Steel and Cermet
Steel is the single most important engineering alloy, not least because the iron which forms its basis is cheap. The general lack of corrosion resistance, however, precludes applications in dentistry in both the oral environment and where sterilization is necessary, as in hand instruments. Consequently, stainless steel is the alloy of choice.
The mechanical properties of steel depend on crystal structure, and especially as this is modified by the presence of carbon – which defines the alloy as steel. Control of the amount, distribution and form of the carbon is critical, and this is effected through combinations of thermal and deformation history. Equally, further thermal treatment and deformation can change those properties; such changes may be detrimental to the service behaviour of the material.
Stainless steel belongs to the passive group of corrosion resistant alloys, relying on the presence of a thin coating of chromic oxide to isolate it from the environment. The formation and maintenance of this oxide coat is a function of composition; heat treatment may spoil it. The mechanical properties have to be adjusted by adding other alloying elements to offset the effects of including the chromium.
The proper care of stainless steel, and its application in dentistry, depends on a recognition of the factors that effect its structure. A basic understanding of its metallurgy is therefore necessary.
Cermets are a class of materials that utilize the extreme hardness of carbides for cutting tools such as enamel chisels and burs for use on cobalt-chromium alloys. The difficulties of fabrication in manufacture, and the extreme brittleness in service, are overcome by using a matrix of metallic cobalt. Understanding the structure of these materials permits their effective use without damage.
Steel in several forms is used in the fabrication of many dental instruments: burs, scalpel blades, probes, and so on. As wires and bands, stainless steel finds applications in orthodontics and as matrices in restorative dentistry, and as small-bore tubing for injection needles. Other steels will probably form a number of parts of handpieces, retention pins, and such items as rubber dam clamps.
The topic of steel is of vast scope, forming the basis as it does of one of the world’s major industries and having applications in nearly all possible fields. Its low cost, strength, ease of fabrication and general durability are the basis of this. The diversity of application arises from an equally diverse range of properties, depending on the particular treatment and composition. It is not proposed to deal with steel-making or its development in any detail, and we cannot help but oversimplify the subject in trying to extract some basic principles whereby the main ideas may be understood. Nevertheless, these ideas will serve to point out the applications – and the limitations – of steel in dentistry.
§1 Carbon Steel
Pure iron is a soft and malleable metal that has little structural use. A simple steel, consisting of iron and a small amount of carbon, is harder, tougher and stronger. The importance of the carbon arises firstly from the fact that it is a small enough atom that it can form interstitial solid solutions (19§2.3). The sensitivity of the properties of steel to the dissolved carbon is very great, as with the Co-Cr alloys. Even so, the diversity of steels is due to not just this possibility but is also related to the dimorphism of iron, that is, it exists in two distinct crystal forms. Pure Fe at low temperatures has a body-centred cubic (b.c.c., 11§3.4) structure. This converts to face-centred (f.c.c.) on heating to 906 °C, and then back again to b.c.c. at 1401 °C. This last structure then persists up to the melting point of ~ 1535 °C.
While the maximum radius ratio of an assumed hard, spherical atom that can be fitted into an f.c.c. lattice is ~ 0.41 in an ‘octahedral’ hole, in a b.c.c. lattice without distorting it is rather smaller at ~ 0.29 (Table 1.1; Fig. 19§2.3). For carbon and iron the radius ratio is actually ~ 0.60 so some considerable distortion of the iron lattice is expected if it contains any carbon at all. Indeed, C in b.c.c. Fe results in severe tetragonal distortion. This distortion is mainly the cause of the hardening effect (cf. δ-AuCu, 19§1.3). It follows from this that the solubility of carbon in iron is expected to be limited. Further, the solubility is expected to be much less in the case of b.c.c. iron than in f.c.c. If, then, there are to be structural transformations, the fate of the carbon must be identified.
Table 1.1
Relative sizes of interstitial holes in the common metal structures.
hole type: | octahedral | tetrahedral |
b.c.c | 0.155 | 0.291 |
f.c.c., h.c.p. | 0.414 | 0.225 |
Part of the C-Fe constitutional diagram is shown in Fig. 1.1,[1] and the processes involved can be traced here as with other alloys (Chap. 12). Note that because the molar mass of carbon (12) is much smaller than that of iron (56), a small mass proportion (lower scale) in fact corresponds to a large atomic proportion (upper scale) by very roughly a factor of four. For structural matters, we should of course think in terms of atomic proportions. For example, at 1A7 mass% C the proportion C : Fe is 1 : 12, or 1 C atom per 3 unit cells (11§3.3) – a rather easier concept. However, in common with the usual practice, all compositions given here will be in mass percent.
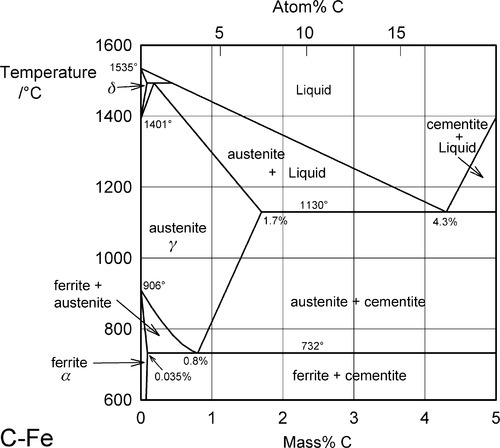
Steel has had a long history, and many special names have been introduced in the literature associated with various kinds of structure and composition. These names are frequently used as a kind of shorthand to refer to these forms. Thus, ferrite is the name given to the solid solution of C in b.c.c. Fe (also known as α-iron); this has a maximum solubility of about 0.035% at 732 °C (Fig. 1.1) (i.e. C : Fe = 1 : 612!). Austenite, on the other hand, C in f.c.c. Fe (γ-iron), shows a much greater maximum solubility of ~ 1.7% at 1130 °C (C : Fe = 1 : 13); this phase is only stable at high temperatures.
•1.1 Cementite
One other aspect of the system is of great importance: Fe forms a carbide, Fe3C, called cementite, which corresponds to 6.7% C. Because of the formation of this compound, interest in the C-Fe phase diagram is restricted to the Fe-rich end. However, cementite is in fact only metastable, the true equilibrium is between iron and graphite. This means that while cementite is a persistent species, this is for kinetic reasons (the decomposition to Fe and graphite is very slow). It is therefore not actually a thermodynamically equilibrium phase in the C-Fe system. Ordinarily, constitutional diagrams show only stable phases, that is, they are equilibrium diagrams. Although graphite occurs extensively in cast irons (2 ~ 4 mass% C), it is usually difficult to obtain this equilibrium phase in steels (0.03 ~ 1.5 mass% C). Thus, the relative stability of cementite is such that it is an important constituent of many iron products and so must be taken into account, being relevant to most steels in practice (recall that dental amalgam does not attain thermodynamic equilibrium, and its working constitutional diagrams too are non-equilibrium; 14§1). This is another example of the working compromise between kinetics and thermodynamics.
In the process of smelting iron from its oxide ores with coke there is a naturally a great excess of carbon present. Up to 4.3% of that C will dissolve in the molten Fe, corresponding to the composition of the eutectic of Fe and Fe3C: this liquid freezes at 1130 °C (Fig. 1.1):
< ?xml:namespace prefix = "mml" ns = "http://www.w3.org/1998/Math/MathML" />
That is, the eutectic solid is austenite + cementite. Ordinary ‘pig-iron’, that is, cast from the original melt, has about that composition. If pig-iron is processed to remove all but the last traces of impurities, including C, the result is ‘wrought iron’, essentially pure Fe. Now carbon steels in practice may contain up to about 1.5% C, although ‘mild’ steel contains from only ~ 0.1% to 0.5% C. Thus either the addition or removal of carbon is involved in steel production, depending on whether wrought iron or pig-iron is (or is considered to be) the starting stock. This adjustment of composition is one of the critical factors determining the properties of the steel.
The presence of the carbide, cementite, is responsible for further hardening, depending on grain size and distribution as before (cf. Fig. 19§2.4), by inhibiting dislocation movement.
1.2 Austenite
Austenite (f.c.c.) is a simple interstitial solid solution in which the C atoms are randomly arranged throughout the available octahedral holes (of which there is one per Fe atom), there being insufficient C for a regular structure. The solubility of C in austenite drops steadily from ~ 1.7% at 1130 °C to ~ 0.8% at 732 °C. Thus, when austenite containing more than ~ 0.8% C (the eutectoid composition, C : Fe = 1 : 27, 1 C atom per 6.75 unit cells) is cooled slowly the first reaction to occur is the separation of cementite at grain boundaries, to give a two-phase structure. Below 732 °C the remaining austenite is no longer stable and decomposes into the eutectoid mixture of ferrite + cementite:
This mixture is called pearlite because of the fine-grained banded or lamellar structure which gives a pearly lustre in polished sections (this is due to differential erosion during polishing, 20§4, and the resulting effective formation of a diffraction grating-like surface). However, because it is mostly nearly pure Fe, pearlite overall is in fact not very hard. But because of the lamellar structure dislocations cannot travel very far in the ferrite and cracks would be deviated by the cementite. Hence, this material is nevertheless quite tough and fairly strong. It is important to note that pearlite is not a phase but a two-phase mixture, i.e. it is itself a composite.
•1.3 Martensite
If, instead of slow cooling, the austenite is quenched (cooled very rapidly, at 200 K/s or more) say by dropping into water), the transformation from f.c.c. to b.c.c. still occurs, but the decomposition into ferrite + cementite cannot happen because the necessary diffusion is inhibited by the lack of activation energy and lack of time. The f.c.c. structure is nevertheless too unstable to exist – there would be too much strain – so the structure distorts nearly instantaneously in a non-diffusive, displacive fashion into b.c.c. This kind of transformation has zero activation energy and therefore called athermal. It results, therefore, in a supersaturated solution of C in b.c.c. iron; this is called martensite (actually it is distorted enough that it is better called body-centred tetragonal when there is carbon present in the cell). This material is extremely hard and brittle because of the great strain in the lattice, but also because there are no close-packed planes in the structure slip is difficult (see Fig. 11§5.3). It is therefore of limited use as it stands. Note, however, that since the maximum solubility of C in austenite is about C : Fe = 1 : 13 atoms, on transformation this corresponds to 1 C per 6.5 or so b.c.c. unit cells. The strain is therefore rather localized, but severe, being essentially between the unit cells that are with and without a carbon atom.
On such rapid cooling, the transformation is triggered on reaching what is called the martensitic start temperature, Ms (about 550 °C), when the strain becomes to great to sustain (that is, prior to that, the system is metastable). This transformation is described as military or concerted because of the systematic nature of the wave of distortion which travels at about half the speed of sound (i.e. of an elastic wave) in the material. That is, there is a one-toone correspondence of the lattice positions in the two structures (Fig. 1.2). Note that because the transformation is purely displacive, the two lattices are coherent (cf. 11§6.1). The transformation continues progressively on further cooling and ceases at the martensitic finish temperature, Mf (about 350 °C for plain carbon steel), although there is usually some small amount of untransformed austenite which remains. The displacive nature of the transformation also means that it is completely reversible: reheating will return the original austenite, with all atoms in the exactly the same place (assuming that no time for diffusion is allowed).
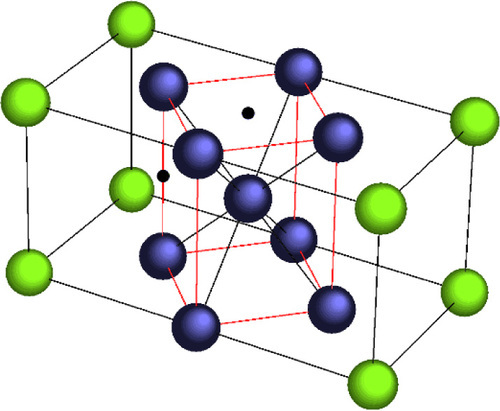
A further factor contributing to the strain of the system is that there is an associated transformation expansion. The specific volume of b.c.c. Fe is about 9% greater than that of f.c.c., and this expansion has to be accommodated in the parent matrix of the transforming grain. It arises because, as can be seen in Fig. 1.2, the c-axis (vertical) of the soon-to-be b.c.c. unit cell needs to shrink and the a– and b-axes need correspondingly to expand to make the cell cubic rather than tetragonal. Thus there is a coherency strain between the transformed and untransformed regions in the grain (cf. 19§1.4). The presence of an interstitial carbon atom makes this worse. (Notice that although the b.c.c. lattice lies at 45° to that of the f.c.c., crystallographic axes are an artificial scheme of classificatory convenience – our point of view; no physical rotation is involved in this case.)
•1.4 Tempering
The process of tempering, by which steels with more useful properties are made, involves the carefullycontrolled reheating of martensite to 200 ~ 300 °C. As the transformation to ferrite + cementite is relatively slow (i.e. diffusion limited), the duration of reheating and the temperature may be used accurately to control the amount of conversion. The newly converted eutectoid material is much coarser than pearlite and is known as bainite. The presence of the mixture bainite + martensite greatly increases the toughness of the steel (hard core, ductile matrix). Steel in general, then, has a composite structure, primarily because carbide is present (as in Co-Cr alloys). However, if the idea is continued, all alloys with more than one phase are also composite.
If the original austenite contained less than 0.80% C (that is, the eutectoid composition), ferrite is the first phase to separate as crystals on slow cooling, but now in the form of dendrites within the austenite grains (cf. the Widmanstätten structure in amalgam alloys, 14§3). The remaining austenite later (below 732 °C) converts to pearlite as before, and this remains surrounding the ferrite dendrites; the structure is therefore characteristic of such hypoeutectoid compositions. Conversely, hypereutectoid compositions are those with more than 0.80% C and up to 1.7% C. These terms are sometimes used to describe the alloys as they indicate the amount of carbon present in relation to the eutectoid composition, but they cannot be used to accurately deduce structure (and therefore properties) except in a very limited sense. This is because the extent of the various transformations depends on the rate of cooling and subsequent treatment in terms of time and temperature, i.e. the thermal history. In general terms, the transformations that are possible are summarized in Fig. 1.3.
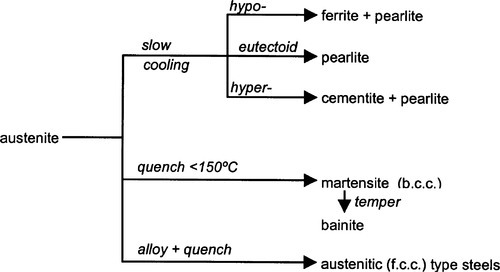
•1.5 Properties
There are many other details and complications to the science of steel and steel-making into which there is no need to go here. However, it is critically important to recognize that because all such transformations are time and temperature dependent, any subsequent heat treatment may be expected to modify, or even totally destroy, the properties for which the steel had been chosen and prepared. In particular, the hardness of the martensitic structure will be lost, and extremely soft metal will result from overheating. Wax knives, for example, should not be overheated if they are to remain useful. The flexibility of steel instruments such as endodontic files and reamers will be lost if they are exposed to too high a temperature, and the associated softening means that there will be very rapid wear of the cutting edges.
Carbon steels can have a vast range of property values and combinations of properties, depending on carbon content and both mechanical and heat treatments (11§6). Only a brief indication of the possibilities can be made. The typical variations in tensile strength and notch toughness on impact (‘Izod’, see Fig. 1§10.1) are shown in Fig. 1.4, which indicates that there is a certain compromise to be made. Overall, toughness declines rapidly (i.e. brittleness increases) as the carbon content rises; simultaneously the strength can be made very high. It is this kind of variation that is the basis of the selection of steel grades for particular jobs. Some illustrative applications are given in Table 1.2.
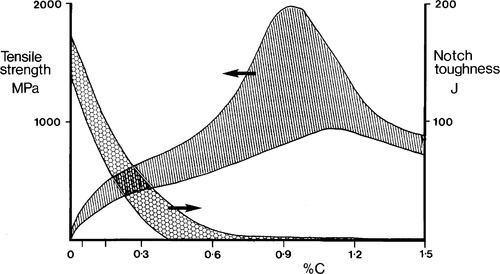
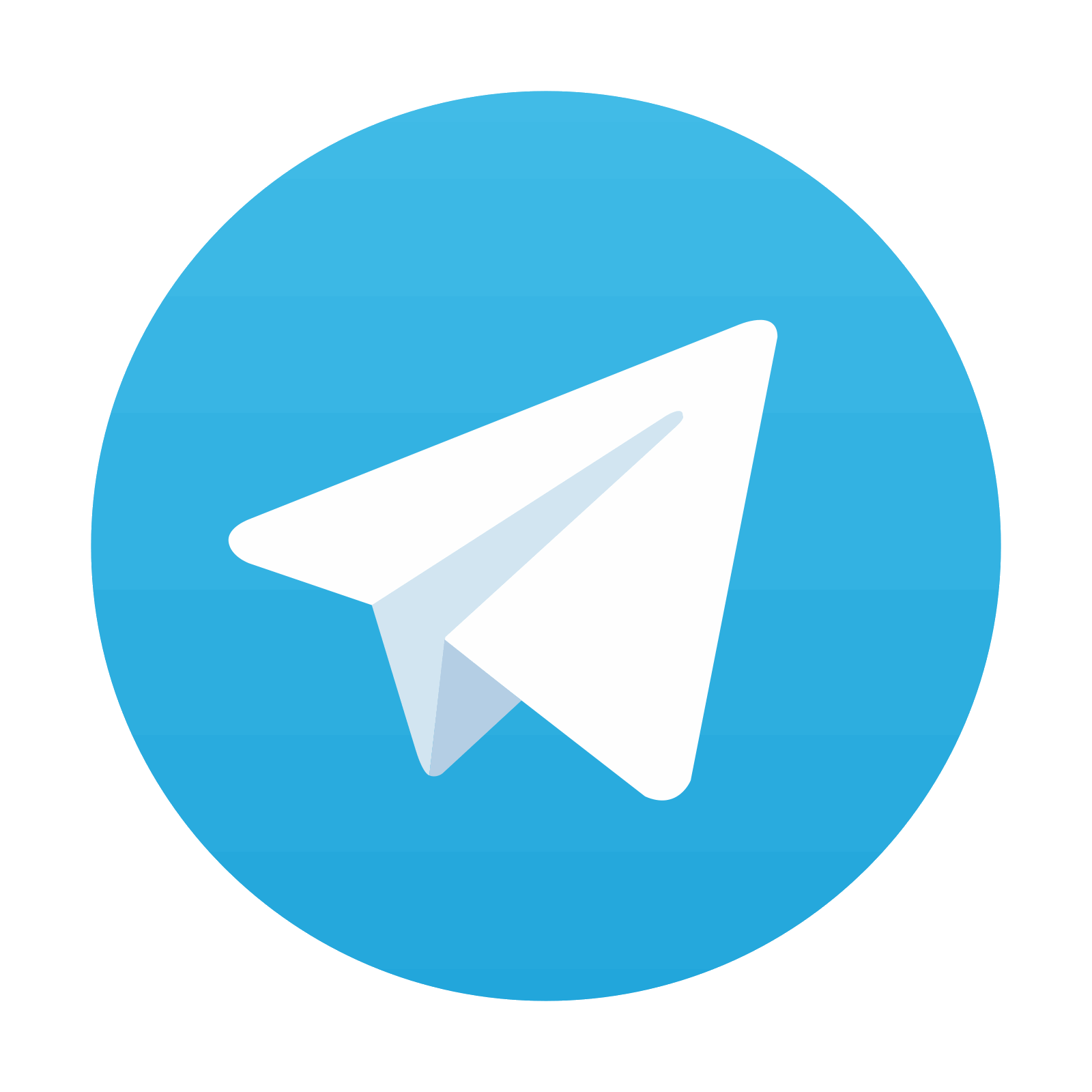
Stay updated, free dental videos. Join our Telegram channel

VIDEdental - Online dental courses
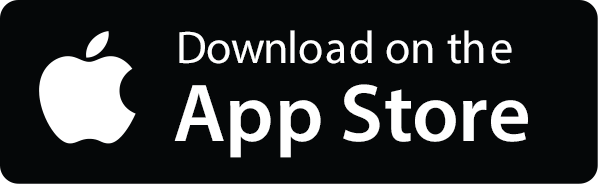
