Soldering and Welding
Since it is not always possible to create a metal device in one piece, such as by casting, it is necessary to assemble it from separately prepared parts. In dentistry, the fabrication techniques used are then either soldering or welding. These approaches are used most often in the context of orthodontic appliances, where wires and bands may need to be joined.
Soldering is distinguished from welding by the use of a third body, the solder, between the two workpieces, but without melting either of them. The conditions for effective joins of these types are discussed.
Unfortunately, metals may oxidize sufficiently to interfere with wetting by the solder, whether this is because the metal is prone to corrosion or naturally-coated by a passivating oxide layer. The use of fluxes is therefore necessary to obtain a good joint. The chemistry of these is discussed, and the means of limiting their influence.
The main features of solder design are outlined, especially from the point of view of selection of the correct grade for the task in hand. Factors to be considered include melting point and toxicity.
Soldering and welding almost inevitably are detrimental to some aspect of the device being fabricated, such as hardness, strength and corrosion resistance. However, by recognizing the problems related to the structure and behaviour of the workpiece materials, it is possible to make appropriate compromises and to limit the damage in order to obtain functional appliances.
Although casting provides a means of making complicated shapes in metals and other materials, there remain types of device where this is insufficient. For example, if alloys with differing properties, such as due to differing amounts of annealing or work hardening, are required to function in different parts of a device then because casting cannot give that variation, some joining method is essential. This is clearly so when alloys with differing compositions are involved. Examples of this include the assembly of orthodontic appliances from stainless steel wires and bands, assembly of bridges, and the fixing of precision attachments to cast devices. In addition, on occasions it may be necessary to repair a fractured device, although this is usually not a satisfactory permanent solution. Although the use of rivets or nuts and bolts may be appropriate fabrication techniques in many circumstances, for intra-oral use there will be severe disadvantages or impracticalities. Thus, there is usually little metal present in which to drill a hole, and this would cause a weakening of the object, even if there were space and soft tissue trauma could be avoided, which is unlikely. The risk of corrosion is also increased with the numerous crevices which are thereby created. The use of adhesives, epoxy resin and the like, is precluded because of relatively low strength, small interfacial area, and poor fatigue-resistance under wet, oral conditions. What are left, then, are soldering and welding as the only generally viable techniques.
§1. Definitions and Conditions
•1.1 Welding
Welding is the joining of two bodies brought into contact by almost any other means than soldering. For example, two perfectly clean gold surfaces (or, indeed, many other metals) placed in vacuum where the adsorbed gases and water may evaporate (perhaps helped by warming), and then placed in contact, will weld together instantly (28§4). The driving force for this is, of course, the reduction in total surface energy by the reduction of the free surface area but it is effected by the diffusion of atoms at the interface. This phenomenon is employed, with the aid of pressure, in the condensation of a direct gold restoration, when a vacuum is not necessary but it is still contingent on the lack of contamination of the surface of the gold. The term welding is usually taken to apply to metals, but it can also be used in the context of some polymers (a polyethylene bag has at least one seam welded), and even some ceramics. In addition, so-called solvent welding may be applied to some polymers: the surfaces to be mated are softened with a solvent and pressed together. When the solvent has evaporated, the entangled chains hold the workpieces together. However, what follows will be restricted to the context of metals.
Industrially, welding often means the melting of the parent metal of both bodies into a weld pool, with or without the addition of ‘filler’ metal (not to be confused with the filler of composite materials), which then freezes to obtain the union. As this technique is of relatively low precision, and the amount of heat required is large, it is better suited to large workpieces, and in fact because of this finds no place as such in dentistry. But welding can be achieved by any means that permits the close approximation of the surfaces to be joined, and this usually entails the use of pressure. Spot–welding does just that: while the workpieces are squeezed together by a pair of electrodes an electric current is passed through them to heat resistively the area to be welded. As the strength of the material decreases as its melting point is approached, the workpieces are plastically deformed between the electrodes, bringing them into close contact over the area of the ‘spot’, and allowing the weld to develop, aided by the rapid diffusion that can then occur. While a small amount of localized melting often occurs, it is not in fact necessary for effective union of the parts. Indeed, it is recommended that melting be avoided, since the low viscosity of the melt means that it will be squeezed or run out of place, reducing the amount of metal at the crucial site. Similarly, too much pressure applied by the electrodes can result in an unacceptable thinning of the workpieces, or even a hole being punched, which thus weakens the structure and fails to achieve an effective weld.
In spot welding the amount of energy delivered is given by the usual electrical relationship:
< ?xml:namespace prefix = "mml" ns = "http://www.w3.org/1998/Math/MathML" />
where R is the resistance of the workpiece. The temperature actually attained depends on the bulk of the metal present, its thermal conductivity and its heat capacity. Thus, because resistance will vary depending on area of contact, surface roughness, oxide coats, and alloy composition, for any particular job the current and its duration as well as the pressure applied must be carefully chosen. Too much energy and metal will melt; too much pressure and a hole could be punched in the workpiece. Different conditions are therefore required for different alloys and different thicknesses.
As has been mentioned before (21§2.5), the heating cycle is crucial to the maintenance or alteration of the mechanical properties and corrosion resistance of stainless steel fabrications, and this puts further constraints on the welding conditions chosen, i.e. to minimize the duration of the heating cycle, the temperature attained, and the volume of metal affected. It is, however, impossible to avoid at least some change.
•1.2 Soldering
This is the joining of two metallic items by an alloy which melts fully, i.e. has a liquidus at a lower temperature than the solidus of either of the pieces to be joined. This is a necessary condition when it is required that the integrity of the pieces to be joined be preserved.
Soldering thus sets out to achieve the same mechanical effect as welding, i.e. the union of two workpieces (which may or may not be of the same alloy), but it does this by the interpolation of a third body – the solder – which is joined to both workpieces. Apart from the basic requirement of a lower melting point, it is evident that the solder alloy must be capable of wetting the parent alloy(s); that is, it may be said to be compatible with them. This certainly means that chemical similarity has a bearing on the matter, but more that there is the potential ability (not necessarily realized) to form an alloy with the substrate metals.
Similar factors as were discussed under casting become of relevance here also. The surface tension of the molten solder and the interfacial tension between the solder and substrate clearly dominate the wetting of the latter and the attainment of good adhesion by close atomic approach. Similarly, the surface tension and the wetting control the ability of the solder to run into small spaces by capillary action, although again the penetration coefficient (dependent on viscosity, meaning that it takes time) (10§2.4) may be a more relevant figure of merit. The filling of crevices is important from at least two points of view: mechanical strength by reduction of the size of Griffith flaws; and avoidance of crevice corrosion – which would reduce strength still further.
The flow of the solder is clearly a crucial factor and the role of surface roughness must be considered. The advance of the liquid front through a rough-surface gap is unlikely to be uniform (cf. 10§2.9), especially when the gap cannot in general be controlled to be of constant width, and the trapping of bubbles is a common observation. Poor technique, applying solder at several locations in succession, and without providing enough to fill the gap unidirectionally, is more likely to trap large bubbles. Subsequent grinding or polishing may reveal these, and they will act both as surface flaws (stress concentration) and as crevices for initiating corrosion promptly; stress corrosion will be likely.
All of this also depends on the cleanliness of the substrate metal. Oxides, sulphides and many other possible contaminants cannot be wetted by solders (cf. mercury and amalgam alloys; casting alloys and investments). It is essential therefore to ensure that both surfaces to be soldered (or welded, for that matter) are scrupulously clean, initially by degreasing and then abrasion or filing. Even so, surface oxidation may be so rapid when the workpieces are heated as still to preclude effective wetting or wetting over a sufficient area. This is where fluxes come in.
§2 Fluxes
The word flux means flow, and in the present context means flow of the molten solder being achieved by allowing or facilitating the wetting of the substrate. The function of fluxes therefore is twofold:
(1) to remove any oxides or other compounds present on the surface, and
(2) to prevent further oxidation by excluding oxygen from the site, purely as a physical barrier.
In general it is not possible to reduce oxides to metal at low temperatures because the oxides are thermodynamically so very stable. Another chemical approach must be taken, which is to dissolve the oxide. Formerly, in workshop contexts, this was done by using a solution of hydrochloric acid or similarly acid substance. This, however, did not provide any protective action.
Boron now provides the basis of many commercial fluxes and the constituents for ‘home-made’ recipes in the form of borax or sodium tetraborate, Na2B4O7.10H2O, and boric acid, B(OH)3. This latter compound dehydrates readily:
The melting point of metaboric acid, HBO2, is 236 °C, while that of B2O3 is 450 °C. Borax also dehydrates in several stages:
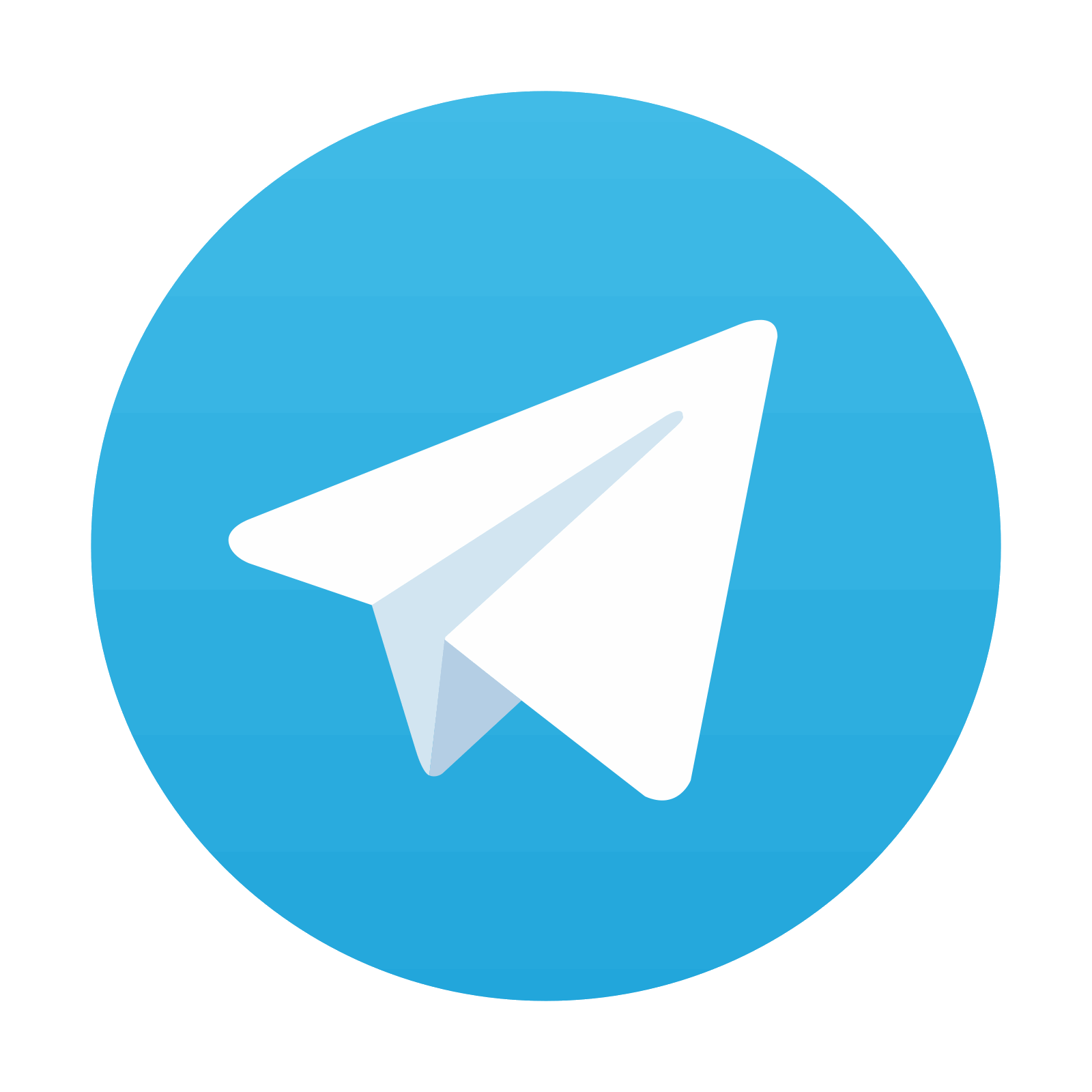
Stay updated, free dental videos. Join our Telegram channel

VIDEdental - Online dental courses
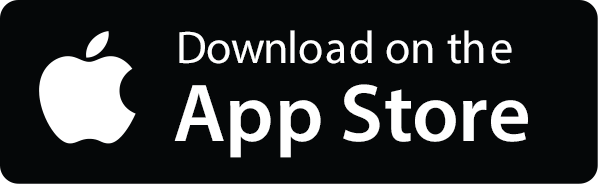
