Abstract
Objectives
The null hypothesis was that mechanical testing systems used to determine polymerization stress ( σ pol ) would rank a series of composites similarly.
Methods
Two series of composites were tested in the following systems: universal testing machine (UTM) using glass rods as bonding substrate, UTM/acrylic rods, “low compliance device”, and single cantilever device (“Bioman”). One series had five experimental composites containing BisGMA:TEGDMA in equimolar concentrations and 60, 65, 70, 75 or 80 wt% of filler. The other series had five commercial composites: Filtek Z250 (3M ESPE), Filtek A110 (3M ESPE), Tetric Ceram (Ivoclar), Heliomolar (Ivoclar) and Point 4 (Kerr). Specimen geometry, dimensions and curing conditions were similar in all systems. σ pol was monitored for 10 min. Volumetric shrinkage (VS) was measured in a mercury dilatometer and elastic modulus ( E ) was determined by three-point bending. Shrinkage rate was used as a measure of reaction kinetics. ANOVA/Tukey test was performed for each variable, separately for each series.
Results
For the experimental composites, σ pol decreased with filler content in all systems, following the variation in VS. For commercial materials, σ pol did not vary in the UTM/acrylic system and showed very few similarities in rankings in the others tests system. Also, no clear relationships were observed between σ pol and VS or E.
Significance
The testing systems showed a good agreement for the experimental composites, but very few similarities for the commercial composites. Therefore, comparison of polymerization stress results from different devices must be done carefully.
1
Introduction
In recent years, composite polymerization stress and related phenomena such as cuspal deflection, microleakage, and post-operative sensitivity have received considerable attention from researchers and manufacturers alike. Formulations emphasizing monomer systems tailored to minimize polymerization shrinkage or increase polymer flexibility were introduced, prompting in vitro studies aimed at evaluating their effectiveness .
Several approaches have been used to try and quantify polymerization stress, including mechanical testing , photoelasticity , finite element analysis (FEA) , mathematical modeling , the crack analysis method and the ring slitting method . Among them, mechanical testing systems stand out as the most frequently found . However, when browsing the literature, one is faced with the difficult task of comparing often contradictory data originated from different devices and specimen configurations. Such discrepancies are explained by the fact that stress is a local physical state and, therefore, the stress magnitude developed by a specific material is largely affected by specimen geometry and boundary conditions .
Though most testing systems use cylindrical specimens with a low aspect ratio ( i.e. , height to diameter) and roughly similar dimensions, their compliance levels vary and this is probably the most critical aspect hindering direct comparisons among data reported by different research groups. It could be argued that ideally, as in any mechanical test, polymerization stress test apparatus should present “zero” compliance. In a failure strength test, for example, this means that the load cell registers all of the force applied to the specimen. In fact, many of the testing devices developed to measure polymerization shrinkage force use rigid components and feedback systems to keep the specimen height constant, in order to achieve “near zero” compliance levels. However, this leads to an overestimation of the stress, as tooth deformation and the relatively low elastic modulus of dentin represent a much less stiff situation overall.
Variations in test outcomes due to the system compliance are better understood if one considers that stress magnitude and distribution are defined by the stiffness of the bonding substrate and the whole testing framework in relation to the composite stiffness and shrinkage.
A universal test machine with a feedback system and a bonding substrate of high elastic modulus, such as steel ( E = 207 GPa) or glass ( E = 64 GPa), is considered a low compliance system . The use of a less rigid material, acrylic for example ( E = 3.2 GPa), characterize a high compliance system. It was observed that changing the bonding substrate from glass to acrylic increases the longitudinal compliance 15 times . Other high compliance systems described in the literature are the single cantilever device (“Bioman”) and the low compliance device . In both systems, the composite is inserted between a steel rod and a glass plate even though these are rigid substrates, the absence of a feedback system increases their compliance .
In a recent FEA study, when acrylic rods were used as the bonding substrate, higher stresses were associated with composites with highest shrinkage and lowest elastic modulus . On the other hand, when less compliant glass rods were used as the substrate, the highest stress levels were found with the association of high elastic modulus and high shrinkage. These findings corroborate those of other experimental studies comparing polymerization stress development of commercial composites tested in low compliance and high compliance systems .
Considering the influence of the testing system on polymerization stress results, it is important to verify to what extent data from different test configurations are comparable. To date, the available information is restricted to a few studies where one set up had its compliance level modulated by changing the bonding substrate or including a feedback system. For example, changing the substrate from glass ( E = 67 GPa) to acrylic rods ( E = 3.1 GPa) decreased the nominal stress values of a series of commercial composites by 34–68% . Moreover, the relative rankings were also affected by system compliance. The highest stress was developed by the stiffest composite with the lower compliance configuration, while in the high compliance set up, the stiffest composite ranked among the materials with the lowest stress. Another study comparing two similar set ups with different compliance levels defined by the use of a feedback system also reported lower values with high compliance systems, without substantial differences in rankings . In the only study found where two test systems with different frameworks were compared, the relative rankings of a series of materials also were similar .
Based on the above, the purpose of the present study was to compare four systems developed for composite polymerization stress testing: a set up mounted in a universal testing machine using either glass or acrylic rods as bonding substrate , the so called “low compliance” device , and a single cantilever device (“Bioman”). The null hypothesis was that for two series of composites, an experimental series composed of a similar resin formulation but different inorganic contents, and the second series constituted from commercial composites, the relationship between maximum nominal stress and elastic modulus or shrinkage is the same for all systems and, as a consequence, the four systems would rank the materials in a similar order.
2
Materials and methods
2.1
Material selection and formulation of experimental composites
Five commercial composites and five experimental composites with similar resin content and different filler levels were tested ( Table 1 ). The rationale for testing two series of composites was to verify if differences among materials would be more evident in materials with similar organic contents, where their shrinkage and elastic modulus were defined mostly by differences in filler fraction.
Composite (code) | Filler content wt% (vol%) | Filler size (μm) | Manufacturer | Batch |
---|---|---|---|---|
Filtek Z250 (FZ) | 82 (60) | 0.19–3.3 | 3M ESPE (St. Paul, MN, USA) | 8PF |
Tetric Ceram (TC) | 79 (60) | 0.04–3.0 | Ivoclar Vivadent (Schann, Liechtenstein) | D62694 |
Point 4 (PO) | 76 (57) | 0.4 | Kerr (Orange, CA, USA) | 206494 |
Filtek A110 (FA) | 56 (40) | 0.01–0.09 | 3M ESPE | 2AX |
Heliomolar (HM) | 76 (46) | 0.04–0.2 | Ivoclar Vivadent | G26494 |
E60 | 60 | 0.1–3.0 | N/A | N/A |
E65 | 65 | |||
E70 | 70 | |||
E75 | 75 | |||
E80 | 80 |
The experimental composites consisted of a matrix of BisGMA:TEGDMA (Esstech, Essington, PA, USA) in equimolar concentrations and 60, 65, 70, 75 or 80 wt% of silane-treated zirconia silica particles (0.1–3 μm, 3M ESPE). The photoinitiator system was composed of 2 mol% each of camphorquinone and 2-(dimethylamino)ethyl methacrylate (Sigma–Aldrich, Milwaukee, WI, USA). Experimental composites were mechanically mixed (SpeedMixer DAC 150 FVZ, Hauschild Engineering, Germany) for 2 min at 2400 rpm and kept refrigerated in dark containers until 1 h before testing. Commercial composites included two microfilled and three hybrid materials, which were chosen to represent a relatively wide range of elastic modulus and shrinkage values ( Table 1 ).
2.2
Specimen preparation
Experimental procedures were standardized among the different testing devices as much as possible. Specimen dimensions were defined as 5 mm diameter by 1 mm height. Photoactivation was conducted with the same light curing unit (VIP, Bisco Inc., Schaumburg, IL, USA). As the actual irradiance reaching the specimen, through the glass plate, or glass and acrylic rod, varied among the different testing systems, irradiation time had to be adjusted to result in a uniform radiant exposure of 12 J/cm 2 . Shrinkage force development was monitored for 10 min and maximum nominal stress was calculated by dividing the maximum load recorded by the cross-sectional area of the specimen. In each of the tests, five specimens were tested per experimental group.
2.3
Universal test machine
Glass or poly(methyl methacrylate) rods (radius, 2.5 mm; 13 or 28 mm in length) had one of their flat surfaces roughened with #180-grit sandpaper, treated with a silane agent (3M ESPE, St Paul, MN, USA) or methyl methacrylate (JET Acrílico Auto-polimerizante, Clássico Artigos Odontológicos, São Paulo, Brazil) (to glass and acrylic, respectively), coated with unfilled resin (Scotchbond Multipurpose Plus, 3M ESPE), and photoactivated with 12 J/cm 2 (500 mW/cm 2 × 24 s). In addition, the shorter rod had the opposite surface polished. The 28-mm rod was attached to the upper fixture, connected to the load cell of a universal testing machine (Instron 5565, Canton, MA, USA). At the lower fixture, the 13-mm rod was fixed to a stainless steel attachment with a slot allowing the positioning of the light guide in contact with its polished surface. The composite was inserted between the treated surfaces and photoactivated under 480 mW/cm 2 for 25 s. Specimen height was kept constant by the feedback from an extensometer (model 2630-101, Instron) at resolution of 0.1 μm ( Fig. 1 ).
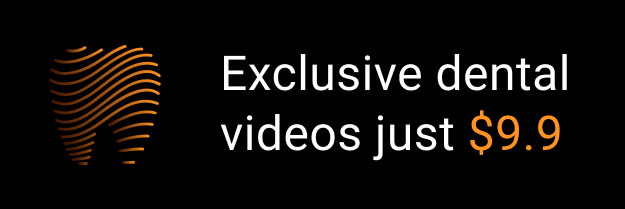