22
Work Equipment
Work equipment is found in every dental practice and includes any machinery, appliance, apparatus, tool, installation, instrument and any assembly that is used by people to carry out their work. Work equipment can present risks to users, if not used correctly or maintained in safe working order. The nature and significance of the risk associated with this equipment depends on the following factors:
- The type of activity/task undertaken
- The type of equipment used
- The purpose of the equipment
- The number of people involved in the activity/task
- The competence of staff
This chapter provides general and specific legislative and good practice requirements in order to facilitate compliance. The general principles of safety can be applied to all equipment used in dental practices, although some equipment requires specific arrangements to be in place. Regardless of the type of equipment used general safety measures must be applied in all cases. The measures apply to new and second-hand equipment purchased and equipment hired or leased for use at work.
- Health and Safety at Work etc. Act 1974:
Employers have a duty to ensure, so far as is reasonably practicable, the provision and maintenance of plant and equipment that is safe and without risks to health.
- Provision and Use of Work Equipment Regulations 1998 (PUWER):
Employers are required to provide and maintain safe equipment and safe working procedures to ensure that work is carried out safely.
- Management of Health and Safety at Work Regulations 1999:
Employers must assess the risks to employees’ health and safety from the use of work equipment. Eliminate the risks where reasonable or reduce to an acceptable level. Employees must use work equipment as trained and instructed to ensure its safe use.
- Electricity at Work Regulations 1989:
Employers must ensure that all electrical systems, including high voltage to battery-operated equipment, is constructed and maintained to prevent the risk of injury arising out of work activities.
- Pressure Safety Systems Regulations 2000:
Employers are required to ensure that pressure vessels are used in line with safe operating limits and pressure and temperature requirements and there is a written scheme of examination in place.
- Medical Devices Regulations 2002 (as amended):
Employers are required to have a system in place to manage the purchase, use and maintenance of medical devices to ensure that all risks, so far as is reasonable, are reduced.
- Lifting Operations and Lifting Equipment Regulations 1998 (LOLER):
Employers must ensure that lifting equipment is of adequate strength and stability for the load that is to be lifted, in particular equipment used for lifting persons must consider the operator and the person being carried.
- Carriage of Dangerous Goods and Use of Transportable Pressure Equipment Regulations 2009:
Employers have a duty to provide a safe place of work where a pressure receptacle is being used, to ensure the equipment is in safe working order and to design and implement a safe system of work.
- Personal Protective Equipment at Work Regulations 1992 (as amended 2002):
Employers are required to select, provide and maintain suitable PPE and to ensure appropriate use, where risks cannot be adequately controlled by any other means.
In dentistry, the range of equipment is vast; however, it can be consolidated into two groups, namely equipment and instruments. Equipment is fixed or portable and manually or power operated. Examples of both groups appear below:
- Decontamination equipment
- Dental chair, unit and light
- Disposables
- Gas cylinders
- Hand-held dental instruments
- Office equipment
- Portable electrical appliances
- Pressure vessels
- Radiography equipment
- Rotary or air-driven instruments
- Suction units
The above is not an exhaustive list as it is impractical to list everything. However, the requirements of the Provision and Use of Work Equipment Regulations and other associated legislation must be applied to everything that comes under the definition of work equipment.
Hazards Associated with Work Equipment
An appreciation of the hazards presented by work equipment is important in order to effectively implement the safety precautions. The hazards range from relatively minor consequences to more serious and, in some cases, potentially fatal ones. The following list provides an overview of the more generic hazards:
- Electric shock
- Fire
- Faulty design or installation
- Entanglement with moving parts
- Entrapment from equipment falling over
- Impact from the release of particles ejecting
- Biological, chemical or radioactive contamination
- Noise or vibration
- Dusts, vapours or fumes
- Burns or scalds from contact with heating systems
- Transmission of infectious disease through sharps
- Upper limb disorder from poor posture
- Uncontrollable release of stored energy under pressure resulting in explosion
Everyone is exposed to the above hazards; therefore, the safety of users, operators, others in the immediate vicinity and the outcome of instrument malfunction or failure which may adversely affect patient care must be addressed.
As you will see from the ‘legislation’ section in this chapter there is a wide range of regulations which apply to work equipment and some will overlap. In order to prevent repetition and unnecessary duplication of information, this section will address general safety requirements as contained in PUWER. Safety must be considered in three stages.
1. Purchasing (New or Second Hand) or Leasing or Hiring
- Review existing risk assessments to identify any additional risks that new equipment may present.
- Revise existing risk assessment or undertake a new one.
- Consider design, intended use and suitability of positioning/location.
- Consider any environmental contamination from the equipment and means of ventilation.
- Obtain information from manufacturers and suppliers on design safety features.
- Check whether equipment is manufactured to the European standard and displays the CE mark and whether an EC declaration of conformity certificate is issued (if required) or
- If manufactured prior to 1995, it is safe for use.
- Safe operating information and instruction manual is provided.
- Confirm that manufacturer or supplier maintenance and testing schedules will be undertaken as and when required.
- Consider competencies of those using equipment and identify training needs.
- Ensure that equipment is safe and suitable for its purpose.
2. Using
- Prior to an employee using new or existing equipment, a risk assessment should be undertaken as follows:
- Identify hazards – look at the activity which involves the use of the equipment and identify any hazards that may be present (use the previous section for a range of hazards).
- Evaluate the risks – determine who is exposed to the equipment and therefore could be harmed, how the harm may arise, for example, steam emits from autoclave when door is opened. Identify how the risks are currently being controlled and are they sufficient and then determine the overall severity of the risk.
- Implement additional controls – if additional controls are required the hierarchy approach should be adopted (see Chapter 19). Control measures should address the equipment, working practices and competence of users. An example is provided in relation to X-ray processing equipment.
- Manual 3-tank X-ray processing equipment
- Substitute the equipment for an automatic processor.
- Ensure equipment is used in well-ventilated area, is turned off when not in use and inspected and tested annually.
- Provide training on safe use and routine maintenance of equipment.
- Monitor control measures – periodically check that the additional control measures are effective and reduce risks; revise controls if necessary.
- Re/>
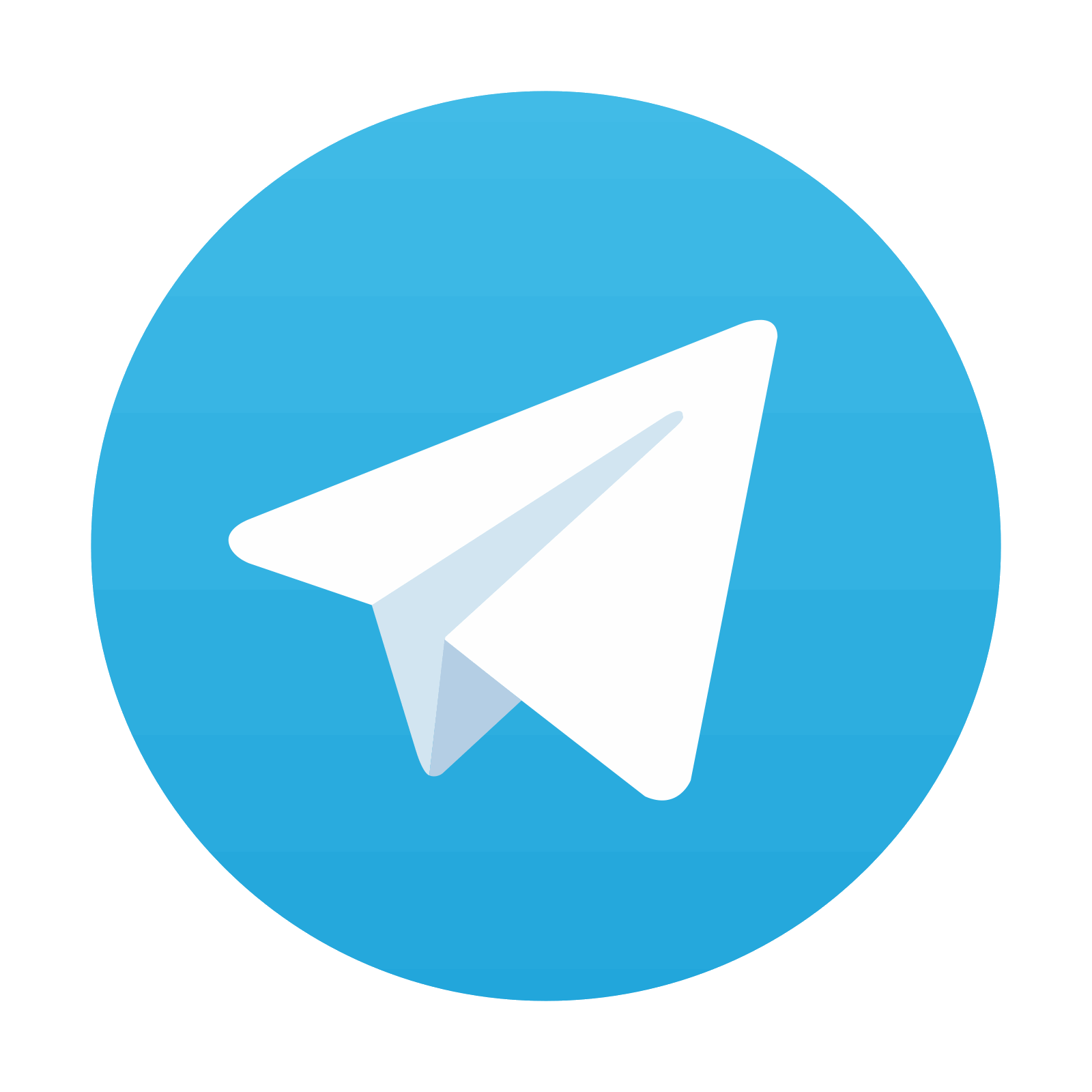
Stay updated, free dental videos. Join our Telegram channel

VIDEdental - Online dental courses
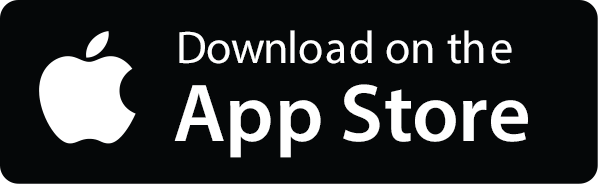
