Abstract
Objectives
This in vitro study aimed to evaluate and compare marginal fit of three-unit fixed dental prostheses (FDPs) fabricated using a newly developed direct metal laser sintering (DMLS) system with that of three-unit FDPs by a conventional lost wax technique (LW) method.
Methods
Ten cobalt–chromium alloy three-unit FDPs using DMLS system and another ten nickel–chromium alloy FDPs using LW method were fabricated. Marginal fit was examined using a light-body silicone. After setting, the silicon film was cut into four parts and the thickness of silicon layer was measured at 160× magnification using a digital microscope to measure absolute marginal discrepancy (AMD), marginal gap (MG) and internal gap (IG). A repeated measure ANOVA for statistical analysis was performed using the SPSS statistical package version 12.0 ( α = 0.05).
Results
The mean values of AMD, MG, and IG were significantly larger in the DMLS group than in the LW group ( p < 0.001). Means of AMD, MG and IG in the first molars were 83.3, 80.0, and 82.0 μm in the LW group; and 128.0, 112.0, and 159.5 μm in the DMLS group, respectively. No significant difference between measurements for premolars and molars was found ( p > 0.05).
Significance
The marginal fit of the DMLS system appeared significantly inferior compared to that of the conventional LW method and slightly larger than the acceptable range. For clinical application further improvement of DMLS system may be required.
1
Introduction
Metal ceramics have been one of the most widely used materials for fixed types of dental prostheses . A porcelain-fused-to-metal dental prosthesis is composed of a metal coping or framework covered with multi-layer sintered porcelain material. An essential factor for maintenance of a metal–ceramic fixed dental prosthesis is marginal fit of the metal coping . A fixed dental prosthesis with good marginal fit may reduce risks of secondary caries and gum diseases by minimizing marginal accumulation of food, bacteria, and plaque . Therefore poor marginal fit has been reported as a critical cause of failure of a fixed dental prosthesis .
Although traditionally metal copings have been fabricated by the lost wax technique (LW) and casting method, possible problems have been suggested related to this complex procedure for crown fabrication. For example, taking impressions in the oral cavity may incur discomfort for patients and inaccurate marginal fit may result from contraction of impression material, distortion of wax patterns, or irregularities in the cast metal. In efforts to overcome the limitations of the LW method, computer-aided design/computer-aided manufacturing (CAD/CAM) systems have been introduced with various ways to produce a dental prosthesis. The newly developed direct metal laser-sintering (DMLS) system is an additive metal fabrication technology, based on information received from three dimensional CAD, in which metal powder is shot selectively using a data file and fused with a laser to laminate approximately a 20–60 μm-thick layer with each shooting to complete a metal structure. Advantages of the DMLS system include easy fabrication of complicated shapes, operation of an automatic system, and short working time due to elimination of the procedures of fabricating a wax pattern, investing, burning, and casting works. While the traditional casting method using the LW method might waste metal in spruing and other procedures, the DMLS system could reduce metal waste by selectively shooting the required amount. One disadvantage of the DMLS system is the expensive price of the equipment. While an essential condition for a successful dental prosthesis is good marginal fit , there is little data on the marginal fit of fixed dental prostheses (FDPs) fabricated by the DMLS system.
The aim of this study was to evaluate and compare marginal fit of three-unit FDPs fabricated using a newly developed DMLS system with that of three-unit FDPs made by a conventional LW method. The null hypothesis was that there would be no difference in marginal fit between two groups.
2
Materials and methods
2.1
Fabrication of models
A typodont model with a missing maxillary right second premolar was prepared (Model #3017, Viade products, CA, USA). Abutment preparation was performed on the first premolar and first molar with 1.2 mm, 360° chamfer margin. A silicone impression (Zerosil, Dreve Dentamid GmbH, Unna, Germany) was taken before cutting to control the amount of the reduction. After preparation ten silicone impressions (Fresh, Dreve Dentamid GmbH, Unna, Germany) were made using personal resin trays (Trayplast, Vertex, Netherlands) and epoxy (Modralit ® 3K, Dreve Dentamid GmbH, Unna, Germany) was injected to fabricate ten epoxy models.
2.2
Fabrication of three-unit FDPs using DMLS system
Ten epoxy models were scanned by laser scanner (D-700, 3shape A/S, Copenhagen, Denmark). An experienced dental technician designed 0.5 mm-thick three-unit FDPs including 30 μm of cement film thickness with no space 0.5 mm from the margin using CAD software (3shape Dental Designer, 3shape A/S, Copenhagen, Denmark), following the manufacturer’s instructions, and completed standard template library (STL) files that were used to fabricate metal frameworks using the DMLS system (EOSINT M270, EOS GmbH, Germany). The DMLS technology fuses metal powder into a solid part by melting it locally using the focused laser beam and builds up additively layer by layer, typically using layers 20 μm thick (accessed on September 20, 2012). A cobalt–chromium (Co–Cr) alloy powder (EOS Cobalt Chrome SP2, EOS, Germany) with major components of cobalt–chromium–molybdenum–tungsten (Co–Cr–Mo–W) according to the EN ISO 22674:2006 standard, was used.
2.3
Fabrication three-unit FDPs using LW and casting method
Based on the STL file created, ten resin patterns of three-unit FDPs were made using the resin printing method with light curing resin (ProJet™ DP3000, Three D Systems Circle, Rock Hill, SC, USA) (accessed on September 20, 2012). Finished resin patterns were duplicated with putty and melted wax was injected to obtain wax patterns whose shapes are exactly the same with the FDPs by DMLS system. The same experienced technician investigated the marginal fit of the duplicated wax patterns using a microscope (AIS-10L, Daemyung optical PRODUCT, Dae-jeon, Korea, 10×). The wax patterns were invested after installing injection line (Bellavest SH ® , BEGO, Germany) and burned out. A nickel–chromium (Ni–Cr) alloy (Bellabond plus, BEGO, Germany) and high frequency casting machine (Fornax, BEGO, Germany) were used in the casting procedure ( Fig. 1 ).
2.4
Preparation of silicon replica and sectioning
To evaluate the gap between the frameworks and abutments, light-body silicone (Fresh ® , Dreve, Germany) was used. The three-unit FDPs filled with light-body silicon inside were set on the model and pressed toward a longitudinal occlusal direction with a constant finger pressure of 50 N ( Fig. 2 ). Finger pressure was standardized by repeated trials and controlled using an electronic scale. After careful removal of three-unit FDPs from the model, the light-body silicon replica was embedded in heavy-body silicon filled in a square box tray made of baseplate wax, in order to support the thin silicon replica. The finished replica was sectioned twice in the buccuo-lingual direction and in the mesio-distal direction with a razor blade. For standardized sectioning, the midpoint was marked of the buccal, lingual, mesial, and distal surfaces.
2.5
Measurements of marginal fit
The thickness of the light-body silicone replica was measured using a digital microscope (KH-7000, HIROX, Hackensack, NJ, USA) at 160× magnification ( Fig. 3 ). To evaluate the marginal fit, three types of marginal fit were measured, including absolute marginal discrepancy (AMD), marginal gap (MG), and internal gap (IG) ( Fig. 4 ). AMD, MG, and IG were defined as distance from the edge of the metal structure to the abutment margin, distance from the abutment margin to the metal coping in a straight line, and distance between the abutment and metal coping at the most inner point which is parallel to the marginal gap, approximately 400 μm inside from the MG, respectively .
Before measuring, calibration of the digital microscope and an examiner (the first author, Kim KB) was done by repeated trials. A total of 480 measurements of marginal fit were obtained by the examiner as three types of marginal fit (AMD, MG, and IG) per four sides (buccal, lingual, mesial and distal) per two abutments (first premolar and first molar) in ten samples for each of the two comparative groups. The same measurement procedure was repeated by the same examiner after two weeks to assess the intra-examiner reliability of measurements.
2.6
Statistical analysis
The descriptive statistics for AMD, MG, and IG were displayed as mean and standard deviation. Mean AMD, MG, and IG by different methods were compared using independent t -test in premolars and molars. A repeated measures analysis of variance (ANOVA) was used to compare mean difference between LW and DMLS groups in premolars and molars under consideration of four repeated measurements on buccal, lingual, mesial and distal sides. Reliability of the measurements was assessed using the intraclass correlation coefficient (ICC). A statistical software SPSS version 12.0 (SPSS Inc., Chicago, IL, USA) was used and a type one error rate of 0.05 was applied in determining statistical significance.
2
Materials and methods
2.1
Fabrication of models
A typodont model with a missing maxillary right second premolar was prepared (Model #3017, Viade products, CA, USA). Abutment preparation was performed on the first premolar and first molar with 1.2 mm, 360° chamfer margin. A silicone impression (Zerosil, Dreve Dentamid GmbH, Unna, Germany) was taken before cutting to control the amount of the reduction. After preparation ten silicone impressions (Fresh, Dreve Dentamid GmbH, Unna, Germany) were made using personal resin trays (Trayplast, Vertex, Netherlands) and epoxy (Modralit ® 3K, Dreve Dentamid GmbH, Unna, Germany) was injected to fabricate ten epoxy models.
2.2
Fabrication of three-unit FDPs using DMLS system
Ten epoxy models were scanned by laser scanner (D-700, 3shape A/S, Copenhagen, Denmark). An experienced dental technician designed 0.5 mm-thick three-unit FDPs including 30 μm of cement film thickness with no space 0.5 mm from the margin using CAD software (3shape Dental Designer, 3shape A/S, Copenhagen, Denmark), following the manufacturer’s instructions, and completed standard template library (STL) files that were used to fabricate metal frameworks using the DMLS system (EOSINT M270, EOS GmbH, Germany). The DMLS technology fuses metal powder into a solid part by melting it locally using the focused laser beam and builds up additively layer by layer, typically using layers 20 μm thick (accessed on September 20, 2012). A cobalt–chromium (Co–Cr) alloy powder (EOS Cobalt Chrome SP2, EOS, Germany) with major components of cobalt–chromium–molybdenum–tungsten (Co–Cr–Mo–W) according to the EN ISO 22674:2006 standard, was used.
2.3
Fabrication three-unit FDPs using LW and casting method
Based on the STL file created, ten resin patterns of three-unit FDPs were made using the resin printing method with light curing resin (ProJet™ DP3000, Three D Systems Circle, Rock Hill, SC, USA) (accessed on September 20, 2012). Finished resin patterns were duplicated with putty and melted wax was injected to obtain wax patterns whose shapes are exactly the same with the FDPs by DMLS system. The same experienced technician investigated the marginal fit of the duplicated wax patterns using a microscope (AIS-10L, Daemyung optical PRODUCT, Dae-jeon, Korea, 10×). The wax patterns were invested after installing injection line (Bellavest SH ® , BEGO, Germany) and burned out. A nickel–chromium (Ni–Cr) alloy (Bellabond plus, BEGO, Germany) and high frequency casting machine (Fornax, BEGO, Germany) were used in the casting procedure ( Fig. 1 ).
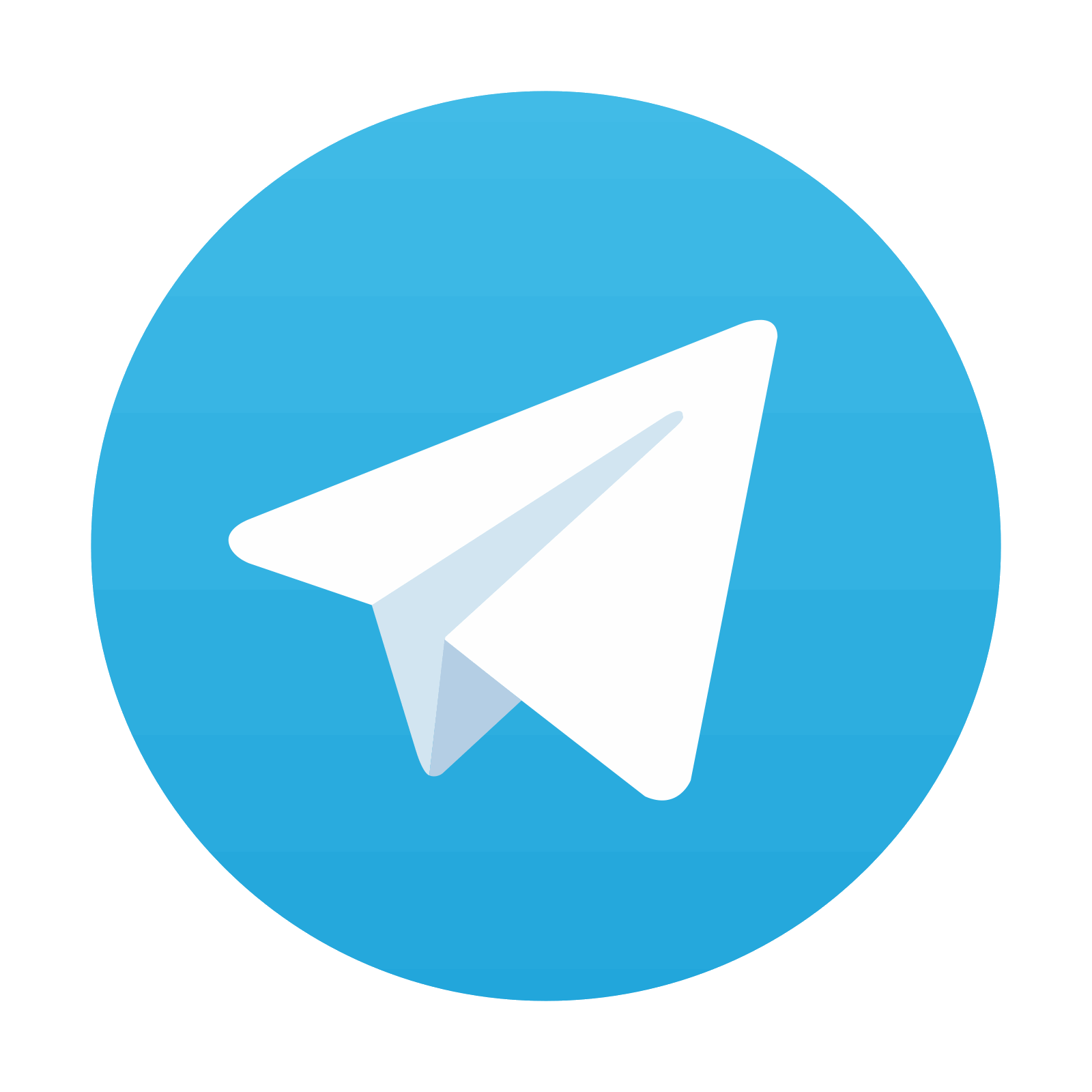
Stay updated, free dental videos. Join our Telegram channel

VIDEdental - Online dental courses
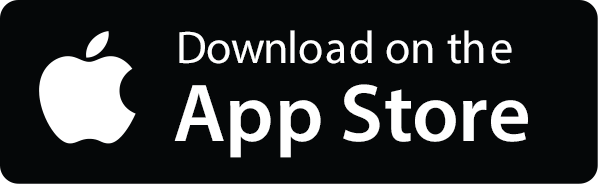

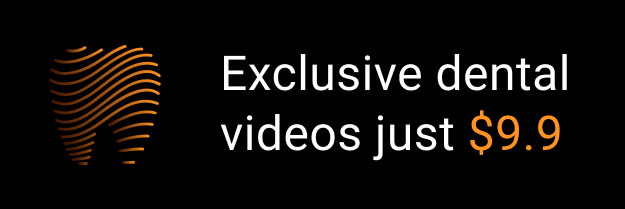