9
Hazardous Substances
Hazardous substances are used and generated in all dental settings. They include chemicals used for cleaning, dental restorative materials and those produced by human beings in the form of bodily fluids. These substances have the potential to cause ill health if not suitably and adequately controlled. The adverse effects on a person’s health may not be immediately recognised, but the consequences of injuries which do occur can be relatively major and long term. Controlling the use of hazardous substances is based on risk assessment where their use is analysed and appropriate control measures introduced. Legislation surrounding hazardous substances is both vast and complex. Therefore, it is the intention that this chapter will address those substances that come under the Control of Substances Hazardous to Health (COSHH) Regulations. Other substances listed in the scope as ‘additional substances’ will be given a brief overview as they are either not covered under COSHH or require specialist attention.
- Health and Safety at Work etc. Act 1974:
Employers have a general duty to ensure, so far as is reasonably possible, the safety and absence of risk to health in connection with the use, handling, storage and transport of substances.
- Control of Substances Hazardous to Health Regulations 2002:
Employers are required to assess the risks to health from exposure to hazardous substances by employees, the self-employed and others and so far as is reasonably practicable prevent or control exposure.
- Carriage of Dangerous Goods and Use of Transportable Pressure Equipment Regulations 2009:
Employers have a duty to provide a safe place of work where a pressure receptacle is being used, to ensure the equipment is in safe working order and to design and implement a safe system of work.
- Chemicals (Hazard Information and Packaging for Supply) Regulations 2002:
The supplier of the chemical must ensure that the chemical is safely packaged and properly labelled. He must also ensure that the recipient of the chemical gets the MSDS containing information to enable the user to store, use and dispose of the chemical safely.
- Control of Asbestos Regulations 2006:
Employers must protect their employees, other people on the premises and other people likely to be affected by the work, against exposure to asbestos.
- Control of Lead at Work Regulations 2002:
An employer must not carry out any work which is liable to expose an employee to lead until he has made a suitable and sufficient assessment of their health risks and the steps that need to be taken.
- Hazardous Waste Regulations 2005:
Producers of healthcare waste have a duty of care to ensure that waste is managed appropriately from the point of production to the point of disposal.
A hazardous substance is defined as any substance which is capable of causing an adverse effect on a person’s health. This includes chemical agents used, biological substances generated and any other substance which arises out of day-to-day activities. COSHH specifically defines hazardous substances as follows:
- Any chemical classified and labelled (orange square with a black symbol) under Chemicals (Hazard Information and Packaging for Supply) Regulations 2002 to include
- harmful or irritant – label is St Andrew’s cross;
- toxic or very toxic – label is skull and crossbones;
- corrosive – label is two horizontal dripping test tubes over a hand and workbench.
- Substances allocated a workplace exposure limit (WEL) as listed in the Health and Safety Executive (HSE) publication EH40, for example, nitrous oxide
- Substantial quantity of dust (may have relevance to dental laboratories)
- Biological agent, for example, bacteria and viruses
Workplace exposure limits (WELs) apply to substances that are airborne and therefore can be inhaled. The limit refers to the amount of substance in the atmosphere as a proportion of the amount of clean air. The lower the limit the more hazardous the substance. For example, a substance with a WEL of 1 ppm is more hazardous than one with 20 ppm. The limit stated in the regulations must not be exceeded. The WEL can be found on the material safety data sheet (MSDS) which the supplier is legally required to provide. A WEL does not apply to substances that can be ingested, injected or absorbed through the skin.
Anaesthetic gases which are used in dentistry include oxygen and nitrous oxide (N2O). N2O is a substance that has a WEL of 100 ppm as assigned by the HSE. The two main hazards associated with the gases as a substance, rather than with the equipment, are as follows:
- Gas escaping from leaking valves
- Exhaled gas in the atmosphere
The use of anaesthetic gases must be managed in order to reduce the risk of exposure to dental personnel and anyone else who may be affected. Risks should be controlled by the following means:
- Use the minimum effective dose of N2O on all occasions.
- Use an effective gas scavenging unit to trap waste gases and disperse them into the outside atmosphere.
- Ensure sufficient ventilation. For example,
- General ventilation, for example, open windows or doors to assist dilution of gases
- Local ventilation, for example, an extractor fan placed low on the wall or floor or air vents
- Use different size face masks to ensure they fit each patient.
- Train staff on the risks associated with the use of gases and the safety of cylinders.
- Monitor airborne concentrations of waste gas by sampling and measuring.
- Discourage patients from talking to reduce the amount of exhaled gas.
- Switch off machine when not in use.
- Prevent cylinders from falling over such that valves cannot be damaged.
- Check equipment prior to use to ensure equipment is not leaking.
- Reduce the need to lift and move cylinders to prevent damage from dropping.
Cylinders must be removed from the practice by a licensed company as this ensures safe transport and disposal to prevent inadvertent release into the environment.
Dental staff are exposed to biological agents as part of their everyday working life. The risk of exposure is incidental as it arises from the work undertaken. Risks from these agents must be controlled in order to prevent the transmission of infection. Chapter 10 specifically addresses the requirements laid down under the Health Technical Memorandum of the Department of Health (DOH HTM) guidance. Biological agents are classified as types and listed as four hazard groups. This is an approved list made under the Health and Safety at Work etc. Act 1974 and COSHH Regulations which impose requirements on employers to control risks. The four classifications and groups are as follows (Source: HSE):
- Classification
- Bacteria
- Viruses
- Parasites
- Fungi
- Hazard Group 1 – This group is unlikely to cause human disease.
- Hazard Group 2 – This group can cause human disease and may be a hazard to employees but is unlikely to spread to the community and there is usually an effective prophylaxis or treatment available.
- Example – herpes virus varicella zoster, influenza type A, B and C and Clostridium botulinum (Botox)
- Hazard Group 3 – This group can cause severe human disease and may be a serious hazard to employees. It may spread to the community, but there is usually an effective prophylaxis or treatment available.
- Example – hepatitis B, C and D and tuberculosis
- Hazard Group 4 – This group causes severe human disease and is a serious hazard to employees. It is likely to spread to the community and there is usually no effective prophylaxis or treatment available.
Hazard Group Control
Each hazard group requires the agent to be contained in the first instance and additional precautions introduced. However, in certain circumstances ‘strict’ containment measures may not apply because of the nature of the work or the nature of the biological agent. Risk assessments of work activities will assist in determining what level of control or containment is required to prevent the risk of transmission. Containment and control measures are discussed in COSHH assessment Steps 3 to 7 below. In particular, an immunisation programme must be implemented for all dental personnel.
Botox
A number of dental practices are providing non-surgical cosmetic treatment; one particular treatment is the use of Botox to smooth frown lines and wrinkles. Botox is the trade name for Botulinum toxin Type A which is derived from the bacteria C. botulinum. Botox must be managed in the same way as any other hazardous substance.
COSHH requires all chemical substances to be used, handled, stored, disposed of and transported safely and without risk to a person’s health. This applies to all substances that are classified and labelled as stated in the ‘Definition’ section earlier. Some chemicals used in dental practices have been assigned a ‘risk phrase’ which appears in the MSDS. Risk phrase refers to how the chemical reacts when exposed to certain conditions or special risks which the chemical presents. Chemicals of particular relevance to women of child-bearing age and new and expectant mothers are as follows:
- R40 – may provide limited evidence of a carcinogenic effect.
- R45 – may cause cancer.
- R46 – may cause heritable genetic damage.
- R61 – may cause harm to the unborn child.
- R63 – may cause possible risk of harm to the unborn child.
- R64 – may cause harm to breastfed babies.
An example of a chemical with a risk phrase is eugenol. Risk phrases assigned to this substance are 22–36/37/38–42/43.
In addition to ‘risk phrases’, chemicals will contain a ‘safety phrase’ which provides advice and describes the measures that must be taken in order to control exposure. For example, eugenol contains safety phrases: S26–S36.
It is important to obtain the MSDS from the supplier when carrying out a COSHH assessment to ensure that any special requirements are identified and controls implemented.
Amalgam
Where mercury is used, an assessment must be undertaken to determine the level of exposure and associated risks. The assessment should take into consideration the preparation of amalgam (e.g. mercury and alloy mixed or capsules); the environmental contamination; storage of mercury; waste amalgam and spent capsules and any special considerations for certain people such as expectant mothers and those with an allergy to mercury. Suitable control measures should then be determined as identified by the assessment (see COSHH assessment Steps 3 to 7 below). Amalgam waste should be stored in the regulated container under a mercury suppressant solution.
Amalgam Separators
Amalgam separators should be fitted in all practices that use amalgam in order to meet the requirements of the Hazardous Waste Regulations. The practice needs to consider how many separators are required and where they should be placed. This will depend on the size and layout of the practice. According to Department for Environment Food and Rural Affairs (DEFRA), ‘amalgam separators will need to be placed in such a way to protect all routes by which amalgam enters the drains’. Information from suppliers will assist in selecting the most suitable type of separator, where and how to install it and how to ensure it conforms to the British Standard.
Amalgam and mercury must be segregated and packaged in line with the regulations and consigned as hazardous waste. Amalgam has risk phrases of R23 (toxic by inhalation) and R33 (danger of cumulative effects) and safety phrases S (1/2), S7, S45, S60 and S61.
The risk associated with hazardous substances must be assessed and reduced to a level which is as low as reasonably practicable. A COSHH assessment is more than collecting data and filling in forms. It should clearly show that everyday activities have been assessed and suitable and sufficient control measures implemented. Before undertaking the assessment the following should be considered:
- Substances used during normal work activities, for example, dental amalgam
- Substances that arise out of normal work activities, for example, blood and saliva
- Information that may be needed to assist the assessment
- How the work areas and activities should be broken down
- Those people who may be more vulnerable because of individual circumstances or needs (see Chapter 3)
You should maintain an ‘Approved Substance List’ for all manufactured substances to assist with identification of substances and to facilitate review. The list should be updated accordingly and indicate substances that have been taken out of use (Figure 9.1).
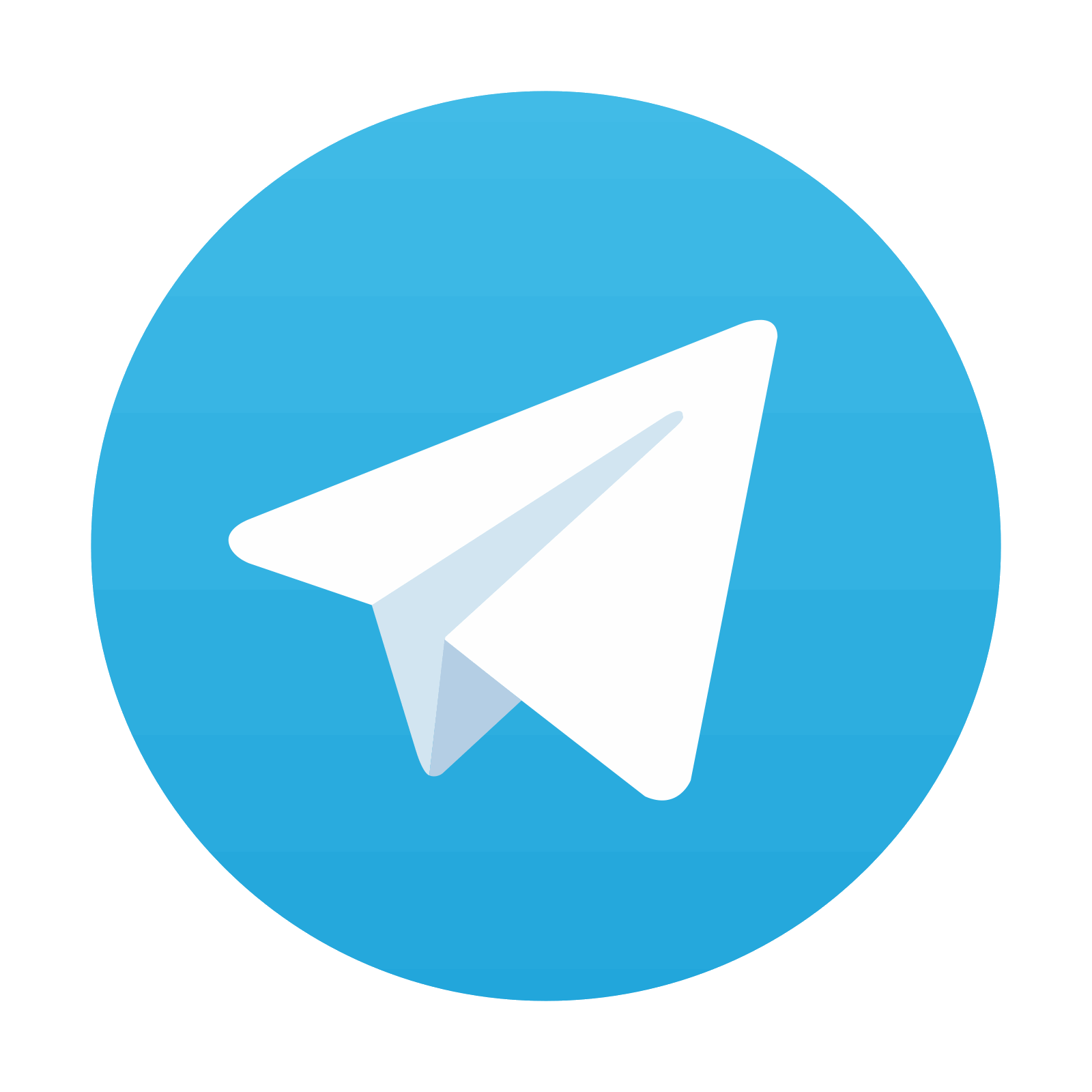
Stay updated, free dental videos. Join our Telegram channel

VIDEdental - Online dental courses
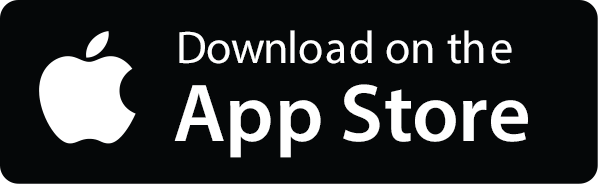
