terms of elasticity theory the specimen is effectively a semi-infinite solid.
An early reference to the relationship between Shore hardness, and International hardness appears in graphical form in a British Standard Specification . Subsequently, Gent derived the following formula, using the classical theory of indentation by a cylinder.
E ( MPa ) = 56 + 7.66 s 2.67 r ( 254 − 2.54 s )
where E : Elastic (Young’s) modulus, s : Shore hardness, and r : the radius of the indenter (note the original formula of Gent has been adjusted to give E in SI units).
As the indenter of the Shore A hardness tester is a truncated cone, Gent used the mean radius for r . This gives:
E ( MPa ) = 56 + 7.66 s 0.1375 ( 254 − 2.54 s )
Fig. 1 shows a plot of Eq. (2) .

This fitted the BSI curve well, except for low hardness values.
The theory from which Gent derived Eq. (1) , and hence (2) , is that for the deformation of a semi-infinite sold by the flat end of a cylindrical indenter :
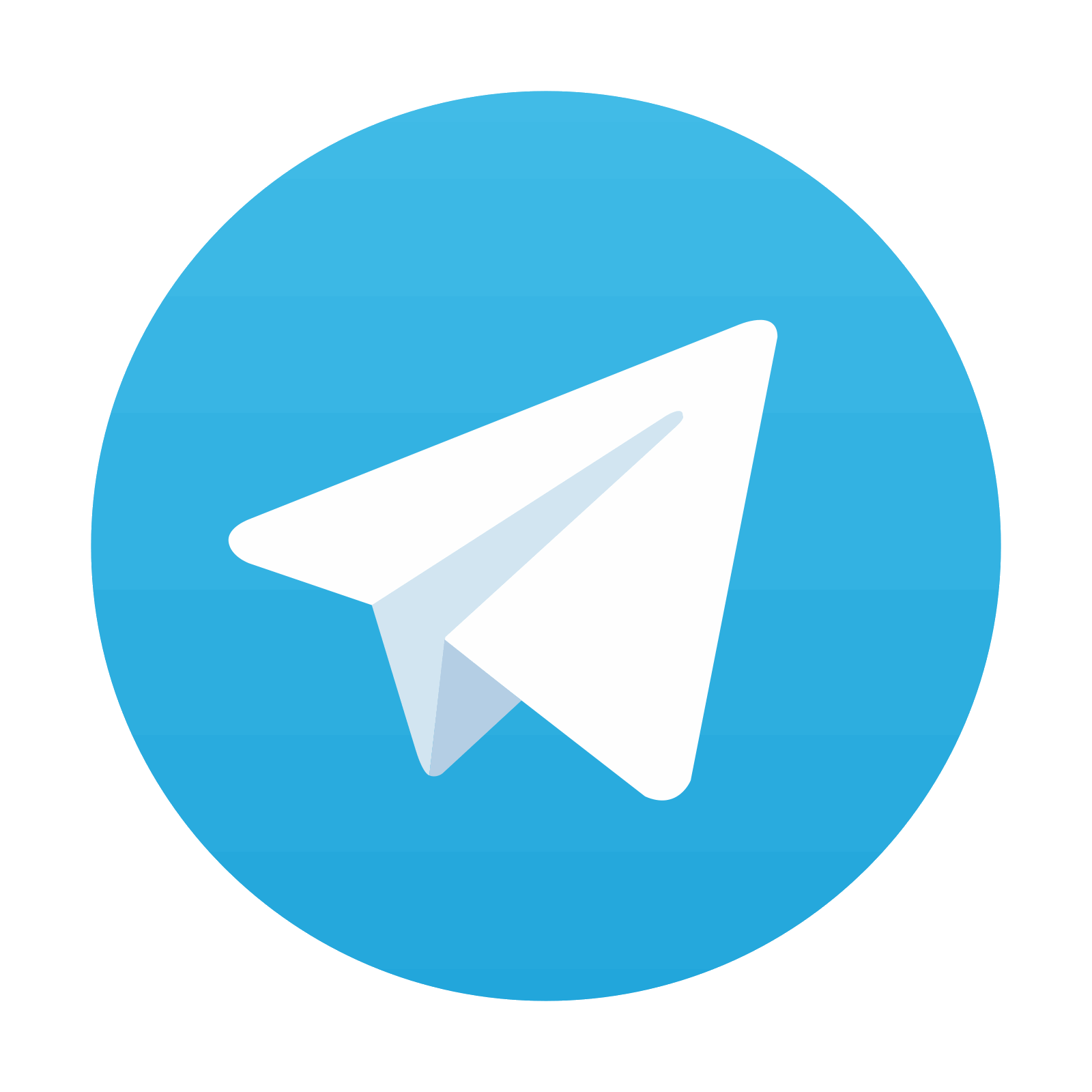
Stay updated, free dental videos. Join our Telegram channel

VIDEdental - Online dental courses
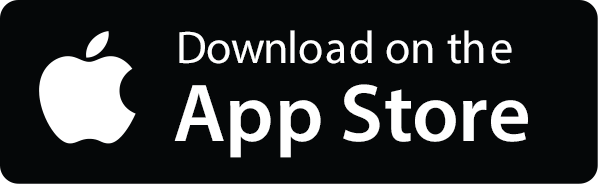
