Key Terms
Amalgam An alloy containing mercury.
Amalgamation The process of mixing liquid mercury with one or more metals or alloys to form an amalgam.
Condensation The process of pressing dental amalgam by force to remove excess mercury and ensure continuity of the matrix phase.
Creep The time-dependent strain or deformation that is produced by a stress. The creep process can cause an amalgam restoration to extend out of the restoration site, thereby increasing its susceptibility to marginal breakdown.
Delayed expansion The gradual expansion of a zinc-containing amalgam over a period of weeks to months. This expansion is associated with the development of hydrogen gas, which is caused by the incorporation of moisture in the plastic mass during its manipulation in a cavity preparation.
Dental amalgam An alloy that is formed by reacting mercury with silver, copper, and tin, and that may also contain palladium, zinc, and other elements to improve handling characteristics and clinical performance.
Dental amalgam alloy (alloy for dental amalgam) An alloy of silver, copper, tin, and other elements that is processed in the form of powder particles or as a compressed pellet.
Marginal breakdown The gradual fracture of the perimeter or margin of a dental amalgam filling, which leads to the formation of gaps between the amalgam and the tooth.
Trituration The mixing of amalgam alloy particles with mercury in a device called a triturator ; the term is also used to describe the reduction of a solid to fine particles by grinding or friction.
When metal particles are mixed with mercury in certain proportion at room temperature, the mixture appears plastic initially. At that consistency, the mixture can be adapted to any shape with light pressure. Meanwhile, the outer portion of the particle in the mixture dissolves into mercury that slowly hardens the mixture. When the solubility of the metal in mercury is exceeded, crystals of mercury-containing compounds start to precipitate within the mercury. The process increases the firmness of the mixture, which enables sculpting of the mixture to the desirable anatomical form with instruments. The reaction continues at a slower rate as the mixture transforms into a solid with sufficient strength to resist fracture. The reaction process is called amalgamation, and the metallic solid containing mercury is called amalgam.
After reacting with liquid mercury, how do the original powder particles become structural components of the set dental amalgams?
Amalgam Alloy
The amalgams used today are largely based on the formulation published by G. V. Black in 1895. The major modifications to that formulation were raising the copper content and the making of spherical particles during the early 1960s. Despite amalgam’s long history of success as a restorative material, there have been periodic concerns regarding the potential adverse health effects arising from exposure to mercury in dental amalgam. Because of advances in resin-based composites and adhesive technology in dentistry, the use of amalgam has declined substantially. Dental amalgam use will be limited in the future and may eventually be phased out of the clinician’s armamentarium.
As with other materials discussed in this book, practical skill and sound scientific familiarity with the material are needed for making high-quality restorations. Even when no new amalgams are being placed in patients, there will still be billions of amalgam restorations remaining in patients’ mouths. Many of these restorations will require attention, such as for replacement, repair, or refurbishing procedures. In this chapter, amalgam structure, properties, and manipulation characteristics are discussed. However, these concepts require an understanding of several key terms commonly used by the dental profession.
Before these alloys combine with mercury, they are known as dental amalgam alloys. They are usually provided as (1) irregularly shaped particles ( Figure 8-1 , A ) produced by milling or lathe-cutting a cast ingot of the amalgam alloy, (2) as spherical particles ( Figure 8-1 , B ) produced by atomizing the liquid alloy in a chamber filled with inert gas, or (3) as a mixture of both lathe-cut and spherical particles ( Figure 8-1 , C ). The powder may also be compacted in the form of pellets, which are readily crushed to powder during trituration, the process of mixing mercury and alloy.

Originally, the dentist had to dispense alloy powder and mercury in a mortar and mix them together with a pestle by hand. Later, the components were dispensed in a reusable capsule ( Figure 8-2 ) with a pestle and triturated by a power-driven mechanical device called a triturator ( Figure 8-3 ). Today, disposable amalgam capsules are widely available. Each capsule contains a predetermined amount of alloy powder and mercury in a sealed pouch, and the capsule is sealed to prevent evaporation of the mercury.


Composition
Amalgam alloys are classified as either a low-copper (conventional) or high-copper alloy ( Table 8-1 ). In both types, the major components of the alloys are silver and tin.
COMPOSITION (MASS %) | ||||
---|---|---|---|---|
Amalgam | Ag | Sn | Cu | Zn |
Low copper (lathe-cut) | 70.3 | 25.9 | 2.8 | 0.9 |
Low copper (spherical) | 72.0 | 25.0 | 3.0 | — |
High copper (admix) | 69.5 | 17.7 | 11.8 | 1.0 |
High copper (spherical) | 61.0 | 26.0 | 13.0 | — |
The Silver-Tin System
Figure 8-4 is an equilibrium-phase diagram of the silver-tin alloy system. Conventionally, starting from the left of the phase diagram, each phase is designated in Greek alphabetical order. The ratio of silver to tin in Table 8-1 shows that amalgam alloys have a narrow range of compositions, falling within the β + γ and the γ phases of the diagram.

How can zinc be a beneficial additive to alloy for dental amalgam but also a component that can potentially cause significant postoperative discomfort to the patient?
Low-Copper Alloys
Silver-tin alloys are quite brittle and difficult to blend uniformly unless a small amount of copper is substituted for silver. The chief function of zinc in an amalgam alloy is to act as a deoxidizer that reacts with oxygen during melting to minimize the oxide formation of other constituents. Alloys without zinc are more brittle, and their amalgams tend to be less plastic during condensation and carving. The specification of the American Dental Association (ADA) for amalgam alloys allows some mercury in the alloy powder. The structure of these conventional alloys was dominated by Ag 3 Sn (γ phase), with some Cu 3 Sn (ε phase).
High-Copper Alloys
The first high-copper alloy was formulated by mixing one part of silver-copper eutectic spherical spheres particles with two parts lathe-cut particles of Ag 3 Sn. This modification raises the copper content to 11.8% by weight. This is often called dispersed-phase alloy or admixed high-copper alloy. A second type of high-copper alloy was made by melting all components of the dispersed-phase alloy. This process yields a single composition system. The presence of the higher copper content makes cutting the powder into particles difficult. Thus they are often provided in a spherical form that is produced by an atomization process. The copper content of this group of alloys could be as high as 30% by weight. Various amounts of indium or palladium have been included in some commercial systems.
Gallium-Based Alloys
Gallium, when alloyed with indium or tin, can be a liquid at room temperature. It has been used to triturate with alloys for high-copper amalgam as a substitute for mercury.
Powder Configuration
Dental amalgams are made by mixing alloy powders with mercury. The reaction begins at the particle–mercury interface. Therefore the physical configuration and condition of the particles have a significant influence on the setting process.
Lathe-Cut Powder
An as-cast ingot is first annealed to retain a uniform phase, and then placed in a milling machine or in a lathe to be fragmented by a cutting tool or bit. The powders obtained from cutting are acid-washed to produce a more reactive surface. Because the stresses induced into the particle during cutting are not uniform and can slowly be self-relieved over time, they can cause the performance of the amalgam to be inconsistent.
Atomized Powder
The molten amalgam alloy is atomized into fine spherical droplets of metal in a chamber of inert gas. If the droplets solidify before hitting a surface, the spherical shape is preserved, and these atomized powders are called spherical powders. Like the lathe-cut powders, spherical powders are given an annealing heat treatment and surface washing. Note in Table 8-1 that alloys for making spheres do not contain zinc because there is no oxygen in the chamber to cause oxidation.
Particle Size
The average particle sizes of modern powders range between 15 and 35 μm. Smaller particles greatly increase the surface area per unit volume of the powder. A powder containing tiny particles requires a greater amount of mercury to form an acceptable amalgam. The particle-size distribution can affect the character of the finished surface. When the amalgam has partially hardened, the tooth anatomy is carved in the amalgam with a sharp instrument. During carving, the larger particles may be pulled out of the matrix, producing a rough surface. Such a surface is probably more susceptible to corrosion than a smooth surface. A smaller average particle size tends to produce a more rapid hardening of the amalgam, with greater early strength.
Lathe-Cut Powder Versus Spherical Powder
Amalgams made from lathe-cut powders or admixed powders tend to resist condensation better than amalgams made entirely from spherical powders. Because freshly triturated amalgams from spherical powders are very plastic, one cannot rely on the pressure of condensation to establish the proximal contour for a class II restoration. Spherical alloys require less mercury than typical lathe-cut alloys because spherical alloy powder has a smaller surface area per volume than does the lathe-cut powder. Amalgams with low mercury content generally have better mechanical properties.
Through what mechanism does the addition of 6 wt% or more of copper by weight prevent the formation of the undesirable γ 2 phase?
Amalgamation
As discussed earlier, modern dental amalgam alloys are based on the intermetallic compound Ag 3 Sn; therefore the main reaction occurring after trituration with mercury will mainly be that between Ag 3 Sn and mercury. Other elements in the alloy, especially copper, also play a significant role in the final microstructures of set amalgams.
Low-Copper Alloys
The main reaction products of low-copper alloy are the body-centered cubic Ag 2 Hg 3 (γ 1 ) phase and the hexagonal Sn 7-8 Hg (γ 2 ) phase ( Figure 8-5 ). Both phases are designated γ because they happen to be the third phase of the respective Ag-Hg and Sn-Hg systems. Because the solubility of silver in mercury is much lower than that of tin, the Ag 2 Hg 3 phase precipitates first and is designated as γ 1 , whereas the Sn 7-8 Hg phase precipitates later and is designated as γ 2 . There is evidence from x-ray diffraction and thermal analyses of set amalgam that a δ phase, which is richer in mercury than γ 2 , is present in low-copper alloy instead of γ 2 . The existence of γ 2 or δ phases in low-copper amalgams remains an unresolved question. For the purpose of this discussion, the Sn-Hg phase is designated as γ 2 .

The low-copper alloy is usually mixed with mercury in about a 1:1 ratio. This amount of mercury is insufficient to consume the alloy particles completely; consequently, unreacted particles are present in the set amalgam. Thus a typical low-copper amalgam is a composite in which the unreacted particles are distributed within the γ 1 and γ 2 phases. The sequence of amalgamation of the silver-tin alloy is shown schematically in Figure 8-6 .

The physical properties of the set amalgam depend on the relative percentages of each microstructural phase. The greater the number of unreacted Ag-Sn particles retained in the final structure, the stronger the amalgam will be. The γ 2 phase is the weakest and least stable in a corrosive environment and may suffer corrosion attack, especially in the crevices of the restorations. A reaction between Cu 3 Sn (ε phase) and γ 2 also occurs and yields Cu 6 Sn 5 (η′ phase) to a lesser extent because of the low copper content. Figure 8-7 illustrates the features found in a typical microstructure of amalgam made from a lathe-cut, low-copper alloy.

Compared with amalgams made from admixed high-copper alloys, what are the benefits and the risks of the amalgams made from high-copper, single-composition, spherical particles?
High-Copper Alloys
As discussed earlier, high-copper alloy powders are available in a two-phase admixed powder and a single-composition, single-phase powder, each with a unique amalgamation process ( Figure 8-5 ).
Admixed Alloys
When mercury mixes with an admixed alloy powder, the silver in the Ag-Cu spheres and the silver and tin from Ag-Sn particles dissolve into the mercury. Although both γ 1 and γ 2 crystals form, as in lathe-cut alloys, the tin in mercury diffuses to the surfaces of the Ag-Cu alloy particles and reacts with the copper to form a layer of η’-phase crystals on the surface. The η’ layer on the surface of Ag-Cu alloy particles also contains γ 1 crystals because the γ 1 and η′ phases form simultaneously. In this reaction, the γ 2 phase forms along with the η’ phase, but the γ 2 phase later reacts with copper from Ag-Cu spheres, yielding additional η’ phase (the secondary solid-state reaction in Figure 8-5 ). The γ 2 phase can be eliminated with at least 12% of copper by weight in the alloy powder. Figure 8-8 illustrates the microstructure of an admixed amalgam. As in the low-copper amalgams, admixed amalgam is a composite of γ 1 because of the matrix phase with discrete unreacted alloy particles.

Single-Composition Alloys
The major components of single-composition particles are usually silver, tin, and copper. The copper content of various single-composition alloys ranges from 13% to 30% by weight. Some alloys contain a small quantity of indium or palladium. Several phases are found in each single-composition alloy particle, including the β phase (Ag-Sn), γ phase (Ag 3 Sn), and ε phase (Cu 3 Sn). Some of the alloys may also contain the η’ phase. The particles usually are spheres, but a formulation with all lathe-cut particles is also available.
When triturated with mercury, silver and tin from the Ag-Sn phases dissolve in mercury. Very little copper dissolves in mercury. The γ 1 crystals grow, forming a matrix that binds together the partially dissolved alloy particles. The η’ crystals are found as meshes of rod-like crystals at the surfaces of alloy particles dispersed in the matrix. In most single-composition amalgams, little or no γ 2 forms (see Figure 8-5 ). Figure 8-9 shows the microstructure of a typical single-composition amalgam. This structure includes unreacted alloy particles, γ 1 grains, and η’ crystals.

What steps can be taken by a dentist to extend the survival time of amalgam restorations?
Clinical Manipulation of Amalgam for Restorations
A good modern dental amalgam alloy can be manipulated so that the restoration lasts, on average, 12 to 15 years. The cavity preparation must be designed correctly, and the amalgam must be manipulated properly so that no part of the amalgam restoration is placed under excessive tensile stress. The manipulation variables discussed in this section are the mercury/alloy ratio, trituration, and condensation.
What is the ideal mercury/alloy ratio for an admixed amalgam and a spherical particle amalgam? What are the consequences of insufficient and excess amounts of mercury for the amalgam restorations?
Mercury/Alloy Ratio
The mercury/alloy ratio is the weight of mercury divided by the weight of alloy needed for trituration. Sufficient mercury must be present in the original mix to provide a coherent and plastic mass after trituration, but the amount must be low enough that the mercury content of the restoration is at an acceptable level without the need to remove an appreciable amount during condensation. The mercury content of the lathe-cut alloy is about 50% by weight, and that for spherical alloys is 42% by weight. When a mortar and pestle were used for mixing amalgam, an excess amount of mercury would be needed to achieve a smooth and plastic amalgam. Removal of excess mercury would be accomplished by squeezing or wringing the mixed amalgam in a squeeze cloth prior to insertion of the increments into the prepared cavity.
The most common dispenser is based on volumetric proportioning. Preweighed pellets or tablets are first placed in a capsule ( Figure 8-2 ). In mechanical mixing, the capsule serves as a mortar. The mercury dispenser should be held vertically to ensure consistent dispensing of mercury. The dispenser should always be at least half full when used to ensure that the proper weight of mercury is dispensed.
Disposable capsules containing preproportioned mercury and alloy are now widely used. Both components are physically separated in the capsule. Some capsule designs require activation before trituration to bring the components together. Other designs, called self-activating capsules, bring the alloy and mercury together automatically during the first few oscillations of the amalgamator.
Regardless of the method used, the proper amount of mercury and alloy must always be proportioned, or the preproportioned capsule must be activated just before the start of trituration.
How should the optimal trituration time be determined for a given dental amalgam product?
Mechanical Trituration
The objective of trituration is to ensure proper amalgamation of the mercury and alloy and provide the optimal consistency for condensation. The focus of trituration includes the triturator and the consistency of the mixture.
Triturators
The main mixing mechanism of a triturator is a reciprocating arm holding the capsule under a protective hood. The hood is to confine mercury that might escape into the room and to prevent a capsule from being accidentally ejected from the amalgamator during trituration. Older models are usually a single-speed device with an automatic timer to set the length of mixing. Later models have multiple speed settings. A modern triturator is often microprocessor controlled ( Figure 8-3 ) and contains preset trituration programs for several materials. These newer models can also be programmed by the operator to include other materials. The capsule serves as a mortar. A cylindrical metal or plastic piston of smaller diameter than the capsule is inserted into the capsule, and this serves as the pestle. Spherical alloys often do not need a pestle ( Figure 8-2 ).
Alloy manufacturers often provide a list of recommended time schedules and speed settings in cycles per minute for their alloys and various types of amalgamators. Because of the speed variations in amalgamators, the schedule should serve only as a rough guide. Dentists and assistants may want to adjust the time required to attain a mix of the correct consistency. For a given alloy and mercury/alloy ratio, increased trituration time and/or speed shorten the working and setting times.
A reusable capsule should be clean and free of previously mixed, hardened alloy. At the end of each trituration procedure, one should quickly remove the pestle from the capsule, replace the lid, reinsert the capsule in the amalgamator, turn it on for a second or two, and then remove the amalgam. This mulling process generally causes the mix to cohere so that the amalgam can be readily removed from the capsule with minimal residue in the capsule. Mulling minimizes the need for scraping out partially hardened alloy, which usually produces scratches in the capsule.
Consistency of the Mix
The proper time of mixing can be determined by observing the consistency of the mix. For example, the mix with a somewhat grainy and dull appearance ( Figure 8-10, A ) indicates undertrituration. Not only will the amalgam restoration made from this mix be weak, but also the rough surface left after carving of the granular amalgam will increase the susceptibility to tarnish. If the trituration has produced an amalgam of the general appearance shown in Figure 8-10, B, the strength will be optimal, and the smooth carved surface will retain surface luster longer after polishing. Because of the friction between particles during trituration, such an amalgam mix should be warm (not hot) when the mix is removed from the capsule. This will have no effect on the physical properties of the amalgam other than to shorten the working time somewhat. Overtrituration through a higher speed or a longer mixing time results in a softer (mushy) mixture that often sticks to the wall of the capsule. Compared with the properly mixed amalgam, the surface of overtriturated amalgam is shinier, the shape of the mass is flatter ( Figure 8-10, C ), and the working time is shorter and has a slightly higher setting contraction.

During the condensation of an amalgam, at what point in time should the triturated mixture be discarded and replaced by a new mixture?
Condensation
The goal of condensation is to compact the alloy into the prepared cavity so that the greatest possible density is attained, with sufficient mercury present to ensure continuity of the matrix phase between the remaining alloy particles. This results from a reduction of excess mercury and porosity within the set amalgam.
After the mix is made, the increments of alloy should be carried to, and inserted in, the prepared cavity by means of instruments such as small forceps or an amalgam carrier designed for this purpose. Condensation of the amalgam should then be promptly initiated. The field of operation must be kept absolutely dry during condensation. Because of the nature of the operation, condensation is usually accomplished within four walls and a floor. One or more walls may be a thin sheet of stainless steel, called a matrix band.
Condensation Procedure
Condensation is pressing a condenser point on the amalgam mass under hand pressure. This procedure is usually started at the center, and then the condenser point is stepped incrementally toward the cavity walls. The force requirements depend on the shape of the alloy particle.
After condensation of an increment, the surface should appear shiny. This indicates that there is sufficient mercury present at the surface to diffuse into the next increment so that the subsequent increment added will bond to the preceding one. Removing some of the soft or mushy material before adding the next increment is desirable. This step is less critical with modern-day amalgams that require less mercury for mixing.
If the cavity is a large one or if for some reason undue time is taken to complete condensation, another mix should be made just before the original one is used up or when plasticity is lost. Condensation of partially set material fractures and breaks up the matrix that has already formed. In addition, when the alloy has lost a certain amount of plasticity, condensation without producing internal voids and layering is difficult. The procedure of condensation is continued until the cavity is overfilled.
Condensation Pressure
The condensation pressure is governed by the area of the condenser face and the force exerted by the operator on the mixture. When a given force is applied, the smaller the condenser, the greater is the pressure exerted on the amalgam. If the condenser point is too large, the operator cannot generate sufficient pressure to condense the amalgam adequately and force the mix into retentive areas. A study of 30 practitioners showed that the forces applied are in the range of 13.3 to 17.8 N (3 to 4 lb). To ensure maximum density and adaptation to the cavity walls, the condensation force should be as great as the alloy will allow, consistent with patient comfort. Many of the spherical alloys offer only minimal resistance to the condensation force. Therefore the strength properties of spherical amalgam alloys tend to be less sensitive to condensation pressure.
In many instances, condensation becomes a matter of attaining good adaptation. The potential disadvantages of a spherical alloy compared with an admixed alloy (lathe-cut and spherical particles) are the tendency for overhangs in proximal areas and weak proximal contacts. The shape of the condenser points should conform to the area under condensation. For example, a round condenser point is ineffective adjacent to a corner or angle of a prepared cavity; a triangular or square point is indicated in such an area. Points of various shapes are available to provide effective condensation.
Carving and Finishing
After the amalgam has been condensed into the prepared cavity, it is carved to reproduce the proper tooth anatomy. The objective of carving is to simulate the anatomy rather than trying to reproduce extremely fine details. The carving should start only when the amalgam is hard enough to resist the carving instrument. A scraping or “ringing” sound should be heard when the amalgam is carved. Softer amalgam may be pulled away from the margins by the carving instrument. The matrix band should be removed during the final carving procedure. Make sure that excess amalgam has not been forced beyond the matrix gingivally during condensation.
After carving, the surface of the restoration should be smoothed. This may be accomplished by burnishing the occlusal surface with a ball burnisher and the margins of the restoration with a rigid, flat-bladed instrument. Final smoothing can be concluded by rubbing the surface with a moist cotton pellet or by lightly smoothing the surface with a rubber polishing cup and an extremely fine polishing or prophylaxis paste ( Figure 8-11 ). Clinical data on the performance of restorations support the desirability of burnishing the fast-setting, high-copper systems. Burnishing slow-setting alloys can damage the margins of the restoration.
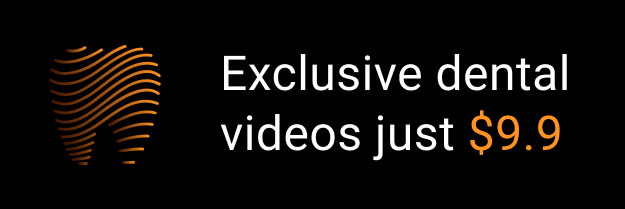