Abstract
Objectives
Veneered zirconia restorations predominately fail due to veneering fractures. It is hypothesized that a cusp-supporting framework design can prevent these catastrophic failures in all-ceramic restorations. Therefore, we investigated the influence of framework design and framework material on the stress distribution in a single tooth restoration using the numerical finite element method.
Methods
A three-dimensional model of a veneered lower molar (36) crown with constant outer shape was used. The framework design was either cusp supporting or with a constant framework thickness. Zirconia, alumina, and a gold alloy were used as framework material. A glass ceramic material was used as veneering material for both cases. Two different load cases were simulated: terminal occlusion with load distributed over the occlusal surface of the tooth and a fairly extreme load case with all force concentrated on one cusp.
Results
Maximum tensile stresses in the glass ceramic veneering material concentrated in the fissure region for all models. A cusp supporting framework design decreased the maximum tensile stresses significantly up to 30.5%. The distolingual load case resulted in an approximately fourfold higher stress level compared to the terminal occlusion load case.
Significance
A cusp supporting framework design can significantly decrease the maximum tensile stresses in the veneering material of single crowns. Based on the numerical results of this study it can be expected that such a design could decrease the risk of veneering failure in vivo .
1
Introduction
Failure of all-ceramic dental restorations is predominately caused by cohesive fractures of the glass ceramic veneering material. Failure rates up to 13.6% were reported due to this “Chipping” called failure mode . Chipping occurs more often for glass ceramic veneers on zirconia frameworks compared to alumina or metal supported restorations .
One reason for this fact could be the phase transformation mechanism from tetragonal to monoclinic that is present in zirconia. Therefore, this mechanism was considered to have an impact on the chipping behavior .
Other investigations showed an influence of the firing process of the glass ceramic veneering . Comparing metal alloys, alumina, and zirconia material properties as thermal conduction k and specific heat capacity C are highly different (gold alloy: k = 200 W m −1 K −1 , C = 130 J K −1 kg −1 ; alumina: k = 30 W m −1 K −1 , C = 775 J K −1 kg −1 , zirconia: k = 2 W m −1 K −1 , C = 450 J K −1 kg −1 ) . Therefore, a slower cooling process was suggested to decrease the stress level within the veneering material . Other approaches to reduce these residual thermal stresses focused on the difference in the coefficients of thermal expansion (CTE) . It is discussed that the mismatch between the CTE of veneering material and framework material should be adapted for veneered zirconia restorations .
Another important factor influencing the chipping behavior of veneered zirconia restorations is the framework design. An anatomical shape of the framework results in a low and nearly constant veneering thickness. This design is considered to prevent chipping in contrast to a thin framework with a thick and irregularly shaped veneering . Two different stress types can be considered to explain this behavior: residual thermal stresses due to the firing process and mechanical loading stresses.
Residual thermal stresses were shown to be affected by the framework and the veneering thickness. A thin veneering layer tends to a higher stress level using samples with constant zirconia thickness compared to a thicker veneering layer . Compressive stresses occur in the framework due to the CTE mismatch . For a simple bilayer model, stresses can be calculated using equations derived by Swain . However, no clear advice can be given for an adequate thickness ratio because additional residual stresses can be affected by other influences e.g. the phase transformation in zirconia as well .
Zhang et al. investigated the residual stress distributions in an anatomical 2D-Model with constant outer shape of the veneering using the finite element method (FEM) . They found decreasing maximum tensile stresses in the glass ceramic material with increasing framework thickness. A cusp supporting design of the framework may therefore be advantageous to prevent chipping.
Mechanical stresses that occur during mastication can also be strongly affected by the framework design. In a previous FEM-study we investigated the influence of connector thickness in a dental bridge on the stress profile within the veneers . A strong dependence of the framework design and material on the stress distribution was found for different connector sizes.
We hypothesized in this study that a cusp supporting framework design can significantly decrease maximum tensile stresses in the veneering material of a single crown. Therefore, we studied different mastication scenarios using the finite element method. If this hypothesis can be confirmed a cusp supporting design could decrease the risk of veneering failure in vivo .
2
Materials and methods
Geometrical data of the abutment 36 was generated by scanning a prepared gypsum model in vitro . A lower molar was designed to define the veneering surface. This outer contour of the crown was kept constant for all simulations. The 3D-model was imported in STL-format into a commercial CAD software (3matic 5.1, Materialise, Leuven, Belgium) to fix artifacts and holes in the mesh.
Two different framework designs were constructed: a coping with an almost constant framework thickness of approx. 0.8 mm and an anatomically shaped cusp supporting framework with an almost constant veneering thickness of approx. 0.5 mm ( Fig. 1 a and b). No cement gap was simulated. The geometric data was meshed using a curvature-based mesh software (ANSYS ICEM CFD, CFX Berlin Software, Berlin, Germany). Approximately 185,000 tetrahedral elements were generated for each model. Finite element calculations were carried out using a commercial software package (ANSYS 14.0, Ansys Inc., Canonsburg, PA, USA).

In order to simulate the influence of different framework materials the Young’s moduli and Poisson’s ratios were varied. Zirconia, alumina, and a typical gold alloy were used as framework materials. The material properties of a dental glass ceramic were chosen to define the veneering material. The abutment material was defined as dentin. All material properties used are listed in Table 1 .
Young’s modulus (GPa) | Poisson’s ratio | |
---|---|---|
Dentin | 18 | 0.27 |
Glass ceramic | 64 | 0.21 |
Gold alloy | 93 | 0.39 |
Zirconia | 205 | 0.31 |
Alumina | 410 | 0.23 |
Two different loading cases were assumed. To simulate a physiological mastication behavior nine loading areas were defined on the occlusal surface. Additionally a fairly extreme loading situation was simulated by defining one loading area on the distolingual cusp of the crown. Each defined loading area had a radius of 1 mm ( Fig. 1 c and d). A force of 600 N in total was allocated to the respected areas as pressure load normal to the surfaces in each model. The bottom of the abutment teeth model was fully constrained for all simulations. The finite element analysis type was linear and quasi-static.
Stress concentration zones in the framework and in the veneering materials were investigated in post processing. Quasi-brittle materials as glass ceramics, zirconia, and alumina predominately fail because of tensile stresses . Therefore, first principal stress was analyzed for those materials. For the ductile gold alloy von-Mises-Equivalent-Stresses were calculated and used as failure criterion.
2
Materials and methods
Geometrical data of the abutment 36 was generated by scanning a prepared gypsum model in vitro . A lower molar was designed to define the veneering surface. This outer contour of the crown was kept constant for all simulations. The 3D-model was imported in STL-format into a commercial CAD software (3matic 5.1, Materialise, Leuven, Belgium) to fix artifacts and holes in the mesh.
Two different framework designs were constructed: a coping with an almost constant framework thickness of approx. 0.8 mm and an anatomically shaped cusp supporting framework with an almost constant veneering thickness of approx. 0.5 mm ( Fig. 1 a and b). No cement gap was simulated. The geometric data was meshed using a curvature-based mesh software (ANSYS ICEM CFD, CFX Berlin Software, Berlin, Germany). Approximately 185,000 tetrahedral elements were generated for each model. Finite element calculations were carried out using a commercial software package (ANSYS 14.0, Ansys Inc., Canonsburg, PA, USA).
In order to simulate the influence of different framework materials the Young’s moduli and Poisson’s ratios were varied. Zirconia, alumina, and a typical gold alloy were used as framework materials. The material properties of a dental glass ceramic were chosen to define the veneering material. The abutment material was defined as dentin. All material properties used are listed in Table 1 .
Young’s modulus (GPa) | Poisson’s ratio | |
---|---|---|
Dentin | 18 | 0.27 |
Glass ceramic | 64 | 0.21 |
Gold alloy | 93 | 0.39 |
Zirconia | 205 | 0.31 |
Alumina | 410 | 0.23 |
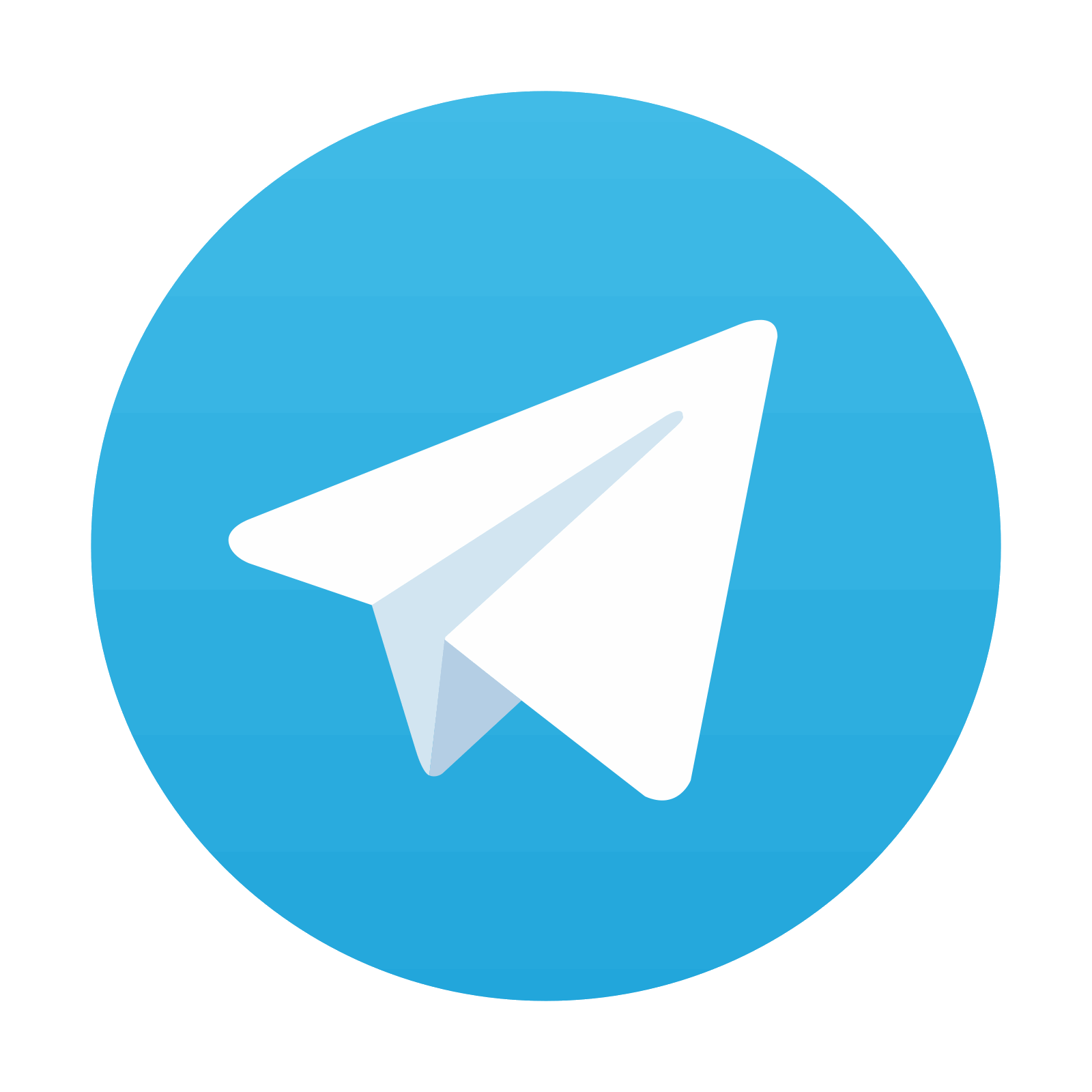
Stay updated, free dental videos. Join our Telegram channel

VIDEdental - Online dental courses
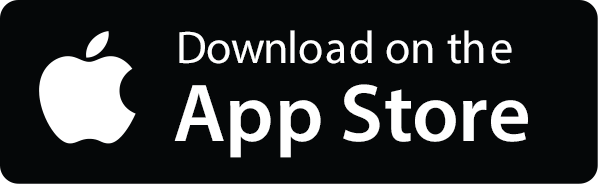

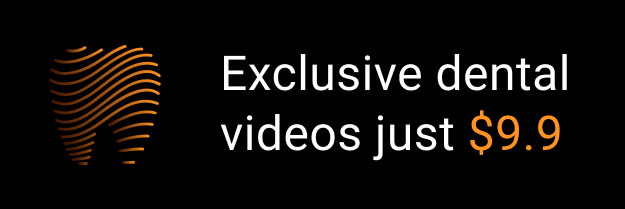