Abstract
Objectives
To identify a reproducible and discriminatory mechanical testing methodology to act as a performance indicator for hand-mixed glass-ionomer (GI) restoratives.
Methods
Groups of 20 (five batches of four) cylinders (6.0 ± 0.1 mm height, 4.0 ± 0.1 mm diameter) for compressive fracture strength (CFS) and compressive modulus (CM) testing, bars (25.0 ± 0.1 mm length, 2.0 ± 0.1 mm width, 2.0 ± 0.1 mm thickness) for three-point flexure strength (TFS) and tensile flexural modulus (TFM) testing, discs (13.0 ± 0.1 mm diameter, 1.0 ± 0.1 mm thickness and 10.0 ± 0.1 mm diameter, 3.10 ± 0.03 mm thickness) for biaxial flexure strength (BFS) and Hertzian indentation (HI) testing, respectively, were prepared using a hand-mixed GI restorative manipulated with 100–20% (in 10% increments) of the manufacturers recommended powder content for a constant weight of liquid. Data were statistically analyzed at p < 0.05, the coefficient of variation (CoV) was assessed for the four tests at each powder:liquid mixing ratio investigated ( n = 9) and a Weibull analysis performed on the CFS, TFS and BFS data to assess the reliability of the data sets. The failure mode and fracture origin of the HI specimens was assessed by fractography.
Results
For the hand-mixed GI restorative, a progressive reduction in the powder content (by 10% for a constant weight of liquid) resulted in a progressive linear deterioration ( p < 0.001) in the CFS ( R 2 = 0.957), CM ( R 2 = 0.961) and TFM ( R 2 = 0.982) data. However, no linear deterioration ( p > 0.05) was identified for the TFS ( R 2 = 0.572), BFS ( R 2 = 0.81) and HI ( R 2 = 0.234). The CoV and Weibull data identified distinct regions – three for the CFS and TFS data and two for the BFS data sets, within the range of powder:liquid mixing ratios investigated. Fractographic analysis of HI specimens revealed a transition in failure mode from bottom-initiated radial cracking to top-initiated cone cracking on reducing the powder content for a constant weight of liquid.
Significance
The CFS test is the only discriminatory performance indicator for hand-mixed GIs from amongst the four mechanical testing approaches (CFS, TFS, BFS and HI) investigated. The CM and TFM represent an intrinsic material property independent of specimen dimensions and may be used as an adjunct to a mechanical testing approach when investigating hand-mixed GIs.
1
Introduction
The discovery of glass-ionomers (GIs) by Wilson and Kent in 1969 was accomplished on testing the 200th glass composition (G-200) and a clinically acceptable dental cement was realized . G-200 remained the only glass composition capable of forming a GI suitable for clinical use prior to the discovery of the role of tartaric acid in the setting reaction . Following the establishment of the role of tartaric acid as a chelating agent , further opportunities were identified for a number of glass compositions other than G-200 . Since the original ground breaking research into the development of GIs, manufacturers and investigators have employed different glass formulations to improve the mechanical properties, enhance radiopacity and increase the reactivity of the glass powder by modifying the calcium fluoroaluminosilicate glass composition with strontium , zirconia , lanthanum and zinc . Additionally, investigators have prepared aluminoborate and zincsilicate glass compositions for use in GIs with varied levels of success.
The compressive fracture strength (CFS) testing methodology is the only strength test specified in the International Organization for Standardization (ISO-9917-2003) for GIs. However, the reliability and validity of the CFS testing protocol have been questioned . A ‘test-house variability’ study in 1990 identified inter-operator variability (between different test centers) was considerable and intra-operator variability (between individual operators) was also significant such that the poor reliability of the CFS testing protocol was ‘inappropriate’ for inclusion in the standard . Additionally, the failure mode of dry gypsum cylinders was ‘vertical split slabbing mode’ but when wet with water or alcohol changed to failure on the ‘diagonal planes running from top left to bottom right’ . However, the stress at failure calculation was independent of the failure mechanism which raised concerns regarding the validity of the CFS test . Alternative mechanical testing approaches including three-point flexure strength (TFS) , biaxial flexure strength (BFS) and Hertzian indentation (HI) tests have been suggested as potential replacement testing methodologies to be adopted in ISO-9917-2003 – albeit for encapsulated GIs. Encapsulated GIs offer control over inaccurate dispensation of the powder and liquid components by the operator, where the optimum powder and liquid proportions are predetermined by the manufacturer . The issue of identifying a reliable and valid testing methodology is complicated further for hand-mixed GIs as a result of the range of powder:liquid mixing ratios routinely employed clinically . Interestingly, powder contents as low as 37% of that specified by the manufacturer were identified for Chemfil II, a hand-mixed GI, when prepared by 22 dental nurses – eleven employed in general dental practice and eleven from a dental hospital setting . Hand-mixed GIs tested in the laboratory are prone to large variations in the mechanical property data arising from inadequate control of the testing conditions and the non-standardized nature of the product delivery systems namely powder scoops and liquid dropper bottles . The microstructure of a set GI is composed of unreacted glass core fillers sheathed by a siliceous hydrogel and dispersed in a polyacrylate matrix . Therefore, the mechanical properties of GIs arise from the reinforcing glass phase where a linear deterioration on reducing the powder content from that specified by the manufacturer would be expected following testing with an appropriate testing methodology .
It is important to appreciate, however, that if one was charged with the task of delivering a novel reinforced GI restorative, the optimum powder:liquid mixing ratio would need to be identified by hand-mixing the GI liquid with varying GI powder content and performing preliminary mechanical tests. The mechanical testing protocol of choice would therefore require to be discriminatory between the different powder:liquid mixing ratios employed, thereby identifying a linear deterioration when the powder content is reduced from the optimum value. As a result, the aim of the current study was to identify a reproducible and discriminatory testing methodology to act as a performance indicator for hand-mixed GI restorative materials. The hypotheses proposed was that each of the commonly used mechanical testing protocols employed to determine the performance of GIs (CFS, TFS, BFS and HI) would act as performance indicators by identifying the linear deterioration in the mechanical properties on reducing the powder content from that specified by the manufacturer.
2
Materials and methods
The GI restorative used (Ionofil Molar: Voco GmbH, Cuxhaven, Germany, Powder: V50335, Liquid: V50375) was hand-mixed for 40 s with the manufacturer’s recommended powder:liquid mixing ratio (4:1 g:g) . A glass slab was placed on a balance accurate to 0.001 g (Sartorius Expert, Sartorius AG, Goettingen, Germany), the appropriate weight of GI powder and liquid were dispensed and the powder divided into two equal portions. A stainless steel mixing spatula was used to mix half the powder with the liquid for 20 s, followed by the addition of the remaining powder for a further 20 s in a temperature (21 ± 1 °C) and humidity (50 ± 5%) controlled laboratory . To simulate the distribution of powder:liquid mixing ratios routinely produced by operators in clinical practice, GIs were prepared by reducing the manufacturers recommended powder content (in 10% increments for a constant weight of liquid) – to a minimum of 20%.
To identify a reproducible and discriminatory test methodology, 20 (five batches of four) specimens were prepared for each test methodology (CFS, TFS, BFS and HI) at the powder:liquid mixing ratios ( n = 9) investigated. Specimen manufacture was randomized by assigning a number to each specimen batch and prior to specimen manufacture a number was drawn to determine the mixing ratio group to be manufactured. Only five batches of specimens were made daily to minimize the influence of operator fatigue .
2.1
Compressive fracture strength (CFS)
CFS specimens (6.0 ± 0.1 mm height, 4.0 ± 0.1 mm diameter) were prepared using a polytetrafluoroethylene (PTFE) split-mold resting on top of a PTFE base which was covered by an acetate strip. Alignment of the split-mold was achieved by inserting a locating pin and the split-mold was fixed using nylon wedges which ensured equal pressure was applied along its length. The GI restorative was consolidated to one side of the unfilled mold to avoid air trapping and packed to excess before an acetate strip was used to cover the filled mold. Pressure was applied using a 1 kg weight, the assembly clamped and stored for 1 h in a water-bath (37 ± 1 °C). After 1 h, the mold assembly was disassembled, the specimens demoulded, numbered and stored in 50 ml of distilled water (37 ± 1 °C) for 23 h. Prior to CFS testing, the mean specimen diameter was calculated from three points along its length using a digital micrometer screw gauge reading to 1 μm (Mitutoyo, Kawasaki, Japan). The flat ends of the specimen were covered with wet filter paper (Whatman No. 1, Whatman International Ltd., Maidstone, England) and a compressive load was applied to the long axis of the specimen at a crosshead speed of 1 mm/min (Instron Model 5565, High Wycombe, England). The load-to-failure was recorded and the CFS calculated using Eq. (1) .
where P was the load-to-failure (N) and d the mean specimen diameter (mm). Additionally, the individual stress/strain plots were used to determine the compressive modulus (CM) by calculating the slope of the initial linear segment.
2.2
Three-point flexure strength (TFS)
TFS specimens (25.0 ± 0.1 mm length, 2.0 ± 0.1 mm width, 2.0 ± 0.1 mm thickness) were prepared using an open-ended knife-edged PTFE mold by condensing the GI along the length of the mold. The filled mold was covered with acetate, a 1 kg weight applied, clamped and transferred to the water-bath for 1 h. Following removal from the water-bath, the specimens were demoulded, numbered and transferred for 23 h to 50 ml of distilled water at 37 ± 1 °C. At 24 h, the specimens were loaded in a three-point flexure test rig at 1 mm/min and the load-to-failure recorded. The width and thickness of each fracture fragment was measured using the digital micrometer screw gauge and the TFS was calculated using Eq. (2) .
where P was the load-to-failure (N), L the span between the two point supports (20 mm), b and h the mean specimen width (mm) and thickness (mm). In addition, the tensile flexural modulus (TFM) was calculated using Eq. (3) .
where (ΔPΔD)
Δ P Δ D
was the gradient of the steepest linear portion of the load–deflection curve.
2.3
Biaxial flexure strength (BFS)
BFS specimens (13.0 ± 0.1 mm diameter, 1.0 ± 0.1 mm thickness) were prepared using PTFE ring-molds resting on an acetate-covered glass slab by condensing the GI into the center of the ring-mold to minimize air bubble incorporation. The filled mold was covered with an acetate strip, a 1 kg weight applied, clamped and transferred to the water bath for 1 h. The specimens were then demoulded, numbered and stored in 50 ml of distilled water (37 ± 1 °C) for 23 h prior to testing. The discs were centrally loaded using a 4 mm diameter ball-indenter on a 10 mm diameter knife-edge ring annulus covered with a thin sheet of rubber at 1 mm/min. The load-to-failure was recorded and the BFS calculated using Eq. (4) .
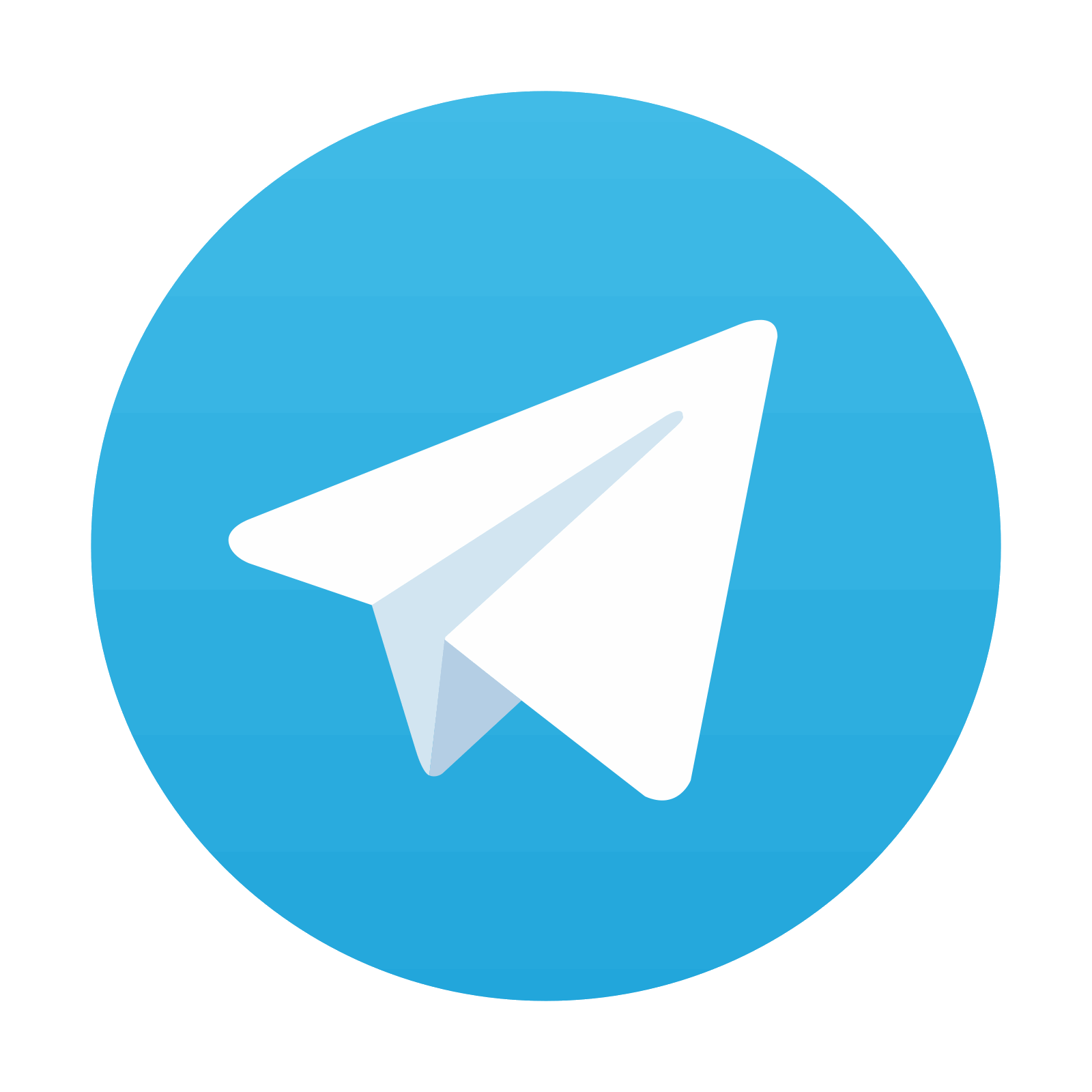
Stay updated, free dental videos. Join our Telegram channel

VIDEdental - Online dental courses
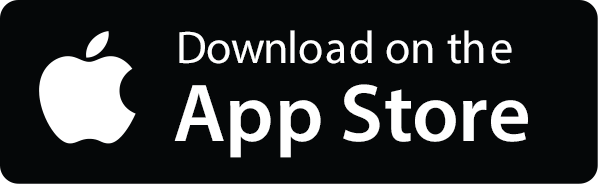
