Cutting, Abrasion and Polishing
This Chapter deals with the set of procedures involved in surface reduction. Whether this is the preparation of a tooth to take a filling or other device, the adjustment of the size and shape of that filling or device, or simply the final finishing of a surface to be smooth and shiny, the processes usually depend on the interaction of the mechanical properties of the tool or abrasive the workpiece.
The distinction is often made between bonded and loose abrasives, but this is superficial. Loose abrasives can only work as a cutting tool if held by some support, however temporarily. The behaviour of abrasives and cutting tools alike depends on the geometry of the interaction and the relative hardness with respect to the workpiece.
Blasting employs loose particles, but these need not be sharp or hard to be effective, although variations here are important. The kinetic energy at impact is a major factor in determining the effect, as well as the direction of delivery. In this and ordinary abrasion, thermal effects may be very important, especially on polymers. There are also implications for vital teeth subject to cutting or polishing.
Electrolytic polishing is only applicable to metals but offers a means of polishing otherwise awkward shapes. It is affected by the previous mechanical history of the surface, and this provides insight into the processes of mechanical abrasion.
Consideration of surface reduction, and the need for it, is connected with the question of roughness. The expression of the idea of roughness depends in part on the techniques used to measure it. The terms are explained to facilitate discussion and interpretation of advertising and other literature.
Frequently neglected, the techniques for the preparation and finishing of surfaces are of evident importance in determining the quality, even the success, of a treatment. Understanding the factors involved will give better control, more efficient operation, and reduced risk of faults in all the many areas in dentistry where surface reduction is employed.
In the course of dental procedures there are many jobs which require materials to be shaped and their surfaces finished, most immediately teeth themselves, to take restorations. Then there are the restorative materials: amalgam, filled resins, glass ionomer cements amongst the direct filling materials to be handled in the mouth, and acrylic, cobalt-chromium, gold and so on to be cut, trimmed and polished in the laboratory, sometimes at the chairside. Other techniques, such as sand-blasting, toothbrushing, electropolishing, and dental prophylaxis are similarly under the heading of shaping and finishing. In view of the frequency with which such operations are carried out, controlling not just the success but the very execution of a procedure, it is worthwhile giving some consideration to the factors which influence such processes. To these deliberate actions must be added the undesired or unintentional effects of abrasion, i.e. wear. Tooth on tooth, tooth on restoration, bur on tooth; each of these and others have a detrimental effect. Some may be minimized by a proper choice of materials, some may be reduced by proper design; none may be avoided altogether. All must be recognized and taken into account.
The three terms that form the title of this Chapter may appear to be separate ideas, even though the purpose, shaping and finishing, is more general. In fact, each involves surface reduction in some fashion: removal of material. This provides the common theme and the reason for the grouping. What is needed then is an understanding of the basis of the choices to be made, and the processes involved, such that the user can take control of the outcome.
§1 Background
It is noteworthy that relatively little is understood about the processes involved in cutting and wear. This is despite the evident economic considerations of doing these kinds of task efficiently, and not least in the industrial context where milling and turning are routine manufacturing processes. Because of this, a vast amount of effort has gone into studies of cutting and wear, but the theoretical basis remains weak. Questions such as which mechanisms of those proposed in an enormous literature are actually operating or important cannot easily be answered in a direct and theoretically-informed way, although there is much data and much experience to guide decisions.
This situation is probably due to three factors. Firstly, as classified by chemical nature and mechanical properties (especially viscoelasticity and strength), the range of types and behaviours of material is very large. To this must be added the complications of composite materials, where very many combinations are possible and increasingly are being applied. Secondly, many of the range of several possible mechanisms for the removal of material from a substrate may be operating simultaneously. They will then vary in their relative contribution to the overall effect with changes in temperature, pressure, speed and time in any one operation, possibly continuously throughout an operation, and particularly so if the tool is itself wearing (which, of course, it always is). In addition, changes in material properties, most importantly work hardening, add a further dimension of variability. Thirdly, what may be learned about the behaviour of a material under one reduction regime may provide little or no guide to behaviour under a different procedure. We shall rely greatly, then, on the result of careful observation, for it may be that for surface reduction processes, taken as a whole, there may never be a general explanatory theory. In common, then, with many other fields, cutting and abrasion in dentistry rely on empirical knowledge, but this does not preclude attempts at better understanding.
Many of the materials themselves have already been discussed and what follows will relate only to the several possible factors of interest in order to give a broad overview of the subject, rather than attempt to assess their importance under specific conditions and on specific materials. However, it does assume that the structure and general behaviour of these materials is understood.
§2 Bonded Abrasives
An abrasive is a material which is understood to wear away the substrate to which it is applied, with some relative motion between the two. It does this by means of many small particles, whether sharp or otherwise, but which are not organized in any regular fashion. Often this wear is described as the result of friction, but we distinguish abrasion from the effects of merely rubbing (§3.2) because the former involves the generation of scratches, rough grooves which have been gouged in the surface by the passage of the abrasive. Repeated scratching results in the detachment of particles of the substrate and thus the reduction of the surface.
Abrasives are employed in two major forms in dentistry: bonded, as in sandpaper, interproximal finishing strips, cut-off discs, grinding stones, diamond points, and model trimmers; and loose, as in toothpaste and various other kinds of prophylaxis1 and polishing pastes, as well as for sand-blasting and similar operations. However, with the exception of the blasting materials, the loose abrasives can be usually treated as if they were bonded because in use they will be caught up in the bristles of brushes or the fibres of fabric mops and thereby held, even if temporarily, to be dragged across the substrate. Thus the surface texture of the carrier material is important. For example, natural bristle toothbrushes provide greater abrasivity than nylon ones because the bristles of the former have sculptured surfaces, those of the latter are very smooth. We shall return to blasting materials later (§4). The term ‘loose’ abrasive also applies to products supplied in a waxy or viscous medium as well as dry powders because the essential feature is that the particles are permitted, indeed expected, to move relative to one another. Partly this is to allow the treatment of complicated surfaces, such as the occlusal form of a tooth, without the restriction of access imposed by a fixed shape tool or the damage that would ensue to carefully carved contours. Partly, too, it is to allow replenishment of the abrasive.
•2.1 Rate of removal
So, if we consider a generalized bonded abrasive particle in its interaction with a substrate (Fig. 2.1), there are a number of factors which are of interest as having an influence on the outcome.[1] Since the abrasive particle works by gouging a scratch, the first requirement is that the particle be pushed into the surface to some extent. Clearly, the load, F, acting on the particle controls the depth of penetration, p, as this must be related to the indentation hardness (1§8) of the substrate material. If the particle is now to move, the rate of doing the work of deformation obviously depends on the speed of the particle, u, and for strain rate-sensitive systems (such as polymers) this will be of great importance. However, the amount of deformation imposed on the emerging swarf is controlled by the geometry of the system, in particular as measured by the included or ‘attack’ angle, θ, between the advancing face of the particle and the substrate surface.
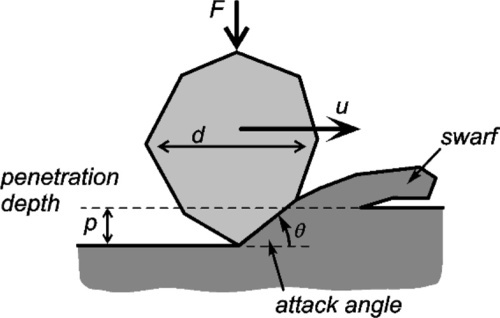
If for the moment we ignore angle and velocity, we can commence an analysis by assuming (reasonably) that the cross-sectional area, A, of the groove produced by a single particle is on average indicated by:
< ?xml:namespace prefix = "mml" ns = "http://www.w3.org/1998/Math/MathML" />
for particles of similar shape; the constant of proportionality is independent of particle size. If we treat the individual particles as hardness test indenters, a hardness value, H, may be represented by a relationship of the form (cf. 1§8):
because the indentation diameter di will be proportional to p, again on average. Now, the maximum number of particles that can contact unit area of the surface is indicated by:
But the mean load per particle in contact with the surface is:
where σ is the applied load per unit area overall, the nominal stress. Thus, substituting from relations 2.2 and 2.4 in 2.1:
If we further assume that the material ploughed from the groove is not merely pushed aside but broken free, the volume removed by each particle, δV, is proportional to the length of traverse of the particle, the length of the scratch, L, i.e.
Therefore, for the n particles in contact,
where V is the total volume. Hence, from relation 2.5, substitution for A gives
If we then address the rate of removal, the volume per unit time is found by substituting velocity, u, for L:
Already we have some justification for the intuitive view that the faster we move the abrasive, the harder that we press, and the softer the workpiece, the more rapidly we will indeed remove material. Conversely, this immediately gives us control of the process: light pressure and low-speed application of the abrasive permits more gradual removal of material, and therefore less risk of unintentionally going too far. Once material has been removed the workpiece can rarely be rebuilt. To this we must add intermittent application with frequent inspection, for safety.
In practice, the constants of proportionality in the above will depend on a number of factors, and vary with time. Thus, wear or breakdown of the abrasive particles themselves will change their shape and so their efficiency may deteriorate. For example, so-called gamma alumina is a milder abrasive than the alpha crystal form (corundum) because it is a weaker solid and breaks down during use. Thus the scratches it produces get smaller as the polishing process proceeds. Conversely, the alumina grinding stones used in dentistry (“white stones”) should not break down for continued rapid reduction of hard substrates. Obviously, sharp particles will produce higher stresses beneath their points than would rounded ones, and penetrate further for a given load, while smooth rounded profiles will tend to slide more easily over the substrate and not plough up any material. Similarly, removal of abrasive particles from the work area as their bond to the carrier breaks down will reduce the values of n and A: sandpaper wears out.
•2.2 Particle size
It might appear from the above that the effect of an abrasive is expected to be independent of particle size. This can be largely true under some circumstances in practice, but there are limits. One is clearly implied by relation 2.2: if F > k.d2H (where k is the unknown constant of proportionality); no further increase in the value of A can follow as no greater width of penetration than d is possible. Nor is greater depth of penetration possible if the particles are randomly oriented and roughly equiaxed, as is reasonable and commonly the case for abrasives. In fact, a bonded abrasive particle obviously does require at least part of its depth embedded in some binder: on average about half can be expected; this therefore limits the maximum penetration possible even further. However, from relation 2.4, for larger particles the load per particle is greater and thus the depth of the scratch produced is greater for a given overall stress, σ.
It is also difficult to ensure that the load on each particle is accurately controlled to be more or less uniform. This is because it is essentially impossible for all abrasive points to lie in the same plane, as is implicitly assumed in the above development, even with carefully selected abrasives; there must be a size distribution (a factor range for maximum and minimum of 1.5 ~ 3 and 0.7 ~ 0.3 is commonplace). Uniformity is certainly impractical with commercial abrasives (for reasons of cost if nothing else) and these generally consist of a range of sizes laid down on a smooth backing. It is also very difficult to control particle orientation, to ensure that the cutting points are all near an optimum orientation. This kind of effect is especially relevant to items such as hard-bonded grinding wheels and ‘rubber’ wheels which rely on wear to expose fresh, sharp abrasive.2 In fact, a good abrasive must be brittle if it is to do its job without becoming uselessly distorted by plastic deformation, and brittle fracture cannot be expected to occur in a regular manner across the abrading surface. Thus, the maximum depth of scratch possible will depend on the irregularity of the abrasive layer, while the number of particles in contact will therefore vary with the pressure applied.
These two issues lead naturally to the general practice of using finer and finer grades of abrasive successively, not just to control the rate of material removal but to control the size of scratch remaining in the surface. Each stage should be aimed at eliminating all scratches from the previous stage. This means in part that less effort is required to complete the following stage because the amount of material it is necessary to remove is less. It also means that the grade of grit in each abrasive system that is available in the surgery or laboratory should be properly characterized if time and effort are not to be wasted by ‘polishing’ with a similar or (worse) coarser grit than that just used. A typical and efficient sequence involves using grits whose sizes differ by factors of 1.5 to 2. Unfortunately, there are several systems in use for designating particles sizes and the correspondence between them may be poor (Fig. 2.2). Manufacturers may use different schemes or criteria, and these can vary between types of product so that the numbers not comparable, even within one manufacturer’s range. Worse, few dental products give any indication of grit size, being coded by colour or just given crude labels (‘coarse’, ‘fine’). These designations clearly vary between products, sometimes with very confusing results.
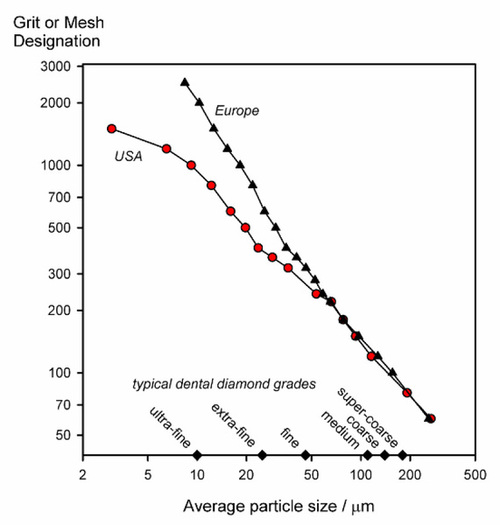
Notice that very fine finishes indeed are possible with coarse abrasives, as in industrial surface grinding of metal. Here, a high speed grinding wheel has its spindle fixed in the machine, and the workpiece is rigidly attached to a movable table. The workpiece is then moved back and forth, scanning slowly sideways, ensuring that any high point is eventually struck by the highest point on the abrasive wheel. That is, the relationship of abrasive to workpiece is very tightly controlled, i.e. constant separation between the rotation axis of the wheel and the base of the workpiece. This condition does not apply to any dental procedure. Normally, in dentistry, a rotating instrument is held freehand against the substrate and control even of the load applied is very difficult. Control of geometry in the workpiece is therefore usually poor unless great care is taken, but it can never be considered to be very good.
•2.3 Effects of abrasion
In abrading a surface the material from the scratch is clearly displaced, and sometimes this just fills previously made scratches. But there may also be considerable distortion in the regions adjacent to the scratch, depending on how ductile or brittle is the substrate. Remembering that the effect of a hardness test indentation extends over several diameters into adjacent material (1§8.5), both sideways and down into the workpiece, the plastic flow and deformation produced may result in a considerable altered zone (Fig. 2.3).[2] Consequently, there may be work-hardening, especially with metals and sometimes polymers, which may change the efficiency of material removal as the grinding proceeds. The scale of these effects depends on the depth of the scratch and therefore the size of the abrasive particle under most conditions (Fig. 2.4). It is the depth of the affected zone that leads to the rule of thumb in metallographic polishing (12§2) to polish for twice as long as it takes to remove the scratches from the previous stage. This is to allow the study of unaltered material, but it obviously has implications for the corrosion behaviour of a surface if there is much strained material remaining.
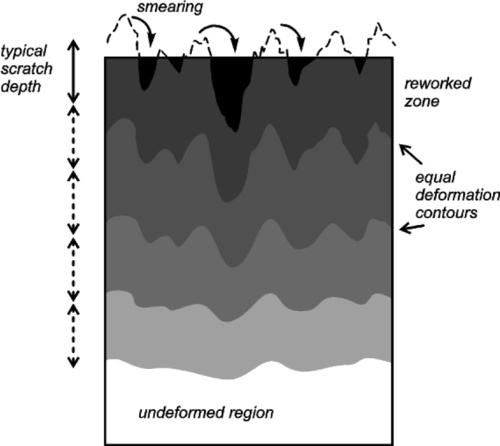
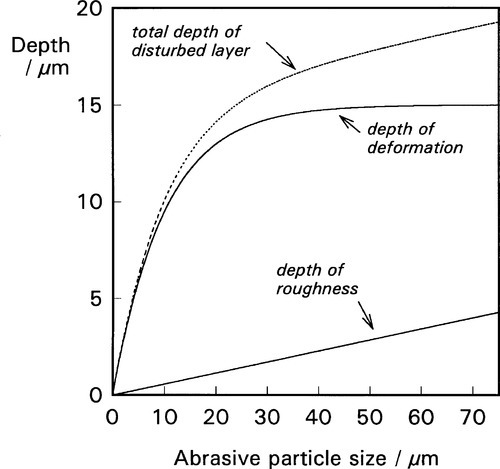
•2.4 Polymers
The properties of polymers are strongly dependant on temperature (Chap. 3) so that considerable variation in abrasion rates may be expected as friction warms the surface and the work of plastic flow is delivered (Fig. 2.5). The thermal conductivity of polymers is rather low, so that heating in this way is very rapid. The glass transition temperature is typically not far from normal working temperatures. As might be anticipated, property changes are most marked at temperatures around the glass transition, and any aspects of structure and the presence of plasticizers which change this value will produce changes in abrasion behaviour. But it is also apparent that, due to the inverse equivalence of strain rate and temperature, the speed of the abrasive particle over the surface will also influence the rate of abrasion beyond that otherwise expected.
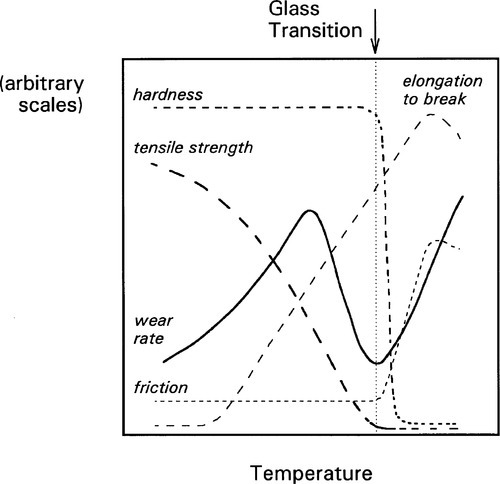
Fig. 2.5 shows how complicated are the interrelationships of the mechanical properties of such a material to produce the typical wear curve shown. The need to use diamond instruments at high-speed to trim filled-resin restorations before they are fully set is apparent from this, but equally the use of coolant and intermittent application of the abrasive device as a general rule when handling polymers is evidently of considerable importance. The most obvious example of what happens when this is not taken into account is in the final polishing of a PMMA denture base: if the temperature rises above about 70 °C, the internal strain relief (stress relaxation) that occurs may be enough to destroy the fit. But even if it does not the acrylic may become sufficiently softened that it will be deformed in the hand.
Relation 2.8 is supported by observations on metals (Fig. 2.6) which indicates a fairly strict dependence of wear resistance to hardness.[1]A similar relationship, although with greater scatter, is indicated for ceramic materials, but the differing slope is probably due to a different mode of failure, i.e. essentially brittle with little if any plastic deformation possible. The polymers seem to occupy an intermediate position, but with much greater scatter, reflecting the greater complexity of the processes involved for these materials.
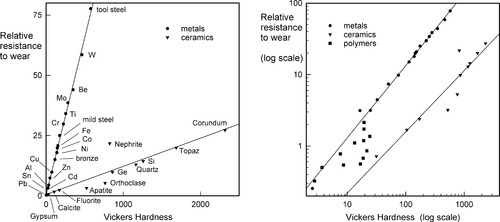
•2.5 Clogging
There is a further source of diminishing efficiency with fixed abrasives: clogging. This is the filling of the roughness between abrasive particles by debris from the substrate. It has the effect of gradually reducing the apparent size of the abrasive, thereby reducing the scratch depth that it can achieve, and thus reducing the rate of material removal. The softer the substrate the greater the tendency for this to happen. It also depends to a large extent on the ability of that material to weld to itself under heat and pressure. Certainly, because of the work being done in friction and deformation, local temperatures can rise very high during abrasion, and melting is common, even if for a short time. Examples of such clogging are resinous woods in sandpaper, aluminium or amalgam on stones, and nearly any polymer on any fixed abrasive. In fact, the chips arising from any abrasive action will be held for a while, even if they subsequently fall clear, because separation between the abrasive body and the substrate must first occur for this to happen. Thus, the penetration of abrasive particles into the substrate and the rate of removal of material are self-limiting as the chips fill the roughness, even if clogging as ordinarily understood does not occur. Some fixed abrasives are made with less than 100% coverage in order to leave more room for chips and reduce clogging.
•2.6 Lubricants
Such inefficiency is wasteful of time and materials, but is generally easily overcome by the use of a liquid lubricant. This will have functions besides the obvious reduction of ineffective friction (which would, on its own, achieve little in the way of surface reduction). The liquid will behave as a coolant, carrying away much of the heat, preventing general temperature rises that could melt or soften the substrate, but also reducing the temperature rise under the abrasive particles themselves. Then, by coating all surfaces, it will provide a barrier between particles of debris which will limit their tendency to weld together (as it were, deliberate surface contamination) or stick to the abrasive. This also assists in preventing the displaced substrate that has yet to break free from re-welding to the parent material. In addition, it will tend to flush away the debris from the grinding site, further reducing the opportunity for clogging and self-welding, although it cannot affect the temporary ‘roughness-filling’ effect.
In industrial contexts, the design of lubricants for efficiency is a very serious matter, and many complicated formulations exist to suit different tasks. In the dental context, the choice is very much more limited. In the mouth, naturally, water is the obvious choice as it is cheap and mostly harmless, but the question of toxicity or hazard is also important in the laboratory or at the chairside because of the close contact and short working distances normally involved: isolation or protection are not practical alternatives. Even so, occasionally fluids such as glycerol offer better results and may be used safely. Nevertheless, it is important that the lubricant actually gets to the site of active cutting. Frequently this just means that a copious supply is required, but when rotating instruments are used the liquid must be supplied on the ‘upstream’ side, where the abrasive or cutter is approaching the workpiece. This means that it will be carried or forced into the area where it is most needed. It will be spun off a high-speed tool very quickly and simply not reach the target if the jet is applied ‘downstream’.
•2.7 Zeta potential
In this general context it is worth noting that the mechanical properties of the substrate depend in part on surface energy. The link here is that much new surface is being created, and the work of its creation must be supplied (1§7, 10§1.2). Surface energy is related to a factor known as the surface or zeta potential. This is the potential which is spontaneously developed due to charge separation across a solid-liquid interface. There are obviously some similarities with the idea of electrode potential (13§1), but it applies to all solids, not just metals. Zeta potential is strongly dependent on the characteristics of the solution, especially concentration and pH, and can be made to be zero by appropriate adjustments in the solution chemistry. These zeta potential variations are accompanied by large changes in the measured surface hardness, strength and, most noteworthy, abrasion and cutting rates. This has great economic importance in such tasks as drilling for oil. It may be that, with suitable non-toxic additives to the cooling water, tooth material cutting may be made much more efficient with less tool wear, although this is still some way off yet as a practical clinical procedure (more directly chemical dissolution methods may preempt this approach). In the laboratory, too, it may become possible to improve efficiency and the finish obtained by an appropriate choice of coolant.
However, despite all of the appropriate precautions being taken, fixed abrasives do sometimes still clog. With abrasive papers or interproximal finishing strips there is no economic choice but to use a new piece. With industrial grinding wheels it is usually necessary to ‘dress’ the wheel by using a single mounted diamond to strip away a layer and expose a fresh abrasive surface. Occasionally it might be possible to dissolve the clogging material with a solvent or acid, but this is rarely worth the trouble and expense. But if the clogging were due to improper procedures, it would be far better to use the correct abrasive for the job in the correct manner – cheaper and faster.
§3 Cutting Tools
The simple relation 2.8 was derived for a particle with an essentially conical shape at the contact point, but this configuration is not very efficient in terms of material removal because the principal action is one of ‘ploughing’: much material is displaced to the sides. Only if the deformation is sufficient to cause fracture will material be removed instead of merely being redistributed. The difference between abrasion and a true cutting action (Fig. 3.1) is very clear.
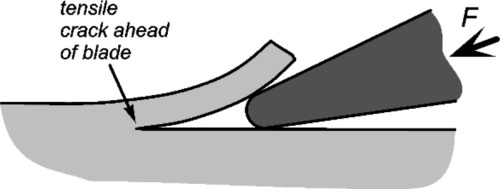
The terminology applied to industrial machine tools such as lathes and shapers – which use a single bladed cutter, and milling machines – which use multibladed rotary cutters, is directly applicable to dental instruments such as enamel chisels and the multibladed cutting tools (‘burs’) used in dental handpieces. It does not matter which part is fixed and which is moving, it is only the relative />
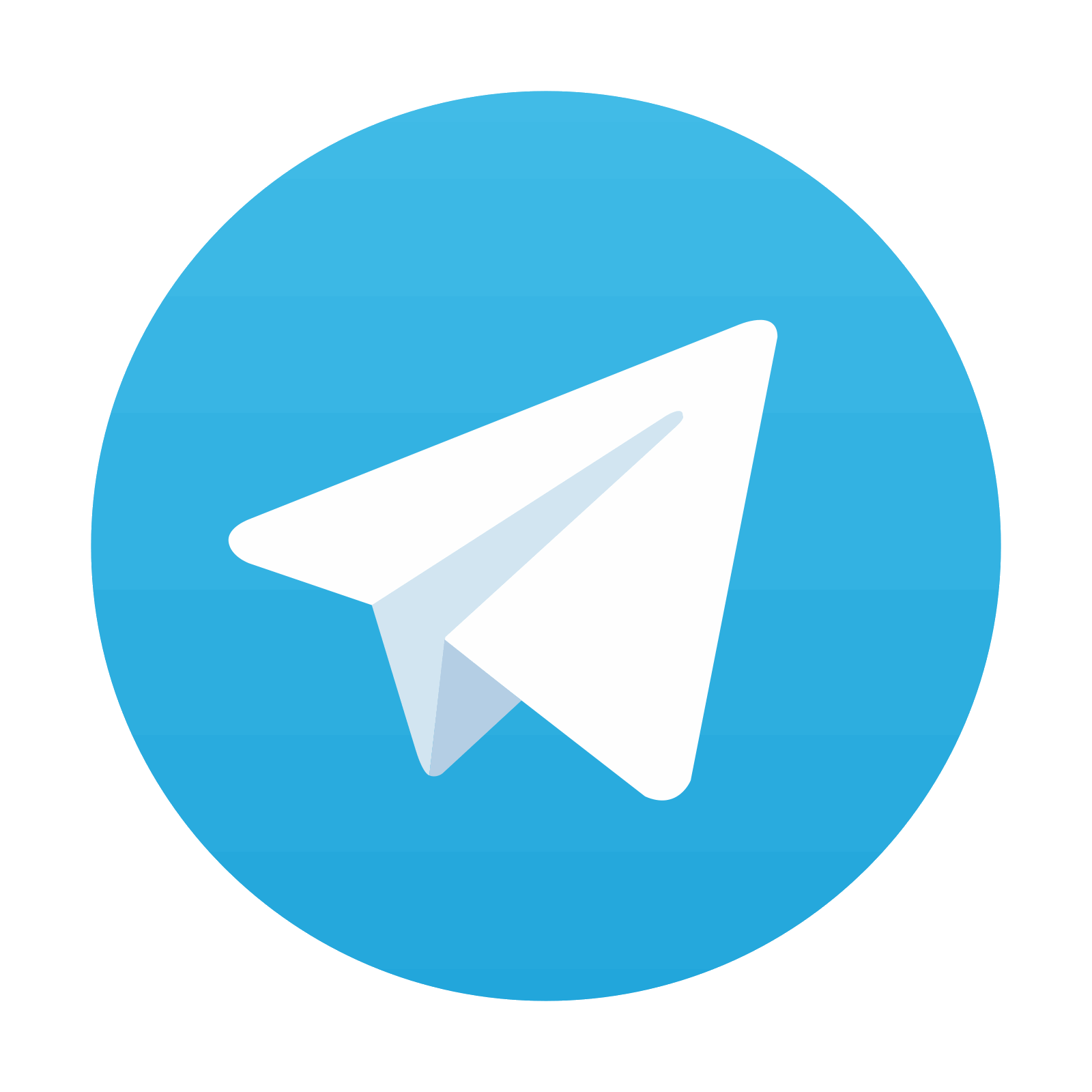
Stay updated, free dental videos. Join our Telegram channel

VIDEdental - Online dental courses
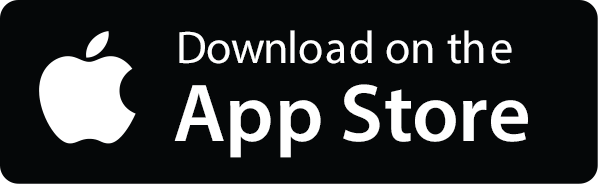
